Precast-monolithic floors: features, types and installation
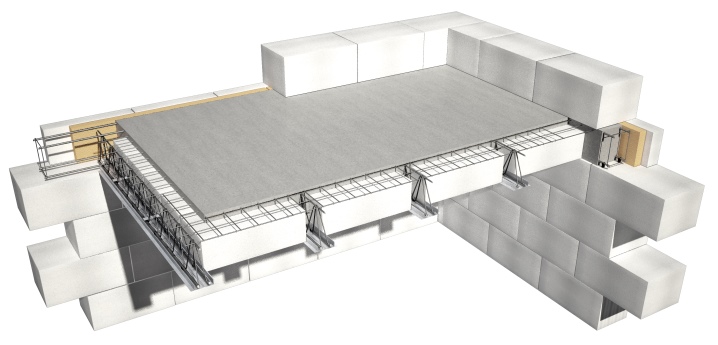
Ceilings used in buildings of both low-rise and multi-storey types must meet very serious requirements. Perhaps the best option in many cases is a precast-monolithic solution, the history of which was unreasonably interrupted in the middle of the 20th century. Today it is gaining popularity again and deserves careful study.
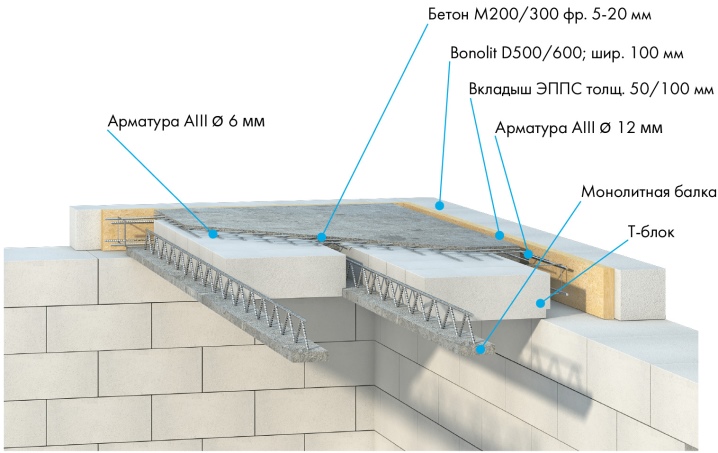
Advantages and disadvantages
By its nature, a precast-monolithic floor is formed by a beam-block frame. In the case of competent execution of work and taking into account all the subtleties, the structure can achieve a very high strength. The most important advantage is increased fire resistance, since the presence of wooden parts is excluded. Additional advantages of the precast-monolithic block are:
- absence of seams during installation and pouring;
- maximum leveling of floors and ceilings;
- suitability for the arrangement of interfloor gaps;
- suitability for arranging attics and basements;
- no need to use powerful construction equipment;
- elimination of the need for reinforced insulation;
- reduction in construction costs;
- the ability to do without several layers of screed, laying floor coverings directly on the overlapping structures;
- maximum convenience of laying electrical and pipeline communications;
- excellent compatibility with walls of bizarre geometric shapes;
- the ability to adjust products to the required dimensions directly on construction sites.
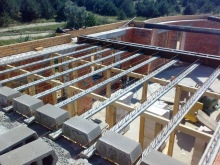
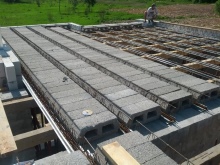
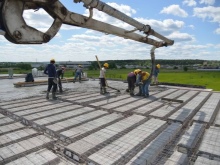
Precast monolithic structures are quite often used in the process of reconstruction work without dismantling the roof. It is easy to purchase blocks of different shapes and other components in a completely finished form.
Among the minuses, it is worth noting that prefabricated monolithic flooring is still more difficult to make than a purely wooden structure... And the costs are growing; however, the technical advantages generally outweigh.

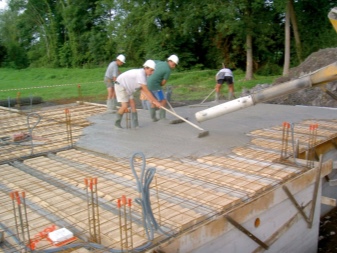
Types
In most cases, precast-monolithic floors are formed in the form of foam concrete slabs. The difference from other structures is that cranes are needed only in the process of lifting and laying out blocks on a wall or on a crossbar. Further, any manipulations are carried out manually. The blocks act as a kind of non-removable formwork. In this way, a very sturdy building board can be formed.
Rig-free execution has also become quite widespread.
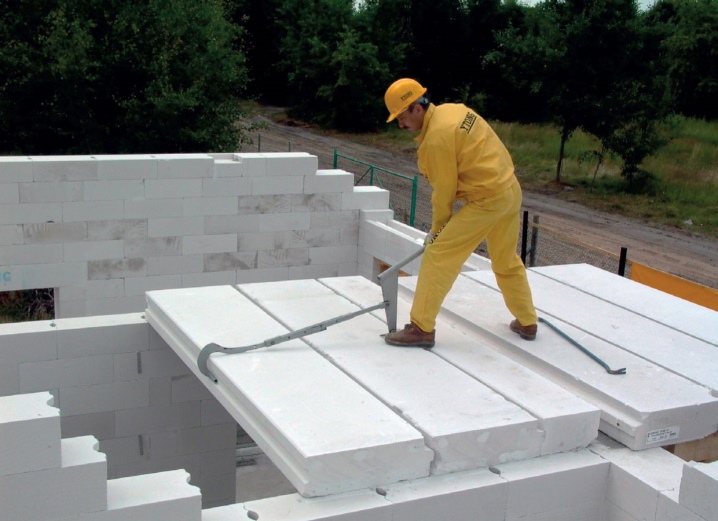
Important: in this version, the plates are laid out only when the capitals are reinforced in full accordance with the project. When calculating for operation, it is assumed that the structure will be used according to a monolithic scheme. The resulting loads are selected and evaluated accordingly.
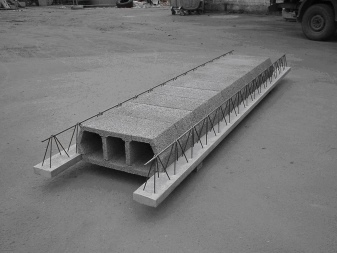
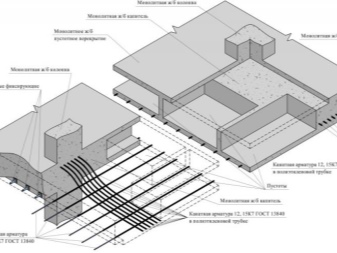
Prefabricated monolithic ceilings with reinforced concrete beam elements with a hidden type of crossbar also deserve attention. Such building systems have appeared relatively recently.
According to their developers, it is possible to significantly reduce labor costs when performing construction and installation work. This is achieved due to the maximum involvement in the process of equipment installed at industrial enterprises. In addition, the covering of the crossbar inside the slab contributes to a better aesthetic perception of the structure.
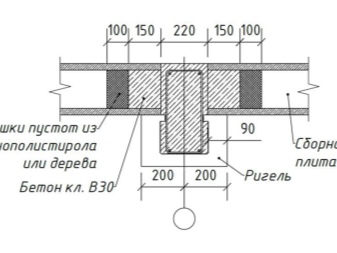
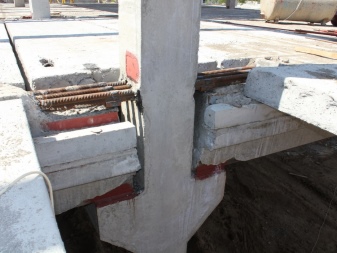
Joints are made according to the rigid monolith scheme; the technology is well developed and allows you to make such joints reliably in the conditions of the construction site.
The floors themselves are formed from slabs containing a large number of voids. Internal crossbars have two functions: some take the bearing load, others act as a kind of mechanical connections. Columns are joined in height using the plug-in method. Inside the columns there are so-called concrete gaps. Crossbars also act as a kind of fixed formwork.
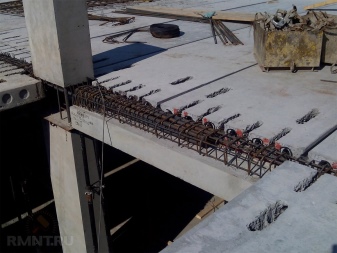
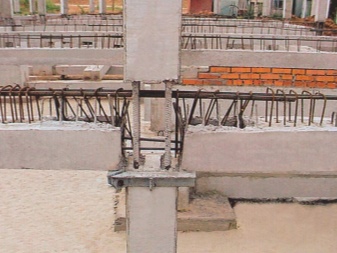
It’s not hard to understand in most cases, precast-monolithic flooring refers to the types of concrete structures... But it can be used not only in capital apartment buildings. There is a great deal of experience in using them in wooden houses.
Modern beams are easy enough to cut into a log, and into beams, and into panels of the SIP format. In addition, if you apply also means for penetrating hydraulic protection, even pipe breakthrough will be practically safe.
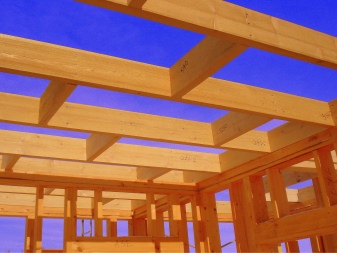
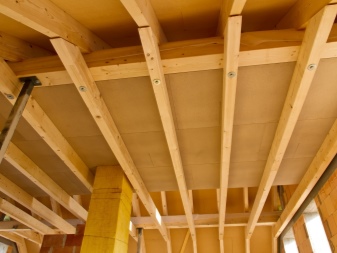
Importantly, there are no problems associated with laying tiles or forming a warm floor. Precast monolithic flooring is much more suitable for such works than the traditional solution made of wood. Separate wood and concrete with plastic wrap. High spatial rigidity guaranteed. But it must be borne in mind that there is no ideal solution for all cases, and you should always consult with specialists.
The use of prefabricated monolithic ceilings for frameless buildings deserves a separate discussion. This technological solution can also be suitable for low-rise buildings. Without fail, the slabs are supported by prestressed reinforcement. The centering elements have a rectangular cross-section, and channels are provided inside them for the passage of this reinforcement. Important: these holes are located at right angles to each other.
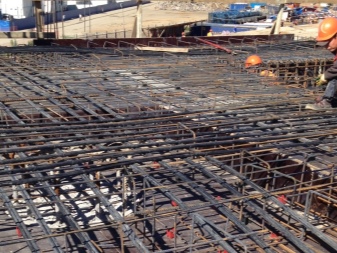
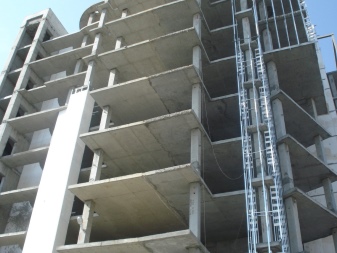
Stamps
The experience of Russian builders shows that there are several brands of precast-monolithic floors that you can trust. A striking example is the products of the Polish company Teriva.
"Teriva"
The delivery sets of its products include:
- lightweight reinforced concrete beams (size 0.12x0.04 m and weight 13.3 kg);
- hollow structures based on expanded clay concrete (each structure weighing 17.7 kg);
- ribs for increased rigidity and effective load distribution;
- reinforcing belts;
- monolithic concrete of various types.
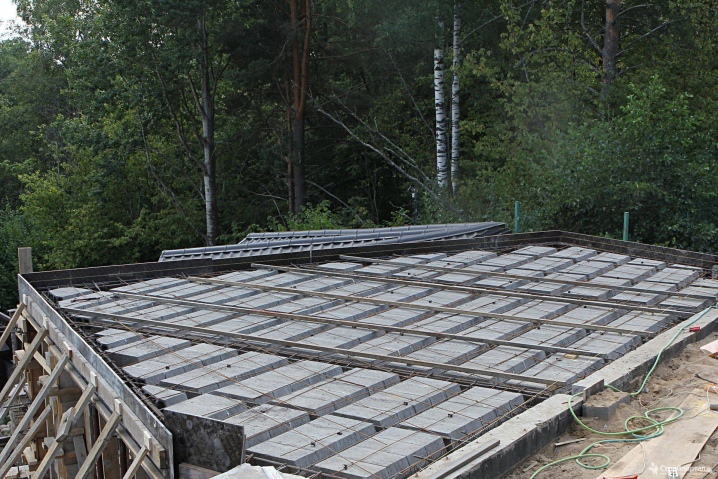
Depending on the specific model, an even load distribution is provided at the level of 4, 6 or 8 kilonewtons per 1 sq. m. Teriva designs its systems for residential and general civil construction.
"Marko"
Among domestic enterprises, the company "Marko" deserves attention. The company has been active in the field of precast concrete slabs since the late 1980s. At the moment, 3 key types of SMP structures have been created (in fact, there are more of them, but it is these that are more popular than other products).
- Model "Polystyrene" is considered the lightest, which is achieved through the use of special polystyrene concrete. This material allows you to do without reinforced insulation and the use of means of increased sound insulation. But one must understand that due to the use of a large fraction of filler, the total strength of the structures is low.
- Model "Aerated concrete" recommended for monolithic buildings with extremely complex configuration. The strength level is 3-4 times higher than that of polystyrene concrete systems.
For these and other types, contact the manufacturer in more detail.
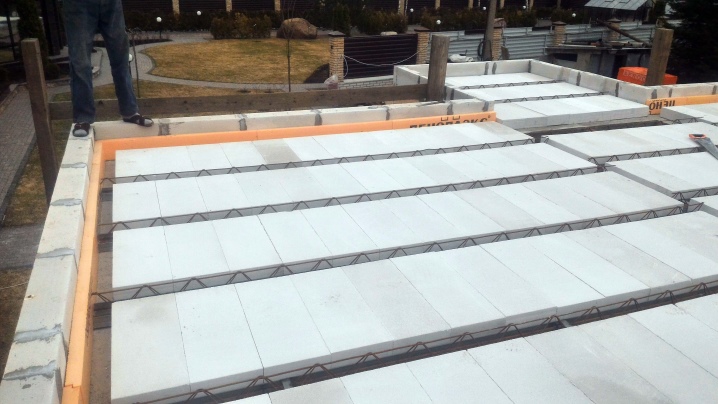
"Ytong"
It is appropriate to complete the review on Ytong precast monolithic floors. The developers assure that their product is perfect for all three main segments of construction - "large" housing construction, private development and construction of industrial facilities. Lightweight beams can be made of reinforced concrete or just steel. Free reinforcement is also used to form a spatial frame.
The length of the beams is selected individually, in accordance with the technical needs. Reinforcement is made at the factory, which allows you to be sure of its quality.
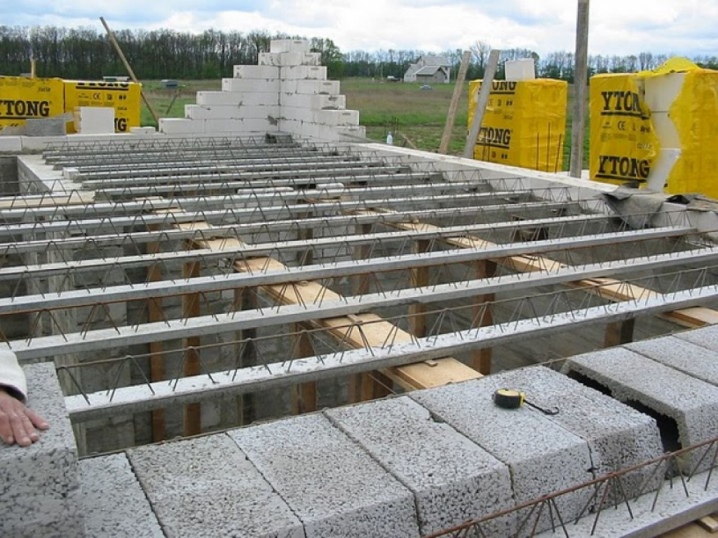
Ytong has mastered the production of beams for spans up to 9 m in length. Permissible total load per 1 sq. m can be 450 kg. Together with standard beams, the manufacturer recommends using branded aerated concrete blocks in the shape of the letter T.
The cross-section, even adjusted for monolithic concrete, does not exceed 0.25 m in height. Monolithic concrete turns out to be a ready-made leveling layer. Weight 1 linear m maximum 19 kg, so manual installation of the beams is quite possible. A small team will build 200 sq. m of overlap during the week.
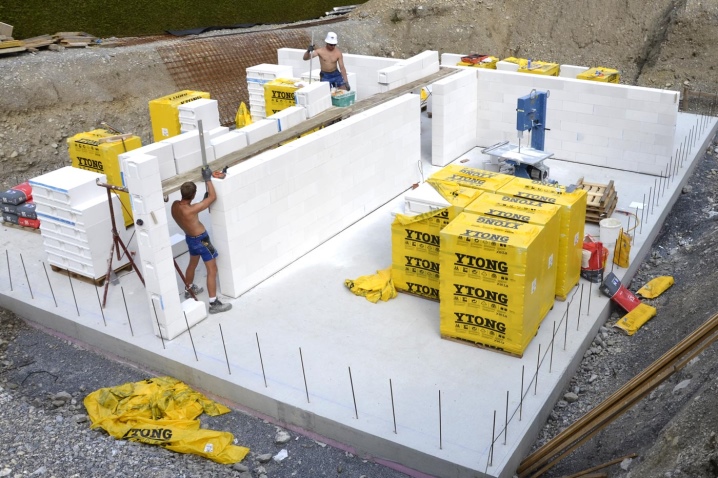
Mounting
Do-it-yourself installation of prefabricated monolithic floors is not particularly difficult, but you must clearly follow the basic requirements and technical requirements.
First of all, it is necessary to put boards with a size of 0.2x0.25 m inside the spans to be processed. They need to be additionally supported with expandable racks of a special sample. Recommendation: in some cases it is more practical to perform this procedure when the layout of the beams has already been completed. Reinforced concrete beams placed in the longitudinal plane are separated by a distance of 0.62-0.65 m.
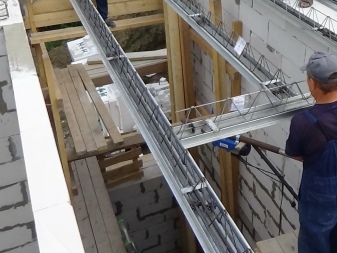
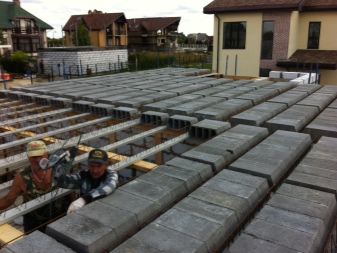
Important: the horizontal lines of the walls are advised to thoroughly clean before laying out the beams. The best way to put them is to use a grade M100 solution. Its thickness can be up to 0.015 m, no more.
The perimeter of the created floor is usually formed from wooden formwork (unless the technology provides for another solution). The blocks are laid out in transverse rows, trying to minimize gaps.
Reinforcement rods are overlapped (from 0.15 m and more). Be sure to remove all dust and dirt that appeared during work. Further, fine-grained concrete is poured from M250 and above. It is watered and carefully leveled. It will take about 3 days to wait for full technical hardening.
About what prefabricated monolithic floors are, see below.
The comment was sent successfully.