Installation of OSB
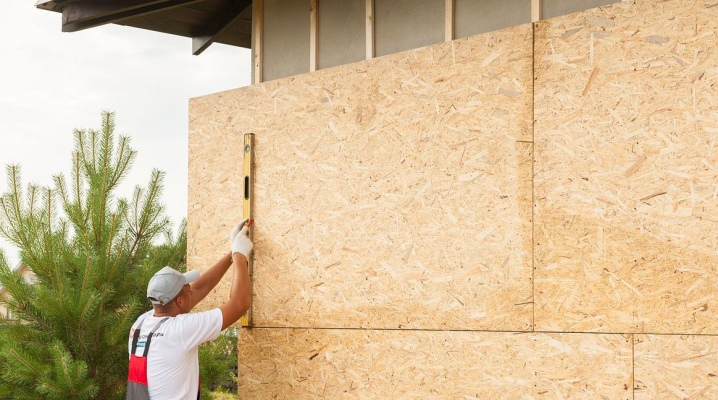
Various sheet materials are widely used in modern construction. The list of the most popular includes oriented strand board (OSB). These panels are most often called using English terminology - OSB, that is, Oriented Strand Board. Taking into account the record demand for the material, the answers to questions related to the installation of OSB plates when performing various types of construction and finishing works are relevant.

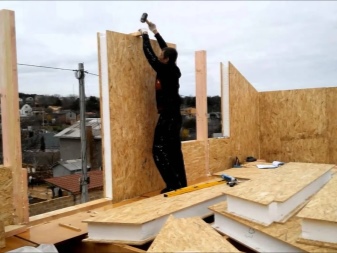
How can you fix it?
The type of installation, therefore, the type of fastening depends on a number of factors. So, when working with a brick or concrete surface, dowels or special glue are used. At the same time, the panels can be screwed to the wood with self-tapping screws 45-50 mm long. Flatness of the surface will always be one of the defining points. If it meets the requirements, then the sheets can be simply glued to the same concrete.
And also in the process of installation and selection of fasteners, the climatic features of the region should be taken into account. For example, when erecting a roof, OSB can be nailed with ring nails, which are characterized by increased shear strength.
This indicator is relevant for wind and snow loads.



However, it is self-tapping screws that are most often used, on the basis of which it is worth highlighting the basic rules for their choice. High-quality fasteners for OSB sheets must have:
-
increased strength;
-
head "in a secret";
-
drill-shaped tip for easy penetration into both wood and metal profiles;
-
high-quality and durable anti-corrosion coating.
It is important to remember that self-tapping screws need to be screwed in, preventing violation of the texture of the panels. Another important point is the consumption of fasteners. One "square" usually takes about 30 screws or nails.

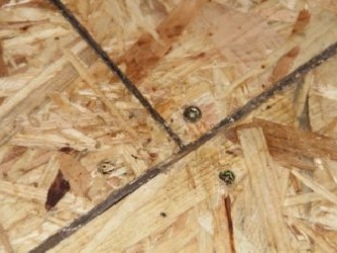
Installation of lathing under OSB
Regardless of whether it will be wall cladding from the inside, attic outside, verandas in the country, creating a floor covering or a base for a soft roof (bituminous tiles), at the preliminary stage, you should take care of the base for the panels. In this case, we can talk about two options:
-
lathing made of bars with a small section and slats;
-
frame, which can be either wooden or made of metal profiles.
The main selection criterion in this case will be the state of the base surface. The greater the differences present, the more difficult the structure will have to be erected.
At the same time, at the preparatory stage, the base, which will subsequently be hidden by sheet material, must be covered with a primer. This minimizes the risk of mold formation.


The next step is marking, taking into account the fact that all the bearing elements of the future crate or frame should be located in the same plane. Today, the best tool is the laser level. In its absence, plumb lines, building levels and cords are used. In order to make the markings on the wall correctly and as accurately as possible, you must:
-
determine and mark the points of attachment of the rails along the top;
-
using a plumb line, duplicate the marks at the bottom;
-
a cord or thread is pulled diagonally between the marks;
-
slats, profiles are aligned in one plane using special mounting plates or any other pads;
-
if necessary, it is possible to maximize the base for laying OSB panels by installing additional transverse jumpers between the main elements of the lathing.
After completing the work related to fixing the lathing, attention should be paid to communications. It is important to remember that all kinds of mortgages, as well as wiring, pipelines, if any, are located and fixed at this stage, if this has not been done earlier.

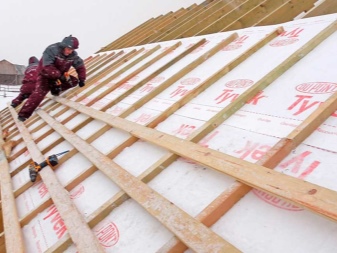
When arranging flooring from OSB panels and the base for them, it is necessary to take into account a number of important nuances. Let's consider the algorithm of actions in such situations.
-
Removal of existing coating, if present, as well as debris and dust.
-
Beam layout. In this case, all elements of the future structure should be located parallel to each other with an interval of 0.8 m. And it is also necessary to retreat from the walls by 10 mm.
-
Making a mark on the wall 10-20 mm above the timber.
-
Drilling a hole through the timber and wedges for the dowel.
-
Fixing the elements of the lathing.
-
Fastening the edged board.
The last point should be given special attention. So, if the room in which the work on the arrangement of the OSB floors is carried out has ceilings up to 2.4 m, then it is better not to mount the board. This will avoid reducing the height of the walls in the end.


Now the described sheet material is widely and successfully used in roofing work. It is necessary to mount the crate, in the future it is necessary to lay the panels themselves, subject to a number of rules.
-
Continuous sheeting is performed on roofs with slopes ranging from 5 to 10 degrees.
-
If the angle of the slope is from 10 to 15 degrees, then the installation of a lathing from a bar with dimensions of 45x50 mm is required. Structural elements in such a situation are placed parallel to the line of the cornice with a step of 45 cm.
-
A beam of a similar section is used for lathing on roofs with slopes at an angle of more than 15 degrees. The difference is that there should be 60 cm between the bars.
When assembling the base under the roof, it is important to take into account that additional bars must be installed in the places where the valley is attached to the ridge girder.
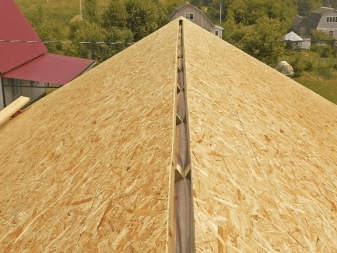

Styling features
In order to properly sheathe various surfaces with oriented strand board, a number of guidelines must be followed. The list of general rules for laying panels includes several important points.
-
At the initial stage, a thorough processing and leveling of the base surface is carried out, as well as its marking.
-
Where exactly the slabs will be installed (floor, walls, ceilings, roof), their thickness depends.
-
Particular attention is paid to the choice of material for the lathing and (or) frame.
-
Taking into account the thickness of the sheets and the state of the surface, fasteners are chosen for the timber and the metal profile.
-
The interval between self-tapping screws (nails) in the middle of the panel should not exceed 30 cm.
-
Light sheets should be fixed starting from the middle. This avoids sagging.
-
Self-tapping screws should be 2.5 times longer than the thickness of the boards to be laid.


Separately, it is worth considering the design features of the OSB ceiling space. After surface treatment, the algorithm will include several stages.
-
Calculation of the height of the room and the level of the ceiling, if the presence of an insulation or soundproofing layer is provided. The recommended clearance in this case is 10 mm.
-
Marking.
-
Installation of fasteners, which will further support the entire ceiling structure. The optimal solution would be to use suspensions - special devices that are fixed on the base surface using dowels or self-tapping screws. They are made of durable materials and are as reliable as possible.
-
The choice of material for the frame.
-
Installation of the lathing. The easiest way to do this is using a laser level. And also at this stage it is necessary to pay attention to the wiring and installation locations of the lighting fixtures.


When all the above operations are completed, proceed directly to the installation of the panels themselves. They are fixed starting from one of the corners of the room.It is best to do this with an assistant.
However, there are now special devices, including lifts, that greatly simplify the installation, allowing you to do it alone with minimal effort and time.

On the floor
The easiest way is to lay the panels on a concrete base. In such situations, at the preparatory stage, you will need:
-
thoroughly clean the surface - the best way out is to use a vacuum cleaner;
-
make a leveling screed if necessary;
-
cover the resulting surface with a primer.
After that, the sheets are laid out on the floor of the room and the extreme elements of the future coating are cut. The panels are then glued to the concrete. At the final stage, the cracks are foamed around the entire perimeter.


If it is necessary to sew up a plank floor with OSB-plates, then it will need to be leveled as much as possible beforehand. The fasteners in such cases will, of course, be self-tapping screws. By the way, sometimes the attachment points are putty, and the coating itself is simply carefully cleaned and varnished.
The described sheet material can also be laid on logs. In this case, it is important to compare the thickness of the panels and the distance between the bars. To create a durable floor covering, you can use a 9 mm thick slab. Therefore, the lag step will be 250 mm.
If you stack 16 mm sheets, then the interval can vary from 35 to 60 cm.


On the walls
Taking into account the laws of physics, many sheet materials, including oriented strand board, can withstand higher loads in an upright position than when placed horizontally. This is primarily due to the direction of the fibers and gravity. It is for this reason that it is better to fix the panels with nails on a wooden crate. At the same time, options with both circular and spiral threads will be equally effective. However, when installing partitions, which in the future may experience increased loads, self-tapping screws should be used.
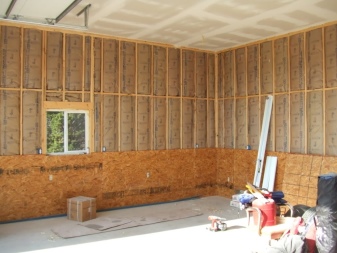

On the roof
Any roofing is a multi-layer structure, assuming the presence of a lathing or frame as the basis for the outer covering. When using modern soft materials, OSB panels act as a base. A solid surface is often mounted with gaps between the elements. The technology also provides for a sparse lathing, calculated individually in each case, taking into account the characteristics of the roof.
Roof slabs are fixed along the load-bearing bars starting from the bottom row. It is important that each sheet is placed on at least two bars. In this case, the joints are located on props. Leave gaps of at least 2 mm between the sheets.
They are fastened to the lathing with ring or spiral nails, the length of which should be from 45 to 75 mm, with a step along the beams and transverse beams of 300 and 150 mm, respectively, with an indent from the edge of 10 mm.


How and how to seal the seams?
It's no secret that all wood materials react to temperature changes. And oriented strand board is no exception in this case. When heated, these panels expand noticeably, which can lead to their deformation. Based on this, between them when laying, it is necessary to leave compensating gaps of about 3 mm. In parallel, a 15 mm indent is made around the perimeter. These intervals should perform their functions throughout the entire life of the coating, but at the same time not affect its appearance.
Taking into account all of the above, it became necessary to find material for grouting. It is important to take into account that the materials must be elastic and at the same time perform a moisture-protective function. When choosing exactly what to cover up the gaps between OSB sheets, a number of factors should be taken into account. First of all, the external conditions (external or external work), as well as the type of surface finish, are taken into account.

At the moment, most often used to fill the joints:
-
acrylic-based putty;
-
parquet varnish;
-
silicone or acrylic sealant.
Sawdust is added to the composition of the varnish solution, which allows you to completely close the seams and make them almost invisible. After the mixture has dried and high-quality sanding, the joints are difficult to determine visually.
Correct application of this and other methods significantly reduces the time spent on further finishing.


In this case, it is necessary to pay attention to some important points.
-
If decoration is intended, then the panels are cleaned of the paraffin layer. They are then coated with an antifungal primer.
-
After the primer is completely dry, the edges of the sheets at the joints are covered with masking tape.
-
The varnish solution and putty are rubbed into the seam with a spatula. The gaps are filled with sealant using special guns.
-
Excess grout is carefully removed until it hardens.
-
After complete polymerization, remove the masking tape.
-
The sealed joint is sanded to align with the plane.


If the width of the gaps is 5 mm or more, then they should be pre-reinforced with a serpentine. In such situations, only putty is used to fill the gaps between the boards. As a rule, this is true in the places where the OSB adjoins the walls along the perimeter. In the absence of a reinforcing tape, after the composition hardens, cracks may appear, and it will begin to spill out over time.
In addition to the traditional grouting methods listed, in some cases it is necessary to resort to alternative options. For example, when the temperature drops to +5 degrees, you cannot use a sealant and putty. A rational solution can be:
-
autoplasticine;
-
two-component automotive putty;
-
rubber based mastic.



It is important to take into account that the listed compositions are used for outdoor work.
If we are talking about the interior decoration of unheated rooms, then the use of substances with a pungent odor and toxic emissions is unacceptable. In such situations, elastic cork can be used as a filling material for expansion joints.
However, this option has a number of significant drawbacks, based on which many experts prefer a liquid cork used when installing a laminate flooring. Another, albeit less common, method is to close the cracks with thin wooden slats. To do this, you will have to make gaps of the same width using a hand mill.

For the installation of OSB slabs on the ceiling, see the video.
The comment was sent successfully.