What is Alucobond and how to install it?
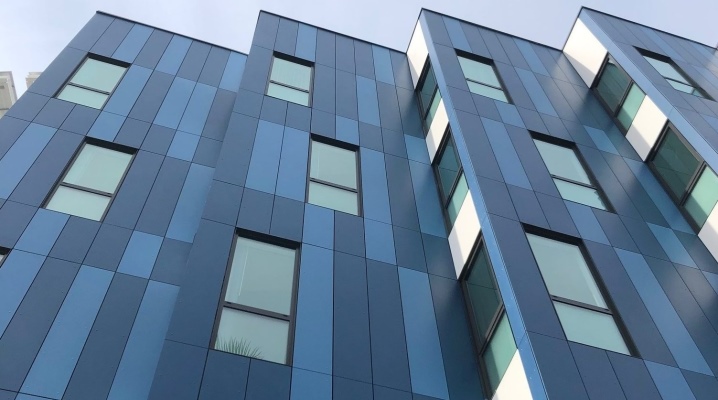
The material for facade decoration called alucobond is gaining great popularity every year on all continents. There are several reasons for this. First of all, it is an acceptable cost. Next comes the external beauty of the slabs. And, undoubtedly, high quality is a positive characteristic. Craftsmen also appreciate this material for its ease of installation. However, before proceeding with the independent installation of the alucobond on the facade of your own house, it is recommended to learn about the properties of this material, the advantages, disadvantages, and also get acquainted with some of the nuances of installation.
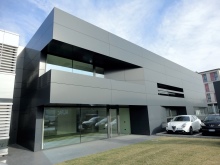
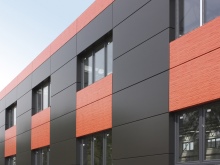
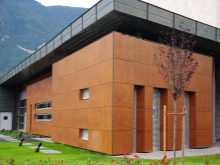
What it is?
Alucobond is a composite material whose full name sounds like aluminum composite panels. In this case, the composite is a harmonious duet of aluminum and polymer. The polymer used in the manufacture of composite blocks differs in type and thickness. The performance characteristics of the finished material depend on this.
On the territory of the Russian Federation alone, there are about 15 companies engaged in the manufacture of this facing material.
The thickness of the aluminum sheets used in each plate is 0.5mm. The inner filler of the blocks is wrapped with metal plates on both sides. Thus, a kind of sandwich is formed.
The inner component of such a sandwich is most often presented in the form of high-pressure polyethylene.
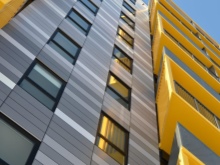

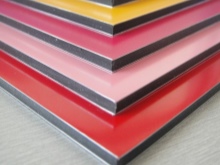
It is important to know that aluminum sandwich sheets have an anti-corrosion coating to ensure that the slabs will not deteriorate prematurely. Besides, anti-corrosion coating helps prevent damage from rubbing against the lattice base. An oxide composition in the form of a sodium hydroxide solution is used as an anti-corrosion layer, due to which a film appears on the surface of the metal plate, which protects the material from moisture that can cause irreparable harm to the metal.
The front side is aluminum coated with polyester. However, manufacturers most often use fluorinated carbon instead, which is not exposed to ultraviolet radiation and chemicals. What is noteworthy is that fluorinated carbon, even after long-term operation of the slabs, does not crack, and even more so does not move away from the base.
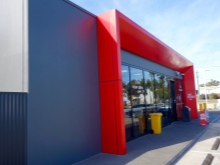
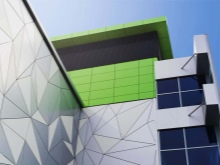
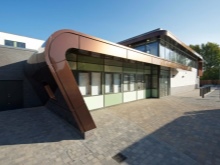
The final layer of the composite sandwich is a laminated film. It should be removed prior to installation as it is part of the original packaging. Thanks to this film, the decorative surface of the slabs is protected during transportation and handling. Some craftsmen install aluminum composite panels without removing the film, and then remove the protective layer from the surface.
The front side of alucobond plates is distinguished by a large number of layers. When viewed from the central filler, the next layer is adhesion, then an aluminum sheet, then a primer, resin, enamel and a protective film.
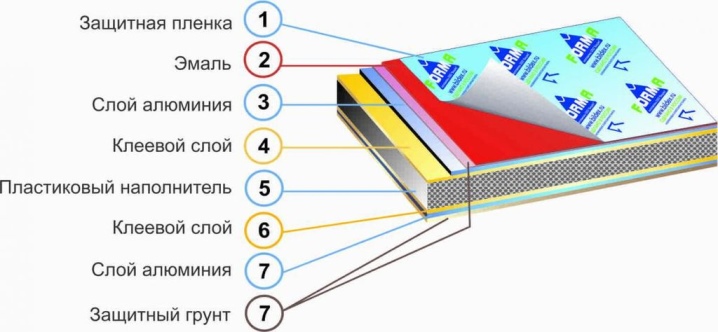
Main characteristics
Alucobond is a facing building material in the form of aluminum composite blocks. Due to their content, the boards have good performance characteristics.
Further, it is proposed to get acquainted with the advantages and disadvantages of alucobond, which every person who wants to use this material as a cladding of the facade of a building needs to know about. First of all, you need to know the benefits of composite boards.
- Durability. Each manufacturer provides a quality certificate and a warranty card, confirming that the panels will serve up to 25 years. However, the owners, who have used this material a long time ago, claim that high-quality slabs from well-known companies can last half a century.
- Ease of processing. Despite the multi-layering, composite panels are quite easy to cut into several pieces. They are fed by rolling and welding.
- Strength and elasticity. Steel sheets in a composite sandwich give the boards high resistance to any mechanical stress. But what is interesting, despite the presence of such a strong material, the alucobond can be bent.
- Resistant to weathering. The alucobond coating is able to withstand harsh weather, sudden temperature changes.
- Aesthetics. Thanks to a wide variety of colors and shades of the front side of alucobond plates, everyone will be able to embody the most daring ideas into reality. The exterior can mimic decorative plastering and other unique design options. And what is most pleasant, even with prolonged exposure to ultraviolet radiation, the color saturation of the front side of the plates does not disappear.
- Smooth, flat surface. Even when the slabs are bent, cracks and seams do not appear on the face of the material. What is most pleasant, the unusual texture of the blocks when bending, and even during installation, allows you to make the structure seamless.
- Heat and sound insulation. Thanks to their layering, the slabs suppress noise and retain heat inside the premises. The sound insulation properties of buildings located in the city center are especially important.
- Easy to install. Due to the lightness of the composite slabs, a large load is not applied to the foundation of the building. And given the strength of the slabs, there is no need to use additional reinforcing parts. It is enough to apply a simplified frame structure for a ventilation facade.
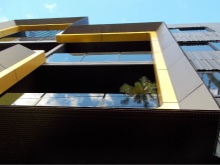
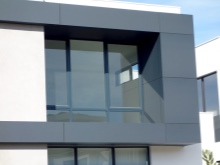
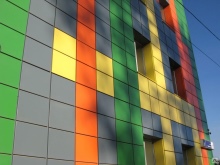
Alucobond also has some disadvantages.
- Low fire resistance. Of course, this indicator is determined by the type of filler. Plates, inside of which there is a polymer, not only burn out, but also release toxic substances into the air. That is why most people opt for boards with expanded polyethylene, as it belongs to the flame retardant class. Today the construction market is filled with alucobond panels with improved internal composition. They contain aluminum hydroxide, which is able to withstand open fire for several hours. However, the price of such material is much higher. Accordingly, they are not purchased so often.
- Restoration of slabs. If the block is suddenly damaged, it may be necessary to dismantle several adjacent slab blocks to replace it.
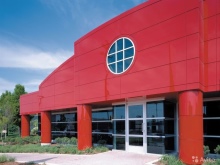
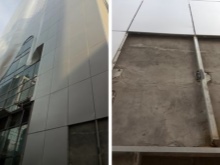
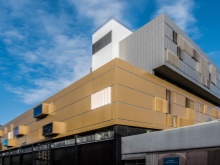
Applications
Alucobond is such a versatile building material that it is used in a wide variety of production areas.
- Composite panels today occupy the 1st place among the materials intended for the decoration of the facade of buildings.
- Alucobond is used as a ventilation facade of outdated buildings to renovate the exterior and increase the sound and heat insulation properties.
- Block sandwiches are used as cladding for architectural details.
- Plates of this type are used in the design of advertising signs, standing boards, light boxes.
- New blocks can be used to make partitions inside the premises or to decorate the interior space, including the ceiling.
- Surely few people know, but composite panels are used for the manufacture of some finishing elements for cars, buses and even cars.
- Alucobond is used as protective packaging for fragile equipment.
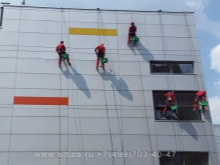
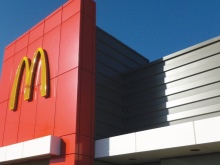
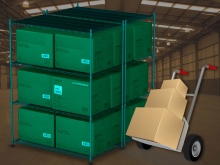
Aluminum composite panels easily do their job. However, they are most often used as a finishing material for the front side of buildings and interiors.
It is these blocks that make it possible to create unique architectural masterpieces when arranging the exterior of a building.
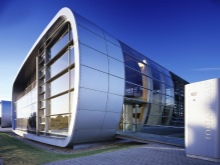

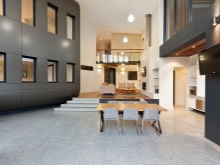
Description of species
Today, there are several varieties of aluminum composite panels, each of which has numerous advantages, but may have some disadvantages.
- Ventilated facade with alucobond. Installation is very easy. For installation, fasteners are used, on which the insulation is initially installed. Next, the guides and profile are attached, and after that the panels are fixed. Thanks to this design, the buildings receive maximum protection from mechanical damage, and most importantly, heat is retained inside the building.
- Alucobond under a tree. With the help of such slabs, the building acquires an unusual appearance. Each individual block is covered with high-quality paint that does not crack over time, does not lose saturation and color depth, as well as the visible texture of natural wood.
- Alukobond A2. A distinctive feature of this type of panel is incombustibility. Even with strong heat from direct flames, the stove will not ignite. Accordingly, such plates are intended for use in buildings where the issue of fire safety is in the first place.
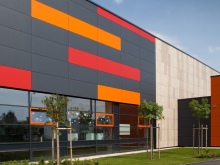
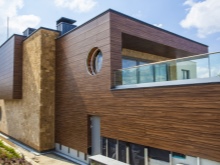
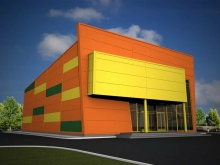
It should be noted that aluminum composite plates are manufactured under several markings.
The first is B2. Such plates cannot withstand an open flame, which is why they belong to the 4th flammability group. They not only flare up from contact with fire, but also quickly flare up. Another distinguishing feature of B2 aluminum composite panels is the minimum bending strength.
The next brand is A2. These models have a minimum flammability index, which is indicated by the symbols "G1". There are varieties of plates with the designation "NG". This suggests that they are non-flammable. As for the dimensions of the plates marked A2, they are completely identical to the B2 alucobond. The only difference is in mass. Plates A2 are 1.5 kg heavier than plates B2.
Another type of composite cassettes is plus. These boards differ in maximum thickness. The weight of each individual unit is 7.3 kg. Flammability and flammability indicators are minimal.
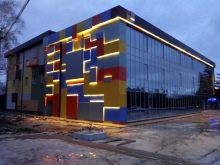
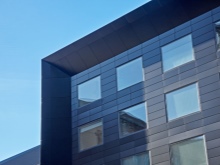
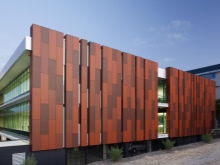
Dimensions and weight of sheets
Aluminum composite panels with plus marking have the maximum possible width of 1.5 m. And the width of composite panels with B2 marking is 1 m. Alucobond A2 marking has an average width of 1.25 m. The same slabs can be ordered with a width of one and a half meters, since it is almost impossible to find A2 slabs larger than the specified width on sale.
There is no specific standard for the length of alucobond blocks. This dimensional indicator fluctuates between 2-4.5 m. However, when examining the facades of buildings finished with alucobond, there are also atypical dimensions of the slabs. This is due to some of the nuances of block production. They go along the conveyor in a continuous belt and are cut according to the length required by the customer.

But even in the case of individual orders, it must be remembered that the permissible norms cannot be exceeded.
For example, the maximum length of a slab can be 6 m. The length of each individual block should not exceed 160 cm.
The thickness of the alucobond is equally important. However, this figure depends on the filling of the sandwich. According to the manufacturers, consumer demand is more focused on slabs with a thickness of 4 mm.
It is worth familiarizing yourself with the mass of the alumabond. For 1 sq. m of this material accounts for 3 to 8 kg. It all depends on the materials used to compose the composite panels.
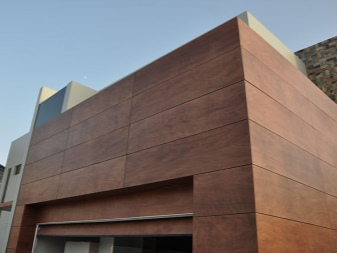
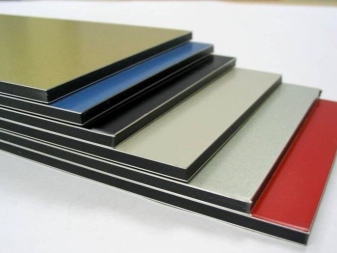
How to work with panels?
People who have never come across such material find it very difficult to work with it. But it is not so. In fact, aluminum composite panels can be installed without even a minimal understanding of how to do it. The main thing is to understand the installation technology and find out some of the nuances of the installation. At home, slabs can not only be cut, they can be bent on their own to install on a curved surface.
With regard to bending aluminum panels, 3 methods have been developed for this purpose.
- Press brakes, where specialized automation is used, designed to bend sheets, plates, panels and other types of material.
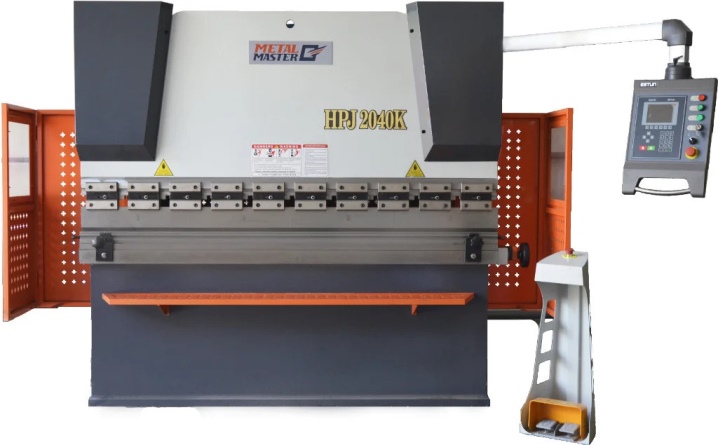
- Round bending rolling machines. In this case, the deformation process is somewhat similar to a press brake. However, special attention must be paid to protecting the front of the panels.
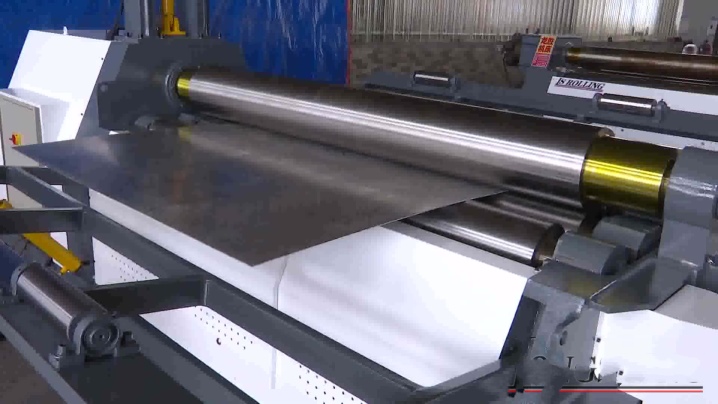
- Manual bending by milling. Milling is carried out in the part of the panel where bending is required. Using cutters, you can make rectangular or v-shaped cuts. These cuts should not extend to the interior of the panel where the filler passes. After preparing this groove, bending is carried out by hand to the required radius.
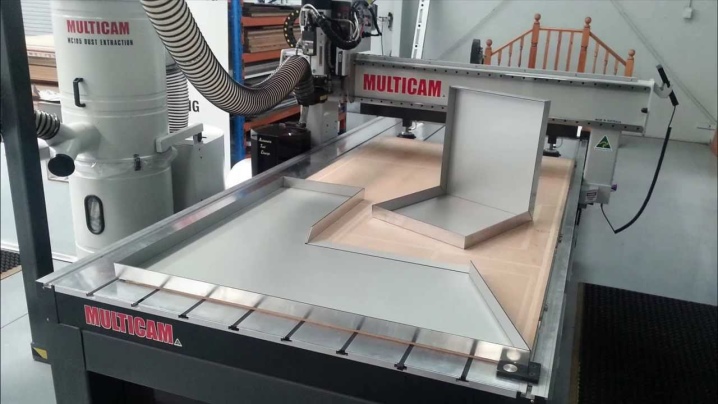
The third method is ideal for homework. And what is most remarkable, in the presence of such grooves, the slabs do not lose their qualities.
When it comes to cutting the aluminum composite board, it is necessary to use a cutter with a guide fence. But if there is no such tool, you can use a grinder. Only when working with it, it is important to exercise special care and caution, even a small spark can lead to unpleasant consequences.
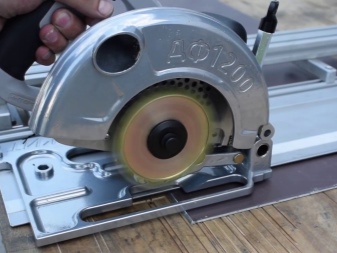
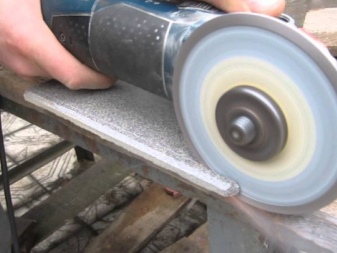
Installation technology
People who are not related to the construction industry invite specialists to mount the alucobond on the facade of the building. It seems to amateurs that only a professional with considerable experience in assembling composite plates can cope with this work. Of course, for the arrangement of multi-storey buildings, you should conclude an agreement with a construction company, but when decorating the facade of your own house, you can do it yourself. After all, not everything is as complicated as it might seem at first glance.
The Alucobond is fastened to the metal frame using special assemblies. The fixing nodes on which the building sheathing slabs should be fastened are divided into several types:
- suspended on bolts;
- fastened by grooves and ridges;
- riveted;
- screw-in;
- adhesive.
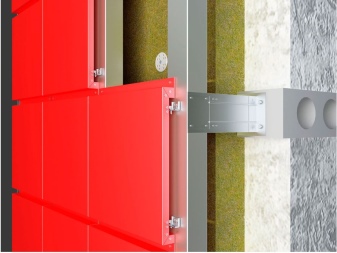
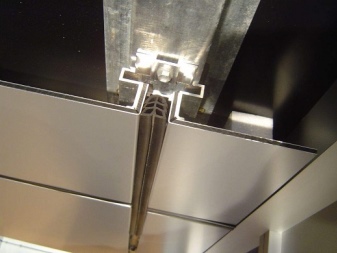
Each individual option guarantees high strength and reliability of fixing the plates, the main thing is to observe the technology of installing the profile.
In general, the installation process consists of 3 stages, the first is to install the subsystem, the second is insulation, and the final stage is to fix the plates themselves.
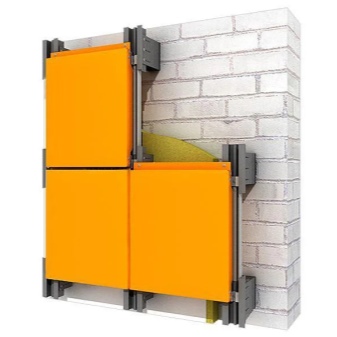
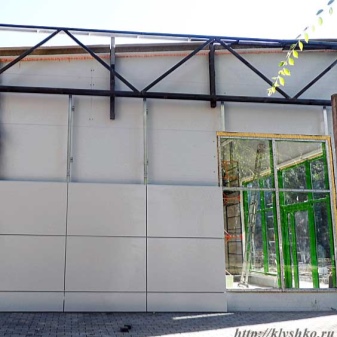
Subsystem installation
According to the alukobond installation technology, first of all, it is necessary to make a facade marking. For this it is necessary to use high-precision tools designed to work on large canvases, for example, a laser or theodolite. If the building is not tall, it is sufficient to use a construction tape or a measuring rod.
The next stage of installation is to install the brackets. Using a punch, it is necessary to create holes, the diameter of which must match the anchor bolts. And here is an important nuance: the depth of the hole should be 10 mm more than the length of the bolts.
Next, the brackets are installed. It is on them that the entire load of the facade will be carried out. Accordingly, in order for the cladding to sit firmly, it is necessary to correctly install the brackets. To begin with, a disk washer is placed on a self-tapping screw. Then a thermal insulating gasket and a plastic dowel are inserted into the hole. After the screw is twisted.The latter in the installation of the subsystem involves the installation of guides.
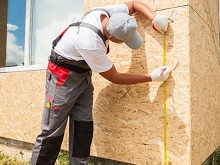
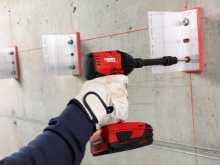
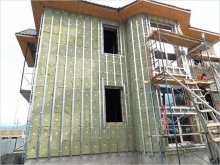
Warming
An important stage in the installation of the plates is the laying of the insulation. The most commonly used mineral wool. You can also use polystyrene or expanded polystyrene.
Insulation sheets are strung on brackets. And for greater fixation, in some places they are fixed with dowels.
In this case, you need to know an important nuance: if mineral wool is used, its ends must be carefully tucked under the brackets.
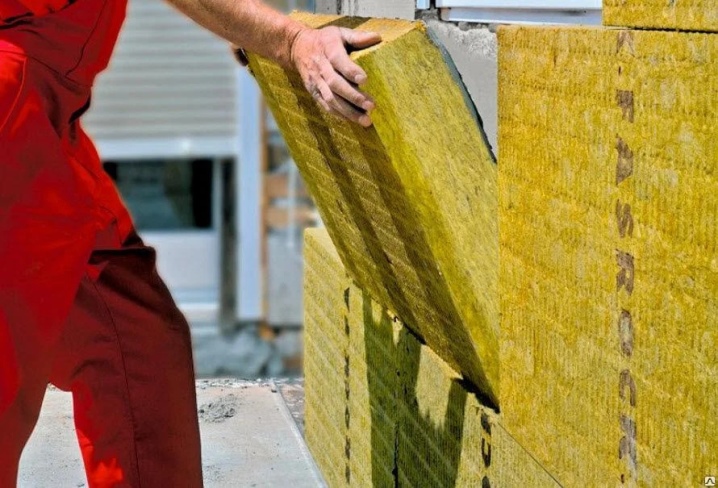
The final stage
And now it remains only to install the alucobond itself. Installation of aluminum composite plates is carried out depending on the type of fastener. The most common, however, is with and without a lock. The blocks should be installed from bottom to top, from left to right. With the help of self-tapping screws, the starting bar is fixed. For a tighter connection, it is recommended to place double-sided tape under the cassettes. During installation, it is important to ensure that the next cassette coincides with the previous one in the locks.
After installing each new plate, the screws are tightened. If necessary, a small gap can be left between the blocks. Cassettes that do not have a lock are installed using a similar technology using rivets.
As it became clear the installation of the alucobond is not particularly difficult. Of course, for a beginner, installing the first few slabs will seem incredibly difficult. However, if you adhere to all the intricacies of the installation, even an inexperienced person will be able to equip the facade of his own house without involving specialists in the construction industry.
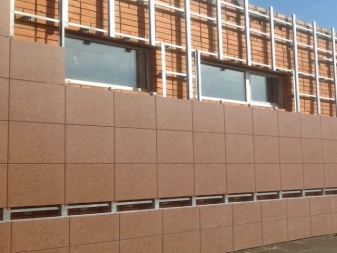
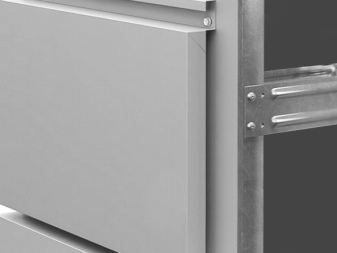
The comment was sent successfully.