Floor slabs: types, applications and sizes
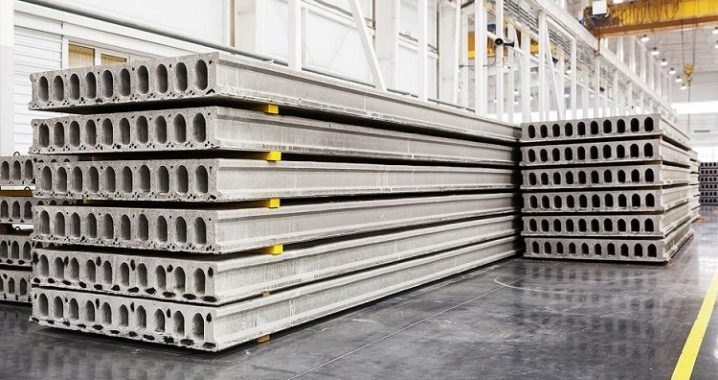
For the formation of floors, not wooden or steel structures are often used, but capital slabs. There are many varieties of such products, and each type deserves special attention. But first you need to figure out exactly how such a product is made.
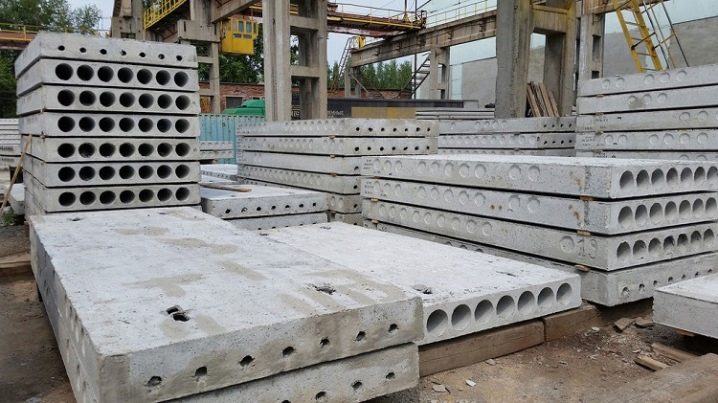
Production technology
It is appropriate to start the conversation about the manufacture of floor slabs with the fact that these are mainly reinforced concrete structures. Therefore, they can be made either at industrial enterprises, or, at best, at large construction sites, with the involvement of experienced technologists. Slabs can be made from various types of concrete. A dense concrete mix is needed if you want to limit the mass. And then there is structural lightweight concrete, which forms a dense structure.
If you plan to use the slab where significant bending stresses are created, so-called stressed reinforced concrete is used. Products with internal voids are manufactured using a formwork technique. Various grades of "heavy" concrete are used as raw materials. At the very beginning, the reinforcement is prepared, which is needed to create frame gratings.
Important: The frame grille must comply with manufacturing standards for strength and geometrical configuration.
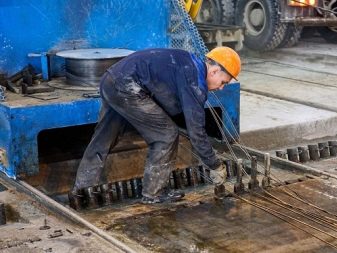
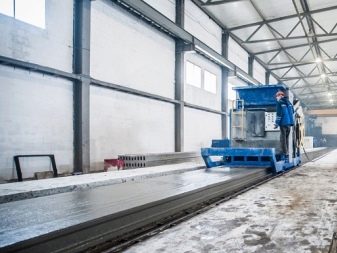
While the fittings are being prepared, the solution is mixed. As usual, it is made by mixing gravel and sand with cement. The exact proportions are selected individually each time. Depending on the organization of production, gravel with sand is obtained ready-made from quarries or directly kneaded at the enterprise. In this case, such a workpiece is necessarily sieved.
The purpose of screening is to get rid of too large fractions that cannot be molded. Next, the lattice is laid in the mold and concrete is poured into it. To improve the uniformity of the distribution of the mass, vibration processing is often practiced. In some enterprises, additional steam treatment is practiced.
Important: if the technology is observed, such plates should be obtained that will not sag or deform.
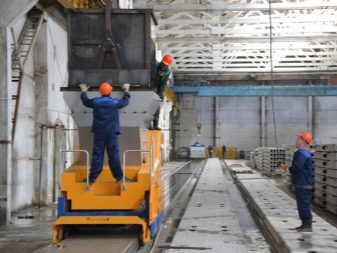
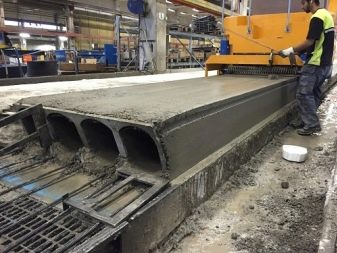
Marking
Even a cursory acquaintance with the technology of manufacturing floor slabs shows how different they can be. And for a complete understanding of the essence of each product, its purpose, it is important to be able to read the labeling. It is by no means spontaneous, on the contrary, manufacturers are obliged to follow the instructions of GOST 2016. The usual order of notation is as follows:
- type of structural element and product;
- length;
- width (the height is always the same, therefore it is not prescribed);
- permissible level of bearing load (1 unit is equal to 100 kg per 1 sq. m);
- reinforcement category;
- other parameters.
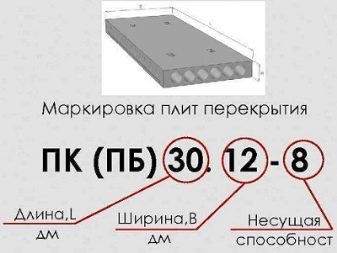
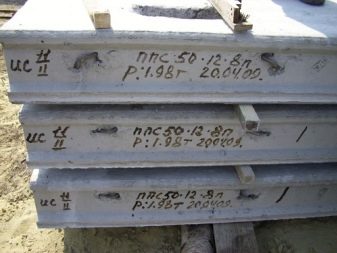
The last group includes information about:
- resistance to corrosive and aggressive substances;
- seismic resistance;
- resistance to low temperature;
- embedded elements or special holes.
The letters P, PTS or PP denote a full-weight monolithic product. Behind the reduction of GHG or PR, solid ribbed slabs are hidden. If the plate is marked as PV, it means a continuous ribbed plate with ventilation openings. When the holes for the lights are being prepared, the designations PS or PF are used. The combination of PL symbols means that the overlap is designed for an easy-to-drop roof.
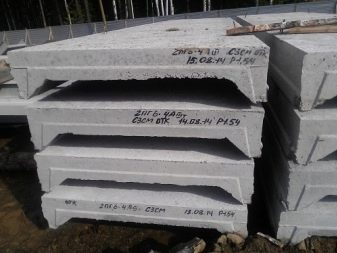
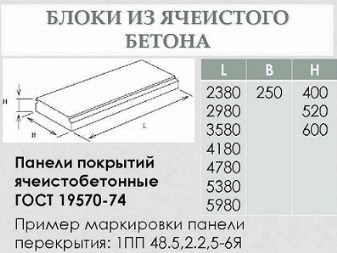
An easily removable roof made of arched and vaulted ribbed slabs can be marked as POS, POV, POF, POL.Hollow core slabs are labeled according to the number of points on which the slab rests. Products of class T rest on 3 sides, and products of class K - on all four. If there is no letter at all, this means that the structure is designed to be supported on both sides. PC and PG slabs differ from other hollow core (PB) in the production method.
PG, PK - means pouring into the formwork structure. But PB means forming on a continuous conveyor. The result is a very high level of smoothness and security. In addition, the PB does not have significant length restrictions. Therefore, such plates can be used in places with atypical dimensions.
But the mold plate has relatively narrow openings. Drilling of such products is not allowed, therefore the laying of communications through them is impossible. In addition, the markings also indicate the type of concrete. The letter C stands for increased resistance to seismic shocks, and I stands for cellular materials.

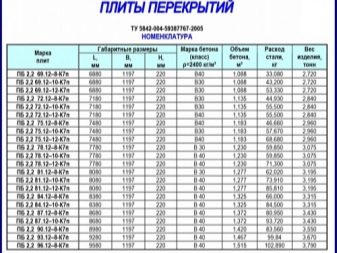
Further:
- M - fine grain;
- C - dense silicates;
- L - lungs;
- W - resistance to heat;
- P - sand concrete;
- H - normal permeability.
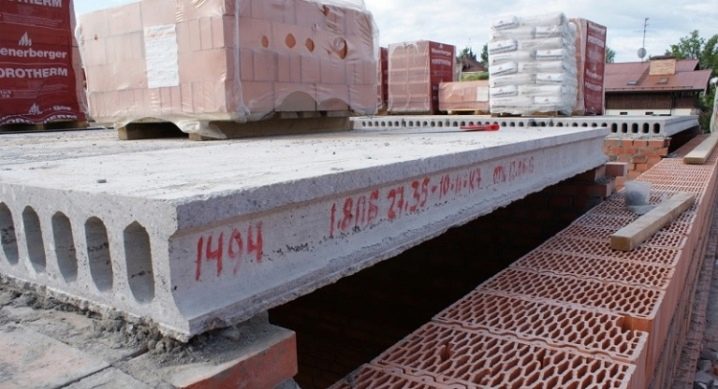
Views
Precast concrete slabs can only be prepared in a large specialized production environment. Concrete of selected grades is necessarily used, which is additionally reinforced with a lattice of reinforcement. Each such product is standardized. Its dimensions are as follows:
- in length not less than 2.5 and not more than 12 m;
- in width strictly from 1 to 1.5 m;
- in thickness from 0.14 to 0.22 m.
The use of standard concrete products allows you to build a floor as quickly as possible. Manages to significantly reduce the cost of work and simplify installation. Precast concrete structures can be completely solid, and at the same time they look different from other types in the appearance of the end surface. The appearance of longitudinal cavities is completely excluded there.
The solid block is extremely robust, yet quite heavy.
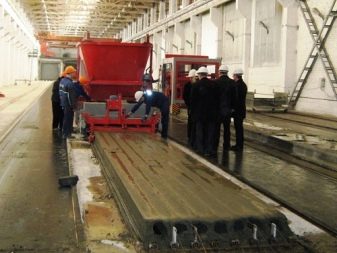
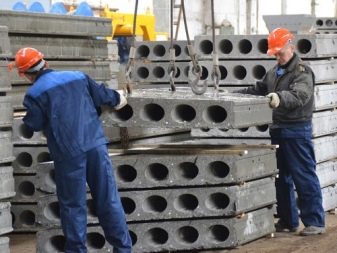
In addition, a monolithic prefabricated RC block allows a relatively large amount of heat to pass through. And the noise in the room will pass very well, which, of course, is not at all good for the residents of the house or those working there. The hollow core slab is made with cavities that are positioned along the longitudinal axis. The cavities usually have a circular cross-section, the inner diameter is 0.11-0.16 m.
Slabs with oval channels inside are less common. The use of hollow core products in construction has become commonplace. They are appreciated for their excellent sound insulation parameters. The reduction in mass reduces the stress on the main elements of the building, including the main walls. The tent construction also deserves attention.
Such slabs are similar in cross-section to a tray having parallel-oriented ribs. The thickness of each rib is from 0.14 to 0.16 m. The lightweight construction of the hipped-roof slab does not prevent it from maintaining high strength and resisting powerful deformations. However, the U-shaped block is very difficult to finish from the inside.
And one more weakness will be its increased thermal conductivity.
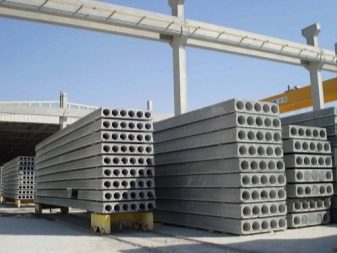
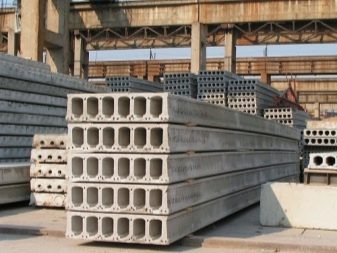
Some types of floor slabs can be made from reinforcing cages. The welded method involves contact or semi-automatic welding of a steel bar. The knitted lattice is assembled from single rods. A special annealed wire is used to connect them. The final version of the slab is chosen, of course, even during the design process.
A flat solid slab is used to cover ceilings and interfloor gaps. In this case, you will have to abandon the harness. The same product is very often used in low-rise construction. But there are other uses for flattened elements:
- construction of technical and industrial facilities;
- the formation of openings;
- laying of heating mains;
- construction of balconies and many other objects.
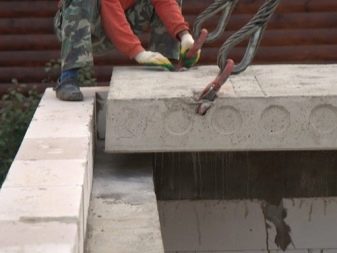
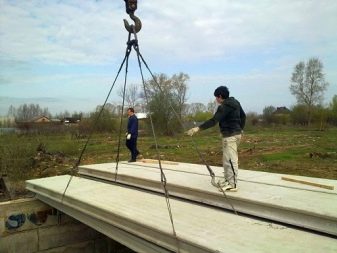
A standard product can only be made using heavy concrete of at least M300.Strength categories - B12 or B20. A minimum of 50 freeze and thaw cycles are guaranteed. The floor slab is completely resistant to water penetration. In addition to simple ones, prestressed plates can also be used.
Such a product allows you to significantly reduce the cost and shorten the construction time. Importantly, this does not affect reliability. Therefore, designers and builders are paying more and more attention to pre-tensioning technology. It can also be done with simple "mechanics" (more precisely, with jacks). But sometimes electrothermal treatment is also practiced, when a strong heating is obtained during the passage of a high-frequency current.
The mixed electrothermomechanical technique is characterized by increased productivity. But the payment for the products obtained in this way is too high. Therefore, this version of the technology is used only when there are extremely high requirements for strength, stability and resistance to bending force. The characteristics are obtained, indeed, at a very high level. The only problem is that only the most prepared enterprises can produce electrothermomechanical prestressing.
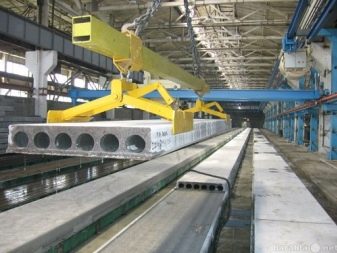
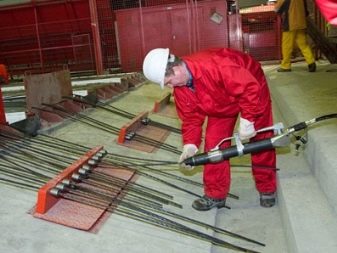
The prestressed plate can be prefabricated or monolithic. The prefabricated type is quite cheap, but it should be used only for spans no longer than 6 m. The highest permissible load per 1 sq. m does not exceed 10,000 newtons. A monolithic prestressed block is in demand when creating high-rise structures.
Strengthening can be done "on the stop" (before the mortar is applied). But hardening "on concrete" is also practiced. It is produced only when the solution hardens to the declared brand strength. Importantly, prestressing is great for earthquakes and explosions. An increase in the service life of structures as a whole is provided.
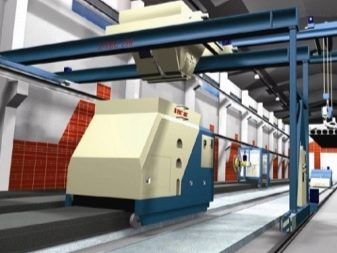
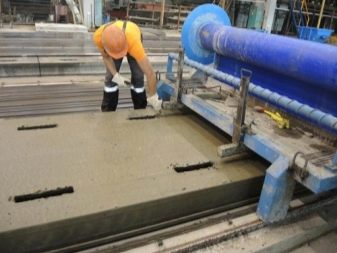
Caisson slabs can give good results. First of all, they began to be used in the construction of bridge supports located directly in the reservoir. First, an island is formed using the soil filling method. Next, a structure is formed from reinforced concrete or metal. The entire lower part of the structure is equipped with first-class steel knives.
The problem is that using a caisson slab to work people under bridge supports is extremely dangerous in terms of health. For more than half a century, caissons have been used only in completely exceptional cases, when one cannot do without them. But in construction, a coffered slab means a completely different object, which is much more practical. The purpose of such elements is to divide the ceiling or the inner surface of the vault with the help of recesses similar to boxes. These indentations are located in the gaps of the cross beams.
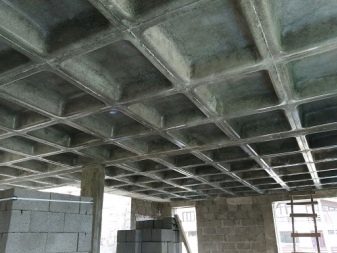
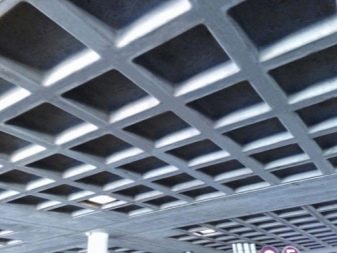
The lower section of the section is equipped with reinforced ribs. Stretched reinforcement is concentrated in them. At the same time, there is no concrete there. The ribs are placed in two directions at right angles to each other. The rib step is 1.5 m. A slab is placed on the ribs.
Technical considerations are unlikely to justify the use of complex coffered slabs. But their use for purely architectural and design purposes is quite reasonable. As a result, you can simulate:
- ancient Egyptian mosaics;
- ancient greek style;
- Roman frescoes.
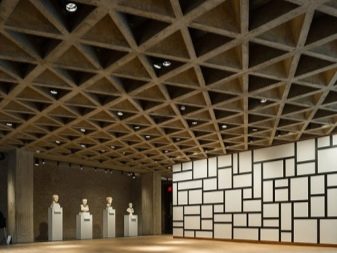
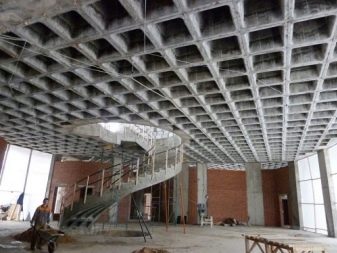
The channel type of floor slabs (VP) is not used in the construction of the buildings themselves. But on the other hand, it is irreplaceable wherever sewerage, collectors or water-pressure structures are installed. And also such elements are needed to lay a heating main channel. Modern channel slabs are equally good both underground and in overground parts of special structures. The old technology of vibration casting has now been replaced by vibrocompression.
This change was not accidental - thanks to it, the protection from water has significantly increased.Additionally, the resistance of the boards to acids and various metal salts has increased. The channel plate is equally in demand when arranging the roofs of an industrial building or a private dwelling. Despite the same dimensions with the same type of solid structures, a lighter product is obtained. The channel plate is widely used for construction work in loose soil, where soil water is high.
Increasingly, not only reinforced concrete, but also expanded clay concrete slabs are used for the construction of floors. According to the combination of parameters, some specialists even prefer them to ordinary concrete products.
Expanded clay concrete blocks can have both prefabricated and monolithic execution; in both cases, they are fully applicable without specialized equipment.
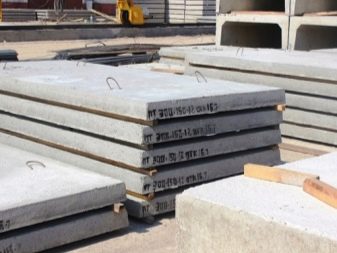
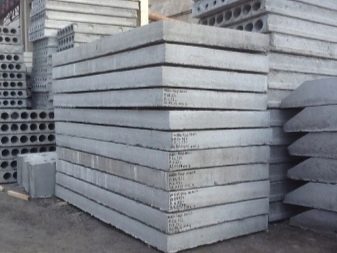
Ribbed structures can withstand significant loads perfectly. This allows you to switch to using a medium density material.
Important: the expanded clay concrete slab can only be laid after final hardening. But an unbreakable claydite concrete coating is attractive in that it is easy to build even without outside help. To form the bearing beams, a steel I-beam or channel is used.
To simulate the formwork, corrugated board is used. Important: expanded clay concrete blocks are made only from raw materials that do not contain chlorides and are characterized by increased resistance to fire. To complement and reinforce the beams, slabs with frequent ribs are used. But this solution is only suitable for spans no longer than 8 m.
Of course, any of the described overlap options can be used only after careful calculation.
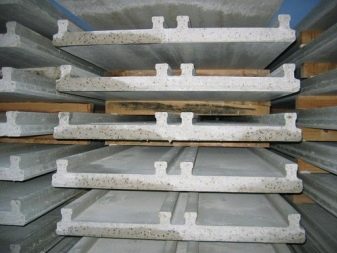
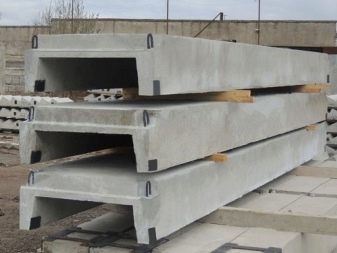
For the formation of slabs in a pure form, concrete grades from M250 to M350 can be used. Of course, the higher this category, the higher the load the elements will be able to survive.
In section, the overlap looks like this:
- hollow slab;
- full-bodied construction;
- classic caisson product;
- channel block.

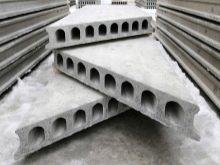
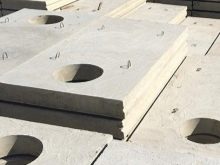
Dimensions (edit)
Hollow core slabs (most used in private construction) mainly have the following dimensions:
- thickness 0.22 m and length 4.78;
- thickness 0.26 m with a length of 5.679 m or less;
- thickness 0.22 m, length is chosen arbitrarily.
The slab of the PB brand can have a length of 1.8-9 m. This solution is most convenient when ordering "additional" blocks. As for the voids, they are at least 0.114 m for PC or SG products. Therefore, the passage of sewer risers does not cause problems. But at the PB, the holes are narrower (maximum 0.06 m).
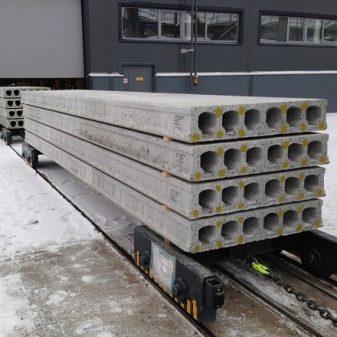
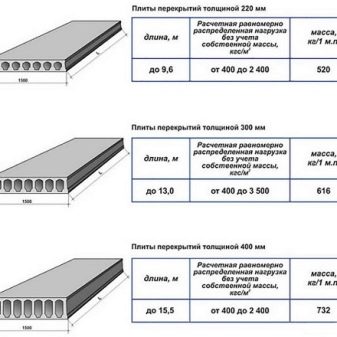
Applications
Based on what has already been said, it can be emphasized that floor slabs are used for interfloor space in panel houses and for private construction. It is customary to divide such structures into public, industrial and residential categories. Of course, the industry is supplied with the most durable products. It is able to withstand maximum loads and even exposure to aggressive substances. The slab with the upper rib orientation is used mainly in industrial buildings, and with the lower one in flooring.
Ribbed products are used mainly where a lot of people go:
- in hypermarkets;
- in cinemas and leisure centers;
- at stadiums;
- in other similar places.
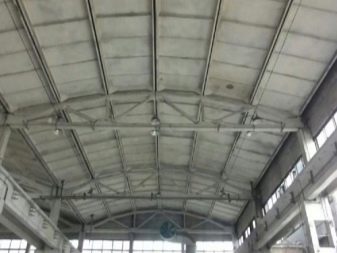
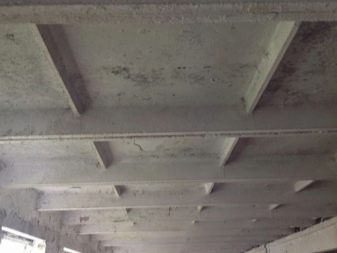
How to choose?
This question arises for private developers in the first place. A slab with many voids is light, but its strength must be carefully controlled. It is recommended to check the marking with special tables where it is deciphered. PC and NV designs are chosen mainly where strength is especially important. But PNO is allowed to be used exclusively in low-rise construction (1, maximum 2 floors).
It so happens that typical slab blocks cannot be used for some reason. Then you will have to fill in the product directly at the facility. Prefabricated monolithic structures (a type of cast-in monolithic) are easier to build. At the same time, the most daring projects are being successfully implemented.
But the final decision should be made only after consulting with experts when ordering directly.
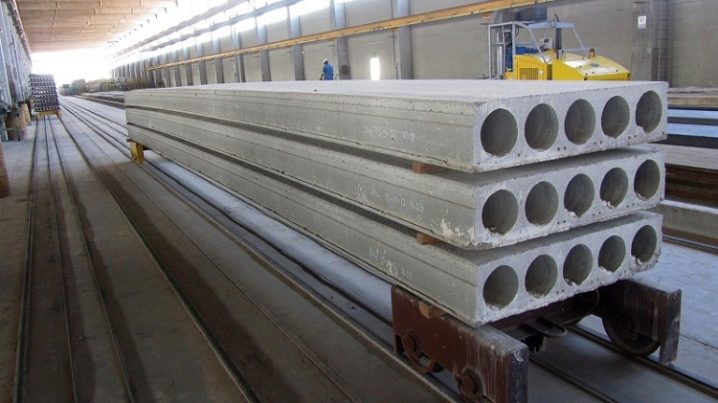
For information on how to lay the floor slabs evenly, see the video below.
The comment was sent successfully.