Standard sizes of MDF panels
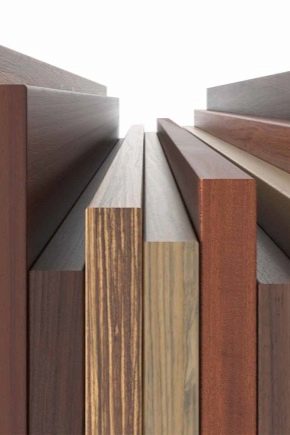
Recycled wood trim panels have been used in renovation and interior decoration for decades. Plywood, fiberboard, chipboard, panels from pressed sawdust - the assortment is very wide. These are environmentally friendly, high-quality and durable materials, the production of which allows the use of affordable and cheap waste from the woodworking industry.
Working with recycled wood is easier than working with natural wood, and its cost is much lower, making the material available to most Russians.
Over the past 20 years, MDF boards have firmly ousted the usual chipboard and fiberboard from the market: it is quite problematic to find the latter in stores, but MDF is presented in any building supermarket in all its variety of sizes, textures and shades.
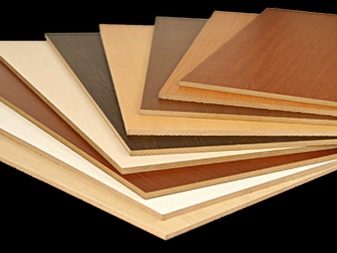
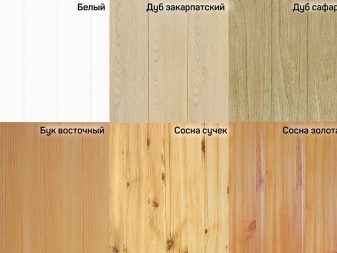
Peculiarities
MDF stands for fine fraction. The panels are made from medium density wood fibers, compressed under high pressure.
The material has all the advantages of natural wood, but its structure is heterogeneous and not solid. The raw material for the production of boards is fine shavings, which are compacted on professional equipment with the addition of adhesives.
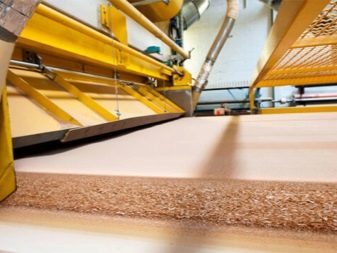
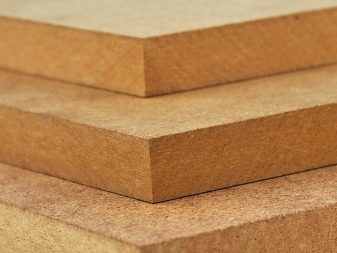
Dignity
The density of MDF products leads to a variety of applications in the construction sector, as well as in the manufacture of furniture.
MDF has many advantages:
- homogeneous structure;
- high noise insulation;
- thermal insulation properties;
- attractive appearance;
- ease of processing and installation;
- versatility;
- environmental friendliness;
- hygroscopicity;
- hygiene.
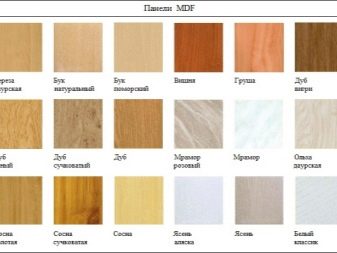
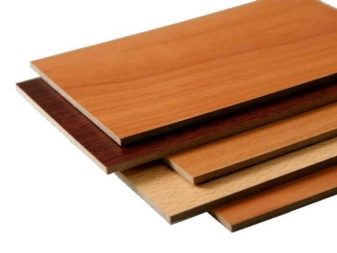
Benefits of MDF
MDF, in comparison with similar building materials, has undoubted advantages.
Compared to plywood
- does not have external defects inherent in typical plywood sheets (veneer overlap, cracks, wood knots falling out);
- does not deform under the influence of steam;
- has perfect geometry;
- more affordable prices.
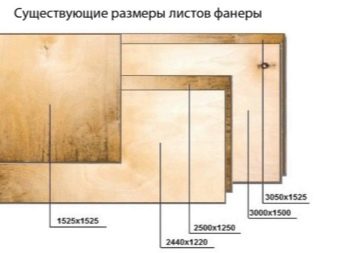
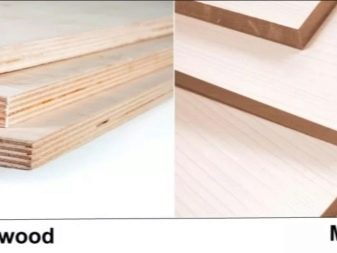
Compared to wood
- uniformity of the structure throughout the thickness;
- absence of any knots, voids and other natural defects;
- the possibility of embossing the coating;
- resistance to mold and dangerous fungi;
- the price difference reaches 80%.
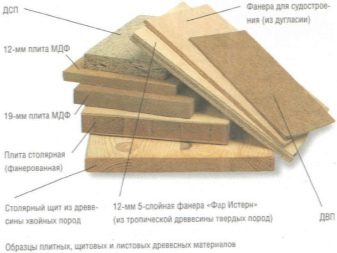
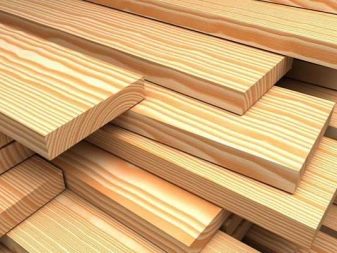
Compared to fiberboard and chipboard
- allows for edge milling;
- more environmentally friendly material;
- it has a high density, due to which it holds the base of the furniture well;
- the surface can be laminated;
- does not deform under the influence of moisture.
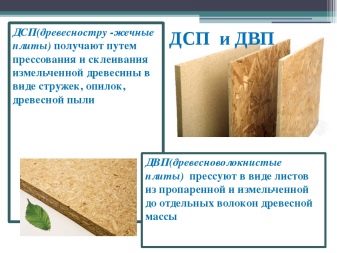
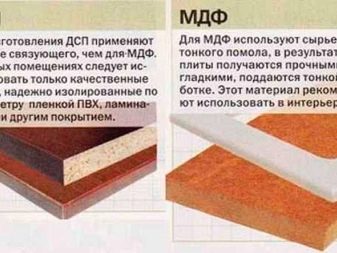
Sizes of MDF boards
: Depending on the standard sizes, MDF boards are subdivided into:
- rack - they have a narrow long shape;
- tiled - square or small rectangular;
- leafy - are large.
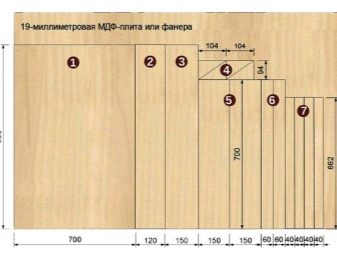
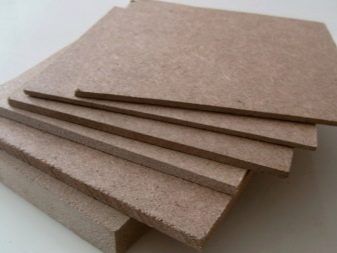
Classification by processing method
According to the processing method, they are distinguished:
- flat slabs - obtained as a result of pressing;
- embossed - are created by milling, stamping or applying decorative elements;
- laminated - pasted over with a special protective layer consisting of a polymer film (transparent or matte);
- veneered - wood of valuable species is usually used as veneer in order to imitate the texture of natural wood;
- painted - coated with special paints containing dyeing matte or glossy pigments, as well as anti-dust additives.
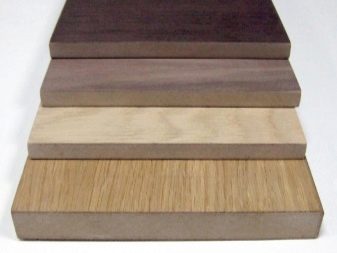
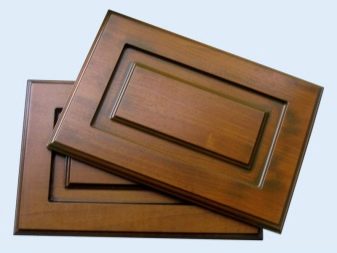
disadvantages
Despite the obvious advantages, the products also have disadvantages. One of them is low resistance to combustion and high temperatures. In the event of a fire, the panels are deformed, which significantly limits the scope of use of MDF: such plates are not recommended for installation near fireplaces, gas stoves and other sources of fire.
Another disadvantage of the panels is low wear resistance. The material is easy to scratch or crack and should not be used for high traffic areas or homes with small children.
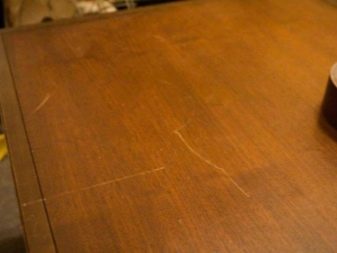
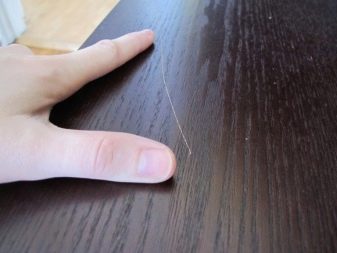
Size range
If we talk about sizes, then their range is also quite wide. Today, the most common are:
- length - in the range from 2.4 to 2.7 m;
- width - from 150 to 900 mm;
- thickness - from 3 to 60 mm.
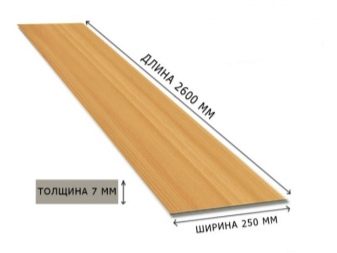
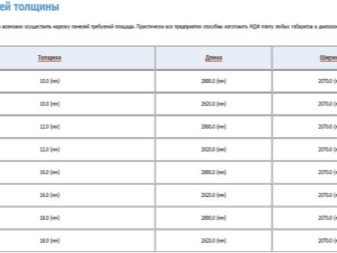
Length
The typical length of the wall panel is 2.62 m, while some manufacturers have launched products with a length of 2.44 and 2.8 meters. For installation, this does not really matter, especially since sawing is usually done directly in the store.
The parameters and dimensions of the boards differ depending on the MDF manufacturer. So, for example, the popular Kronospan brand produces panels with dimensions of 2600X200 mm, 2600X325 mm, 2600X153 mm and 2600X200 mm. The world-renowned manufacturer HDM offers panels with parameters 1300X198 mm and 2600X198 mm. Finally, the Russian firm "Soyuz" produces panels in a uniform size 2600X238.
Each of the manufacturers (within their size range) produces a wide variety of panels that differ in texture and color scheme.
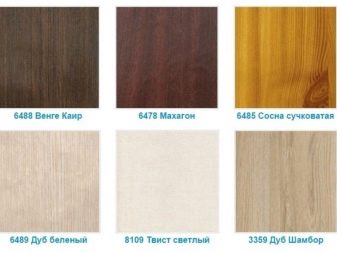
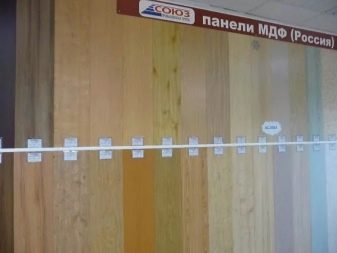
Thickness
Depending on the brand of the manufacturer and the chosen model, the thickness of MDF varies from 3 to 30 mm. In addition, individual enterprises produce veneered modifications, the thickness of which reaches 60 mm.
Thanks to this variety, each consumer can always choose the best option, taking into account the dimensions of his premises.
By the way, the thickness of the panel is quite important when choosing a suitable finishing material: the weight of the product and the load that it can withstand depends on it.
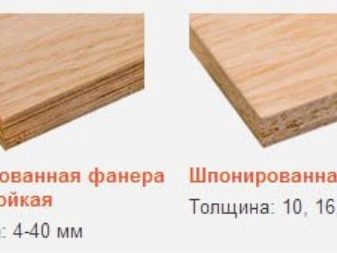
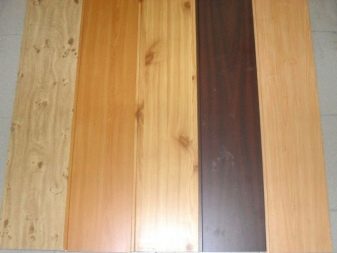
Standard panels weigh:
- with a thickness of 3 mm - 16 kg;
- 6 mm - 31 kg;
- 12 mm - 60 kg;
- 22 mm - 106 kg;
- 28 mm - 142 kg.
Under the Kronospan brand, panels are produced with a thickness of 7.8, 9 and 14 mm. Among the HDM products you can find narrow MDF boards (only 6 mm thick). Some manufacturers have models with a thickness of 10 and 18 mm.
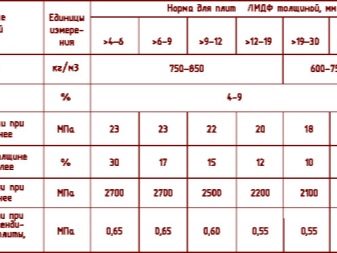
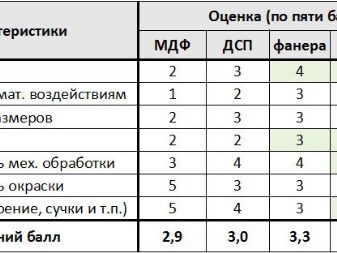
Width
The standard width of the panels is 150-190 mm, it is very rare to find 900 or 1200 mm MDF on the free market. The width largely determines the aesthetics and decorativeness of the finish: the wider the panel, the fewer butt joints on the coating and the smoother the surface appears.
Scope of application
The extremely positive performance properties of MDF, combined with environmental friendliness and affordability, have made these boards popular in a wide variety of construction, interior decoration and industrial sectors. The wide assortment made it possible to widely use the panels during repair and finishing works, as well as for the manufacture of furniture.
The ability to sound absorption and thermal insulation led to the use of the material for the production of wall plates, doors, interior partitions and other decorative elements.
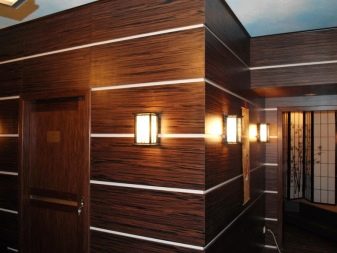
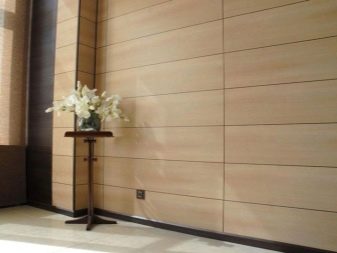
MDF, due to its high density, is considered the optimal material for the production of joinery. Also, panels are used for rough laying of floor coverings and final leveling of walls. And, of course, panels are widely used to create office and cabinet furniture.
Hygroscopicity and resistance to mold and mildew have led to the fact that the boards have become popular in furniture for medical facilities, laboratories, as well as living rooms with a high index of humidity (bathroom and kitchen).
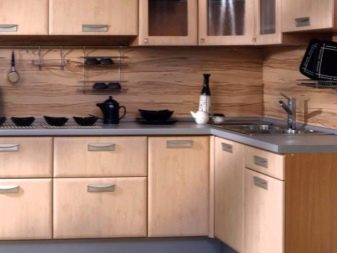
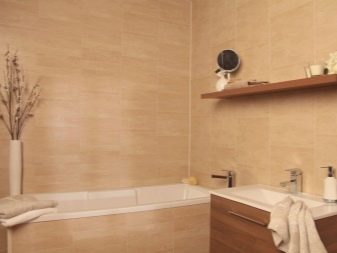
The scope of use of MDF is wide and varied:
- sheet-type panels are widely used for laying ceilings and floors;
- wall decoration with MDF plates is very common;
- used as a connecting material for the formation of frame facades;
- production of all types of furniture;
- for soundproofing rooms - panels significantly reduce the audibility between rooms, therefore they are used in panel houses, as well as for cladding the walls of the parent's bedroom in houses with children;
- an unusual scope of application of the material - the restoration of old steel doors, MDF is used as a coating, transforming and updating the look of an old door that has lost its luster;
- for the arrangement of slopes.
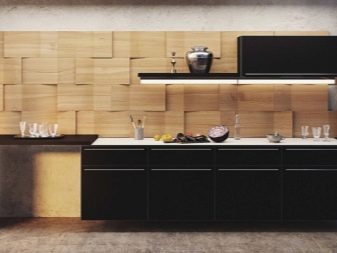
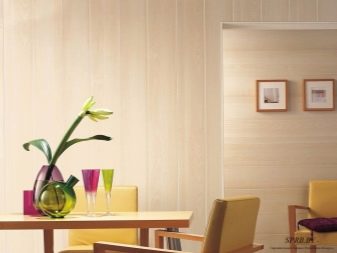
When using panels, the parameters of length, width and thickness of the material come to the fore. If there are practically no restrictions for wall cladding (the size of the slabs depends on the personal preferences of the owner of the room), then for other categories, the scope requires specific dimensions:
- kitchen aprons - it is optimal to use slabs 3 m long, 60 cm wide and 6-10 mm thick;
- countertops - this element is subject to loads and pressure, therefore, a panel thickness of 28-38 mm is required here, the parameters of length and width, as a rule, are 1 meter and 60 cm, respectively;
- doors - interior doors made of MDF are manufactured in accordance with the accepted standard: the thickness is 35-45 cm, the length is 190-200 cm, and the width is 70-90 cm.
The material belongs to the category of wear-resistant, however, it is noticed that morally it becomes obsolete before it wears out physically. That is why it (in the overwhelming majority of cases) is used for cladding non-residential premises: an entrance hall, a corridor, a bathroom, loggias and balconies, as well as utility blocks.
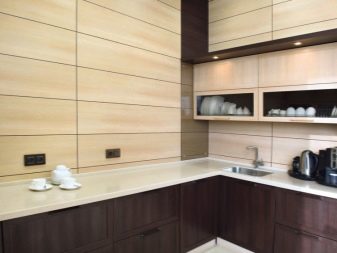
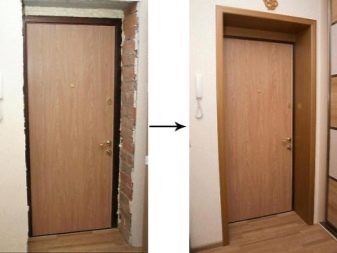
Tips & Tricks
In accordance with how you decide to use the MDF boards, the panel parameters must be taken into account. In each individual case, one should focus on the highest possible indicators:
- So, painted panels will be optimal for the manufacture of kitchen furniture. They are hygroscopic, do not deform or crack with frequent contact with water.
- But this is not enough for shower and bathroom cabins - here it is better to purchase laminated plates, which are distinguished by increased moisture resistance, and the lamination should be two-sided to protect the product both from the outside and from the inside.
- When working on furniture facades, use veneered modifications. If we are talking about facing large volumes of coverage, then standard tiled MDF will do.
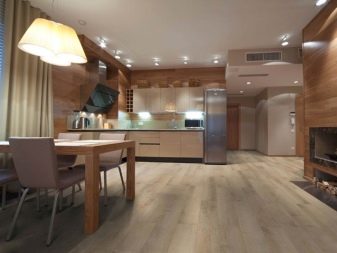
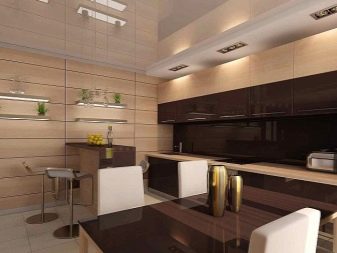
The board manufacturer is also of great importance. Models from Swedish, Polish and German manufacturers are of high quality. By the way, companies from these countries have their offices in Russia, so the cost of their products is affordable for most of our compatriots.
Chinese products occupy a significant market share. It attracts with a low price, however, its quality does not always please consumers with its wear resistance and durability.
You can find many Russian-made products on the shelves of building stores. Small companies produce MDF panels, the quality of which is often in no way inferior to European counterparts. Unfortunately, sometimes a model of an inappropriate level with low moisture resistance and a short service life is hidden under an attractive appearance.
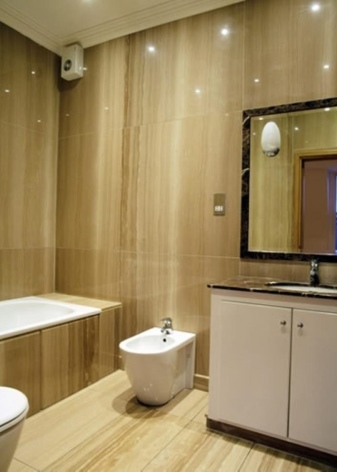
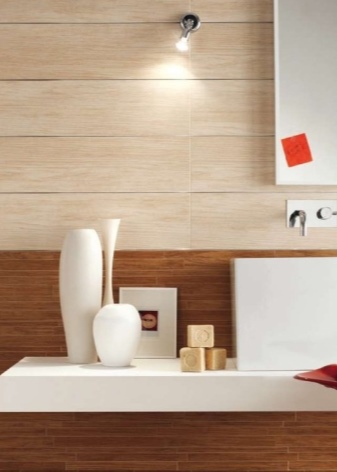
Regardless of which brand you decide to give preference to, it is worth conducting the most thorough inspection of the panels upon purchase.
The inspection procedure boils down to the following steps:
- inspect the product and make sure there are no various chips and cracks;
- the surface must certainly be flat and smooth to the touch, any depressions or, conversely, bumps serve as sources of deterioration in the strength of MDF and a decrease in its operational parameters;
- the appearance of any smell from the plates is unacceptable.
It is imperative to study the certificates and documentation on the panel, in particular, focus on such an indicator as the degree of swelling of the panel upon contact with liquid. Its optimal value is 17%.
And, of course, the choice of panels largely depends on the degree of skill of the finisher. If this is the first time you come across this material (and in general you have little experience in finishing), then give preference to thick models: they are stronger and more reliable. In turn, thin MDF boards are quite fragile and can break from illiterate handling.
For information on how to mount MDF panels on the wall, see the following video.
The comment was sent successfully.