Aluminum Composite Panels
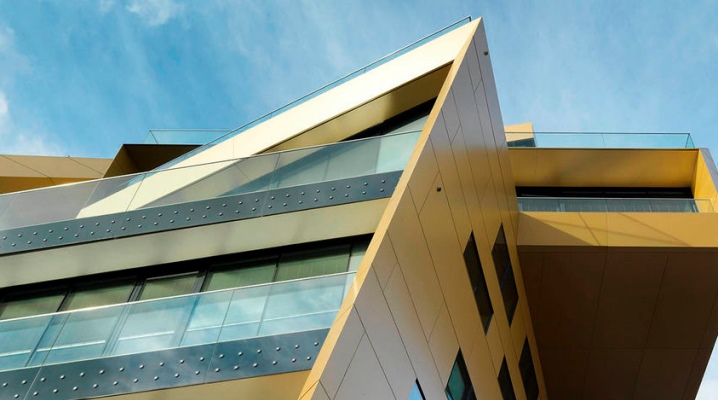
Aluminum composite panels (ACP) are used in various areas of construction. The material is in demand due to its many advantages. From the article you will learn about the types of panels, the features of their production, areas of application and the intricacies of installation.
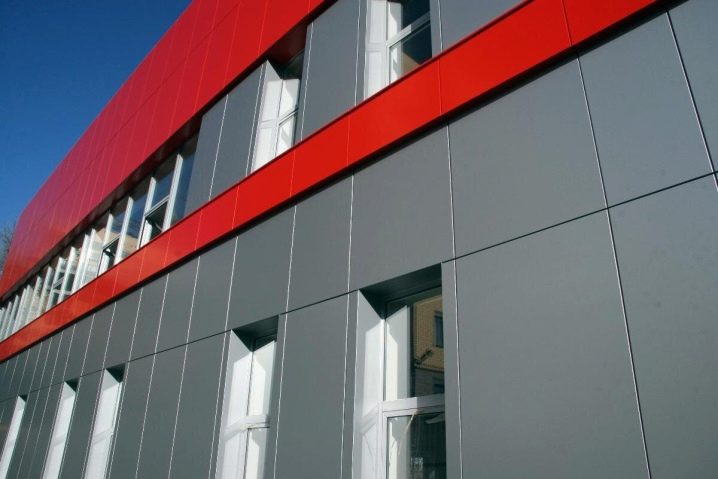
What it is?
Aluminum composite panels are durable, but at the same time quite ductile building material. Its basis is 2 sheets of aluminum, the thickness of which does not exceed 0.5 mm. There is a filler between them to improve the sound insulation properties of the material. Depending on the type, the panels are covered with different protective compounds that protect the products from negative weather conditions and exposure to ultraviolet radiation.
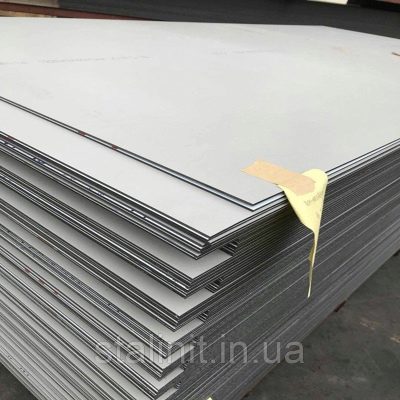
To distinguish their products and be one step ahead of competitors, many ACP manufacturers add additional layers to the material structure in order to improve its technical properties and consumer qualities. For example, on sale there are panels with a carbide layer or the use of anti-toxic components.
It should be borne in mind that improved products are more expensive than conventional ones.
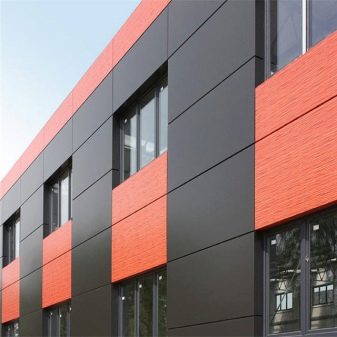
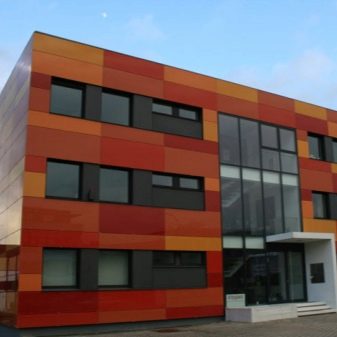
Peculiarities
AKPs are in demand in the construction market due to a number of indisputable advantages. Consider the weighty advantages of the material.
-
Ease. The thickest panels weigh less than 8 kg (1 m2). Due to its lightness, the cladding does not impose a significant additional load on the building structure.
-
Strength and rigidity. These characteristics make it possible to produce large-sized cassettes, which are distinguished by a high installation speed.
-
Durability. Coated panels last over 20 years, retaining their original appearance. Over time, traces of fading and cracks do not appear on their surface.
-
Variety of colors. Bright sheets, materials of muted shades, warm and cold tones - thanks to the multifaceted palette of shades, it is possible to implement a project with any requirements for its appearance.
-
Easy care. The surface of the sheets is not electrified, so that it does not attract dust and small particles of debris. Contamination from the material is removed by rain. When using the panels internally, it is sufficient to wipe the dust 6-7 times a year with a damp cloth.
-
Possibility of processing and bending. Aluminum panels are flexible - they can be bent at an angle of up to 180 degrees, which greatly facilitates the installation process. They go around corners, trim oval objects.
-
High resistance to various negative external factors. The building material is not subject to corrosion even when used in high humidity conditions. It does not interact with chemically aggressive substances, does not deform under accidental impacts and pressure.
-
Resistant to high and low temperatures, as well as to temperature fluctuations, due to which the automatic transmission can be used in any area, regardless of the climate.
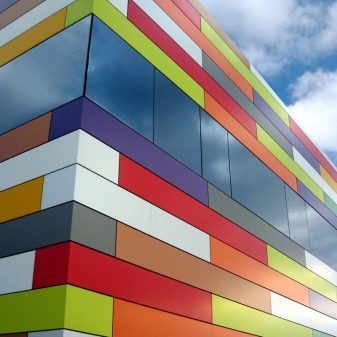
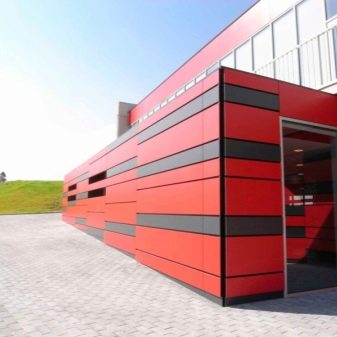
Using aluminum composite panels as exterior cladding will help make any building stylish and presentable. The disadvantages of automatic transmissions include their high cost and poor maintainability. If the material is damaged, you will have to change the cassettes. The disadvantage is also the fire hazard of cheap panels.
To save money, unscrupulous manufacturers in the manufacture of building materials use low-quality raw materials that easily ignite, releasing toxic substances into the atmosphere.
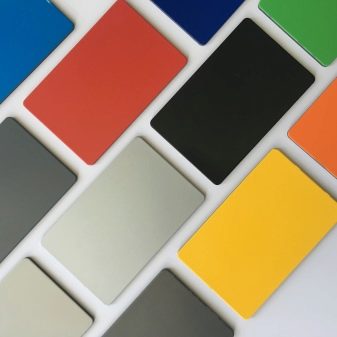
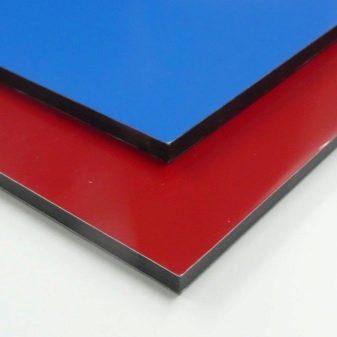
Views
The material is classified according to the type of filler and protective coating.
By type of filler
It can be polymer, mineral or metal with an intermediate layer of aluminum plates. The technical characteristics of the material and the scope of application depend on the filler.
In panels with polymer filler, the intermediate layer is made of polycarbonate, foamed polyethylene and other materials. Such automatic transmissions combine a low specific weight with high strength. They do not exert a significant load on the foundation and supporting structures.
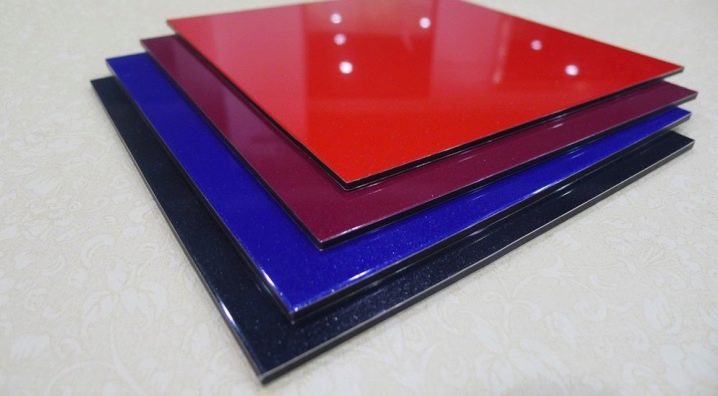
The field of application of composites with polymer filler is the finishing of simple construction objects.
Panels with a mineral layer are classified as low-combustible materials (hazard class G1). When ignited, such automatic gearboxes do not emit harmful substances into the atmosphere. To improve fire resistance, some manufacturers include aluminum hydroxide in their products.
Panels with aluminum plates inside - the most durable. Their rigidity allows them to withstand strong winds. Reinforced building materials are characterized by high fire resistance, which allows them to be used when decorating multi-storey buildings.
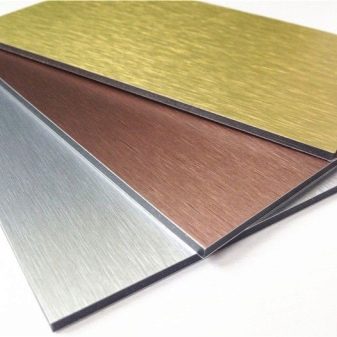
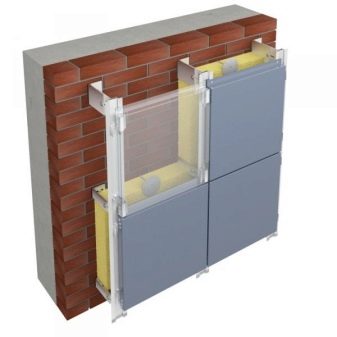
By type of protective coating
The panels are coated with different compounds to protect them from weather and force.
-
PVDF coated. This is a polymer protective layer, 70% of which is polyvinylidene fluoride, 30% is acrylic. The coating is durable, but at the same time plastic, which is especially important for the profiling of products. Panels with PVDF coating are durable, they are well resistant to ultraviolet and aggressive substances. Their surface is dirt-repellent, which makes it easier to maintain the lining.
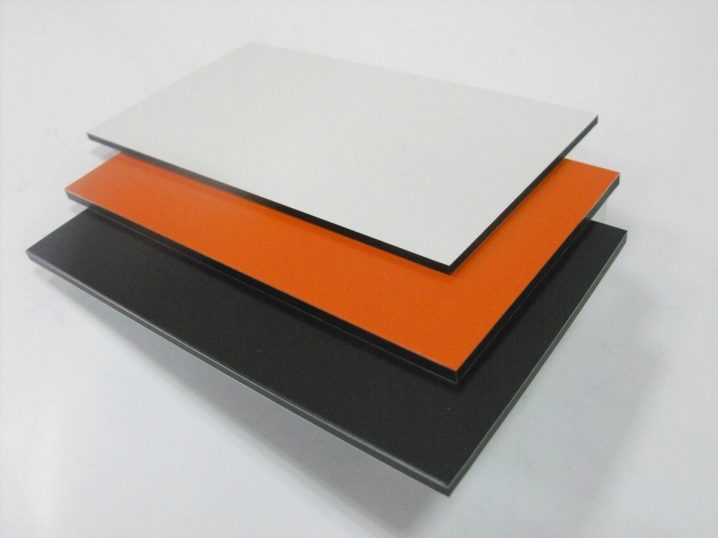
- With polyester lacquer outer layer. The differences between such ACPs are bright colors, resistance to moisture and sunlight. Such panels are inexpensive, but their service life is short, it is only 5-7 years.
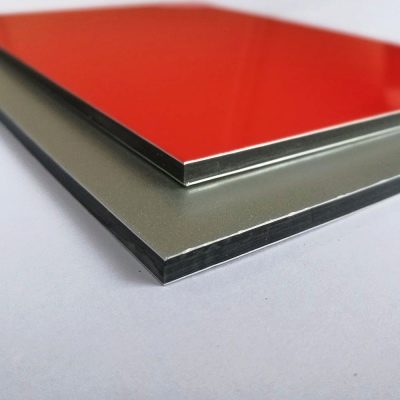
- Oxide coated. Oxidation of the metal allows you to obtain a durable and visually attractive decorative shell. The panels retain their original appearance for 15-20 years when operated in difficult conditions (with high humidity, temperature extremes). They are often used not only for exterior decoration, but also for interior decoration.
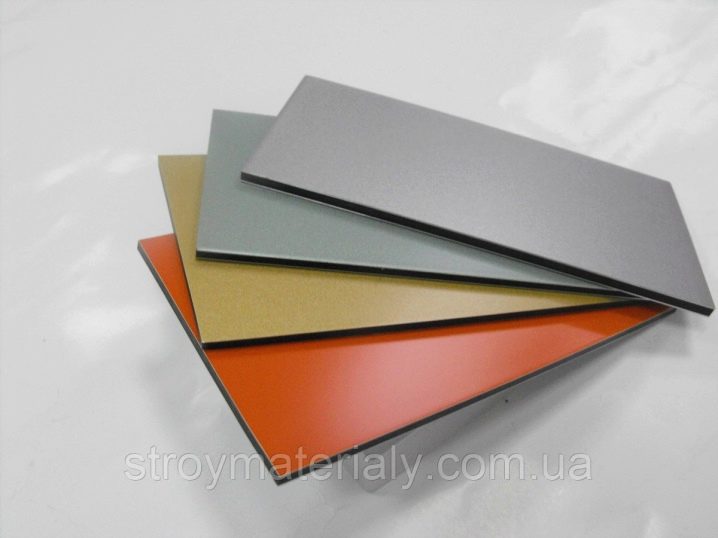
- With laminated film. This is the most expensive, strong and durable cladding. The service life declared by the manufacturers is 25 years, but in fact such automatic transmissions retain their aesthetics and consumer qualities for 40-50 years. The composite is visually attractive. It can imitate natural and artificial materials. Panels for wood and stone are popular. In addition to standard samples, there are metallic, materials with mirrored surfaces.
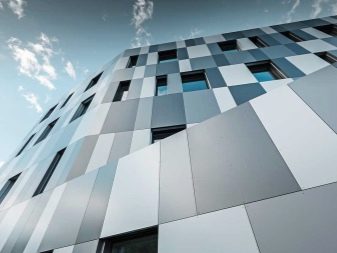
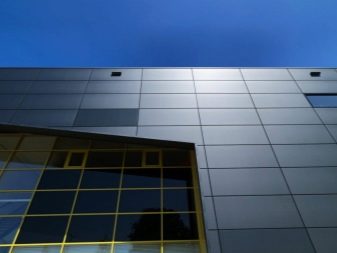
Dimensions and weight
At the request of the customer, manufacturers can produce panels of any size and weight, but there are also standard dimensions. According to GOST, the total thickness of the composite ranges from 2 to 6 mm. In the construction industry, building materials are often used with a thickness of 3 mm and 4 mm. The standard length of the ACP is from 2000 to 8000 mm, the width is from 1000 to 1500 mm. The weight of 1 m2 of material directly depends on its thickness and the type of filler. For example, the mass of 1 m2 of a panel with 2 aluminum sheets 0.5 mm thick and 3 mm polyethylene filler is 5.5 kg. The maximum panel weight is 8 kg.

Top manufacturers
We will present several leading domestic and foreign companies for the production of composite materials, whose products are in demand among consumers from Russia and neighboring countries.
-
Alucobond. It is a German-Swiss brand. Under this trademark, high-quality panels with high strength and flexibility are produced in thicknesses of 3 and 4 mm. The service life of such panels reaches 50 years. The color range of Alucobond composite materials is extensive: the range includes a design solution for every taste.On sale there are panels with bright and muted colors, "chameleon", with imitation of natural materials.
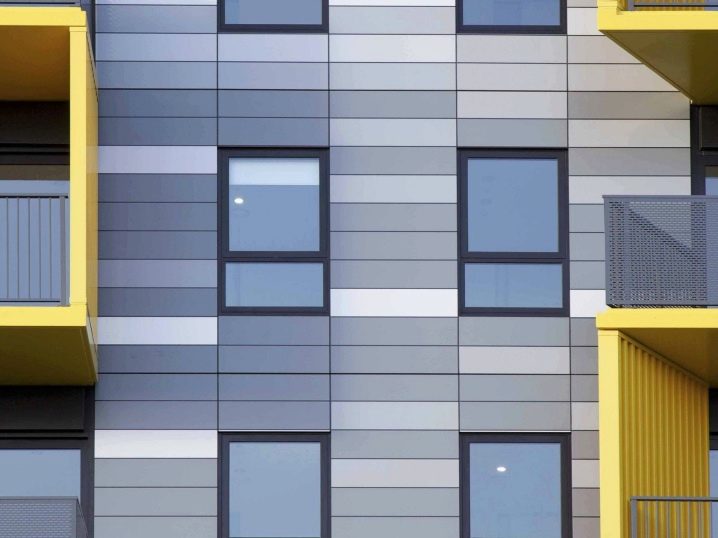
- Aluminstroy. A domestic company that produces aluminum composite panels under the GoldStar trademark with a polymer and mineral filler and a PVDF protective coating. The line includes spectacular series - wood-like panels with mirrored surfaces, polished metal, gold, silver and natural stone. The manufacturer sells a composite with a thickness of 3 and 4 mm.
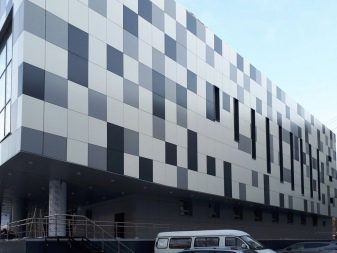
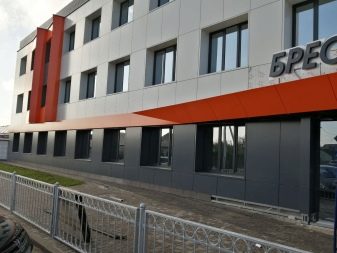
- Alluxe. The production facilities of this company are located in China. The manufacturer manufactures composite materials using Western technologies. The products are certified. ACPs are made using polymer and mineral fillers, and PVDF coating acts as a protective layer. The assortment includes panels with a thickness of 3 and 4 mm, a width of 1.25 m and a maximum length of 5.7 m. The color range includes more than 20 options with a matte and glossy surface.
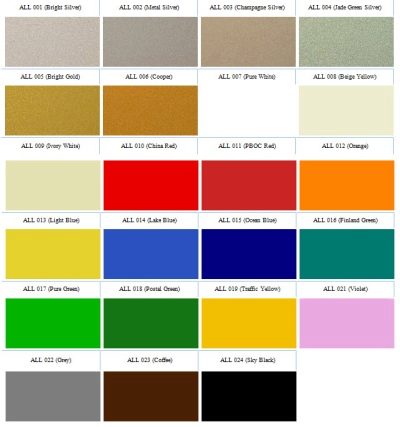
Products of the companies Goldstar, Sibalux, Alcotek, Dibond are in demand. To eliminate the risks of buying a fake, you need to buy building materials from official representatives.
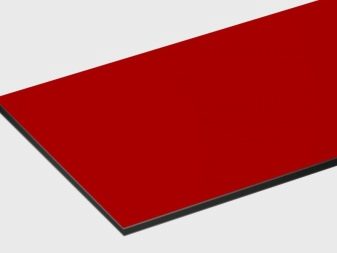

Application area
Most often, aluminum composite panels are used for external decorative cladding and arrangement of ventilated building facades. With their help, they decorate the entrance groups of large retail outlets, offices and administrative facilities.
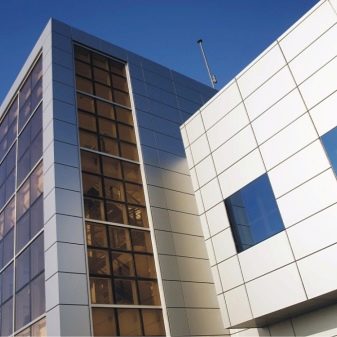
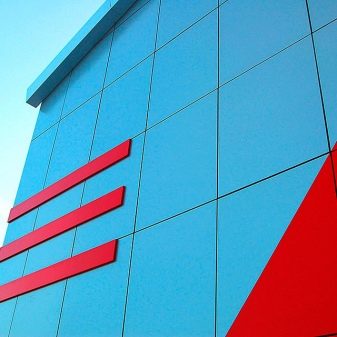
Other areas of application:
-
production of elements of outdoor and indoor advertising - signboards, signs, stands, racks;
-
interior design, room decor;
-
manufacture of industrial refrigeration units;
-
construction of partitions;
-
installation of suspension systems.
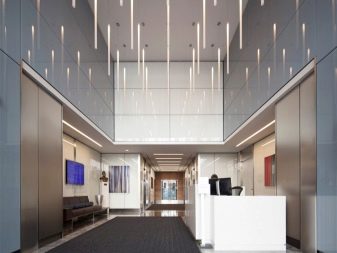
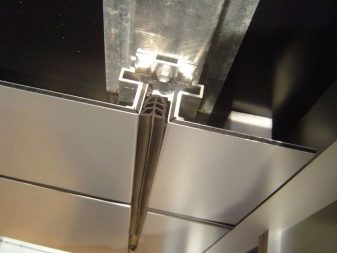
Aluminum composite panels are ideal for the restoration of old objects, the walls of which are difficult or impossible to restore.
Thanks to the use of ACP, it will be possible not only to make the facade of the building attractive, but also to significantly improve the sound insulation in the room.
Processing methods
To obtain products of the desired configuration, the composite material can be processed in several ways.
-
Cut. Allows to obtain cassettes with optimal dimensions. Most often, products are sawn using a circular saw, less often - using a guillotine. Cutting is the most common type of processing. Please note: when cutting sheets, it is not recommended to use a grinder. In this case, the temperature in the cutting area rises significantly - this can lead to damage to the protective decorative layer.
-
Flexible. To bend the material, use a 1-roll press or three-roll bending machines. To prevent the risk of composite crushing, it is recommended to insert a soft material between the ACP and the roller.
-
Rolling. Thanks to processing, it is possible to obtain products for finishing objects with complex architectural forms. In this case, the composite is processed on special rolling machines.
-
Milling. This type of processing is designed to change the shape of the panels.
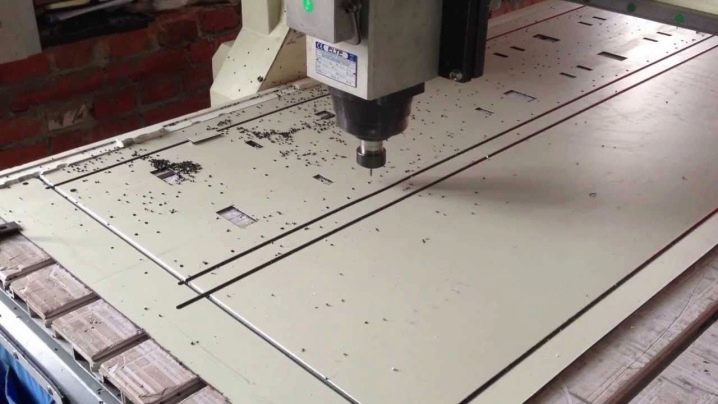
The automatic transmission is allowed to be drilled for making holes.
Installation technology
Installing panels is a simple process that you can do yourself. When working, it is important to follow a certain sequence.
-
Marking for accurate mounting of brackets. To perform marking work, you cannot do without a laser pointer, a building level and a tape measure.
-
Installation of supporting brackets. For these purposes, anchor metal fasteners or dowels with plastic sleeves are suitable.
-
Lining of thermal insulation material and protective film. It is best to fasten them with umbrella dowels.
-
Installation of the frame guides.
-
Fastening the automatic transmission to the crate guides. For these purposes, you can use self-tapping screws, rivets or clamping strips.
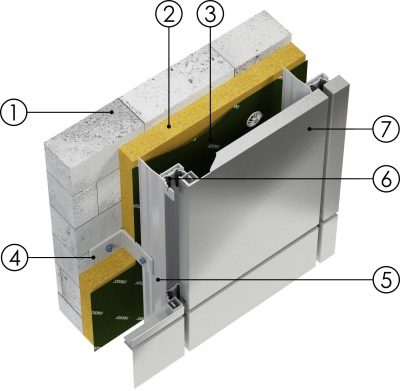
Aluminum composite panels have a feature that must be taken into account when installing them - this is a slight expansion when heated.In order for the lined surface to be flat, small gaps must be provided when installing the cassettes.
After installing the panels, carefully remove the protective film (at an angle of 180 degrees). Incorrect movements can lead to bending of the composite material.
With the right choice and installation, composite panels will last for decades.
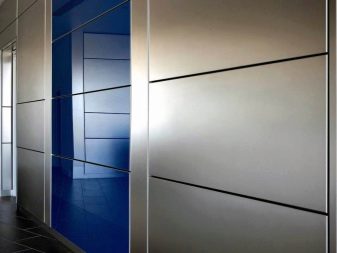
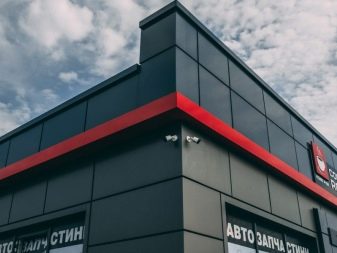
The comment was sent successfully.