All about hollow core slabs
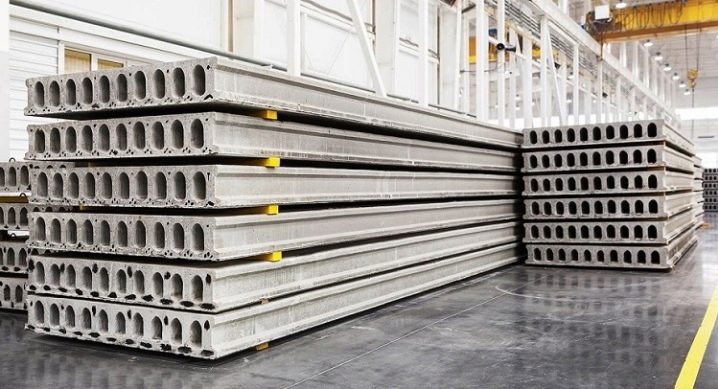
Floor slabs are a reinforced concrete type of structure, which finds its application during the construction of a private house or industrial facility. They are used to separate the number of storeys of underground, aboveground boxes of residential buildings, public and industrial buildings. These structures are characterized by a large number of advantages, among which are high bearing capacity and low cost.
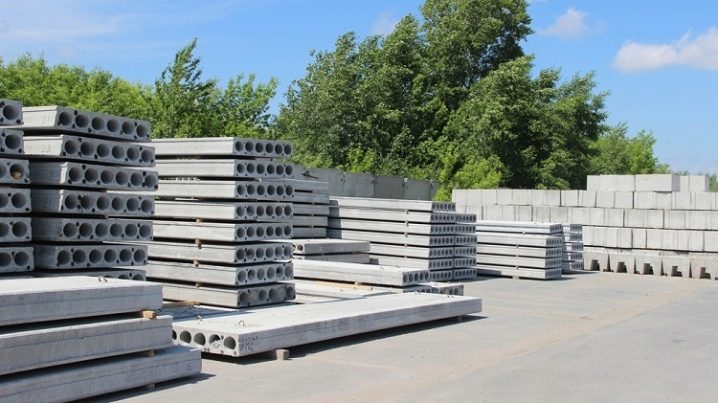
Peculiarities
The hollow core slab is made of strong concrete combined with high quality steel reinforcement that can be prestressed. This design has the shape of a rectangle, it is equipped with through air round chambers. This feature determines the lightness of hollow core slabs, so they can reduce the overall load on the foundation and walls. Moving them using the technique does not cause discomfort, since there are special loops for this.
The construction of hollow slabs is lighter than that of solid ones, but at the same time their strength and reliability are at a high level. The presence of air cavities in this product contributes to heat and sound insulation. The production of slabs of this type is carried out in two ways:
- without formwork, which involves the use of vibration rammers;
- pouring stationary metal formwork with a concrete mixture, after which the poured structure is sent for vibration compaction and heat treatment.
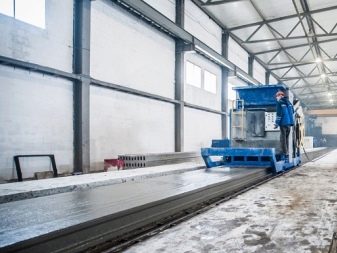
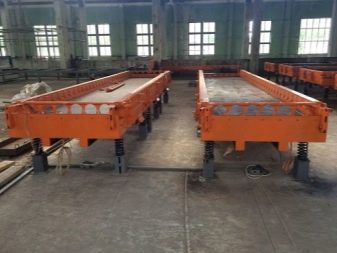
Due to the presence of cavities in the form of a cylinder, the following operational capabilities of the plates are improved:
- increased strength;
- improved thermal insulation;
- facilitating the procedure for laying communications by engineers;
- reducing the influence of external sounds.
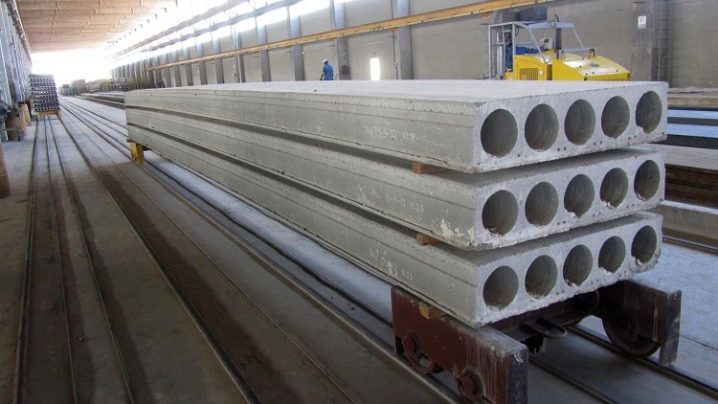
Advantages and disadvantages
When a structure is being built, you want to save not only finances, but also your time, while maintaining the quality of the structure. In order for the structure to be reliable and safe, you should not save on materials. The best option for floor slabs is hollow structures, which are characterized by the following advantages:
- strength, safety and long service life;
- moisture and liquid resistance;
- fire resistance up to 3 hours;
- simplicity and speed of installation;
- the possibility of using it as an option for a load-bearing wall.
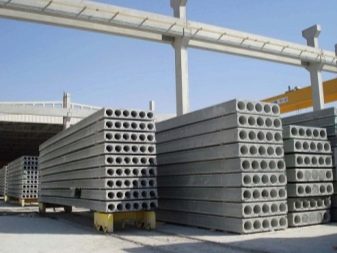
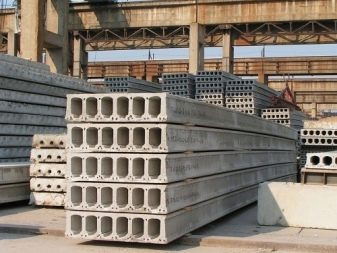
If we compare solid slabs and hollow slabs, then the latter have the following advantages:
- high level of heat and sound insulation due to the presence of air inside;
- simplicity of communication and, as a result, reduction of time for finishing processes;
- the possibility of using in seismic zones;
- high level of bearing capacity;
- ease of transportation and installation;
- an increase in the useful volume of the structure being erected;
- the floor can be loaded immediately after installation without concrete screeds;
- low cost, which is based on low consumption of concrete and reinforcement.

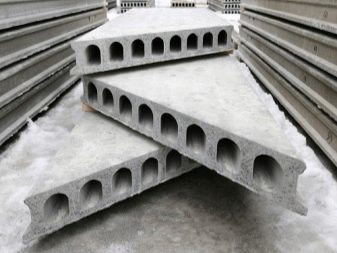
There are practically no disadvantages of hollow floor structures, but the following features can still be attributed to the disadvantages:
- limited availability, which lies in the fact that today a small number of companies are engaged in their production;
- when installing plates of this type, it is necessary to use special heavy equipment.
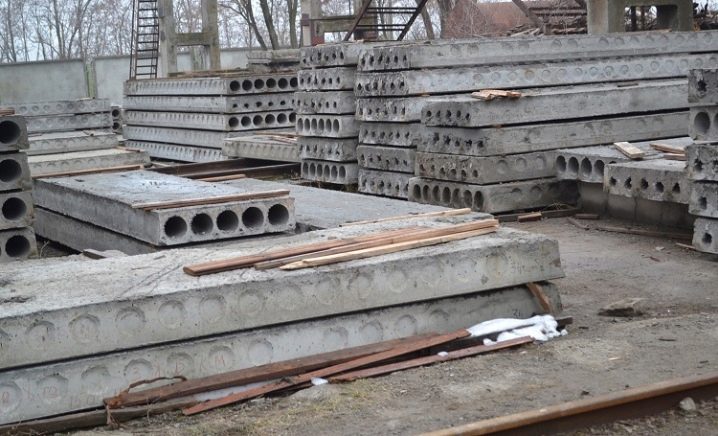
Specifications
Its price will depend on the size of the hollow core slab, in addition, parameters in the form of length, width, weight are taken into account.
Structures of this type can be characterized by the following dimensions:
- slab length - 1.68-12 m;
- width - 0.98-1.48 m;
- thickness of the structure - 22 cm;
- the diameter of the plane of the cylinder - 11.4-15.9 cm;
- concrete grade - M200-M400;
- the amount of concrete and reinforcement used in the production of future floor foundations;
- weight - 0.75-5 tons;
- the indicator of the calculated efforts - 800 kg / cm2.
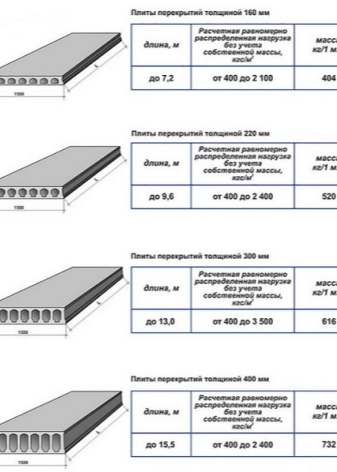
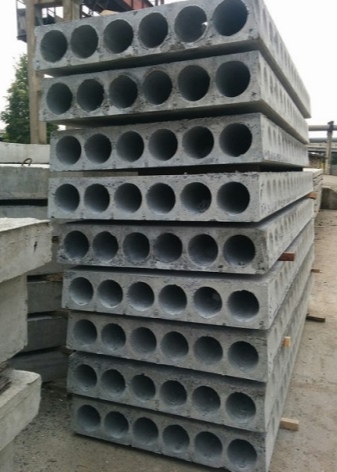
It is worth remembering that during the production of a slab with voids, the technology of its manufacture must be fully observed. Only in this way can you be sure of the reliability of the products with the help of which the interfloor base is formed.
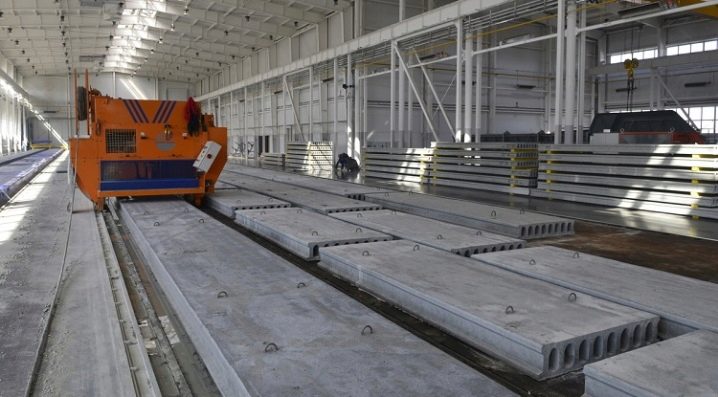
Varieties of designs.
- PC characterized by a standard thickness of 22 cm, the presence of through cavities of a cylindrical shape. Slabs are made of reinforced concrete, which has a class of at least B15.
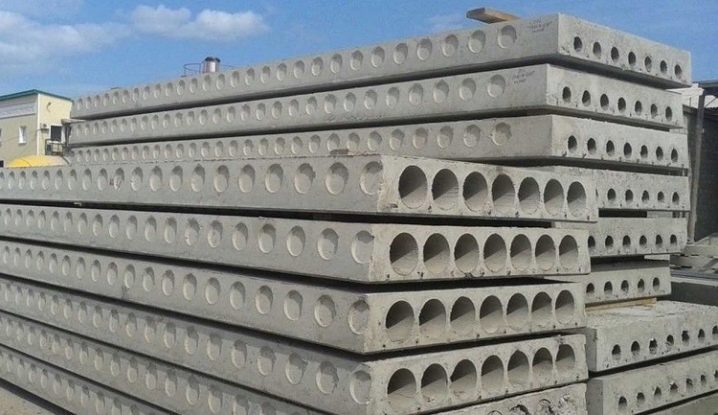
- PB - this type of product is obtained using a non-formwork method using a conveyor. In the manufacture of these structures, a special method of reinforcement is used, with its help, cutting off occurs without loss of strength. Since the slabs have a flat surface, the subsequent finishing of floors and ceilings is easier.
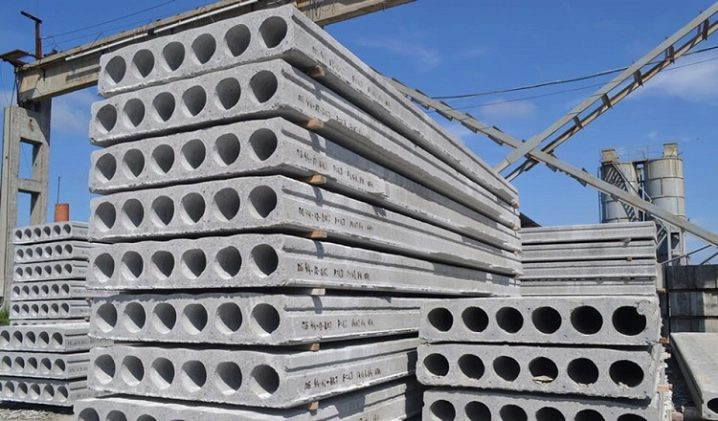
- PNO - a lightweight type of structure that is produced by the formless method. The difference from the previous type can be called a smaller thickness of 0.16 meters.
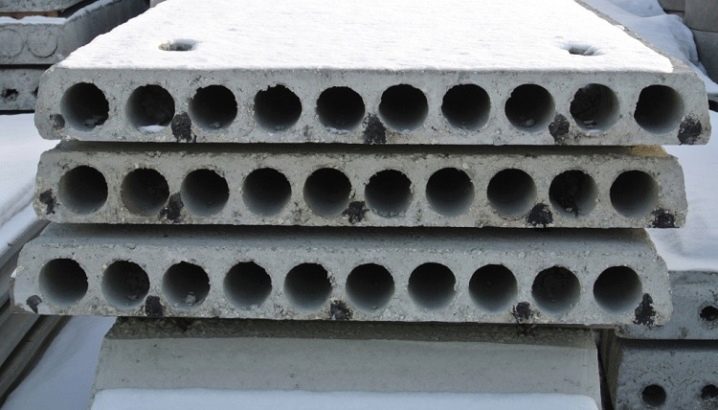
- HB - internal type of flooring, made of reinforced concrete of class B40, with reinforcement in one row, which is prestressed.
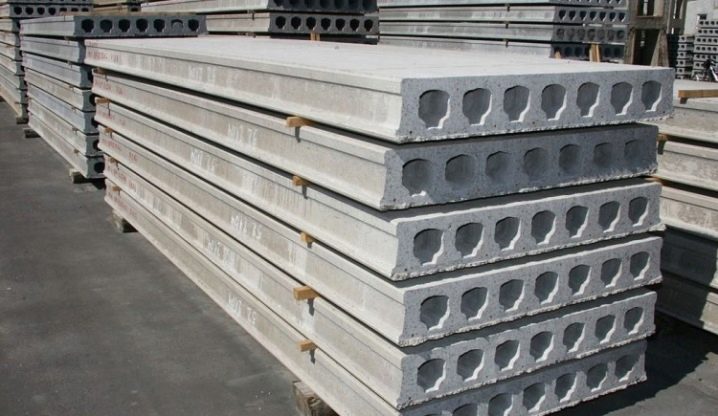
- NVK is an internal type of flooring that has two rows of stress reinforcement and a thickness of 26.5 centimeters.
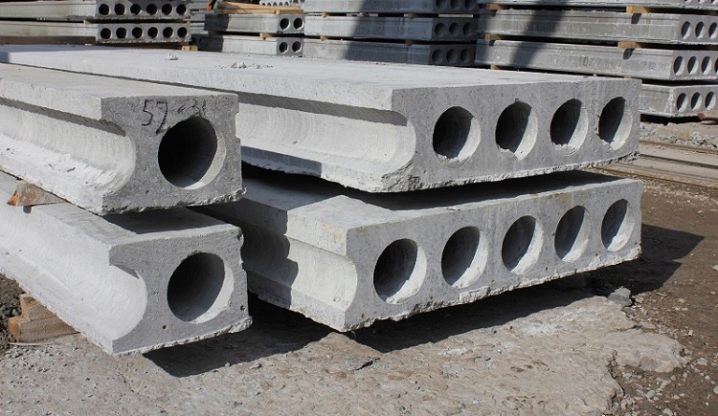
In the manufacture of floor structures, prestressed reinforcement is subjected to compressive stress at the points where the greatest tension will take place. After passing this treatment, prestressed hollow-core structures become stronger and more stable. The characteristic of such devices contains the designation "prestressed plate".
The standard dimensions of 0.22 m thick circular hollow-core slabs (PC, PB, NV) and 0.16 m (PNO) are characterized by a length of 980-8990 mm, which is recorded in the marking as 10-90. The distance between adjacent dimensions is 10-20 centimeters. The width of a full-size product is 990 (10), 1190 (12), 1490 (15) millimeters. So that the consumer does not have to cut the products, additional elements are used, the width of which is 500 (5), 600 (6), 800 (8), 900 (9), 940 (9) millimeters.
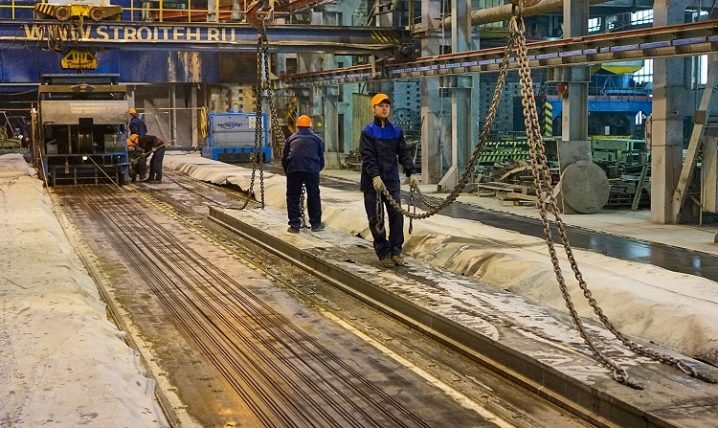
PBs are characterized by a length of up to 12 meters. If this figure is more than 9 meters, then the thickness must correspond to 22 centimeters, or the bearing capacity of the slab will be less. Products of the NVK, NVKU, 4NVK series can be characterized by dimensions that do not fit the standard ones. The distance between the slab voids is assigned using the equipment parameters that are used in the factory. According to GOST, the distance should be less than the following indicators:
- for plates 1PK, 1PKT, 1PKK, 2PK, 2PKT, 2PKK, 3PK, 3PKT, 3PKK and 4PK - 185;
- for structures of type 5PK - 235 millimeters;
- 6PC - 233 mm;
- 7PC - 139 mm.
The optimal number of voids in this design is 6 pieces.
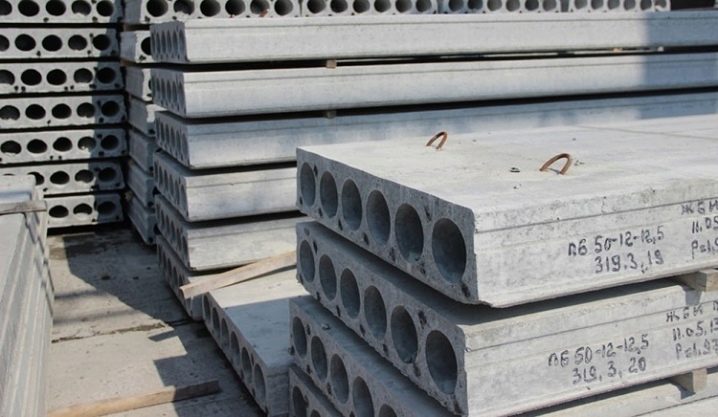
Marking
Each type of hollow core slab is equipped with markings that meet quality standards. Thanks to this, the customer and the designer can determine the required parameters. At the end of the structure, the consumer can see the marking, the date of manufacture, the weight and the OTK stamp.
In the standard marking, there are several letters that designate the series, as well as 3 groups of numbers that determine the dimensions, the carrying capacity. Both groups are in the form of two numbers, which are considered to indicate the length, as well as the width in decimeters. These indicators are rounded up to whole numbers. The last group is presented in the form of a single figure, it determines the uniformity of the distribution of loads in kPa.
This indicator is also rounded up.
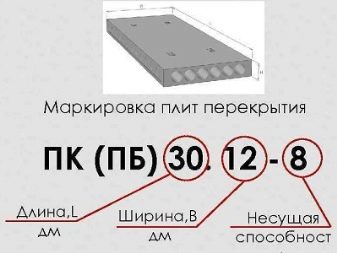
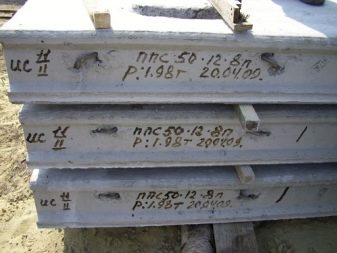
Example of marking: PK 23-5-8.Its decoding is as follows: the plate has round voids, it is characterized by a length of 2280, a width of 490 millimeters, while the structure has a bearing capacity of 7.85 kPa. There are such types of products that are equipped with markings, supplemented by Latin designations, which determine the types of rods. One of the examples of marking: PK 80-15-12.5 means that the frame was made from stressed reinforcement. As a supplement, the following designations are available on hollow structures:
- t - heavy concrete;
- a - the presence of inserts for the seal;
- e - formation using the extrusion method.
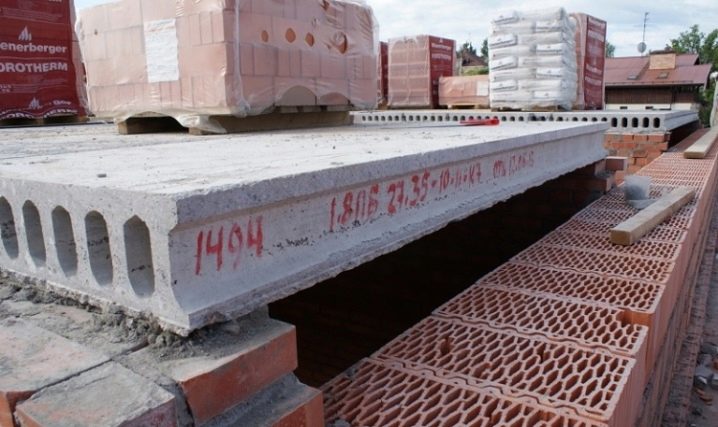
What kind of load can they withstand?
The load-bearing capacity of floor slabs is determined by a standard that regulates the observance of manufacturing according to the technology that is applied at the time of their production. The calculation of the permissible maximum load of reinforced concrete elements is needed to find out what indicator the structure will withstand, and thereby avoid its destruction. The load on a hollow floor structure can be statistical and dynamic. The first includes those elements that are located or attached to the plate. Anything that moves around the structure is considered dynamic.
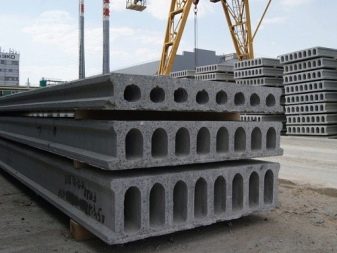
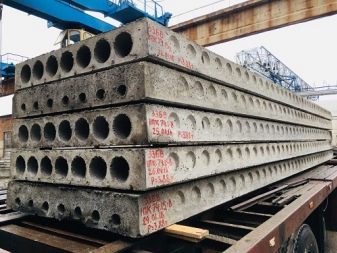
Loads can also be evenly and unevenly distributed. For example, for a building where people live, a uniformly distributed load is calculated, which is determined in Newtons per meter or kg / cm. A common slab with voids is calculated according to the distributed load, which is 400 kg per m2. To this indicator, it is necessary to add the mass of the structure, which is about 2.5 centners, screeds and ceramics, which weigh about 1 centner. The calculated mass must be multiplied by the safety factor (1.2). As a result, 900 kg / m2 comes out. There are also specially developed documents that allow you to accurately calculate the load on a reinforced concrete slab that has reinforcement.
To calculate the optimal load, it is necessary to know the weight of all elements that will affect its effect., namely, cement-sand screeds, gypsum concrete partitions, flooring masses and thermal insulation. After summing up all the above indicators, it is necessary to divide the number by the number of panels that will be present in the building. In the same way, you can calculate the maximum ultimate load on each of the hollow structures.
Many panels that are commercially available have a standard bearing capacity of 800 kg / m2.
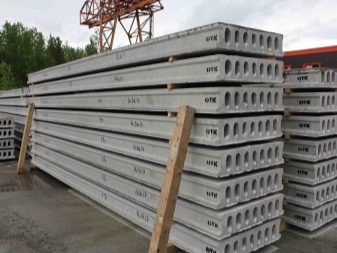
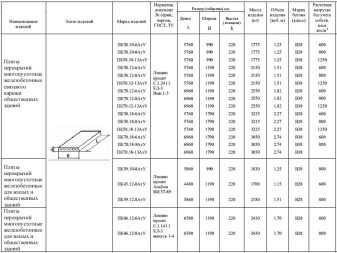
Installation rules
To carry out a reliable installation of hollow-core floor slabs, it is worth strictly following all the rules. If the support area is insufficient, the walls may deform, and in a situation with an excess of area, an increase in thermal conductivity is possible. When installing slabs of this type, it is worth taking into account the maximum support depth:
- for a brick structure - 9 centimeters;
- for aerated concrete and foam concrete - 15 centimeters;
- for steel structures - 7.5 centimeters.
In this process, it should be borne in mind that the depth of embedment of the panel in the wall should not be more than 16 cm for a light block and brick building, as well as 12 cm for a structure made of concrete and reinforced concrete.
Before starting the installation of the slabs, the marginal voids must be sealed with a light concrete mixture to a depth of 0.12 meters.
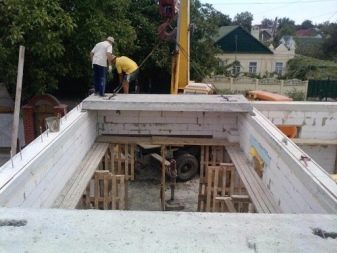
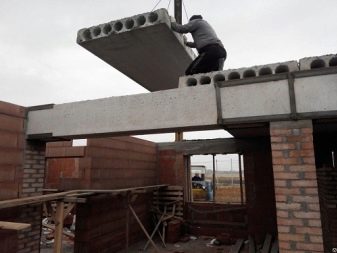
It is strongly not recommended to install boards without using mortar. A layer of solution of at least 2 millimeters is laid on the working surface. Thanks to this measure, the load on the wall is transferred evenly. When equipping the slabs on a fragile wall, it is necessary to make a reinforcement procedure, thanks to which there will be no bending of the blocks. In order to reduce the thermal conductivity of the floor slabs, it is worth insulating the structure from the outside.
When buying hollow-core floor panels, you should pay attention to their quality, appearance and availability of certificates, since safety will depend on them. The use of hollow core slabs provides a small load on the entire perimeter of the structure, guarantees high strength and reliability of the structure.
This type of structure contributes to a lower draft of the building than when using full-bodied options, besides, the price for them is acceptable.
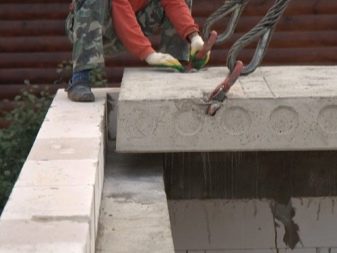
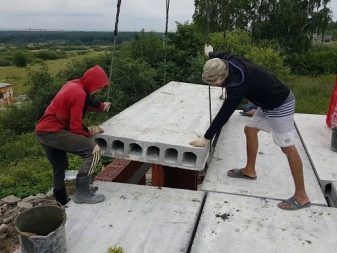
You can learn how to properly lay floor slabs from the video below.
The comment was sent successfully.