Plates PB: varieties, characteristics and properties
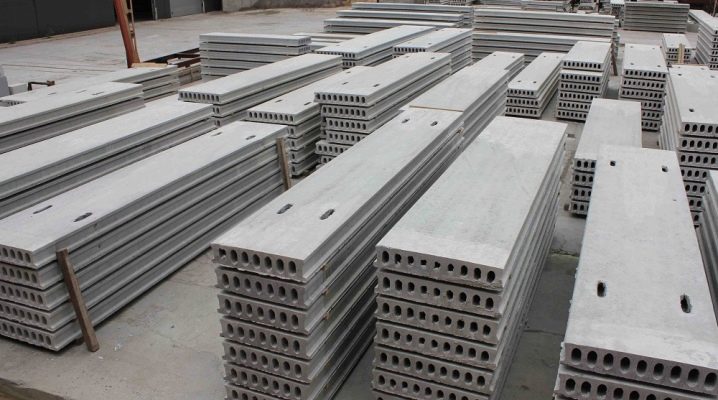
When implementing processes associated with the construction of residential buildings and industrial buildings, high-quality reinforced concrete floors are used, mounted between floors. At construction sites, seemingly identical reinforced concrete products were stacked in piles. It is difficult for an ordinary man in the street to see the discrepancies among them. Only designers and builders are able to confidently separate the hollow (hollow-core) PB floor panels in appearance from similar PC panels.
What are they and where are they used?
Reinforced concrete panels PB are widely practiced in the construction of industrial enterprises, as well as for covering floors of structures and residential buildings with concrete flooring. Reinforced concrete slab PB includes high-strength concrete, pre-tensioned reinforcing ropes, contains oval voids, has dowels on the side edge. The PB panel allows you to create horizontal concrete flooring, withstands high stresses, is designed to retain heat in the premises, and reduces the noise level.
The voids running along the panel allow wiring and also reduce the weight of the structure, thereby reducing the load on the walls of the structure.
Reinforced concrete slabs PB are practiced in:
- frame construction;
- panel housing construction;
- prefabricated monolithic housing construction;
- construction of buildings made of stone, wall panels, blocks, bricks;
- low-rise buildings, construction of household facilities and manor-type facilities.
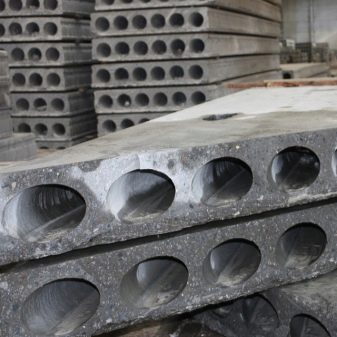
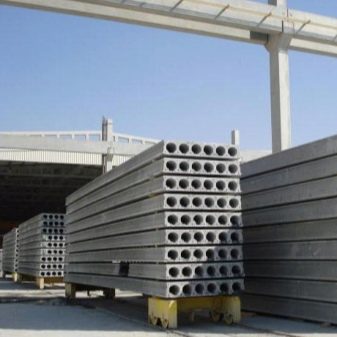
Views
Currently, there are thousands of samples of slab products produced in accordance with GOST 9561-91, which are divided according to the production method (conveyor, aggregate-flow, non-formwork), materials, durability and structure. The most common plates are PC and PB.
Let's consider the features of this product in more detail.
- Floor panels PB are manufactured without formwork on special equipment with the use of vibration compaction. The creation of products of the required length occurs by cutting the concrete in the hardening stage on the conveyor line with the constant movement of the concrete mass. The footage into which the PB panel is cut depends on the needs of the consumer and is at most 12 meters. When inspecting the end part, it is easy to see that the power supply panel is reinforced with ropes. The slabs are reinforced with strong steel reinforcement, which guarantees high strength characteristics.
- The product marked with PC is made by filling with concrete mortar of iron formwork with reinforcing rods and nets. The formed base is subjected to vibration compaction, heat treatment with further extraction of the completely finished structure. Length no more than 7.2 meters.
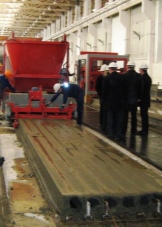
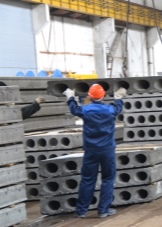
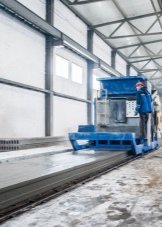
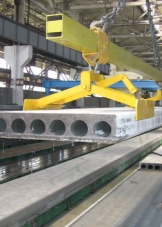
Panels PB and PC have a significant difference associated with the specifics of the production process.
Peculiarities
Floor panels PB, manufactured by permanent formless formation of a concrete mass without the use of formwork, known for their good technical characteristics:
- high soundproofing parameters;
- flawless outer surface;
- the ability to withstand impressive mechanical stress, shock;
- an impressive margin of safety;
- the ability to use in a variety of climatic regions;
- reduced weight;
- good heat-shielding characteristics;
- a wide range of lengths of structures, predetermined by the specifics of production technology;
- the presence, if necessary, of an oblique cut of the end surface;
- resistance to moisture penetration deep into the concrete mass, which activates corrosion.
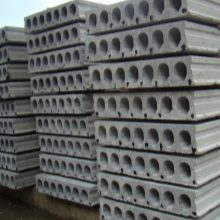
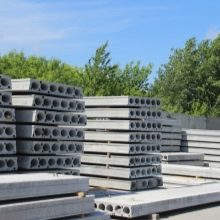
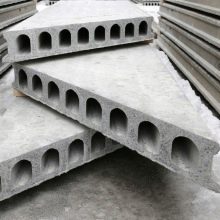
Technical requirements
Panels must be manufactured in accordance with the requirements of this standard and technological documents approved by the manufacturer, according to working drawings of projects of structures (buildings) or standard structures.
It is allowed, by agreement between the manufacturer and the customer, to produce panels that differ in sizes and types from those specified in this standard, subject to the rest of the requirements of this standard.
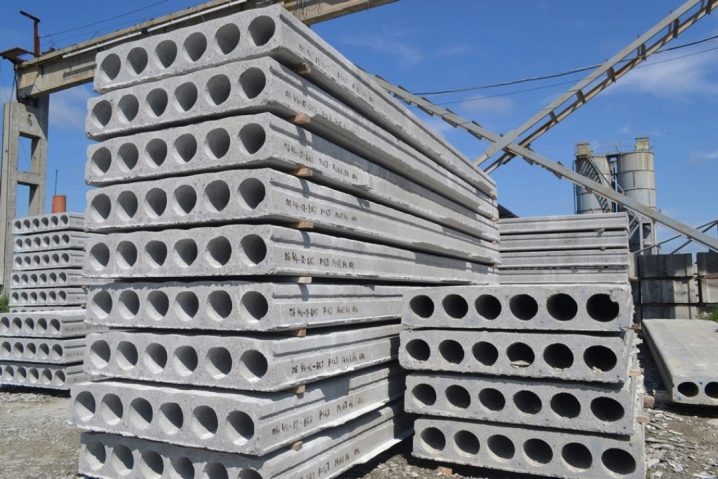
Dimensions (edit)
Plates PB are manufactured according to a relatively new method of forming on stands without the use of molds. The key feature is the use of prestressed reinforcement, regardless of length, and, of course, concrete of class M-400 and higher. The decoding of the marking is similar to the PC.
The width depends on the stand on which the molding is carried out, it is mainly 1.2 meters, but there are paths of other widths. Only a 12-decimeter slab is more convenient for filling the average opening.
The length is quite variable and ranges from 1.8 to 12 meters, it all depends on the height (thickness) of the panel and the load received. Basically, a standard load of 800 kgf / m2 for a thickness of 220 millimeters using this technology can be made up to a length of 9.6 meters. After that, either the ultimate load of the structure is reduced, or the height of the slabs increases.
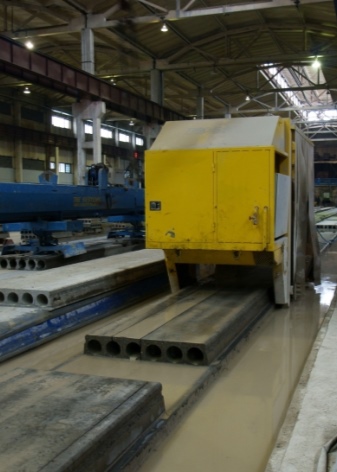
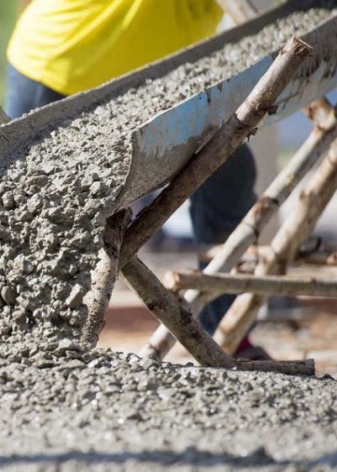
The most common widths of reinforced concrete panels in precast concrete factories are: 10, 12, 15 decimeters, in other words, 1 meter, 1.2 meters and 1.5 meters. The most common parameters for the length of PB panels: from 24 decimeters to 90 decimeters.
The configuration of the holes, the diameter, as well as the distance between them are set by the equipment manufacturer and the project. For any enterprise, these standards are individual. As a rule, round holes have a slightly smaller diameter, for example, 150 millimeters, in order to ensure reliability under the pressure of the wall located above the ends without the use of auxiliary reinforcement.
Reinforced concrete panels with a length of more than 100 decimeters (in other words, more than 10 meters) can be made at the individual request of the buyer and slab drawings, and in addition, PB panels - in other required dimensions.
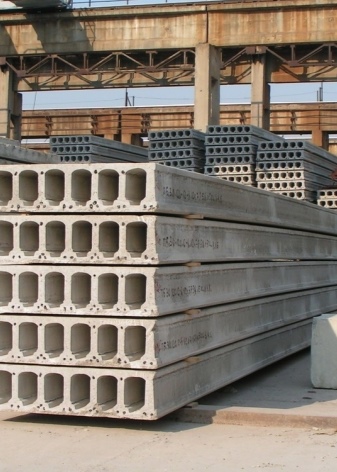
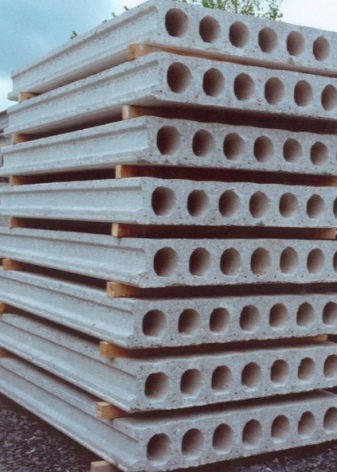
Advantages and disadvantages
PB panels have many positive qualities.
- Due to the presence of voids that dampen vibration processes, good noise insulation properties are maintained, a decrease in the consumption of raw materials, and a lightening of the entire structure. This property applies equally to PC panels.
- Excellent surface quality, uniformity and smoothness.
- Flawless configuration of the finished structure.
- An impressive range of sizes.
- Possibility of purchasing a panel designed for a wide variety of loads. These floor panels are capable of carrying loads from 600 to 1,450 kilograms per m2.
- Prestressing of steel reinforcement in a slab of any length.
- Fire resistance and moisture resistance.
- The ability to cut panels at an angle of 45 degrees to overlap objects of non-standard configuration, which makes it possible to reduce the number of monolithic zones in precast-monolithic floors.
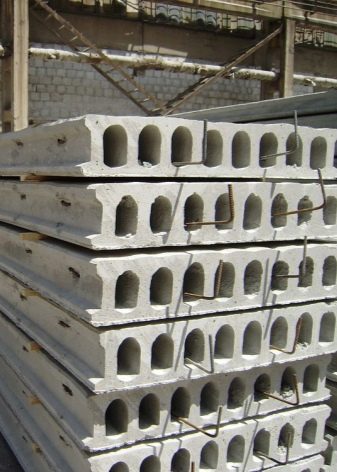
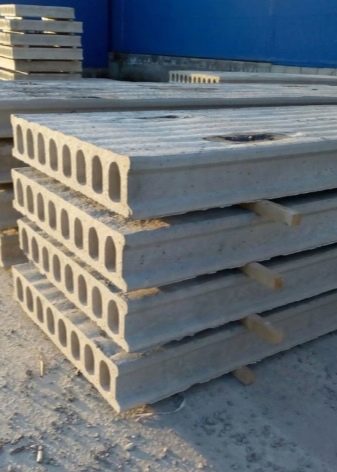
But there are also disadvantages.
- The absence of mounting loops makes it difficult to link the structures together and the procedure for mounting them in the intended position. There is a need to use a roach.
- It is impossible to punch holes in PB panels due to the small width of the holes, which complicates the construction of intra-house communications in comparison with PC plates, the round configuration and rather large diameter of the voids of which will make it possible to punch holes for the pipeline without touching the reinforced partitions.
For comparison - the width of the holes, which have no formwork slabs PB 60 mm, while for the panels of the PK series, the width of the hole is 159 mm. This makes it possible to pass pipes with a diameter of 100 mm through them without complications.
At times, experts allow punching holes for low-rise buildings, but such an operation is undesirable.
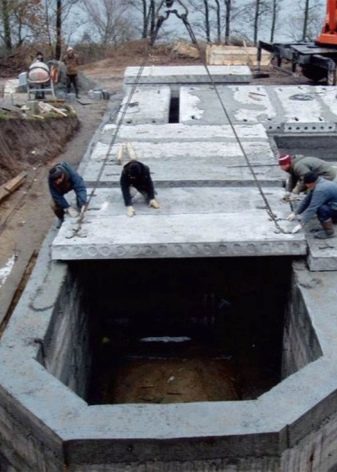
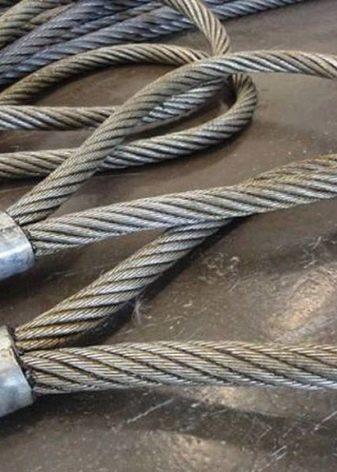
Marking and decoding
Information in the form of inscriptions on the floor structures of the PB means that these are panels that were manufactured at the enterprise of reinforced concrete products according to the latest method of continuous non-formwork molding for the current period using vibration action on the concrete mixture.
Sample marking of reinforced concrete panels PB 63-15-8 and decoding:
- PB - slab produced by formless molding method;
- 63 - length, decimeters;
- 15 - width, decimeters;
- 8 - load in kPa (kilopascals) (kgf / m2 - kilogram / force per square meter);
- panel thickness - 220 mm.
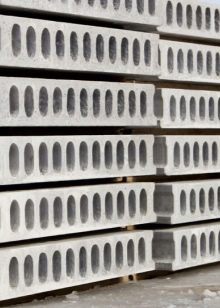
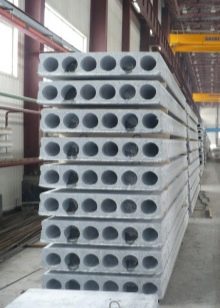
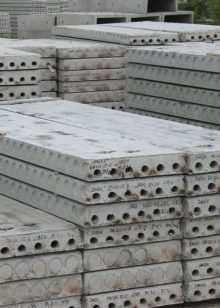
So, we learned that reinforced concrete floors made of hollow (hollow-core) panels of the PB type are the best option for solid construction and a universal solution that will give you the opportunity to build exactly the house you planned.
For information on the properties of PB slabs, see the next video.
The comment was sent successfully.