How is MDF different from particleboard?
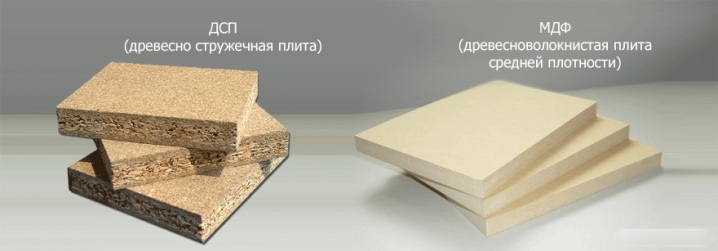
MDF and chipboard - how are they different and which is better? Such questions are regularly faced by both professional designers and ordinary buyers who want to independently update the interior. Indeed, for the uninitiated person, the study of the question of which material for furniture is stronger and more aesthetically pleasing looks difficult. A detailed overview of these chipboards will help you understand everything, evaluate the visual difference and differences in characteristics.

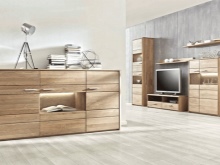

What it is?
The abundance of wood-based materials on free sale allows you to significantly expand the range of typical interior items made from such boards. Furniture made of MDF and chipboard is significantly cheaper than similar products from solid wood; it can have various configuration and design options. But if you need to choose one of the materials, a lot of questions arise that are not related to their cost. To understand everything, you need to know more about each of the options.


MDF
The name MDF is the Russian transliteration of the English term Medium Density Fibreboard, which means a medium density board on a wood fiber basis. This material is produced from finely dispersed raw materials by dry pressing. In the manufacture, a natural adhesive lignin or paraffin is used, which makes it possible to ensure environmental safety of the finished boards.
The finished material receives high strength, density and hardness comparable to natural wood. During production, additional processing can be performed to increase biological resistance, fire resistance, moisture resistance.


The process of making a board is in many ways similar to making paper. Raw materials - wood fibers - are crushed very carefully, which makes it possible to use various types of waste in production. Pre-obtained fractions are cleaned by steam, the mass undergoes additional grinding in special machines, then it is dried, molded, and hot pressed. The resulting material acquires strength comparable to the characteristics of natural wood, density and durability, lends itself to almost any type of processing.
The main field of application of MDF is furniture production; boards are not used for construction needs, since there are alternative, much cheaper options.

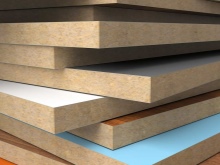

Chipboard
This material, used mainly in furniture production, is more correctly called chipboard - chipboard, but the incorrect designation stuck as a commercial name. In fact, chipboard is a composite sheet consisting of shavings with medium and fine particle size. It is made by hot pressing from sawdust, adding a phenolic-based binder and some other components that increase the strength of the connection.
The finished sheet is subjected to additional processing. This can be surface sanding, lamination or lamination - the last 2 options are considered decorative.

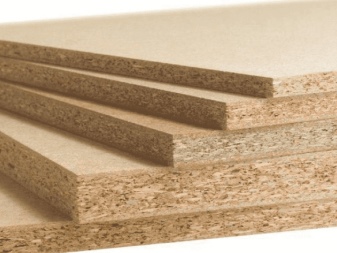
The main area of application of laminated chipboard is furniture production - it is used in the creation of hull structures. The polished material acts as the basis for creating packaging containers for cargo transportation, for partitions and wall cladding in construction.
Particleboard was the first material released from wood products. Its production has been established since the 30s of the XX century, today such sheets are considered one of the most affordable types of building panels, produced in dozens of countries around the world.
We can say that chipboards are a massive option, while MDF can be attributed to the more prestigious types of products.



The main differences
The main parameter by which MDF differs from chipboard is technology used to make slabs. The difference in fractions is visible to the naked eye: in one case it is not always homogeneous sawdust, in the other it is a dense mass, more reminiscent of wood. MDF is a material that can be easily distinguished by its homogeneous structure, surface smoothness, and density.
The main advantage of chipboard is in the price, boards of this type are much cheaper and more affordable, after lamination of the surface they acquire a rather attractive appearance. MDF is more expensive, but more aesthetically pleasing; it can be shaped and milled.


A more detailed comparison allows other differences to be identified. For example, Particleboard material can be assigned to emission classes E2, E3, E4, that is, it contains hazardous resins and formaldehyde compounds that are prohibited for indoor use or in furniture products. If an unscrupulous manufacturer decides to save money, there is a high probability of harm to human health. In this sense, MDF boards are much safer, they always belong to the E1 emission class, which is harmless to humans.
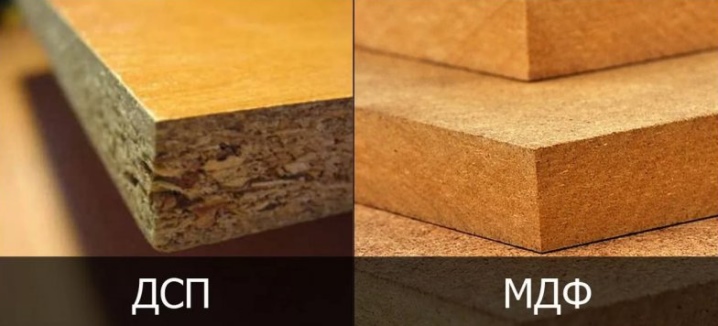
Visual
In finished furniture, MDF and chipboard have pronounced visual differences. So, chipboard is used here in a laminated or laminated form, with a decorative coating, and only to create body structures - frames, lintels, shelves. A fairly massive material is very rarely used in facades because of its weight and not the highest decorative component.
The looseness of wood chip boards is also a serious problem. Usually, such furniture does not tolerate reassembly, repeated screwing of fasteners, and if you try to perform fine processing, you can get chips and defects in the front cover.
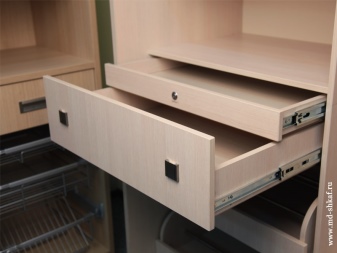
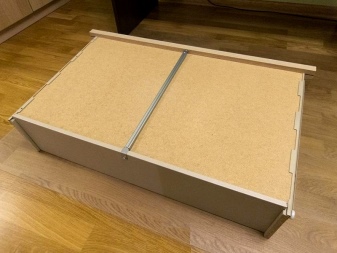
The high density of MDF allows this material to be easily processed: according to these properties, the finished board is close to solid wood. Sheets can be sawn straight and curved, milled, cut. The slabs are used to make elegant furniture facades with patterns, moldings, platbands. Toning is also performed in production, the entire mass on the cut has the same shade. The decor can be anything - from painting to applying texture; preliminary sanding is not necessary for the boards before finishing.
When it comes to choosing an outer coating, MDF also has a definite advantage. The material can be left simply sanded, covered with PVC-based film materials, veneered or painted with enamel in a glossy, matte finish.
In any case, the coating will turn out to be moisture resistant, it will lie well and evenly on the surface of the plate.


In characteristics
Comparison of characteristics also reveals differences between materials. Among the most significant parameters are the following.
- Strength. Here the obvious leader is MDF, it is stronger due to the peculiarities of production - the homogeneity of the fractions makes the material much stronger, the adhesion between the individual elements is higher. Wood-based products are heterogeneous both in composition and in the size of the particles used. Depending on the processing method (pressing density, volumes of added binder), this material can become strong enough, but it is always inferior not only to solid wood, but also to other building boards.
- The weight. According to this indicator, MDF is in the lead - boards are lighter than their counterparts. A sheet material with a size of 2800 × 2700 mm will weigh about 28 kg. Accordingly, the load on the walls is reduced in the manufacture of wall cabinets and shelves, the products are less massive.Chipboard is heavier - about 30 kg per sheet with a size of 2750 × 1830 mm.
- Environmental friendliness. According to this parameter, undoubtedly, MDF is in the lead, which is subject to international standards that significantly limit the use of hazardous formaldehydes. For example, all furniture MDF has the E1 marking, which is much more environmentally friendly, and E2 can no longer be used in children's rooms (in most countries it is no longer produced). Chipboard is manufactured according to different standards. Here, formaldehyde resins are an indispensable component of production, and it is rather difficult to check their volumes.
- Density. All MDF boards have high characteristics in this indicator, close to natural wood - from 720 to 870 km / m3. Accordingly, the material is suitable for load applications. For chipboard, this indicator varies, there are 3 types of boards: with low (up to 550 kg / m3), medium (up to 750 kg / m3) and high density. The last option is considered furniture, the rest - construction, are used as hanging wall cladding, partitions.
- Moisture resistance. Classic sanded chipboard is able to actively absorb water, gaining up to 30% of the original volume. The same applies to laminated chipboard, in which poorly closed edges gain moisture no worse. Due to its high density, MDF is practically devoid of these drawbacks - even when fully immersed in water for several hours, the material does not change its parameters.
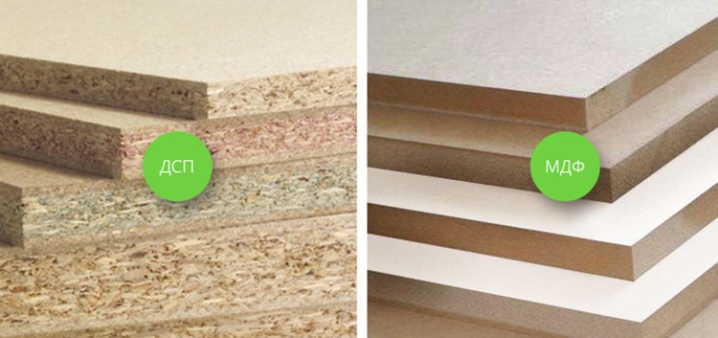
These are the main characteristics by which you can compare 2 types of material in slabs. And here MDF can be called the undisputed leader, since the sheets belong to a higher class of products.
What's better?
When choosing a material for the construction of partitions inside the house, for the formation of decorative screens, when looking for suitable furniture, you always have to make a choice between different types of materials. Of course, if the main criterion is cheapness, chipboards have no competitors here: they are affordable and look quite attractive after applying a decorative layer. But there are some subtleties. For example, this option will not work in rooms with high humidity - you will have to choose furniture and furnishings from other materials for the bathroom.
MDF is significantly more expensive, but it avoids problems not only with the release of hazardous substances or excessive absorption of moisture. This material allows you to significantly diversify the design of finished furniture. For example, fashionable radius or curved facades for a kitchen can be created only from it, chipboard of curved cutting will not transfer, as well as changes in geometric parameters. Humidity restrictions are also minimal. MDF can easily withstand an increase of up to 70%, and with special processing this figure will be even higher.
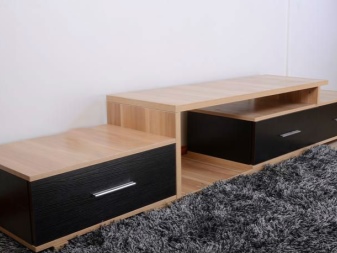

For the kitchen, it is better to choose both types of material in the most expensive version. Such plates have additional moisture resistance, fire retardant components to prevent ignition in case of contact with fire. With a significant thickness, the countertop in the kitchen may well be made of laminated chipboard, but it is necessary that the edges are processed during its manufacture. On the apron, it is better to use MDF boards with fire-resistant impregnation and decorative film coating.
Often these materials are combined to obtain a more aesthetic result, but at an affordable price. The practice is considered widespread when the frames of kitchen cabinets are made of wood-based material, and the facades – from a plate of medium density. However, if the budget allows, it is better to immediately give preference to MDF furniture. In terms of its qualities, it is similar to solid wood, it costs much less than it, and it serves for a long time.
The best slabs are made in the EU countries, they are E1 marked, are absolutely safe, suitable for all areas of the house - from the children's room and bedroom to the bathroom.



The following video will tell you about the differences between MDF and chipboard.
The comment was sent successfully.