How to disassemble and repair a rock drill?

Every real man has a puncher at home or in the garage. But whatever your "golden" and neat hands, sooner or later your loud "assistant" breaks down. The repair of such a device is rarely located near the house, so often the best way is to try to fix it yourself.
In this article, we will look at how to quickly determine the cause of the malfunction and fix the equipment at home.

Features of maintenance of the punch
Any deviation from a good job is already a warning that something is wrong. If your instrument does not work as before, but with some errors, then you can always find out the reason for yourself. But for this you need to understand how the perforator works from the inside.


When buying a device, especially an expensive and branded one, the client first of all pays attention to quality. After all, I really want the device to serve for a long time. But regardless of the price and manufacturer, there are always two parts: electrical and mechanical.
The part of the breakdown will depend on the features of the repair.
When disassembling and repairing a punch with your own hands, you need to know the characteristics of the apparatus, how the engine is installed: vertically or horizontally.

If the rotor is installed vertically, then such rock drills are called barrel rock drills.... Their peculiarity is that they work on the principle of a crank-connecting rod percussion mechanism. Such a tool is heavier, but at the same time it is powerful. It should be borne in mind that because of this, the vertical rock drill needs more lubrication to keep it in order.
Rotary hammers, where the engine is horizontal, are less fussy and more convenient to use. Such a tool is ideal for home renovations.

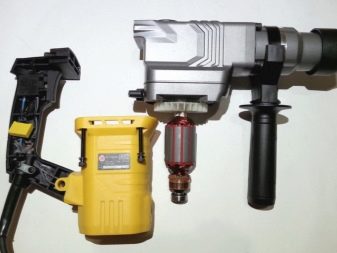
When you know all this, it's time to understand what is inside. The electrical part is always closer to the place where you need to hold the hammer drill. It houses the "heart" of our striking mechanism - the engine. In addition, this part contains a power button, structures that absorb interference, and a power cord.
The mechanical part includes the percussion mechanism itself, the gearbox and the cartridge. These are the main details of this part. Sometimes new mechanisms are added to improve the model: different modes of operation, a vacuum cleaner and other additions.


Identifying faults
As noted, some problems can be identified immediately. The main thing is to understand in which part of the puncher the problem was formed.
If you smell a burning smell, the instrument has become too noisy or heats up quickly, there is a grinding noise, or smoke already appears, then these are signs that your repair tool is not working properly.
If you understand that the problem is in the electrical part, then be careful. Check that the rock drill is de-energizedotherwise, the repair of such a tool is dangerous not only for itself, but also for your health.
When the hammer drill refuses to turn on, the failure is electrical and you should check for broken wires.... In this case, first determine where exactly the wire broke, then replace it or shorten it at the break.


If the perforator is loaded too much, the extinguishing mechanism may burn out.... Then you will have to replace all burnt parts.
Take breaks from work to prevent this. For example, stop the appliance after every 20 minutes of continuous operation.
If something sparkles inside, then most likely the problem is in the brushes.... They either do not fit tightly to the anchor, or moisture got there and they began to oxidize. Then the best solution would be to replace them.
If the water has already hit the anchor, then you will have to carefully dry everything, but so as not to spoil the winding as well. To do this, use a cotton swab and alcohol.


An additional sign of brush problems is smoke.... This means that these devices are worn out, and the wires are in contact with the anchor. In this case, the brushes should be replaced with new.
Besides, smoke may mean that there is a malfunction in the motor - it sticks, heats upand smoke appears from it. Malfunctions in the mechanical part are in most cases determined by ear. Noise and grinding noise are the main symptoms of a problem in this part of the hammer drill. Fixing troubles here is much easier and safer for your health.


The most common sign that a problem has occurred is a decrease in productivity. Often it is because of the breakdown of the switch that the hammer drill stops hammering. It is worth replacing the power button for further work.
Another possible reason for the deterioration of the level of performance may be the contamination of the device. To correct the problem, the instrument must be cleaned and lubricated.
To prevent a malfunction, after each use of the tool, it is necessary to wipe at least its surface from dust and pieces of brick.


In addition, problems often arise with the striking mechanism itself. But to determine the exact cause, it is necessary to examine the entire partas the problem can be in the drill or in the small iron ball inside the chuck. Therefore, to repair the percussion mechanism, one should look for the cause in the entire mechanical part of the device.
Disassembly algorithm
Do not forget that the hammer drill can only be repaired in a de-energized mode! Due to the similarity in the internal composition of the main part of the hammer drills, the tool parsing scheme is approximately the same. Start disassembling the device, if no external faults are observed, it should be from the cartridge.
Further, the following parts are sequentially removed:
- rubber boot;
- retaining ring (using a screwdriver);
- plastic boot;
- washer;
- plate;
- spring;
- small metal ball.
When the last four parts are worn out, the barrel cannot stay in the cartridge and begins to fall out. To fix this, it is necessary to replace the broken part and clean and lubricate the rest of the parts.

The next part in the parsing algorithm is the body... The first thing to do is remove the switch. To do this, it must be transferred to the "Impact" state, indicated by the drawn hammer. Then, holding the button on this mechanism, turn until it clicks.
To complete the removal, take a screwdriver, use it to pry the switch and remove it. In order to get to an electrical fault, it is worth removing the plastic case.
This is not difficult, usually it is held along the perimeter with screws. In the event of a problem in the gearbox, it must be dismantled and the damaged bearings must be replaced.

Replacing the button and brushes
The malfunction of the brushes and the need to replace them is indicated by a pronounced burning smell emanating from the operation of the perforator. Brushes wear out for long periods of time, sparkle, and may even start to burn. In this case, they should be replaced.
The brushes are in the electrical part, so after removing the plastic case and disassembling to the brush assembly, it is necessary to get the old brushes out from under the lock and replace them with new ones. Now, some manufacturers immediately put spare brushes in the kit, which simplifies the task for the average user.

It is much easier to change the switch button, but it does not come with an additional kit. It is enough to disconnect the damaged button in the disassembled case, and put a new one in its place.
Sometimes the problem with the switch is not so serious, and some technicians advise you to simply rotate the button 180 degrees and continue to use. But this life hack only helps if the problems are minor.

The device and repair of the percussion mechanism
It has already been mentioned that rock drills differ in the location of the engine in them. And, therefore, such devices will have different repair schemes.
In a pistol hammer drill, the motor or rotor is horizontal. And the most common cause of failure is bearing wear or seizure. The wear problem can be solved by replacing parts, but bearings in each rock drill are often individually arranged.

The peculiarity of the barrel rock drill is the vertical position of the rotor. In such instruments it is often necessary to check parts for wear and to replace them, otherwise it will feel like the punch has broken.
Particular attention should be paid to lubrication, since the hammer drill is a powerful device, and parts, due to the lack of a sliding coating, become unusable much faster.

Elimination of other breakdowns
In addition to problems with buttons, brushes and impact mechanism, there are a number of other malfunctions that can be repaired and repaired at home. And this will also require the ability to disassemble the puncher.
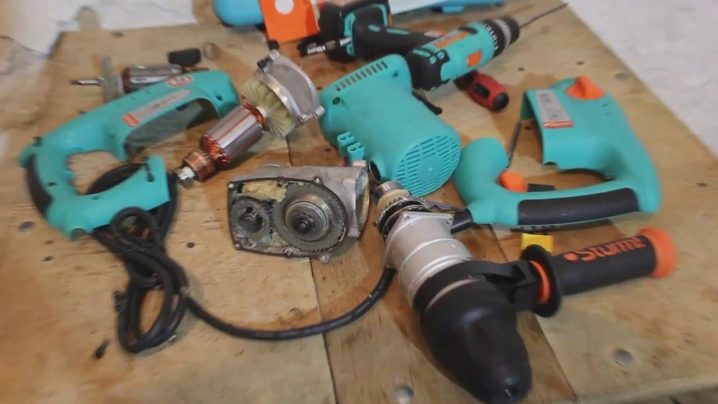
Stuck drill
If the drill does not hold in the chuck, then it is worth paying attention to the small metal ball. Replace it or the retaining spring... If the drill gets stuck, the problem is the lack of lubrication.
When the drill is not inserted or pulled out, the problem lies in the small details. Disassemble the mechanical part and see the cause of the breakdown. As in the case when the drill is dangling in the chuck, this may be due to a defect in the ball.

Stopped working
If your hammer drill starts to hit worse, it is possible that the problem is in worn gear teeth on the moving part of the engine. This could be due to heavy loads or interruptions in the operation of the clutch. As with other defective parts, they must be replaced.
Or there is a malfunction of the switch buttons, then it is worth checking the integrity of the wires.

The drill does not hold
If at work you feel that the chuck does not hold the drill, this means that the hammer drill is defective, and the best option would be to turn it offas continuing to work is hazardous to health.
The problem is most likely not in the drill, but in the chuck.... As in previous cases, the only way out is to disassemble and determine the cause of the breakdown.

The ratchet is triggered
This ratchet is called a clutch, it protects you from breakage and is a warning signal that the hammer drill is reaching its limit. But this signal does not prevent you from continuing to work, you just need to take breaks and give the device a rest. Usually, such problems only occur in cheap devices..
It is almost impossible to repair the clutch with your own hands without professional training, and repairs in the service are expensive. Therefore, it is more profitable to buy a new high-quality rotary hammer.

Pike takes off
While working with a hammer drill, the brick is broken into small pieces, which then end up everywhere, especially inside the tool. The reason for the departure of the peak can be contamination of the cartridge with fragments of bricks.... In this case, the way out of this situation is to clean the cartridge.

Preventive measures
After we have sorted out the main reasons for the malfunction of the hammer drill, as well as ways to repair breakdowns, several points can be highlighted, how to extend the life of your percussion instrument.
- In case of frequent repairs, the rotary hammer should be cleaned at least once a month.
- Remember to lubricate the parts of the device regularly.
- To prevent malfunctions, you should choose a quality rotary hammer. Cheap devices only work a couple of times a year.
- So that the mechanism does not overheat and the brushes are not erased, it is worth taking breaks from work. For example, after use for 20-30 minutes, let yourself and the punch rest for 10 minutes.
- Last but not least, after you are done, do not leave the hammer drill dirty. Be sure to clean it after each use and put it in a special drawer.

By following these little tips, you can extend the life of your hammer drill, which will save you both time to repair it and money on buying a new tool.
Do not be afraid to disassemble it, it may have stopped working due to a small malfunction that you can solve with your own hands.
And remember about the precautions, because this is an electrical device, which means you should handle it carefully.

For information on how to fix a punch with your own hands, see the next video.
The comment was sent successfully.