Slab formwork: types, device and installation technology

Any construction of buildings provides for the mandatory installation of floor slabs, which can be either purchased ready-made or manufactured directly at the construction site. Moreover, the latter option is very popular, since it is considered less expensive. To make monolithic slabs yourself, you need to create a special structure - floor formwork.
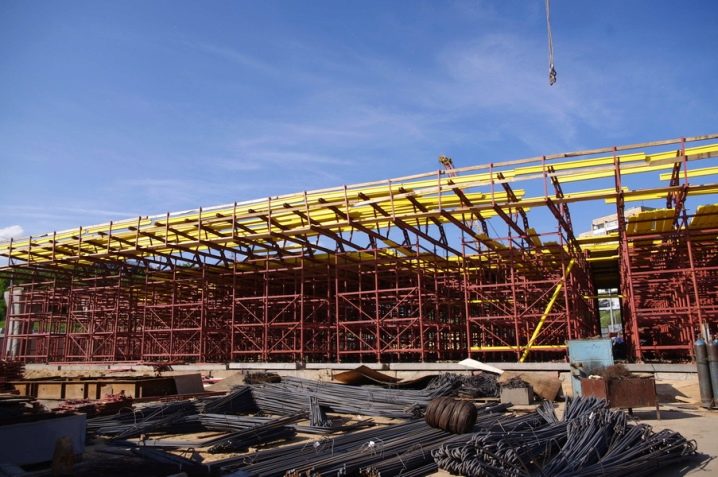
Device
A monolithic floor is one of the main elements of the structure, which increases the operational characteristics of the building and makes it durable. Its installation begins with the assembly of the formwork, which allows the concrete to maintain its shape and immobility until it hardens. Slab formwork is considered to be a complex building structure, which usually consists of such elements.
- Support nodes. These are wooden beams that look like telescopic racks. In order to evenly and correctly distribute the dynamic load on this element, the distance between them should be accurately calculated. With the help of such supports, formwork is assembled for pouring monolithic slabs with a height of not higher than 4 m. Often, additional or starting racks are used in the construction of structures. They are made of a metal profile and are fixed to each other with special fasteners (cup or wedge). Thanks to such supports, formwork up to 18 m high can be built.
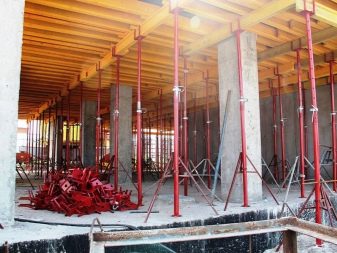
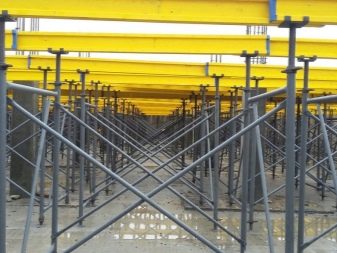
The props, which are commonly used for formwork installation in high-rise buildings, consist of three elements: a fork, a vertical support and a tripod. The fork is the upper part and serves, as a rule, to fix the working surface. It is often referred to as the "support fork". This element is produced from four tubes (square section), which are welded at the corners, and metal plates with a thickness of at least 5 mm. The tripod (skirt) is designed to stabilize the stand and allows it to be held securely horizontally. In addition, the tripod takes on part of the main load when pouring concrete.
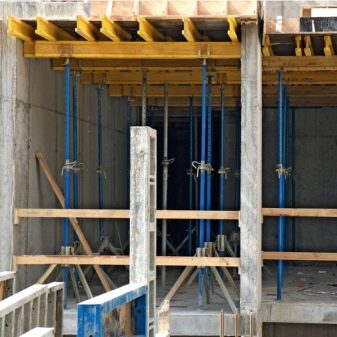
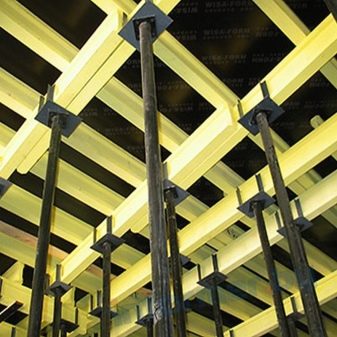
According to the standards, in the construction of ordinary residential buildings for the installation of an auxiliary structure, it is allowed to use racks of the following sizes: 170-310 cm, 200-370 cm.If you plan to build a private house outside the city, then you can get by with supports of a typical size of 170-310 cm, they are placed with a step of 150 cm.
- Base. It is made of sheet material, which is most often used as sheets of plywood, metal profiles and boards from boards. To increase the strength of the structure, it is recommended to use a material with high moisture resistance.
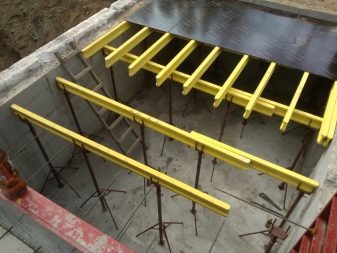
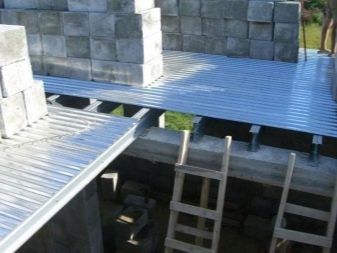
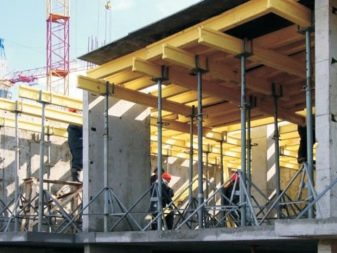
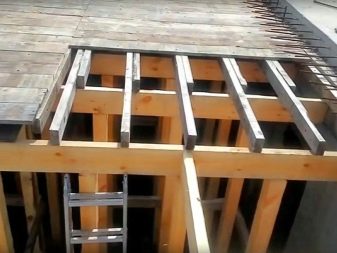
- Metal or wooden beams. These elements are placed perpendicular to each other. For the construction of formwork, you need to choose beams with increased rigidity, since the retention of the mass of concrete and the strength of the formwork itself depend on this.
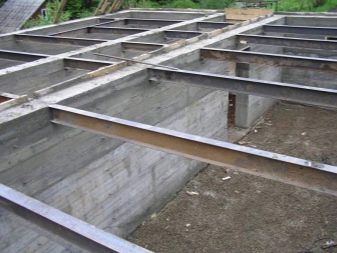
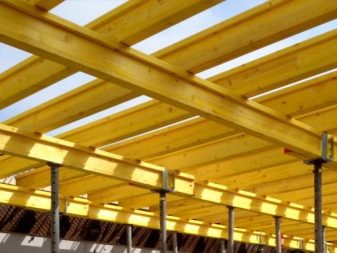
Slab formwork can be made of various types, it all depends on the type of support, the thickness of the concrete pouring and the height of the structure.
Advantages and disadvantages
Slab formwork is considered an indispensable building element. However, they have both advantages and disadvantages. Therefore, before building them, it is important to take into account all the characteristics. The main advantages of formwork include such moments.
- Providing high strength to monolithic slabs.Unlike conventional prefabricated structures, they do not have joint zones and seams.
- The ability to implement non-standard projects, since such formworks allow the manufacture of floors of various shapes.
- Elimination of displacement of floors in the transverse and longitudinal direction. Monolithic slabs acquire additional rigidity.
- Simple installation. Formwork can be created on our own without the use of special equipment, which significantly saves construction costs.
- Reusable. The climbing formwork is used to cast hundreds or more of monolithic slabs. It is financially beneficial.
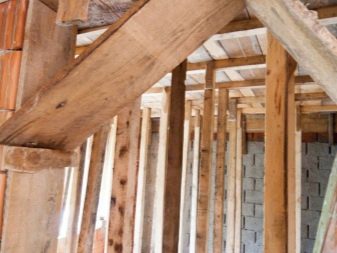
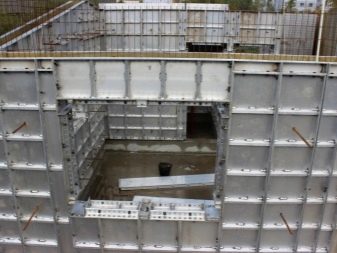
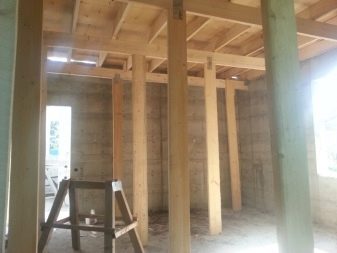
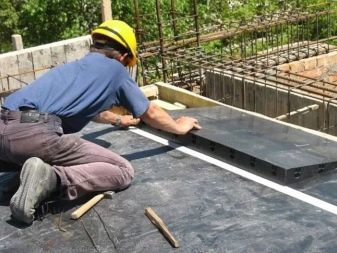
... As for the shortcomings, there are few of them.
- Compared to the use of ready-made slabs, the time is higher, since it is required to additionally erect and dismantle structures. In addition, the construction process is a little delayed, since you have to wait for the concrete filling to gain strength.
- The need for strict adherence to the entire technology of manufacturing and pouring concrete solution. This is difficult to do, because concrete is poured in huge quantities.
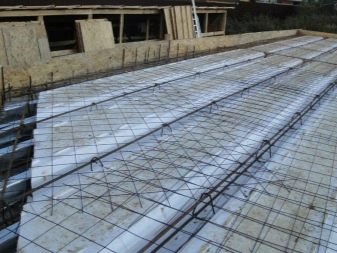
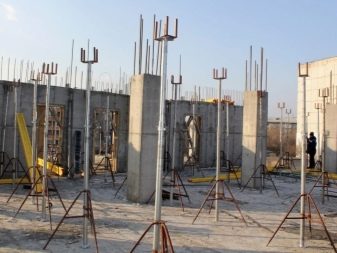
Views
Slab formwork, designed for concreting monolithic slabs, is of several types, each of which differs in assembly technology and technical characteristics. Most often, the following type of structures is used in construction.
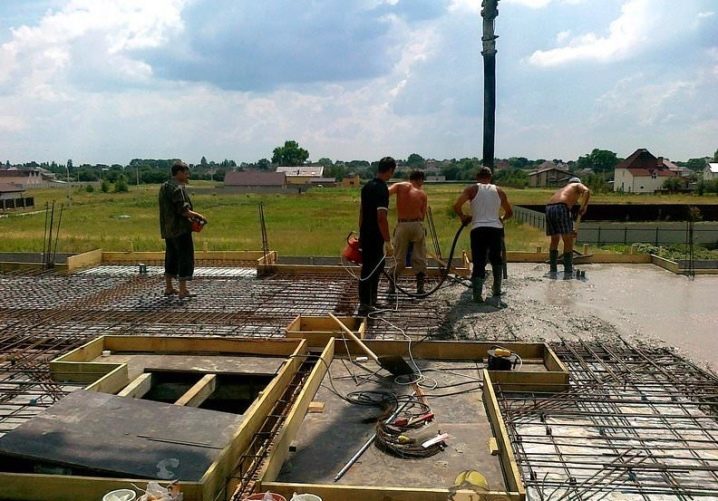
Stationary (non-removable)
Its main feature is that it cannot be removed after the solution solidifies. Stationary formwork consists of sheets of thermal insulation and layers of waterproofing material, so they provide the building with additional heat and protection from moisture. At the end of concreting, non-removable structures are transformed into one of the elements of the reinforced concrete structure. These structures have a number of advantages: they simplify installation work, reduce labor costs, and give the structure a decorative look, as they are made of modern materials.
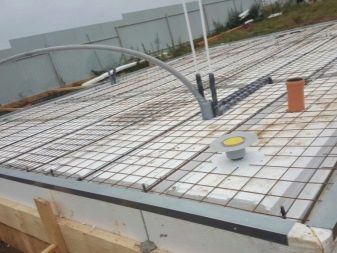
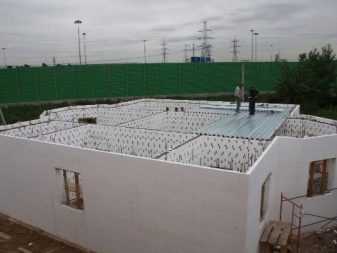
Detachable
Unlike the previous type, these structures can be dismantled after complete hardening of the concrete. They are in greater demand than stationary ones, because they are characterized by a low price and easy installation. Many builders take removable formwork for rent, as this allows you to reduce the cost of assembling the structure and quickly complete the concreting process.
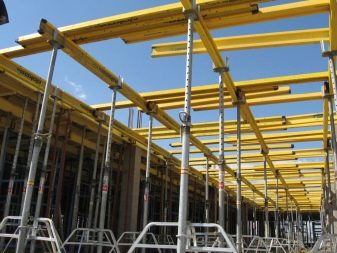
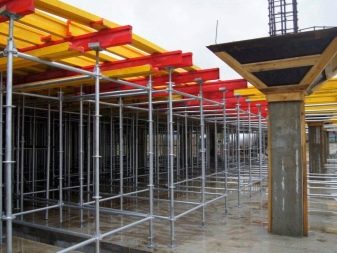
Collapsible
This type of formwork is divided into several classes and differs in the level of complexity. So, for example, when building horizontal planes, a simple (frame) formwork is recommended, but if it is planned to erect buildings of complex shapes, then a volumetric (large-panel) structure is suitable. The assembly of such elements is carried out from moisture-resistant plywood, profiled sheet, polystyrene foam, polystyrene and expanded polystyrene.
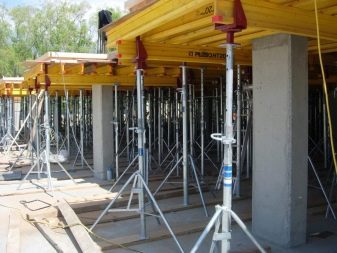
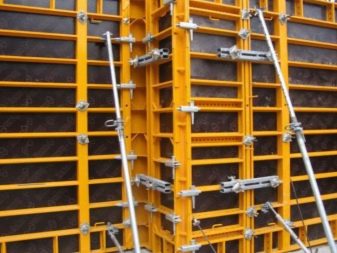
In addition, sliding formwork is sometimes used for the construction of small and large modules. It is installed vertically. The type of construction is chosen in construction depending on the complexity of the project.
Technical requirements
Since the slab formwork is responsible for the further strength of monolithic blocks, it must be erected in accordance with the established construction standards, taking into account all technologies and rules. The following requirements apply to this design.
- High safety margin. Each constituent element of the structure must withstand not only the reinforcing cage, but also the weight of liquid and hardened concrete.
- Safety and reliability. During the reinforcement and pouring of the mortar, workers move along the base, so it must be rigid and exclude any vibration. Otherwise, monolithic slabs can get defects, which can lead to emergencies in the future. Construction tables also help to exclude damage to the integrity of the structure, on which you can also move during construction work.
- Long service life. This primarily concerns the collapsible and removable type of formwork, which are used multiple times in construction. To create a monolithic floor, it is recommended to install formwork made of durable material that will withstand subsequent operation after dismantling.
- Resistance to stress. Since the concrete is poured superficially and with a depression, its mass creates increased dynamic loads on the formwork. In order for the structure to reliably withstand them, it is necessary to correctly select its material of manufacture in advance and prepare a plan for the foundation slab, which complements the formwork drawing and the slinging diagram.
- Have a fast installation. Today, there are many support parts and ready-made sections on the market that allow for quick assembly of structures.
- Disassembly possible. After the mortar has frozen, the formwork, consisting of several elements, can be dismantled for further use. This process should be quick and easy.
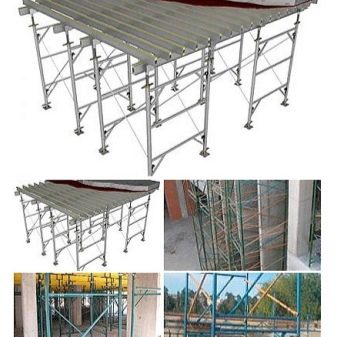
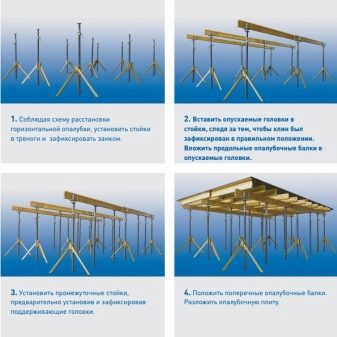
DIY installation
- At the first stage of work, accurate calculations should be made. For this, design is carried out and an estimate is drawn up. In the project, it is important to take into account the strength of the formwork so that it does not crack under the mass of concrete mortar. In addition, a slab placement scheme is made, taking into account the features of the configuration of the future building, the concrete grade and the type of reinforcement. So, for example, for the construction of an ordinary residential building, the width of the spans in which will not exceed 7 m, you will need to make a solid floor with a thickness of at least 20 cm.
- At the second stage, the purchase of all the necessary materials is done. These are the foundation for the formwork, supporting and fastening elements.
- The next step is to assemble the formwork itself. Its installation should be started after the walls have been erected, when their height has already been set. For horizontal casting, you can use two types of formwork: ready-made (purchased or rented, it only requires assembly) and non-removable. In the first case, it is recommended to choose a structure made of durable plastic or metal, it can be reused after completion of work. The complete set of such formwork usually includes sliding supports to keep the floor at a certain level. They are installed very quickly and easily.
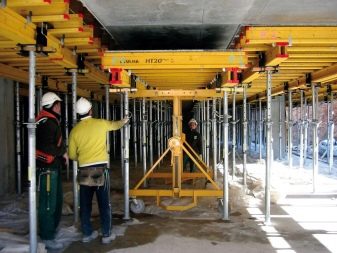
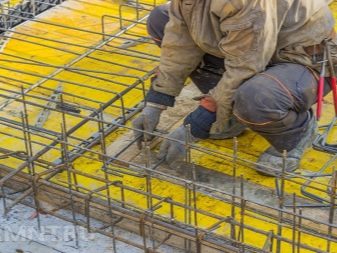
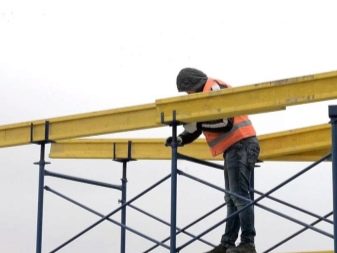
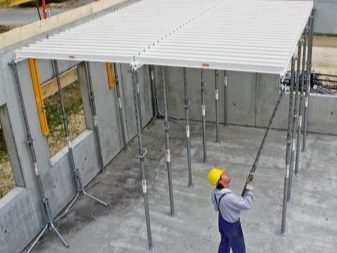
In the second case, you will have to assemble the formwork with your own hands from plywood and edged boards. It is recommended to take plywood with increased moisture resistance, and it is best to select edged boards of the same size, this will save you from adjusting them in height in the future. First of all, the foundation is being prepared for monolithic slabs. In the event that gaps appear between the elements during the assembly of the formwork, then a waterproofing material is additionally laid. You can also make a structure from corrugated board. It is much easier to work with it and this material eliminates the formation of gaps.
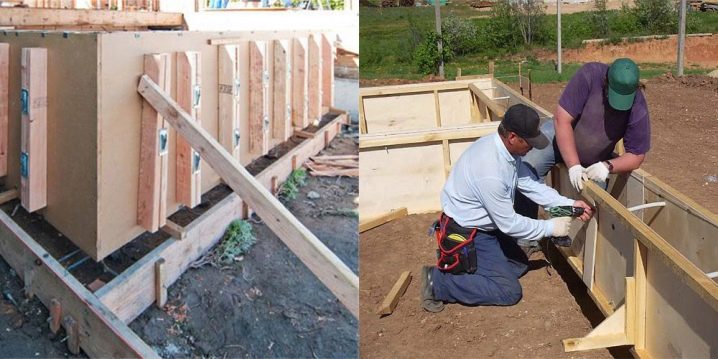
Great attention should be paid to the choice of plywood. It is advisable to purchase laminated or glued sheets with increased moisture resistance and a thickness of 18 to 21 mm. This material is made from several layers of wood veneer, each of which is laid across the fiber. Therefore, this type of plywood is durable.The installation of plywood sheets must be carried out in such a way that their joints fall on the crossbars, in addition, after the assembly of the formwork, not a single seam should be visible.
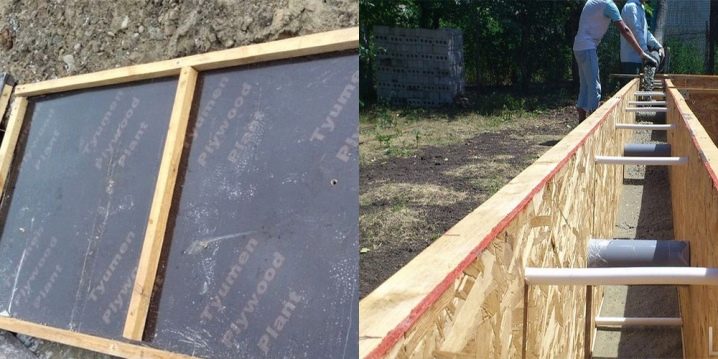
The installation process should begin with the installation of supports that will support the future monolithic block. Both sliding metal elements and homemade ones from logs are well suited as racks (they must have the same thickness and height). The supports must be placed in such a way that a distance of 1 m remains between them, while the distance between the nearest supports and the wall should not exceed 20 cm. Then, beams are attached to the supports, which are responsible for holding the structure. They are additionally equipped with horizontal formwork.
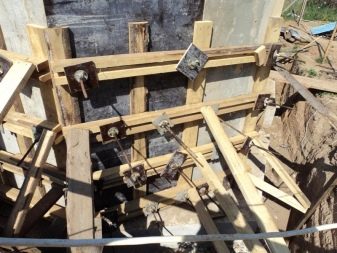
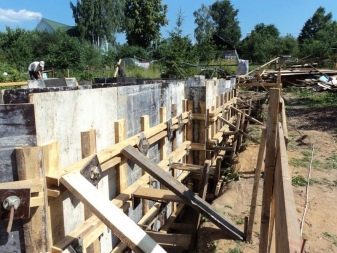
First of all, sheets of plywood are laid on the bars in such a way that their edges fit snugly against the base of the walls, leaving no gaps. The racks must be placed so that the ends of the entire structure exactly coincide with the upper edges of the walls. Great attention must be paid to the entry of floor slabs - they should not be less than 150 mm. Next, they make a control for the horizontal structure of the structure and start pouring the solution. The solution is poured into the manufactured formwork, it is evenly distributed, compacted as much as possible, waiting for solidification (about 28 days) and dismantling of the auxiliary structure is carried out.
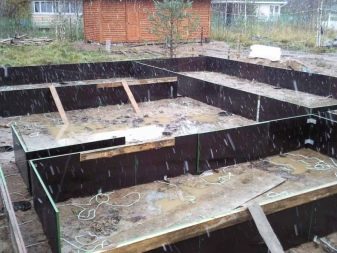
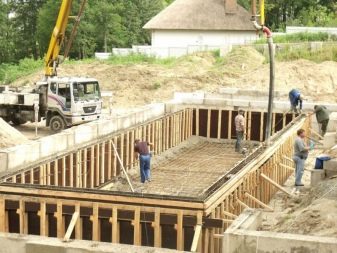
Many craftsmen also often use a non-removable formwork from a metal profile to create monolithic modules in the construction of new buildings of large areas. Installation of such a structure has its own characteristics. To assemble it, you must purchase the following materials in advance.
- Durable metal profile. During concrete pouring, it ensures a good solidification of the mortar and forms a stable frame. It is advisable to choose “M” grade metal profile sheets, since they have a long service life and are resistant to stress. They need to be spaced at equal intervals. They also make it possible to reliably seal the formwork, so the waterproofing material in this case does not fit.
- Support elements in the form of longitudinal beams, cross bars and braces.
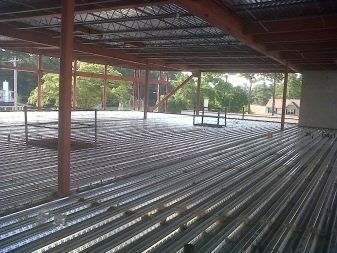

The racks are attached first, they should be placed vertically. Then the crossbars are laid and fixed, the beams are fixed and a metal-profile sheet is laid on the resulting frame. It must be securely fixed to the supporting frame. In addition, during the assembly of such a formwork, attention should be paid to the number of support points.
To exclude possible deflections, it is recommended to correctly select the length of the sheets and provide them with at least three points of support. In this case, the material is best laid in an overlap of one or two waves and fasten all the strips with special rivets or self-tapping screws. As for the reinforced floor, it is carried out according to the standard technology, protecting the surface of the metal profile with plastic supports. The length of the openings in the ceiling should not exceed 12 m. Such formwork is usually used when erecting load-bearing structures and monolithic blocks.
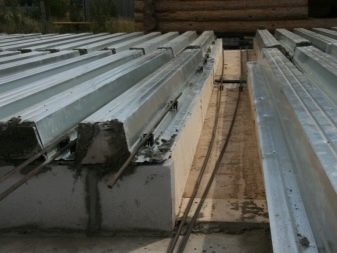
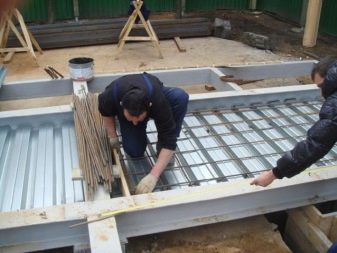
For information on how to properly install floor formwork with your own hands, see the next video.
The comment was sent successfully.