Do-it-yourself monolithic overlap
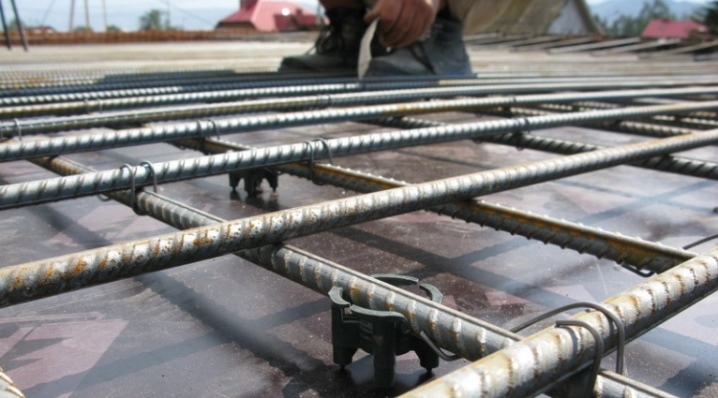
The construction of any house or building involves the installation of ceilings located between floors or in the attic. Wood products are often used to accomplish this task. Wooden elements are easy to make and install, but they have low heat and sound insulation characteristics, therefore they are noticeably inferior to floors made of concrete. For this reason, it is better to give preference to the concrete option. Moreover, making a monolithic overlap with your own hands is quite simple.
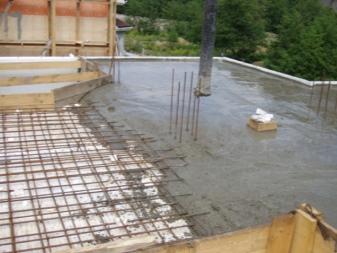
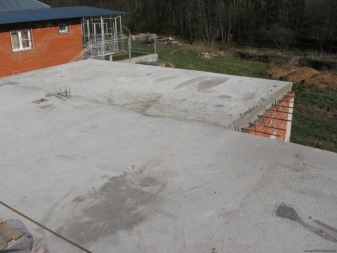
Device
If we talk about the structure of the floor in question, then it is formed from special reinforced concrete. Concrete is poured into the formwork, which does not subsequently deform and will not bend under load. To create such a product with your own hands, you will need lumber, tools for fitting, cutting and collecting shields. After the removal of the formwork, it can be used in the rafter mechanism.
Rebar will become a consumable, and communications will also be concreted. The most difficult will be the basement floor slab - due to the large number of input units for engineering type mechanisms.
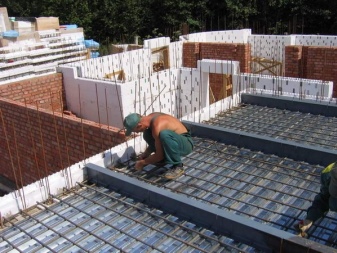
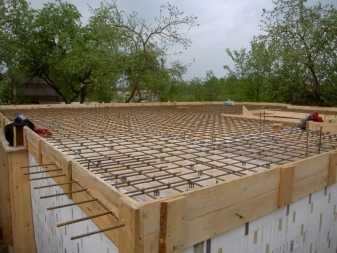
Load calculation
During use, a monolithic type slab is exposed to a variety of loads:
- temporary;
- permanent.
If we talk about the first, their value will be associated with the weight of engineering type communications, flooring, ceilings, furniture, as well as the number of people who are in the room. In the second case, the transfer is carried out by the mass of the walls of the building, internal partitions and the mass of the roof, which also receives additional mass from wind and snow loads. When the work on the construction of the walls is completely completed, and their level is adjusted, you can equip the slab itself.
The load acting on the product is determined by the thickness of the reinforced concrete slab. For example, if the thickness is about 20 centimeters, then each square meter of the surface can take up to half a ton of payload.
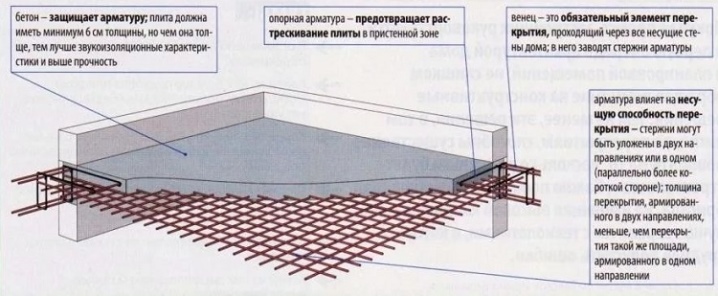
The following aspects will affect the accuracy of calculations:
- reinforced concrete slab thickness;
- used concrete grade;
- load indicator of the calculated type per square meter of floor;
- dimensions.
It should be understood that when designing reinforced concrete floors, an accurate plan must be drawn up, which is usually a drawing.
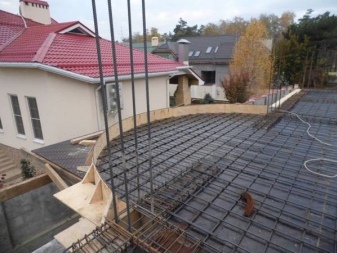
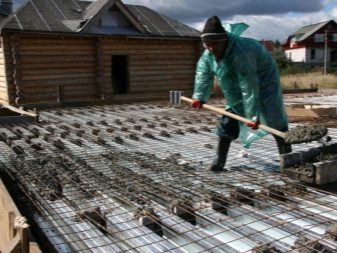
When choosing a span, it is necessary to correlate it with the thickness of the slab. This ratio should be approximately 30: 1. But when implementing an independent project creation, it makes no sense to do something thicker than 40 centimeters, because the bearing capacity increases with its mass, as well as static stresses. For this reason, the permissible load on self-made floors is rarely higher than 1.5-2 tons per square meter.
True, you can correct this situation, if you include steel I-beams in the structure of the load-bearing type, which are laid on the surface of the masonry of the load-bearing type walls smoothed with concrete. Another option, how you can raise the span while maintaining a free layout, is to emphasize the entire structure on the columns.If the thickness of the monolithic solution is up to 40 centimeters, and the span length in 4 directions from the columns is 12 meters, then the supporting section area will be 1-1.35 square meters. But this is only possible if if the reinforcement section, which is laid in the column, will be at least 1.5%.
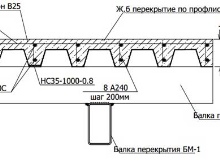
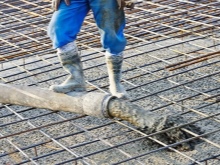
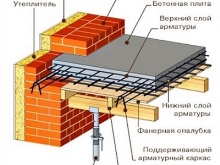
Choosing a concrete grade
It should be said that the question of choosing a grade of concrete for a homemade floor is extremely important. After all, the wrong choice of this material promises problems with strength, a decrease in resistance to stress, and so on. Therefore, the recommendations of specialists in this matter will definitely not be superfluous. Consider what brands of concrete are today.
- Brand М100 is the solution with the lowest quality and is usually used before pouring monolithic structures. Usually, this option is used for pouring a foundation tape, forming a cushion of concrete, installing a curb, and so on.
- M150 grade concrete used for floors, screeds, as well as creating a foundation for buildings with a small number of floors.
- M200 will be used to form the floor, blind area and screed. Due to the high strength of the material, it is used for the production of concrete stairs.
- M250 will be an excellent solution in creating a monolith of strip foundations, as well as floor slabs.
- M300 it is used to form floor slabs, as well as concrete stairs.
- M350 used to create various monolithic surfaces, beams and pools.
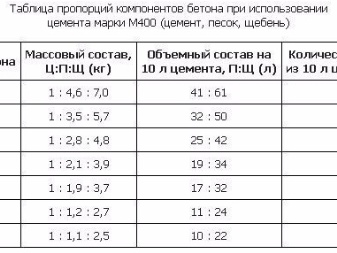
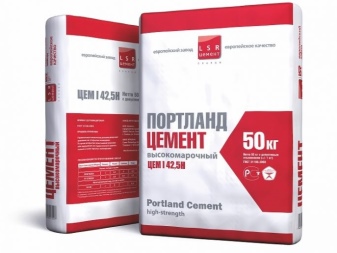
The M400, M450 and M500 brands are practically not used in the construction of private facilities. They are in demand in the creation of structures such as dams, dams, bridges and various hydraulic structures.
If you draw conclusions from the information described, then it is best to use brands M250, M300 or sometimes M350 to create a monolithic floor with your own hands.
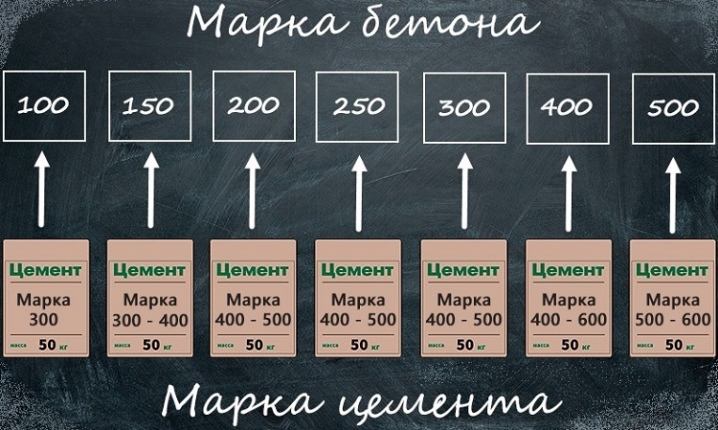
Formwork installation
Now let's talk about such a moment as the installation of the formwork, because the device of the floor slab assumes that the concrete is poured into the formwork, laid horizontally. It usually has the name of the deck. There are the following options for arranging this structure:
- installation of a ready-made removable solution - plastic or metal;
- creation of formwork on site, using boards or plywood of a moisture-resistant type.
The first option is easier to use, because the formwork is disassembled, it has telescopic supports that are needed to maintain it at a certain level. If you create the formwork yourself, then you should know that the thickness of the plywood should be 2 centimeters, and the thickness of the edged boards should be 3 centimeters. Knocking down the structure, you should fit the elements well. If there are gaps between them, then the formwork surface must be covered with a waterproofing type film.
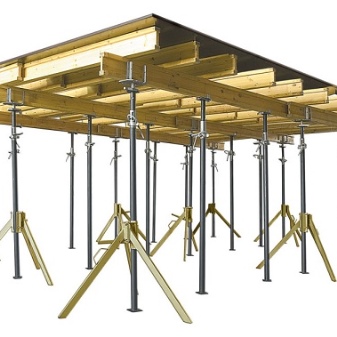
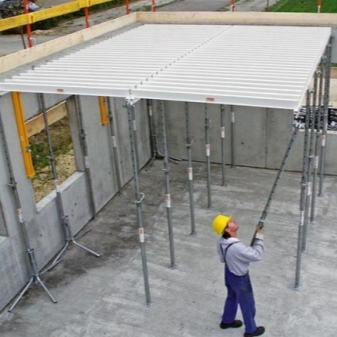
Step-by-step instructions for the installation of the formwork.
- We install vertical rack supports. Usually these are telescopic solutions made of metal with adjustable height. Alternatively, logs can be used, positioning them every meter.
- We put the crossbars on the racks.
- Then we install the horizontal formwork on top. If not a ready-made version is used, but a hand-made one, then transverse-type beams are placed on the longitudinal-type beams, and plywood with moisture-resistant properties is installed on top. The dimensions of such a formwork should be adjusted perfectly so that there are no gaps.
- It is necessary to adjust the height of the upright supports so that the upper part of the horizontal formwork converges with the part of the wall masonry from above.
- Next, we carry out the installation of vertical formwork parts. For a monolithic slab, the dimensions should be such that the edges go 15 centimeters onto the walls. A vertical-type railing should be created just at this distance from the inside of the wall.
- We check with the use of a level the even arrangement of the structure and its horizontality.
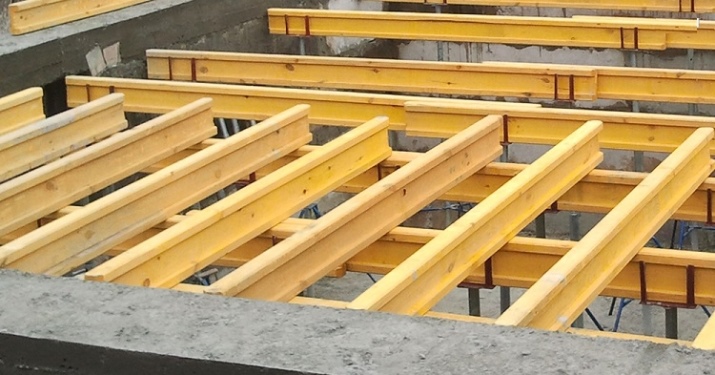
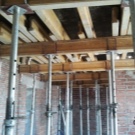
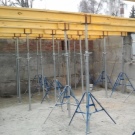
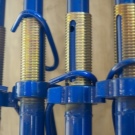
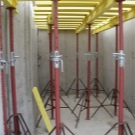
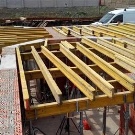
Reinforcement of the slab
The monolith must go through the reinforcement procedure.
- First you need to prepare the fittings. The required diameter of the rods should be selected knowing the design loads. Usually rods with a diameter of 12-14 millimeters are used for this.
- We are laying the first reinforcing mesh at the bottom of the structure - it will become a monolithic slab in the future. It will be a kind of armored belt. First, the longitudinal rods should be laid, after which the transverse ones. The best cell size for such a grid is 12-15 centimeters. If the overlap is not very large in area, then the size of the cells can be increased to 20 centimeters.
- The joints of the rods should be tied using steel wire.
- We lay the second reinforcing mesh in the same way as the first. We carry out tying the nets with wire. If there are not enough rods, then you can take an additional rod, which should be tied with an overlap equal to at least 40 reinforcing diameter. If rods with a diameter of just over a centimeter are used, then the overlap should be 48 centimeters. The joints of the rods should be staggered. The ends of the reinforcement rods should be on the beams of the bearing type.
As you can see, the armopoyas is easy to make. This solution with steel profiled decking will significantly improve the strength of the floor.
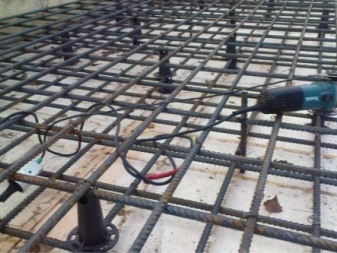
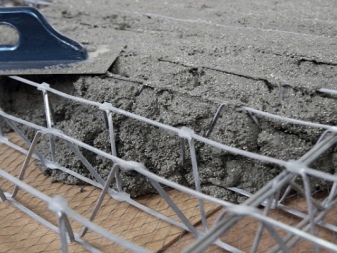
How to fill?
The concrete should be bought directly from the manufacturing plant, which will greatly facilitate the task. Pouring the mortar from a mixer in an even layer makes it possible to ensure maximum strength of the product. It would be better to pour concrete with a 20-centimeter layer without stopping. Before pouring concrete into the formwork, it is necessary to install a frame or a box for technical holes. We are talking, for example, about a ventilation duct or a chimney.
After pouring, vibrate with a special vibrator of a deep type. After that, the concrete is left to dry and gain strength for a month. During the first week, the surface should be constantly moistened with water. And it is precisely to moisturize. After 30 days it will be possible to dismantle the formwork and the slab will be made. As you can see, there is nothing difficult about pouring concrete.
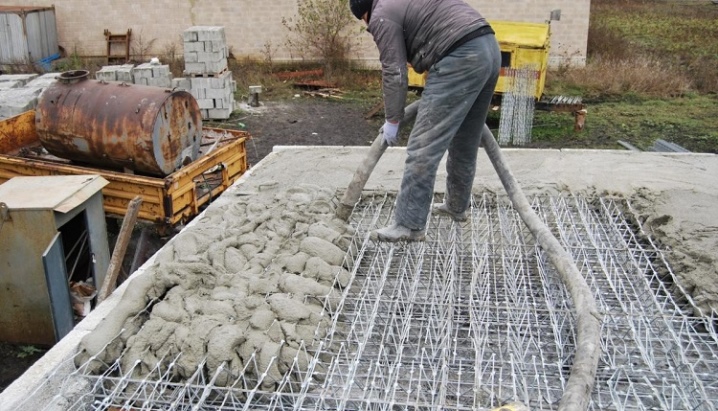
Care after pouring
If we talk about caring for such a product, then it should be said that in the process of hardening a lot of heat emanates, and this becomes the reason for the rapid evaporation of moisture. Its lack leads to deformation of the concrete coating, which is why, at first, the slab should be wetted with water on a regular basis. It can be poured either with buckets or with a hose with a special spray. Before that, you can put rags on the concrete and pour water.
In case of heat, the concrete should be covered with polyethylene so that the slab does not crack. The formwork can be removed within 10 days after the last wetting. Typically, the board gains strength in about 3-4 weeks. When this period has passed, you can continue construction work.
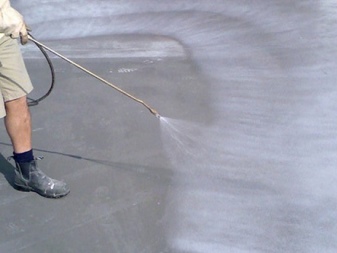
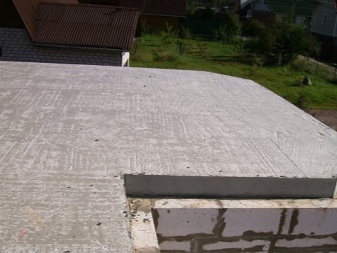
In the next video, you are waiting for the construction of a monolithic floor slab with your own hands.
The comment was sent successfully.