Features and overview of foam cutting machines
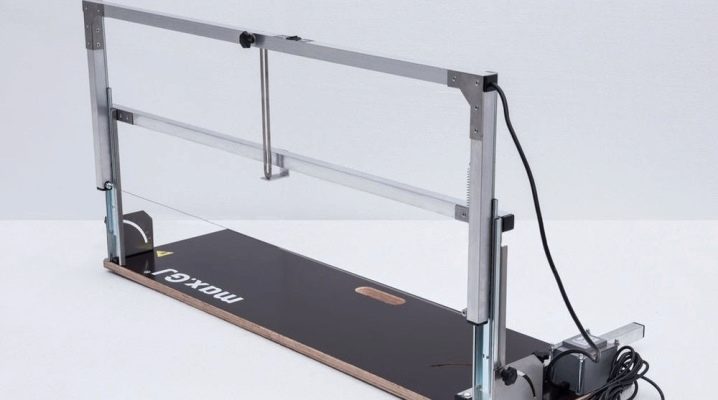
In recent years, a large number of modern thermal insulation materials have appeared on the construction market. Nevertheless, polystyrene, as before, holds the leading positions in this segment and is not going to concede them.

If you intend to insulate the floor in a private house, then cutting polystyrene foam can be dealt with using simple tools, but if a significant amount of work is expected, special machines will be needed.
Description of species
Modern manufacturers offer specialized machines for cutting foam in a wide assortment. On sale you can find models for performing laser, radius, linear, volumetric cutting; shops offer devices for preparing plates, cubes and even 3D blanks. All of them can be conditionally divided into three groups:
-
portable devices - structurally similar to a knife;
-
CNC equipment;
-
machines for cutting horizontally or transversely.
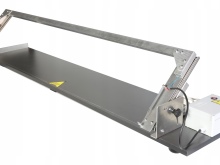

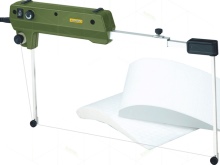
Regardless of the modification, the mechanism of action of any type of machine is in the most general terms identical. The edge, heated to high temperatures, passes through the foam board in the desired direction and cuts the material like a hot knife does butter. In most models, a string acts as such an edge. In primitive devices, only one heating line is provided, in the most modern tools there are 6-8 of them.

CNC
Such machines are similar to milling and laser machines. Typically, CNC machines are used to create blanks from foam as well as polystyrene. The cutting surface is represented by wire with a cross section of 0.1 to 0.5 mm, it is made of titanium or nichrome. In this case, the performance of the device directly depends on the length of these same threads.
CNC machines usually have multiple threads. They are useful in situations where you need to cut complex 2D or 3D blanks. And also they are used when it is necessary to produce products in large quantities.


Portable
Such machines visually resemble an ordinary jigsaw or knife. Most often they have one, less often two strings. Such models are most widespread for self-production in a domestic environment.

For slicing across or horizontally
Depending on the method of processing foam plates, tools are distinguished for transverse and longitudinal cutting of blanks, as well as installations for the production of products of a complicated configuration. Depending on the type of tool, either the thread or the foam itself can move during operation.

Popular models
The most popular are several models of units for cutting foam plastic from Russian and foreign manufacturers.
- FRP-01 - one of the most popular units. The high demand for it is due to its versatility, combined with the simplicity of the design. The equipment allows you to cut letters, numbers, intricate shapes, and produce molded elements. It is used for cutting insulation boards and many other structures. The control of the device operation is carried out by means of the special software included in the kit.
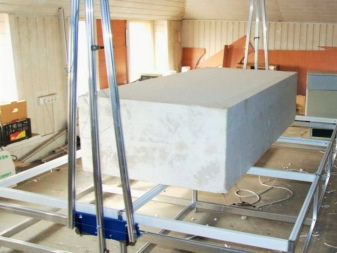

- "SRP-K Kontur" - another common model that helps to carry out all kinds of facade decoration elements, as well as formwork for pouring building mixtures.The control method is manual, but this is fully compensated by the relatively low power at the level of 150 W. Refers to mobile modifications that are convenient to transport from one workplace to another.
- "SFR-Standard" - CNC machine allows to perform figured cutting of polymer plates and polystyrene foam. The control is carried out via a USB port, it is possible to rotate one or several functional circuits. It is supposed to connect up to 6-8 heating threads. At the exit, it allows you to get workpieces of both simple and complex shapes.

The following products are slightly less common.
- "SRP-3420 Sheet" - a device for cutting linear elements made of polystyrene, characterized by increased efficiency and high cut quality.

- FRP-05 - compact installation in the form of a cube. Allows you to cut in 3 planes. The design provides only one nichrome thread, if necessary, its thickness can be changed.

- "SRP-3220 Maxi" - a tool for creating garage, packaging products, as well as shells for steel pipes.
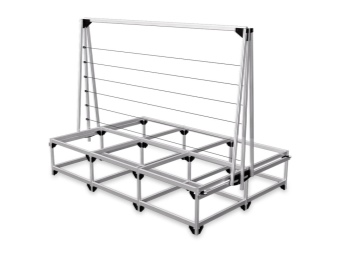

How to do it yourself?
There are many ways how you can make a DIY installation for cutting polystyrene foam. Most often, the simplest hand tools are made at home.
When using a simple knife, preference is given to models with notches. It is advisable to lubricate it with automobile oil even before starting work - this will optimize the cutting process, besides, it will significantly reduce the noise level. And at the same time, this method is the slowest.
Therefore, in practice, it is used only if it is required to process a small amount of foam.
With an insignificant thickness of expanded polystyrene, the use of an ordinary clerical knife is allowed. This is a very sharp instrument, but it tends to dull over time. To increase the efficiency of the work, during the cutting process, it needs to be heated from time to time - then it will more smoothly pass through the material.

A special knife with a heating blade can be adapted to cut the foam, and can be purchased at every hardware store. All work with such a tool must be done strictly from oneself, otherwise there is a high risk of slipping and injury. The disadvantage of such a knife is that it allows you to cut the foam of a strictly defined thickness. Therefore, to obtain even workpieces, it is necessary to accurately mark the foam as possible, and this can take a lot of time.

As an alternative to the heating knife, you can take a soldering iron with specialized nozzles. This tool has an elevated heating temperature, so it is important to be careful during operation. If the molten foam comes into contact with the skin, it can cause burns and cause significant discomfort and soreness.
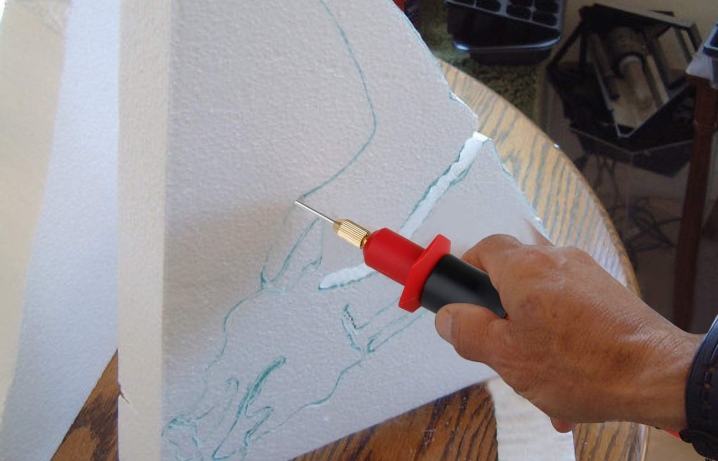
A boot knife with an extended blade up to 35-45 cm can be used to cut Styrofoam slabs. In this case, it is important that the tip is blunt and the blade is as wide as possible. Sharpening should be as sharp as possible.

Advice: it is advisable to make a sharpening adjustment every 2 m of the cut foam.
The course of cutting polystyrene foam with such a tool, as a rule, is accompanied by a strong squeal. To minimize discomfort, it is best to stock up on headphones before work.
Thick pieces of polystyrene are cut with a hacksaw on wood, always with small teeth. The smaller the teeth are, the higher the quality of the finished product will be. However, a perfect cut cannot be achieved with this method. No matter how neat the work, seizures and chips will be present in any case. Nevertheless, this is the easiest way to cut polystyrene foam, which does not require significant physical effort. Most often used for cutting long straight pieces of foam.

The most popular method is cutting slabs with a string. The performance of such a home-made device can be equated with the use of specialized industrial equipment. In this case, the string can be used for expanded polystyrene of the most different degree of density and grain size parameters.
It is not difficult to make such a tool - you just need to hammer a couple of nails into the wooden planks, stretch a wire of nichrome between them and connect to the AC network. The main advantage of such a technique is its increased speed, a meter of foam can be cut in just 5-8 seconds, this is a high indicator. In addition, the cut is very neat.
However, this method is one of the most dangerous and can harm human health. To avoid the risk of injury, cold wire cutting is used. In this case, a steel string is used, it works in the manner of a two-handed saw. This technique is considered one of the most productive.

Sometimes it becomes necessary to use a grinder. It usually works in conjunction with a thin disc. Keep in mind - such work involves increased noise generation and the formation of debris from foam fragments scattered throughout the site.

There is also a more complex method of making a foam cutting machine in everyday life. It is usually used by experienced craftsmen with good skills in drawing, electrical assemblies and parts. To assemble such a device, you will need:
-
a thread of nichrome with a cross section of 0.4-0.5 mm;
-
a wooden lath or other dielectric to create a frame;
-
a pair of bolts, their size is selected taking into account the thickness of the frame;
-
two-core cable;
-
12 V power supply;
-
insulating tape.






The step-by-step instruction assumes the following stages of work.
-
A frame in the shape of the letter "P" is assembled from rails or other materials at hand.
-
One perforation is formed along the edges of the frame, bolts are screwed into these holes.
-
Nichrome wire is attached to the bolts from the inside of the frame, and a cable from the outside.
-
The cable on the wooden frame is fixed with electrical tape, and its free end is brought to the terminals of the power supply.



The styrofoam cutting tool is ready. It can be used not only for cutting polystyrene, but also for plastic bottles and other polymer blanks with reduced density and low thickness.

Important: Keep in mind that when cutting the foam with a heated tool or laser, volatile toxic substances will start to be emitted. That is why all work should be performed in a well-ventilated area and wearing a protective mask, otherwise there is a high risk of poisoning. Cutting outdoors is the best solution.
For more on how you can make a foam cutting machine, see the video below.
The comment was sent successfully.