How to drill a concrete wall with a hammer drill?

Concrete is considered the most durable material and is therefore difficult to drill. There are many technical ways to create holes in a concrete surface, but the most popular and effective is drilling with a hammer drill. Thanks to this device, work is done efficiently and quickly.


Which rotary hammer to choose?
It is difficult to drill holes in concrete slabs, since they have increased strength and often have a heterogeneous structure, including crushed stone, metal reinforcement and other fillers. A hammer drill helps to cope with such a task; it can perform drilling both with a blow and without a blow. Therefore, when you have to carry out such construction work as installing plumbing, air conditioners, removing old finishes, laying electrical wiring, you cannot do without this tool. This device is multifunctional and is designed for drilling wide and deep holes.
Before you start drilling concrete, you need to choose the right perforator, since it is available in several types, each of which is characterized by its own technical capabilities.

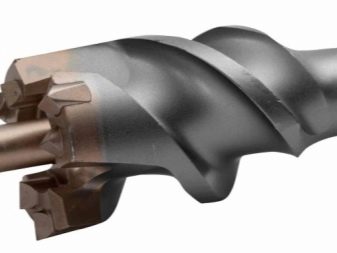
Now on sale you can find simple household and advanced professional models of a hammer drill. Household ones, as a rule, are used for drilling holes in houses and apartments, they have a power of up to 900 W and are equipped with an SDS-plus cartridge. The devices of this type are represented by the trade marks Black Deker, Bosch, Hundai, Skil, Enkor and Caliber. As for professional models, they are suitable for all socket outlets, have additional vibration protection and can work for a long time without interruption. Professional devices from such manufacturers as Dewalt, Makita, Hitachi and Metabo have also proven themselves well.
In addition, when purchasing a perforator for working with concrete, you should pay special attention to several indicators.
- The number of operating modes. Single-mode devices for working with a concrete slab are not suitable, since they are simple and have the functions of an ordinary drill. Dual-mode devices are capable of drilling (drilling with impact force), it is recommended to choose them when it is necessary to make through and blind holes in concrete. These types of rock drills can simultaneously hit and rotate the drill, they are produced from durable metal. Three-mode devices are also considered ideal for working with concrete surfaces. They are versatile, impact without rotating the nozzles and quickly drill through concrete, exposing its solid structure.



- The weight. Impact devices, depending on their weight, can be light, medium and heavy. Lightweight models are electric tools with a capacity of up to 800 W, their weight does not exceed 4 kg. They are most often purchased for processing simple floors. For working with natural stone and concrete, it is best to give preference to middle-class devices that weigh up to 8 kg and have a power of up to 1200 watts. It is possible to drill a hole in concrete with a diameter of more than 40 mm using heavy devices, their weight is more than 8 kg, and the impact energy exceeds 13 J.
- Engine location. Today, manufacturers produce devices with horizontal and vertical motor placement.Horizontal rock drills are of a simple class, they are easy to use, but they cannot cope with concrete surfaces.
They can only drill small holes. Therefore, if you plan to chisel large and deep holes, then you must choose a tool with a vertical type of engine placement. It can work for a long time, since the motor is better cooled in this position.


Types of attachments
Construction work on the processing of concrete slabs or walls is carried out, as a rule, using a perforator, which is often called a drill by craftsmen. This multifunctional tool is sold fully equipped with attachments. Their sizes vary. The main drill bits include a chisel, drill, bit, diamond drill and lance. The longest drill bit available.
The drill is characterized by a spiral shape and is used to drill cylindrical holes. The chisel allows for dismantling, it removes old tiles, plaster and other finishes. The pike has a large diameter and, unlike a drill, is capable of quickly punching holes in concrete floors. The channel drill is designed to create grooves in concrete during the installation of communication systems. The crown is used when it is necessary to drill holes of a certain diameter for switches and sockets.


Boer
This type of attachment differs from conventional drills in that it has the shape of a "tail". Drills are classified as disposable tools, since after long-term use they are practically not subject to renewal and sharpening. The main advantage of the drill is that it is able to clean concrete chips from the holes when drilling. It is recommended to choose this nozzle for drilling deep holes; for drilling through and blind holes in concrete, a drill with a diameter of 6 to 32 mm is suitable.
If it is necessary to drill concrete, the structure of which includes reinforcement, then it is advisable to give preference to nozzles with a diamond coating.



Drill
When choosing drills, it is important to look at their “tail”. This is due to the fact that the design of the chuck and the apparatus often does not correspond to the tail of the drill. The Speed X SDS-max drills work well on concrete surfaces. They are durable, equipped with additional cutting elements and guarantee fast drilling. Most drills also have special channels for removing dust, they are located in the head of the bit, provide accurate direction of shock waves and evenly distribute the impact force.
To quickly and efficiently drill concrete, you should use drills with a diameter of 12 to 52 mm. Their length is different and ranges from 200 to 1200 mm. The choice of this or that drill size depends on the complexity of the work and the depth of the holes. The main feature of the drills is that their spiral part is placed at a certain angle. Thanks to this, the nozzles quickly form holes and remove waste material from them.



Chisel
This tool can have various forms and purposes. The pointed chisel looks like a pyramid with a sharp end or a cone. They dismantle the old finish and punch holes in the concrete floors. The spatula chisel has a curved shape and resembles a screwdriver, only its cutting edge is thin and wide. It is recommended to use it before drilling holes, as the chisel cleans the surface of old concrete layers.


There is also a flat chisel, it differs from the previous types with a pointed tip. A flat chisel is considered the most common in construction work, its cutting edge can be from 1 to 4 cm in size. Moreover, the smaller it is, the more effort will have to be made when drilling. To punch channels in a concrete wall, use chisels of a special shape, which are called a strober.This nozzle is equipped with special wings, they rest on the surface and allow you to adjust the depth of the hole when drilling.

Milling cutter
It is a special type of nozzle, with the help of which you can easily make a hole of any complexity and size, including for socket outlets. If work is carried out on reinforced concrete, then you need to purchase cutters with a diameter of 68 mm or more. However, it is important to consider the surface density and the desired hole depth while drilling. For large and deep holes, cutters with a diameter of 100 to 150 mm are often used.
The length of the cutter also plays a huge role, as standard it is 60 mm, but if you want to make deep holes, then you need to use a tool up to 550 mm long.


Drilling steps
Before you start drilling a concrete slab, you need to prepare not only the cutting tool, but also the workplace itself. The area where work is planned must be completely free of unnecessary items, tools, unauthorized persons and provided with good lighting. Additionally, it is also worth checking with the detector if there are any communication pipes or electrical wiring in the overlap. The drilling site must be thoroughly cleaned. If the concrete surface is loose, mark and expand the point where the future hole is planned before drilling.
Then the puncher itself is prepared. The control of the cartridge is done, a special lubricant is applied to its inner surface. After that, the cartridge is installed and secured well. Since drilling in concrete is a difficult and time-consuming process, you will have to periodically monitor it during operation so that the machine does not overheat.
To reduce the risk of overheating, you should also make sure the tips are sharpened.


Further, all operating modes in the equipment are monitored. To do this, it is connected to the network and the operation is monitored at idle speed. This check usually takes no more than one or two minutes. If there is no vibration and extraneous noise in the device, then you can proceed to direct drilling. If you smell of burning and smoke, you will have to carry out additional diagnostics of the device, finding out the causes of the malfunction.
Then the drill or drill is installed in the intended place of drilling, and the device is connected to the electrical network. It is recommended to start drilling with low nozzle RPM, then the rotation speed should be gradually increased. The tool must be held during operation in the correct position, avoiding distortions. When the hole is filled with concrete particles, the drill is removed and the workplace is cleaned. In the event that during drilling it is necessary to use several nozzles, then they are installed and removed in the off state of the rock drill.


How to work properly?
It is difficult to drill a concrete wall, but with a quality tool and certain skills, anyone can cope with this task. The main thing is to follow all the precautions and rules for operating the punch. Novice masters should take into account a number of points in their work.
- Holes can only be drilled on pre-prepared concrete surfaces. They must be free of dirt, loose layers and oil stains. In loose concrete, you should first expand the point for the future hole. This is necessary so that the drill does not move in different directions and does not slip. Expansion is usually done with a self-tapping screw or a large nail.
- Work with the device in a perpendicular position to the concrete floor. Otherwise, the drill may break when drilling holes.
- With hammer drilling, it is necessary to switch the operating modes in a timely manner. For drilling, the "drilling" option should be enabled, and for "punching" concrete - the "impact" option.


- In the process of work, the perforator and nozzles need to be given a short time to cool. Therefore, it is recommended to take short breaks of 15 minutes.In addition, periodic cooling with water will help protect the drills from overheating.
- For drilling concrete, you must also have a hammer or triangular punch on hand. This is useful if there are rubble and reinforcement in the concrete floor. Metal elements are most often processed with a drill for metal, but crushed stone can only be removed with a punch.
- Drilling holes in a solid concrete wall is easy using a simple hammer drill without impact mode. To do this, in the process of work, you will have to periodically insert the punch, hit it with a hammer and gently turn it in the hole, then continue drilling.
For this kind of work, it is important to have a drill bit made of carbide.



- The workplace should be kept clean, therefore dust and concrete chips should be removed from the hole after each drilling. If this is not done, then the contamination will interfere with the work of the drill, and the process will be delayed. Dust can be removed either with a brush or with a vacuum cleaner.
- Sometimes the drill can get stuck. In this case, it must not be shaken. The bit is carefully detached from the hammer, then the largest drill is taken and the tip that is stuck is released. In this case, you must try not to touch it.
- In concrete surfaces, holes should be made 10 mm larger than the intended dowels. Thanks to this, they will better fit into the ceiling.


Recommendations
When working with a puncher, it is important to take into account certain rules. When drilling concrete, experts recommend using a coolant or special lubricant. Before starting work with a long drill, it is advisable to work with a shorter drill. Often the concrete surface has a loose structure, therefore, in order to prevent it from crumbling, processing is recommended in the "drilling" mode. At the end of the work, the tail of the drill must be cleaned of dust, for this it is wiped dry with a soft cloth and lubricated with machine oil or grease.

To extend the life of the hammer drill, it must be used according to the instructionsprovided by the manufacturer. In addition, regardless of the amount of work, you should take short breaks to cool the case. If the gearbox overheats, the device will quickly fail. The cooling device must not be immersed in water. Increased pressure on the concrete being processed is also not allowed, this will help to increase the impact force of the device, but can lead to quick breakage of the nozzles.
In the next video, you will find tips for using the punch.
The comment was sent successfully.