Floor slab reinforcement: materials and calculation rules
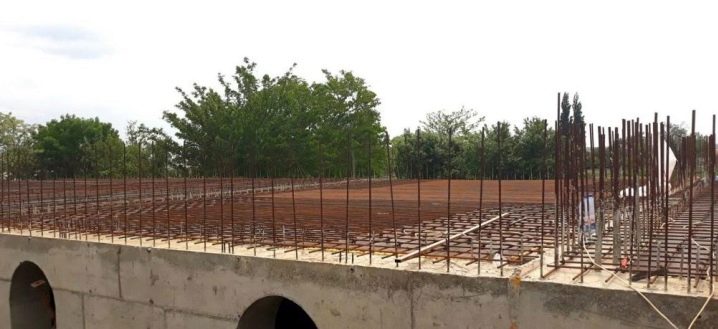
Reinforcement of a non-girder monolithic floor panel (internal horizontal enclosing structure) is a mandatory technological process of their manufacture. The reinforcement in the structure of the structure made of concrete takes the load and increases the strength properties of the product.
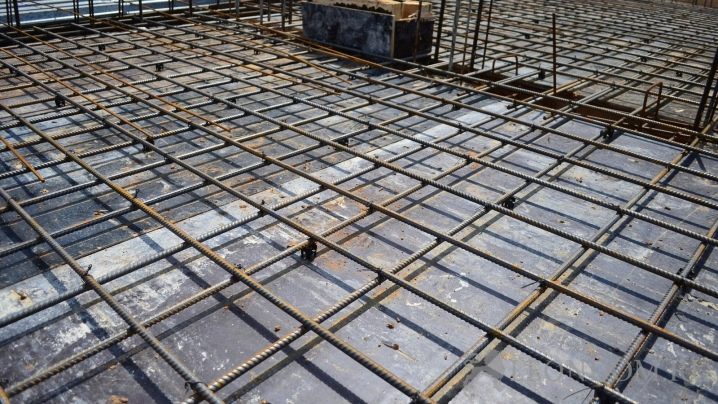
Appointment
The purpose of the reinforcement is to increase the ability to withstand the load of the structure, to reduce the possibility of cracking that appears due to temperature jumps. For such tasks, a material with high strength properties is used - fiber, glass fiber, basalt fiber, steel. In order to eliminate premature corrosion and increase the wear resistance of buildings, the reinforcement method began to be practiced.
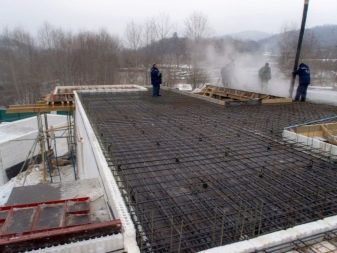
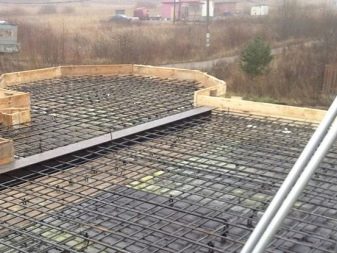
Requirements
Strengthening a monolithic floor panel is a responsible process, the implementation of which is subject to a number of conditions. When carrying out work on the creation of a reinforced concrete floor panel, it is necessary to adhere to the following recommendations.
- To connect metal rods, a knitting wire with a cross section of 1.2-1.6 millimeters should be used. The use of electric welding is unacceptable due to a change in the structure of the metal at the interface points.
- It is necessary to provide for the required thickness (height) of the concrete slab in relation to the distance between the walls that receive the load. The height of the reinforced concrete panel is 30 times less than the distance between the supports. At the same time, the smallest panel thickness is at least 15 centimeters.
- The laying of the components of the iron frame, taking into account the dimensions of the overlap, is carried out vertically. At the smallest panel height, the reinforcement is laid out in one layer. At a height of more than 15 centimeters, a reinforced reinforcement is made in two layers.
- For pouring into the formwork, a concrete mixture of the M200 grade and higher is used. Concrete of these grades has excellent performance properties, can withstand significant loads and has a reasonable cost.
- Reinforcement rods with a cross section of 8–12 millimeters are used to assemble the steel grating. When implementing a two-layer reinforcement, an increased size of the section of the metal profile in the bottom row is practiced. The option of using the finished mesh is allowed.
- The formwork is made of waterproof plywood or planks processed by planing. The joints are carefully sealed. To strengthen the formwork, sliding-type iron racks or pillars of wood with a diameter of up to 20 centimeters are used.
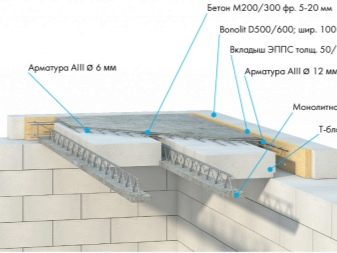
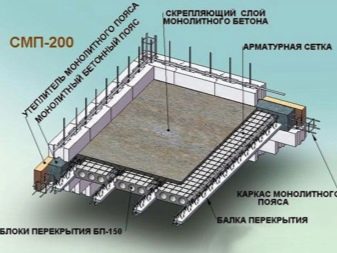
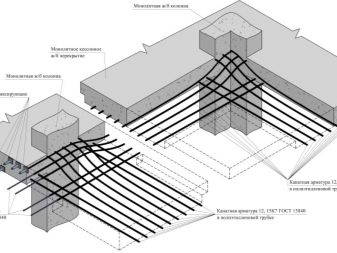
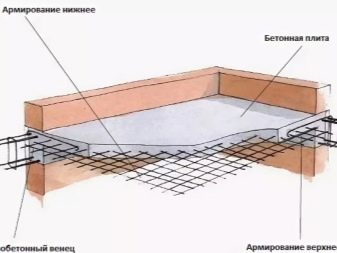
Fulfillment of the specified requirements in the implementation of reinforcement processes guarantees the strength characteristics of the structure being constructed. Reinforced panel, manufactured in compliance with technical conditions, will serve for more than one decade.
What materials are used?
Among other things, you need to worry about choosing the right material that can be used. For the manufacture of floor slabs, as mentioned above, it is preferable to use cement grade 200 and higher. Since it is this cement that is characterized by the highest degree of strength - an indicator that is especially important in the given case. After all, the mass of the panel is approximately 500 kg / m2.
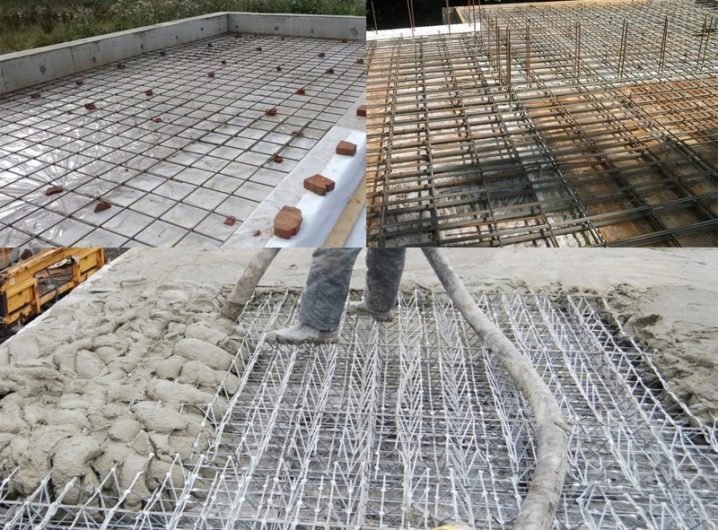
In the role of reinforcement for the slab, mainly metal rods of the A500C class are used. Hot-rolled rebars of periodic profile. The diameter of the bars is determined by the calculation carried out in the developed plan. As a rule, the diameter of the overlap rods is in the range of 8-16 millimeters.
Due to the fact that the monolithic overlap mainly works for fracture, the underlying reinforcement is specifically the underlying reinforcement, which is pulled out during operation. To create it, in some episodes, rods with a larger cross-section are used than for the upper layer. The situation is slightly different in the areas where panels and supports are mated. Here, impressive loads act on the upper rods in a similar way, in this regard, it is additionally strengthened. When the slab is based on columns or between supports that have rather large spans, reinforcement is used that is located in the transverse direction of the reinforced structure, the class of which is A240C or A240 (construction reinforcement with a smooth surface).
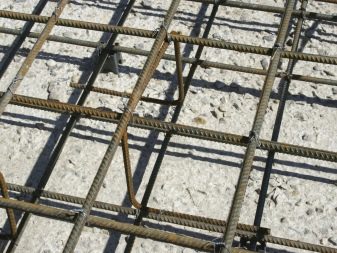
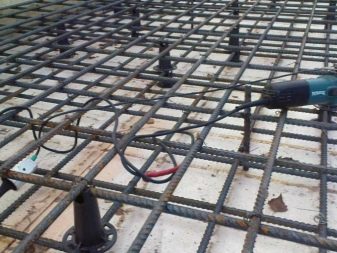
Calculation features
Competent calculation of a monolithic panel for floors and its reinforcement carries many positive qualities.
- A horizontal monolithic panel structure will have a high ultimate load capacity.
- The correct calculation will provide an optimized option for the selection of reinforcement, panel height, grade and volume of concrete. All this together makes it possible to save time and money.
- Highly professional calculation allows, as a support for a monolithic structure, to exploit not only the walls, but also the columns inside the object.
- The calculation will give all the required volumes of work and their value.
- It is possible to calculate a floor panel that does not comply with the configuration standard.
- The service life of a structure built in full proportion to the reinforcement calculations is essentially unlimited.
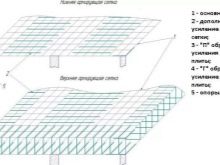
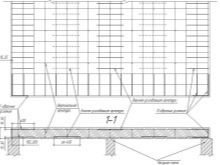
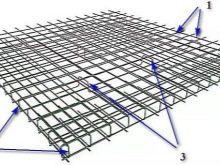
Fundamental rules
Not everyone is capable of making a professional accurate calculation. However, there are uniform standards for the manufacture and reinforcement of a monolithic floor. Based on these rules, the panel height should be 1/30 of the distance between adjacent span supports. For example, with a span of 600 centimeters, the height of the finished monolithic structure will be 20 centimeters. An increase in height will only result in an overrun of expensive concrete.
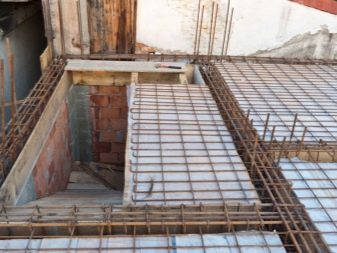
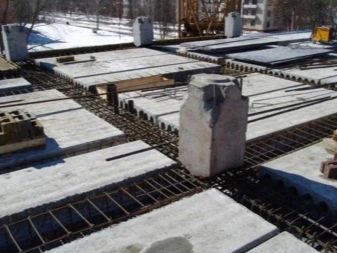
When the length of the overlapping openings does not exceed 7 meters, then the standard calculation method should be used. According to this method, a monolithic panel must be reinforced with two layers of reinforcement. Both layers are laid with reinforcing bars A-500C, having a diameter of 10 millimeters. The rods are placed at intervals of approximately 150-200 millimeters. The connection of the rods into a frame with a cell size of 150-200 millimeters is carried out with a soft knitting wire with a cross section of 1.2 to 3 millimeters. The panel can be reinforced with a standard welded mesh available on the market.
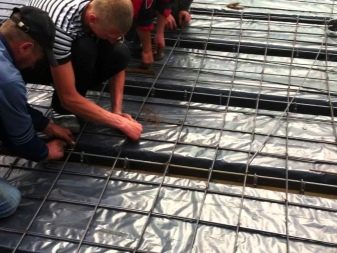
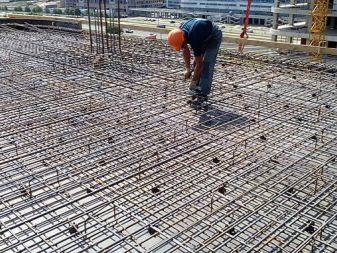
When calculating the dimensions of a monolithic structure, it is necessary to take into account the amount of grip. This is the part of the panel that will fit against the wall. With brick walls, the size of the grip (working surface) should be 15 centimeters or slightly more. For walls made of foam concrete, this size is 25 centimeters or more. Reinforcement rods are cut in such a way that their ends are covered with a layer of concrete mixture with a height of at least 25 millimeters.
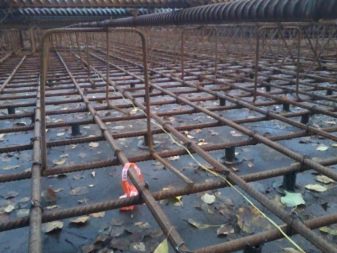
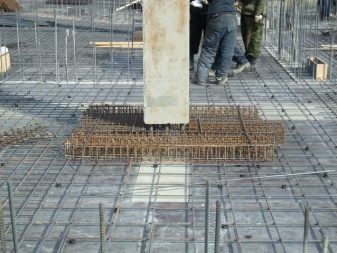
The simplest calculation reveals that with proper reinforcement for one square meter. meter of a monolithic concrete slab with a height of 20 centimeters, the consumption is approximately 1 m3 of concrete grade M200 and above (preferably M350), 36 kilograms of reinforcement grade A500C with a cross-sectional area of 10 millimeters. These are the basic rules. However, only a specialist can perform a careful calculation.
How to reinforce?
The load on non-girder monolithic panels goes vertically downward and spreads proportionally over the entire area.It turns out that the upper side of the reinforcing frame takes on compressive loads, and the lower one takes tensile loads. The rods are laid in the formwork and tied to each other by means of a soft knitting wire. For the underlying skeleton, thick metal rods are practiced. The upper layer is made up of rods with a smaller section.
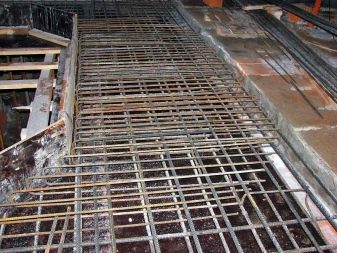
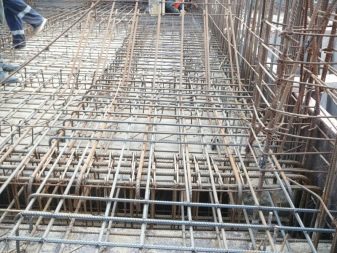
Upon completion of the knitting of the reinforcing meshes, they should be correctly spaced in height.
With a monolithic floor structure height of 180 to 200 millimeters, the span to be covered can extend up to 6 meters. In such panels, the distance between the lower and upper reinforcing mesh is maintained at an interval of 100–125 mm. For this, clamps are practiced, which are made from the remnants of reinforcement with a diameter of 10 millimeters. Long rods are bent into an "L" shape and placed at one meter intervals. In places where reinforcement of the floor panel is required, the distance is reduced to 40 cm. As a rule, this is the middle of the interface with the supports and the area of greatest load.
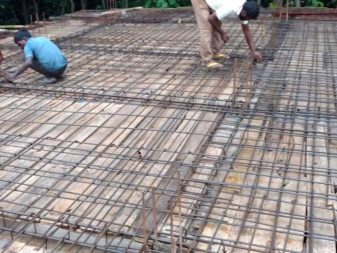
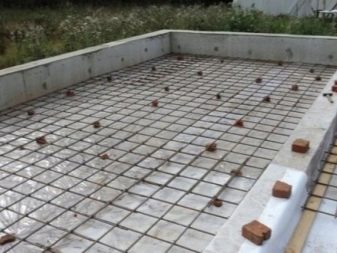
A layer of concrete of approximately 25–30 millimeters, or slightly more, should remain under the underlying panel reinforcement frame. The upper reinforcing mesh is poured with a similar layer. To maintain this size, plastic supports are placed under the intersection of the lower bars of the reinforcement with an interval of about one meter. Such devices are sold in building materials stores. They can be replaced with timber bars nailed or screwed to the formwork using self-tapping screws. If you do not fix their location in this type, then they are able to float when filling the form with a concrete solution.
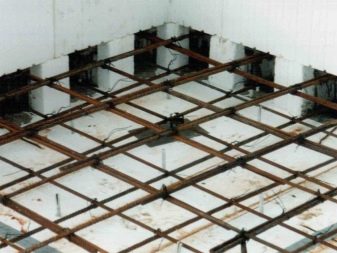
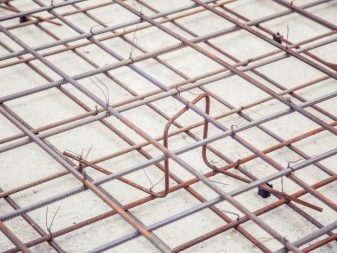
Reinforcement instructions
The construction process consists of a number of steps that need to be implemented in the established sequence.
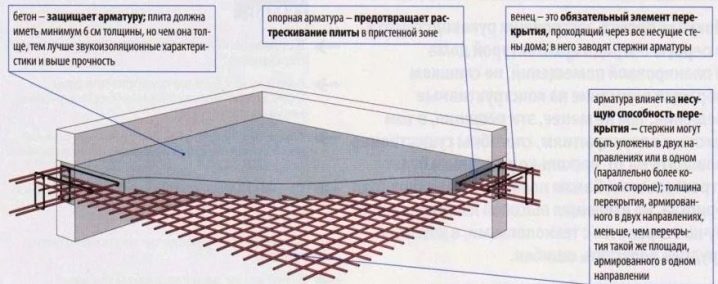
Formwork installation
A collapsible form is made of metal channels, boards and plywood sheets. Under the formwork, special telescopic supporting elements (racks) are placed on reliable and stable tripods. The number of supports should thoroughly support the box, not allowing it to bend under the load of the mortar. With a 200 mm layer height, the weight is 1 sq. meter of concrete solution reaches 300-500 kilograms. Instead of retractable racks, you can practice round timber or wood bars with a section of 100 × 100 millimeters. They are arranged with an interval of 1.2-1.5 meters. Longitudinal beams are placed on the racks and raised to a specified height. After that, the crossbeams are installed, on which the plywood with a moisture-resistant film is fixed on top of the outer layers by means of screws. The permissible thickness is 18–20 millimeters.
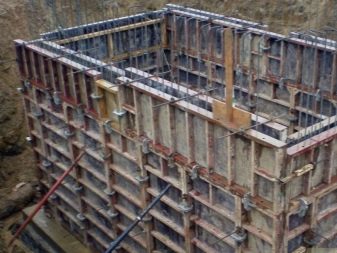
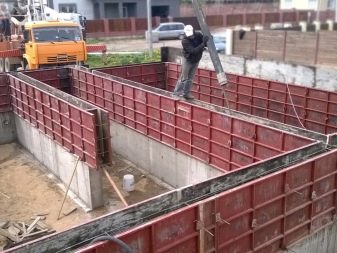
Film-faced plywood can be replaced with ordinary, coated with varnish-based paint. Another type of base is smooth boards covered with cellophane film. The mortar does not stick to a slippery surface - in this regard, the lower part of the floor panel comes out absolutely smooth and even.
How to knit reinforcement correctly?
Layout and knitting of metal rods is carried out according to the design reinforcement scheme. The ideal cell size is 150 × 150 or 200 × 200 millimeters. It is necessary to try to ensure that the sections of the frame running in the direction of length are integral. If the length of the rods is not enough, then the auxiliary rods are laid with a decent overlap. The conjugation zones are arranged in a checkerboard pattern. Such reinforcement guarantees adequate reliability and rigidity of the panel.
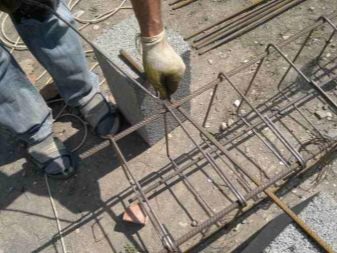
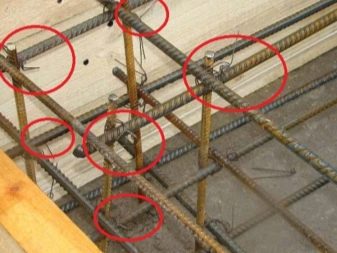
Filling the form
It is advisable to use a prefabricated concrete solution. It maintains the ratio of the components, the mixture includes additives that make better performance indicators. The concrete is subject to reliable control and is brought to the construction site in a volume sufficient for a one-time pouring. By means of a concrete pump, the mixture is distributed directly to the entire space of the panel. The submersible concrete vibrator effectively compacts the mortar and distributes it proportionally over the formwork. In parallel, air bubbles are removed. Upon completion of the pouring, the plane is smoothed with a special trowel on an elongated handle and covered with a thin cover of dry cement.
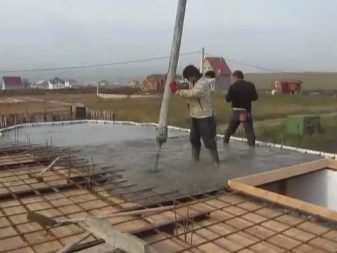
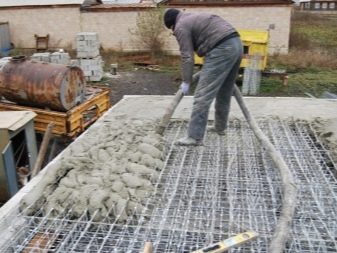
The appropriate temperature of the ambient atmosphere when filling the structure with a solution should be at least +5 degrees. At negative temperatures, the liquid inside the mixture can solidify and break the monolith. Cracking weakens the strength of the panel and shortens its lifespan. At a suitable operating temperature, the reinforced floor will completely harden after a month. The first 3-4 days the concrete is constantly moistened with water in order to retain moisture in it, and in the summer it is additionally covered with a film.
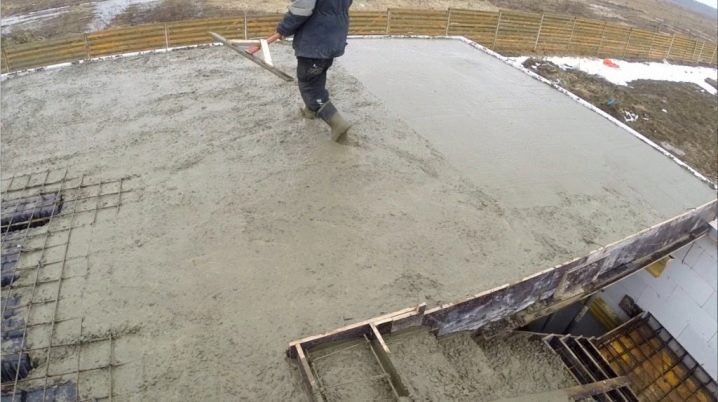
Important! A detailed diagram of the reinforcement of the horizontal enclosing panel must be present in the technical documentation, including the drawings. Having information on how to reinforce the floor panel, it is easy to do the work on your own and save a lot on this. The main thing is to correctly perform the calculations and adhere to the technology.
For information on how to properly fill the reinforcement of the floor slab, see the next video.
The comment was sent successfully.