Do-it-yourself ceiling decoration with plastic panels

It is difficult to overestimate the importance of plastic in the life of a modern person. This material has penetrated into various spheres of human life, and in construction and decoration it is used absolutely everywhere.
One of the stylish and practical ways to finish the ceiling is made of PVC panels. A specialist with little experience in repair or even a beginner will be able to collect them.
In our article, we will talk about how to build a ceiling from panels on your own and save on wages for finishers, whose services are by no means cheap.
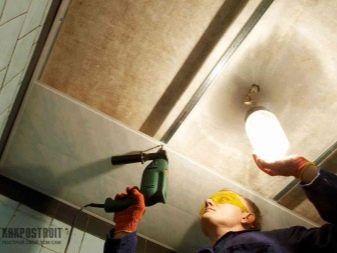

Choice and difference from wall
Ceiling PVC panels consist of two sheets of plastic, which are attached with special stiffeners. A large fastening strip runs along the length of the sheet on one side, and a small fastening strip on the opposite side. The large one is used to fix the PVC sheet to the frame, and the small one is used to adhere the sheets to each other.
All parts have a spike on the side, which contributes to greater structural strength. Ceiling panel manufacturers guarantee that the product will last 10 years.


Ceiling panels are conventionally divided into several types.
By the type of connection, there are:
- suture - after installation, there is a visible joint between the individual parts;
- seamless - the joints remain invisible to the outside view.


Several types are distinguished depending on the color scheme.
- Solid panels are simple yet practical and are UV resistant. They do not change their shade throughout the entire period of operation.
- Lacquered - the surface of such panels is treated with a glossy layer of varnish, which strengthens the panel and also gives it a stylish decorative look. The disadvantages of such models include the appearance of scratches with minimal physical impact.


- With a pattern - a pattern is applied on the outside of the product. Such panels are made from softer plastic, so their price is lower, but the service life is also shorter.
- Laminated - panels imitate natural wood and stone, they are extremely sensitive to sunlight, under the influence of UV rays they begin to crack and lose their consumer properties.


Plastic panels have a number of advantages over other finishing materials.
- they last longer than materials of natural origin;
- reliably protect the ceiling from the adverse effects of external factors;
- the material is easy to use, divided into sheet, plate and rack. they are easy to care for and can be wired underneath (for example, plaster does not allow wiring).
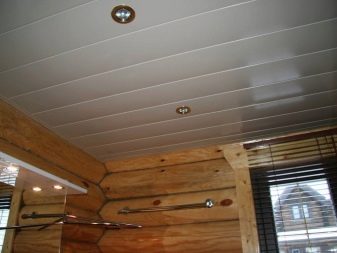

Panels can be of different standard sizes. The length of the ceiling slabs is 270, 300, 400 and 600 cm. And the width ranges from 10 to 25 cm. Long panels are most often used in spacious rooms (industrial compartments, garages), and shorter ones are widely used in the repair of residential buildings and apartments. ...

According to their shape, the panels are subdivided into sheet, slab and rack.
- Sheet panels, as a rule, are large, they are fixed to the ceiling using small nails, and the gaps are rubbed with special sealants.
- Tiled panels in their design resemble ordinary tile-tiles, are small in size, differ in aesthetics and ease of use.
- Rack materials look like lining, and they are mounted in the same way using special construction brackets.

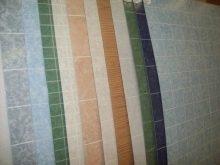

Ceiling panels differ from wall counterparts. Wall ones are much heavier and more durable, since they must withstand additional stress (shelves / furniture / other decorative elements). Ceiling slabs, on the other hand, are thin and fragile. They are lightweight, which greatly facilitates their installation and fixation on the ceiling. At the same time, it is easier to damage them, but this cannot be considered a disadvantage - the ceiling has a minimum of physical impact, so there is simply no need for the panels to have a dense structure.


Pros and cons of the material
The main material for the production of ceiling panels is polyvinyl chloride, it is a very durable material with a number of undeniable advantages.
- has a low cost - any average Russian can afford stylish PVC cladding;
- differs in versatility - it is used in rooms of any type, style and purpose;
- hygroscopicity - plastic does not absorb water, shows resistance to the adverse effects of the external environment, does not deform and does not sag under the influence of humidity and temperature extremes;
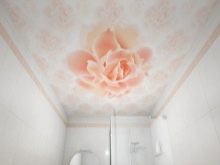


- the material is impact-resistant and wear-resistant - it is not subject to damage due to impacts of medium and low force, but, of course, if you hit such a coating with an ax with all your strength, it will break, but the material is reliably protected from minor scratches and chips;
- the long service life of plastic is well known - if the product is of good quality, then the most unpleasant thing that can await the owner of the plastic ceiling over time is an insignificant change in color, and even then only in those cases when it is under constant exposure to sunlight;
- PVC panels are resistant to aggressive acid-base compounds, they can be easily washed with any cleaning agents;


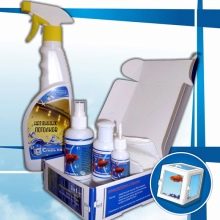
- the material is characterized by good sound insulation and is an excellent choice for those who love peace and quiet;
- PVC panels are not afraid of floods - if neighbors unexpectedly flood you, then the panels can be easily removed, dried and hung back;
- if one of the panels loses its original gloss or breaks, then it is easy and simple to replace, such a repair does not require replacing the entire ceiling covering.


However, the material is not devoid of disadvantages. In particular, the ceiling cannot be installed in rooms where the air temperature is constantly high. In such conditions, the coating quickly deforms; there will be no way to repair it. Plastic, especially if it is of poor quality, can release harmful and toxic substances. That is why you should abandon its use in bedrooms and children's rooms.


High-quality building materials a priori must be combustible. In practice, unfortunately, it turns out differently, and then tragedy cannot be avoided. To prevent this from happening, you should only purchase products from trusted manufacturers.


Calculation, tools and accessories
As already mentioned, the thickness of modern ceiling panels ranges from 5 to 10 mm, the width is 250-500 mm, and the length ranges from 2700 to 3000 mm.
To calculate the required number of panels, you should calculate the area of each panel, for this, its length is multiplied by its width. Then you should make similar calculations and calculate the ceiling area. Everything is simple here: the ceiling area should be divided by the area of one panel, and then add 15-20% in reserve. If, as a result of calculations, a fractional number is obtained, it is better to round it up.


It is equally important to correctly calculate the required number of rails and metal profiles. To do this, you can draw up a diagram: draw a reduced plan of the ceiling, draw longitudinal lines, setting a distance of 500-600 mm between them - this is how the amount of required material is obtained.Well, the number of screws is calculated based on the number of profiles and the standard fixing pitch of the fasteners of 30 cm.
In each calculation, you need to add a margin. As practice shows, people with little work experience often have to buy additional components necessary for finishing.

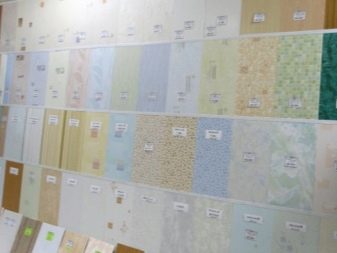
Preparation
When carrying out preparatory work prior to finishing the ceiling, it is not enough to calculate the amount of required materials. It is worth focusing special attention on the presence of cracks, chips and other surface defects.


The following is a complete list of tools that you may need to work with.
- A puncher will be needed when installing the frame.
- The screwdriver is used when attaching panels to beams or metal profiles. In principle, a puncher can be used for this purpose, but it is quite heavy, so it will be difficult for a beginner without work experience to cope with it.
- A construction stapler is needed if the ceiling panels are fastened with brackets.
- The level is used to improve the accuracy of marking.

- Marker - for various markings.
- Roulette.
- Circular saw or jigsaw - will be required at the stage of installation of the frame for cutting off the profile elements.
- Ladder. Since it is supposed to work at height, therefore, a fulcrum is needed. In the absence of a stepladder, you can use a regular table, but a professional tool is still safer and more reliable.


- Rubber mallet - used when adjusting PVC panels.
- Corners.
If you plan to design decorative elements, then you should purchase a molding.


After all the necessary calculations have been made and the tools have been purchased, you can proceed to surface preparation and finishing directly.
To do this, do the following:
- the old coating is removed;
- all lighting and electrical equipment is disassembled;
- the ceiling is cleared of dust and dirt.


After that, you should tap the surface of the ceiling with a hammer - this will allow you to detect defects that must be corrected before starting work.
The preparation is finished by applying a primer. After the surface dries out, start installing the ceiling directly.

Mounting options
All work on finishing the ceiling with PVC panels can be easily and simply carried out even by a non-professional. Nevertheless, you should know the basic nuances of various installation methods.
As a rule, the panels are fixed either framelessly or using a hinged frame.

Lathing
One of the ways to mount the panels is to attach them to the frame. This is especially true when it comes to uneven surfaces. The basis of the frame is the lathing. This is a device that allows high-quality installation in rooms of any type (with a high level of humidity, unheated, etc.). To install the frame, the involvement of specialists is not required, all work can be done by hand.


To fix the lathing, you should use a wooden beam, plastic or metal profile strips.
The choice of material depends on:
- the height of irregularities on the surface of the ceiling;
- indoor moisture level;
- experience of the master with materials of different types.


Plastic lathing is easy to install. It can be used in rooms with any level of humidity, in addition, plastic is a cheap material, which is also a plus of such a crate. Since the elements of the PVC frame are small in thickness, such ceilings can be glued in rooms with low ceilings. In this case, the height will decrease very slightly.



However, on the shelves, plastic profiles for the lathing are rare guests. Finding them on the free market is quite problematic. The disadvantages of overlapping include the possibility of using it only on flat surfaces. If the defects in the base exceed 5 mm, then it will not be possible to achieve a perfect coverage.
Metal and wooden battens are more popular due to their affordability, durability and resistance to adverse weather conditions. These materials have long and firmly established themselves as the most optimal for the production of cladding for the ceiling and further fastening of ceiling tiles.


Hanging frame
High-quality finishing of the ceiling with panels is a simple matter, but it requires great accuracy and meticulousness.
Frame structures are used in rooms with a high humidity index, as well as in poorly heated rooms. Otherwise, the coating will quickly deform, and over time it will become unusable and simply disappear.

The frame is a crate, which is attached with a standard pitch of 40 cm. The panels are then screwed directly to the suspended frame. You can sheathe them with nails or self-tapping screws.

It is not necessary to cut the panels in advance, this can lead to unpleasant surprises and unnecessary damage to the material. It is more expedient to cut the slabs in fact, applying them to the crate and fixing the boundaries of the required element.
Last but not least, it is necessary to dock the panels and decorate the joints; for this purpose, skirting boards and styrofoam borders are used, which are installed with liquid nails.
As you can see, there is nothing difficult in fixing the panels to the ceiling; even an amateur in decoration can handle the work.


Frameless way
An easier way to install ceiling tiles is considered to be a frameless method. In addition to the above materials, in this case, you will need glue, on which the plates on the ceiling will be fixed.


Recommendations for performing such work:
- the surface to be treated is cleaned of dust and dirt, and then primed and covered with an adhesive (it is best to use a notched trowel);
- on the reverse side of the panel, glue should be applied in strips or in dots;
- the panel should be fastened to the ceiling with force for a few seconds;
- after the pressure has ceased, the panel can be released and its location corrected.


This method has one significant drawback - it does not allow to sew spotlights, LED strips and other light elements, therefore, for example, a two-level ceiling will not be effective enough. That is why, even before starting work, you should consider a way to strengthen the panels so that you do not regret the missed opportunities in the future.


Manufacturers
Venta Is a Belgian company, a leader in the construction market. Panels with a wide variety of technical parameters and designs are produced under this brand. Most recently, the company has mastered the production of digital printed panels.
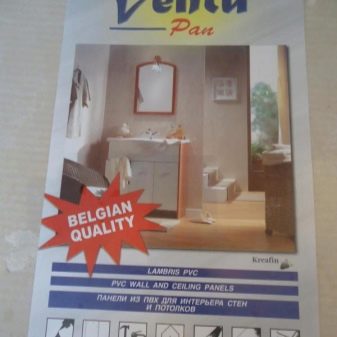

Forte - a manufacturer from Italy with a worldwide reputation. It has been successfully producing and selling its products on the market since 1969. The company owes its success to the introduction of the most advanced technologies, continuous improvement of the organization's management and strict control over quality systems. The company is trying to put on the market a wide range of products that allow you to implement any design ideas in your home.
Russian factory "Planet Plastic" from Moscow has been presenting its products on the domestic market since 2001. All production is based on the use of imported materials and is carried out on foreign equipment. The company offers its customers more than 150 types of panels.


Another manufacturer - Ural-Plast from Magnitogorsk. The production facilities of the company also work at the expense of imported equipment, the breadth of the assortment here is formed by stylish, original and truly exclusive designs.
Manufacturer "AnV-plast" from Krasnodar made a name for himself in 2001 and in a short time achieved success in his industry.The company adheres to the principle of supporting a domestic manufacturer, therefore, all raw materials for the manufacture of PVC plates are purchased only from Russian firms, which significantly reduces the cost of production and makes it available to most compatriots.
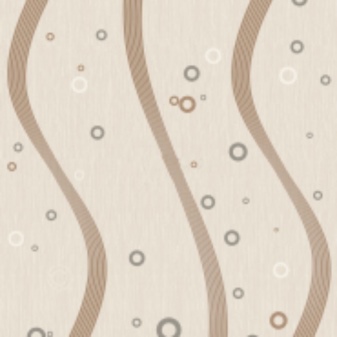

For installation of plastic panels on the ceiling, see the following video.
The comment was sent successfully.