All about wall insulation with foam

Everyone who dares to do such a thing needs to know everything about wall insulation with foam plastic. The fastening of foam structures in the premises and outside has its own characteristics; it is also necessary to deal with liquid and solid insulation, with its optimal thickness. Additionally, you will have to get acquainted with the grinding of joints and other technological nuances.


Advantages and disadvantages
Any technological solution always has pluses and minuses. This fully applies to foam insulation of various dwellings, auxiliary and service buildings. The most important advantage of this approach is the relatively low cost of funds. Polyfoam itself is cheap and does not require complex installation or expensive fasteners. This material performs its main function - retaining heat - quite effectively.
It is lightweight and can be mounted even on relatively weak walls. This circumstance is very important if their bearing capacity (as in the repair of old buildings) can only be estimated approximately. Styrofoam is also good at restraining the spread of extraneous sounds. With its help, it is easy to ensure peace and quiet in the premises, even if the house itself is located near constant sources of noise.
This material is easy to handle and moisture resistant in both directions.



The weak points, however, are:
- violation of normal air circulation;
- limited service life (actually 15-20 years, although manufacturers claim that their product can work up to 50 years);
- fragility and ability to withstand only light loads;
- tendency to damage by fire and maintaining combustion of adjoining structures;
- "Adoration" of foam by rodents.


Tools and materials
It is worth considering that, at least near sources of open fire, heating devices and electrical equipment, it is advisable to use a non-combustible subtype of polystyrene - penoplex. Its fire hazard is reduced through the use of special additives (so-called flame retardants).
For work you will need:
- the insulation itself;
- glue based on cement or synthetic substances;
- special fungi, which are 40-50 mm thicker than wall foam panels (such fasteners are very helpful when working on verticals and inclined surfaces);
- reinforcing mesh;
- standard polyurethane foam;
- building level and plumb line (one of these tools is indispensable, both are needed);
- typical tape measure;
- electric drill;
- a reservoir for glue and a mixer nozzle for mixing it;
- a hacksaw or a working knife with a set of replaceable blades.


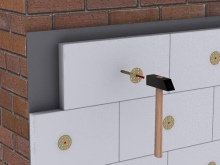
If you use liquid insulation, then it is prepared according to the instructions. When determining the required amount of such a composition, one must remember that it will not expand (more precisely, it will, but the thermal expansion is negligible), but the compression is quite noticeable. Before getting down to work, you still need to determine the exact load from the insulation structures. When calculating, first of all, the dimensions and density of the material are taken into account; correction factors are almost never required.
The Russian GOST stipulates that the foam sheet should have a width of 100 cm and a length of 200 cm. When ordering a large batch, it makes sense to order a cut in a different size. It is easier and more profitable to cut a small amount of material on your own.Sheets of 120x60, 50x50, 100x100 and 100x50 cm are often used.
The optimum density of the material is 25 kg per 1 m3, these are the characteristics of the popular PSB-S 25 brand.
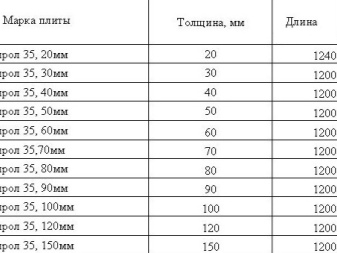

Preparation
Walls inside the house
In wooden rooms, it is very important to fill the crate. In buildings made of natural stone, brick or building blocks, foam insulation is usually carried out using the "wet" technology. Be sure to remove all sockets, switches, lamps, switches and wires connecting them. And also it will be necessary to get rid of even small fasteners. Skirting boards - both on the floor and on the ceilings - must be removed.
It is advisable to remove the previous finish. Therefore, by the way, it is advisable to combine foam insulation with construction, reconstruction or overhaul. All gaps separating the crowns should be cleaned of debris, and then impregnated with an antiseptic. All cracks, except for those that appeared in the wood itself during the drying stage, must be repaired. To eliminate gaps, the following are suitable:
- sealant;
- resin;
- various mastics;
- polyurethane foam.


You can eliminate cracks with sawdust mixed with polyvinyl acetate glue. And also for this purpose they use moss, tow and pieces of fabric. The crate is stuffed last. There is no need to create a vapor barrier - the tree itself will maintain its own optimal humidity. The sequence for installing the lathing is as follows:
- mark the location points of the harness, racks and horizontal rails;
- fix the harness to the wall;
- mount horizontal strapping using metal corners;
- put frame bars (both horizontal and vertical).

Facade
You will have to prepare more carefully for work on the street. Everything is done in several stages. As well as inside, everything unnecessary is removed from the wall, including fasteners. Leave only a flat, smooth surface. Later:
- a plumb line is used to check how vertical the facade is;
- remove blockages with plaster;
- inspect the insulated wall;
- fill up cracks, cracks and recesses with repair mortar;
- beat off by hand beads and protrusions;
- clean the facade that has gained strength from clogging and dust with a metal and soft brush;
- a wooden wall is treated with fire retardants and antiseptics;
- brick, concrete and other stone materials are primed;
- install a supporting profile.


How to insulate correctly?
"Wet" way
This option for installing foam has long proven its promise. In some cases, it has worked confidently for at least 50 years. You will have to glue the structures on the building mixture. Dilute the dry glue mixture in a separate container. All parapets, drips and ebb tides are preliminarily removed - taking into account the fact that the total thickness of the walls is growing, all this will have to be mounted again. If the plaster has time to peel off, it must be knocked down. Then it is dried, primed and dried again (within 2-3 days). It is unacceptable to leave any unevenness more than 30 mm in size. If such deep defects remain, they must be trimmed and primed again. Work should be carried out at temperatures from +5 to + 25 degrees.
Precisely according to the level, they mark where the basement strip will be located. It should be located 2 cm lower than the junction of the wall with the foundation structure. In this case, it is necessary to ensure that it is another 2-3 cm above the blind area. It is necessary to fix the slabs strictly in rows, moving from bottom to top and providing a vertical separation of the joints by at least 20 cm. The first row is placed on a bar that blocks the spread of rodents. Glue is applied around the perimeter of the slab. In this case, the indent from the border should be 1.5-2 cm.In the central part of the slab, glue is applied in the form of strokes in a checkerboard pattern every 20-30 cm.
Leave a gap of no more than 3 mm between the individual fixed plates.


"Well"
We are talking about foam insulation of a two-layer wall system. Installation of boards is carried out either by the usual "wet" technology, or by planting only on glue. The decorative wall is separated from the insulation by a gap of about 35 cm. This is quite enough to ensure air circulation. Otherwise, there will be no differences from the generally accepted technology.

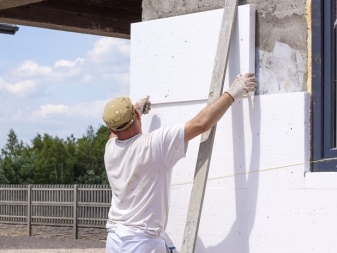
Ventilated facade
This approach is practiced if the facade is to be faced:
- siding;
- clapboard;
- imitating timber material;
- ceramic tiles.
In this case, the fasteners are attached to the lathing. Slabs are inserted into specially selected cells. The absence of loads on the insulation allows you to either directly glue it to the wall, or simply insert it in the right places, limiting yourself to foaming the joints. A vapor barrier membrane will have to be installed over the foam so that the crate does not absorb moisture. It is customary to fasten such a membrane "with an overlap", and glue the seams with a metallized tape. Next comes the counter-lattice, which will have to be sheathed with decorative facing products.
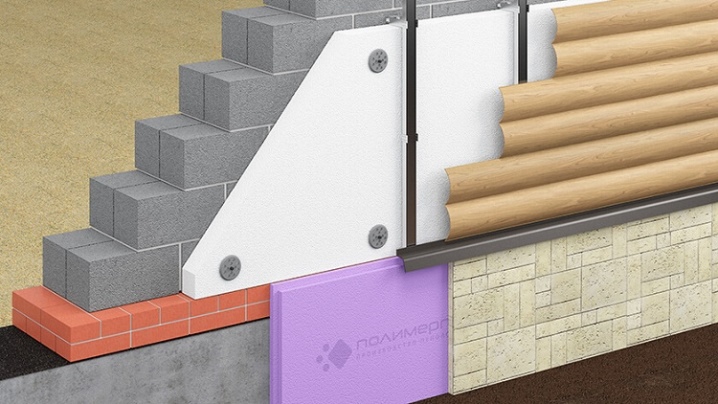
With thermal panels
This is a relatively new kind of foam based solutions. It performs both a protective and a decorative task at the same time. Clinker tiles applied to the surface can reproduce the appearance:
- bricks;
- natural stone;
- other materials traditionally used for facade cladding.


If you mount the structures accurately enough and use high-quality panels, then you can form a monolithic plane, even without small seams and gaps. The standard technology looks like this:
- prepare the facade in the traditional "wet" way;
- dilute glue;
- glue the corner panel;
- cover the main thermal panel with glue using "wet" technology;
- collect all the cover in the manner of a mosaic;
- dowel the fully insulated facade with self-tapping screws and anchor bolts using the provided holes;
- seal the seams so that ultraviolet rays do not fall on the foam.
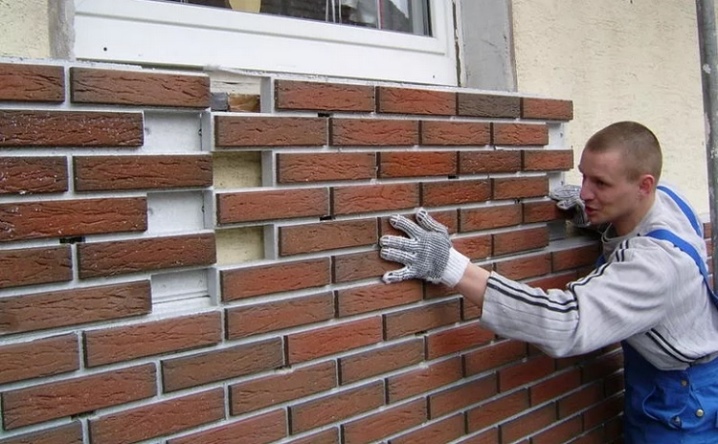
Fixed formwork
This insulation option is also quite simple. Blocks with grooves are interconnected. Thus, hermetically sealed cavities are formed. Reinforcement is inserted there and concrete is poured. When the pouring is completed, the foam is finished from the inside and outside.


Frame house
Making thermal protection on frame walls from the inside with your own hands is carried out using the same technology as outside. Therefore, it is quite reasonable to consider such works in a single block. The technique differs little from the use of basalt wool. However, the insulation can be performed both outwardly and inwardly. The placement of the vapor barrier will depend on this.
The film is placed strictly on one side. The reason is simple: on the other hand, you will have to glue the insulation on the skin. Inside, they are usually sheathed with gypsum board, and outside - with oriented plates. Drywall is usually attached to the frame. Between the frame racks, expanded polystyrene is attached to the gypsum board, a windproof membrane is applied over a thermal layer, and on top of it there is direct finishing or stuffing of counter rails for fastening the finishing material.


When using ready-made branded panels, there is usually no need to grind the joints. The adhesive method of fastening allows the use of a variety of mixtures. Dry formulations are often used. It is enough to dilute them according to the instructions to get the desired result. You can also purchase ready-to-use liquid nails; however, among the ready-made mixtures, especially cheap PVA glue is most often preferred.
Fastening with fungi and other hardware is more laborious. However, it is often more reliable. To achieve maximum effect, glue application and the use of hardware are sometimes combined. In any case, the surfaces are pretreated with deep penetration soils.
The lathing for decorative coverings can also be glued.


The comment was sent successfully.