Features of OSB sheets 12 mm
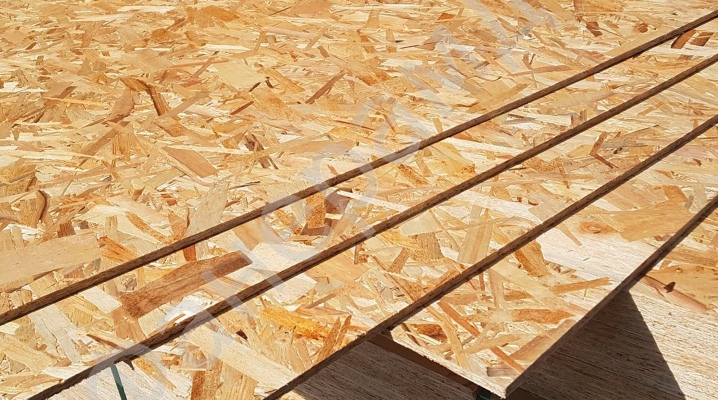
It is very important for any builders and repairmen to know the features of OSB sheets 12 mm thick with dimensions of 2500x1250 and other dimensions of plates. You will have to carefully familiarize yourself with the standard weight of OSB sheets and carefully select self-tapping screws for them, take into account the thermal conductivity of this material. A separate important topic is learning how to determine how many OSB boards are in a pack.
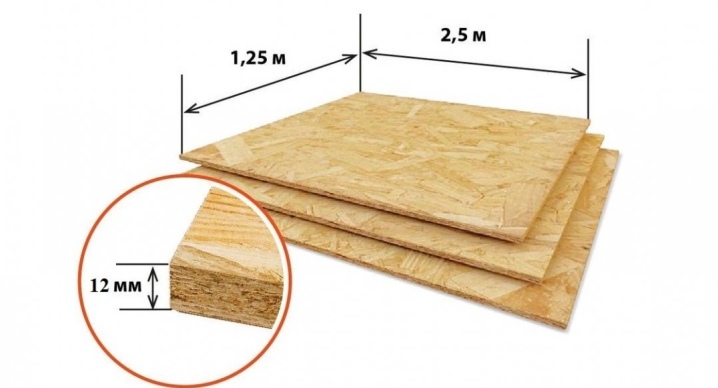
Main characteristics
The most important thing when describing OSB sheets 12 mm thick is to indicate that this is a completely modern and practical type of material. Its properties are convenient for use for construction purposes and in the formation of furniture products. Since the shavings are located longitudinally on the outside, and on the inside - mostly parallel to each other, it is possible to achieve:
- high overall strength of the slab;
- increasing its resistance to dynamic mechanical stress;
- increasing resistance also in relation to static loads;
- optimal level of durability under normal operating conditions.

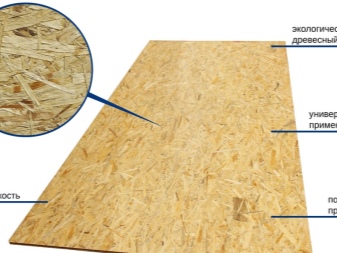
But we must take into account the difference between the individual versions, which will be discussed later. Now it is important to characterize the standard sizes of OSB sheets. Certain misunderstandings may arise with this, because even in the Russian Federation, the import standard EN 300: 2006 is often used by manufacturers. But not everything is so bad - the norms of the European act were taken into account and even taken as a basis when forming the freshest domestic standard of 2014. Finally, there is another branch of standards, this time adopted in North America.
Before clarifying the parameters and properties of the slab, their compliance with the standard, you need to additionally find out which specific standard is applied. In the EU countries and the Russian industry oriented towards them, it is customary to develop an OSB sheet with a size of 2500x1250 mm. But North American manufacturers, as often happens, "go their own way" - they have a typical 1220x2440 format.
Of course, the factories are also guided by the customer's requirements. Material with non-standard dimensions may well be released.


Quite often, models with a length of 3000 and even 3150 mm enter the market. But this is not the limit - the most common modern technological lines, without additional modernization, ensure the production of slabs up to 7000 mm long. This is the largest product that can be ordered in accordance with the general procedure. Therefore, there are no problems with the selection of products of a specific size. The only caveat is that the width almost never varies, for this it would be necessary to expand the processing lines too much.
Much also depends on the specific company. So, there may be solutions with the size 2800x1250 (Kronospan). However, most manufacturers still make a product with uniform parameters. A typical OSB with a thickness of 12 mm (regardless of dimensional standards) can withstand a load of 0.23 kN, or, in more affordable units, 23 kg. This applies to products of the OSB-3 class.


The next important parameter is the weight of such an oriented slab.
With a size of 2.44x1.22 m, the mass of such a product will be 23.2 kg. If the dimensions are maintained according to the European standard, the weight of the product will increase to 24.4 kg. Since in both cases a pack contains 64 sheets, knowing how much one element weighs, it is easy to calculate that a pack of American plates weighs 1485 kg, and a pack of European plates weighs 1560 kg. Other technical parameters are as follows:
- density - from 640 to 700 kg per 1 m3 (sometimes it is considered that from 600 to 700 kg);
- swelling index - 10-22% (measured by soaking for 24 hours);
- excellent perception of paints and varnishes and adhesive mixtures;
- fire protection at the level not worse than G4 (without additional processing);
- the ability to firmly hold nails and screws;
- bending strength in different planes - 20 or 10 Newtons per 1 sq. m;
- suitability for a wide variety of types of processing (including drilling and cutting);
- thermal conductivity - 0.15 W / mK.

Applications
The areas in which OSB is used are quite wide. They largely depend on the category of the material. OSB-2 is a relatively durable product. However, upon contact with moisture, such products will be damaged and quickly lose their basic qualities. The conclusion is extremely simple: such products are necessary for the interior decoration of rooms with typical humidity parameters.
Much stronger and slightly more stable than OSB-3. This material can be used where the humidity is high, but is fully regulated. Some manufacturers believe that even the facades of buildings can be sheathed with OSB-3. And this is really so - you just have to thoroughly think over the necessary protection measures. Most often, special impregnations are used for this purpose or a protective paint is applied.
But it is even better to use OSB-4. This material is as durable as possible. It is also resistant to water. Moreover, no additional protection is required. However, OSB-4 is more expensive and therefore rarely used.
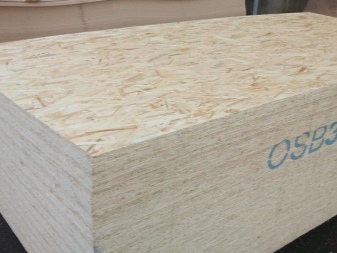
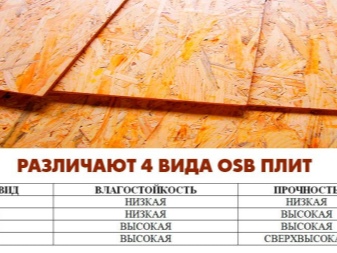
Oriented slabs have excellent sound absorption characteristics. OSB-plate can be used:
- for facade cladding;
- in the process of leveling the walls inside the house;
- for leveling floors and ceilings;
- as a reference surface;
- as a support for lag;
- as a base for plastic cladding;
- to form an I-beam;
- when preparing collapsible formwork;
- as a packing material for transportation of small-sized cargo;
- for preparing boxes for the transportation of larger cargo;
- during the production of furniture;
- for covering floors in truck bodies.




Installation tips
The length of the self-tapping screw for mounting OSB is extremely simple to calculate. To a sheet thickness of 12 mm, add 40-45 mm to the so-called entrance to the substrate. On rafters, the installation pitch is 300 mm. At the joints of the plates, you have to drive in fasteners with a pitch of 150 mm. When installing on eaves or ridge overhangs, the installation distance will be 100 mm with an indent from the edge of the structure by at least 10 mm.
Before starting work, it is required to prepare a full-fledged working base. If there is an old coating, it must be removed. The next step is to assess the condition of the walls. Any cracks and crevices should be primed and sealed.
After the restoration of the treated area, it must be left for a certain time in order for the material to dry thoroughly.


Next steps:
- installation of the lathing;
- impregnation of a bar with a protective agent;
- installation of a layer of thermal insulation;
- sheathing with oriented slabs.
The lathing racks are mounted extremely strictly according to the level. If this requirement is violated, the outer surface will be covered with waves. If serious voids are found, you will have to put pieces of boards in problem areas. The insulation is laid in such a way as to exclude the appearance of a gap. As required, special fasteners are additionally used for the most reliable fixation of the insulation.


Only then can the plates themselves be installed. It must be borne in mind that they have a front face, and it must look outward. The starting sheet is fixed from the corner. The distance to the foundation is 10 mm. The accuracy of the layout of the first element is checked by a hydraulic or laser level, and self-tapping screws are used to fix the products, the mounting step is 150 mm.
Having laid out the bottom row, you can only then mount the next level. Adjacent areas are processed by mounting the slabs with an overlap, forming straight joints. Further, the surfaces are decorated and finished.
You can close the seams with a putty.To save money, they prepare the mixture on their own, using chips and PVA glue.


Inside the houses you will have to work a little differently. They use either a crate made of wood or a metal profile. Metal is much safer and more attractive. Small boards are used to close the voids. The distance separating the posts is a maximum of 600 mm; as when working on the facade, self-tapping screws are used.
For the final coating, apply:
- colored varnish;
- clear nail polish;
- decorative plaster;
- non-woven wallpaper;
- vinyl-based wallpaper.

The comment was sent successfully.