How to process plexiglass?
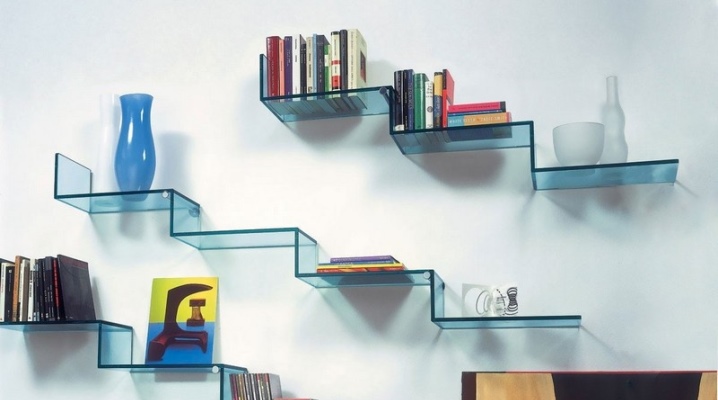
Questions about how to process plexiglass, how to drill it at home, are heard very often. Working with plexiglass on CNC machines has its own subtleties. A separate topic is how to process such a hole additionally. All this will allow even novice craftsmen to avoid many mistakes.
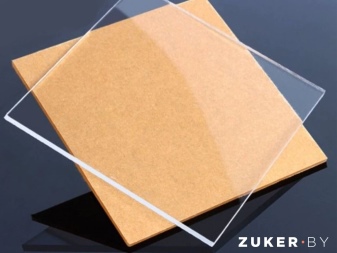
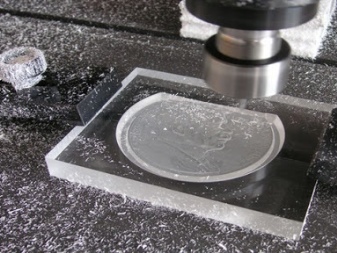
Types of processing
Before talking about exactly how you can process organic glass at home, you need to know about the main types of such processes. If we talk about, in general, all possible options, then the list will be as follows:
- cutting;
- milling;
- grinding;
- plexiglass processing using pumice;
- stamping;
- getting a fold;
- turning work.

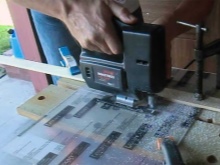
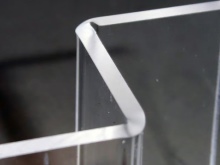
A similar material, regardless of the specific type (this also applies to acrylic glass, of course, and made from polyvinyl chloride), is recognized as a type of thermoplastic plastic. When temperatures rise, even only up to 150 degrees, there is inevitably an increased risk of deformations. Therefore, drilling in organic glass is considered a much more complicated operation than polishing, milling or cutting to size. To properly drill a hole both on the CNC and by hand, it is necessary to carefully select the drill to match the size.
Attention should be paid to the brand of the drilling device.
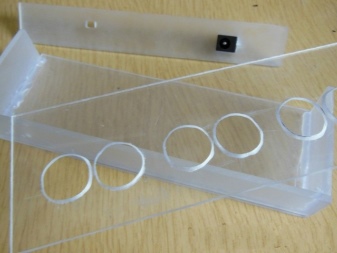
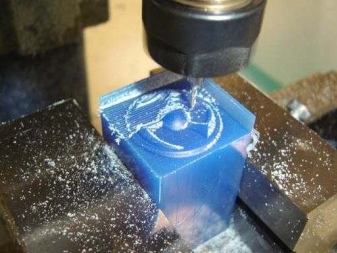
In any case, it must be borne in mind that organic glass, compared to conventional glass:
- twice as light;
- stronger;
- endures blows more steadfastly;
- optimally protects against the spread of heat;
- much more transparent.
By default, the acrylic is covered with an insulating film. It should not be violated. When working with this material, it is necessary to constantly monitor so that it does not heat up excessively, which is achieved by the selection of the tool and the mode of action. All tools must be moved as carefully as possible. Any sudden movement can break the delicate product.
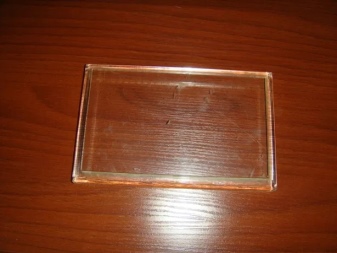
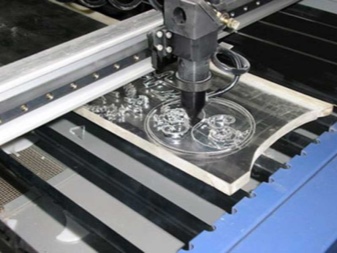
Work rules
Plexiglas can be cut even with elementary improvised means. A banal metal saw is also suitable. In industrial conditions, even special lasers are sometimes used. But in most cases, they still try to find some kind of compromise between the perfection of the instrument and its cost. Therefore, in practice it is usually necessary to use circular saws, band saws and cutters. It is advisable to work with a band saw where a clear straight cut is not needed (that is, when receiving preliminary blanks for molding).
The twisting speed of the belt mechanism is 700-800 m per minute. Where a clear, smooth contour is required, it is advisable to use cutters. With circular saws, precise straight cuts are made. The cut line will be very clear.
Cast acrylic is advised to saw with carbide-hardened teeth; optimal rotation speed from 800 to 1200 m per minute.
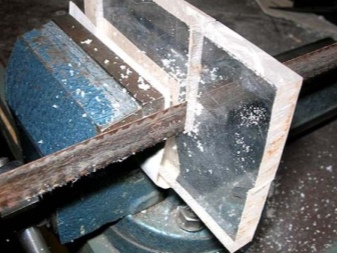
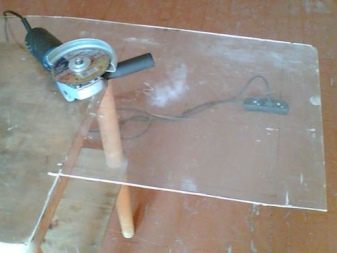
In an industrial environment, it would be better to process plexiglass on high-speed equipment. Faster cuts and low feed rates produce excellent edgesat. The section of the discs is 25 cm. The discs themselves are made from high-speed alloys. Ordinary ferrous metal can also be used, but with hardening with carbide components.
Laser cutting is much more accurate than using power tools. There will be less waste during such work. But in this case, the voltage inside the product rises. Bonding such surfaces is very dangerous.
You can drill plexiglass with a fixed or movable drilling machine. The drill should be made of high speed alloy. It is designed for maximum performance. The deeper the drill is drilled, the more often the drill needs to be lifted. This will allow the chips to be pulled out and at the same time reduce the heating of the material. Cooling the cutting attachments with special fluids or compressed air helps to reduce dangerous internal stresses.
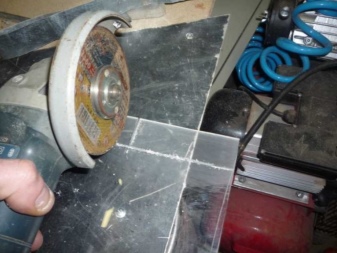
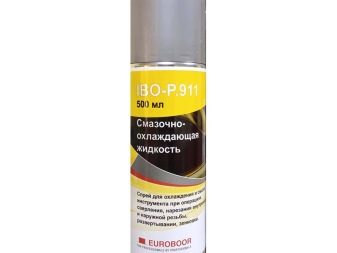
For engraving, in most cases, rippers are used, which are placed on pantographs. The rippers themselves are equipped with small cutters of various profiles.
In difficult cases, laser cutting equipment is used. To make the engraving better, the depth of the beam is limited.
Grinding rough or deformed plexiglass can be done with wet emery coated with fine grains of corundum. When rough grinding is over, the surface is treated with polishing mixtures like VIAM, crocus. The work is carried out either manually or on polishing equipment. Cut edges and matt surfaces are mechanically polished without problems using diamond cutters. On curved cuts and in other difficult cases, high-temperature fire polishing is performed. You will have to work as carefully as possible, carefully cleaning the treated layer; stress is prevented by annealing, which facilitates gluing or staining.
Plexiglass should be molded in three stages:
- warming up;
- actual molding;
- heat removal and cooling.
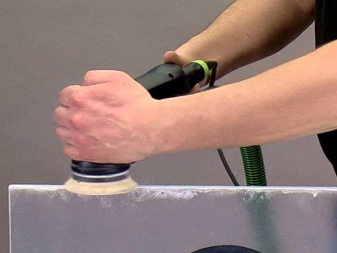
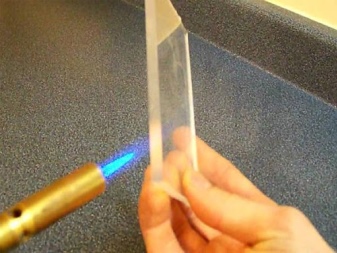
Useful Tips
Extruded organic glass can be glued using:
- film glue;
- polymerizable glue;
- epoxy, polyester adhesives.
A curvilinear cut is made using a nichrome thread or a hot spring. As for turning, the most practical option is the same mode as for high-speed processing of hard wood. Chips are decisive for judging the quality of work.
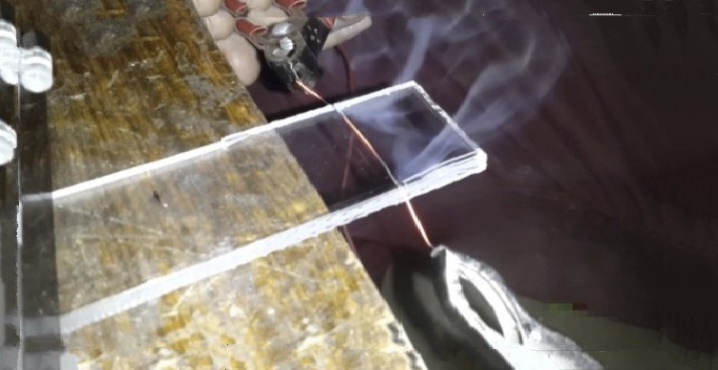
When drilling, the tip angle of the drill should be a maximum of 60 degrees for thin sheets, and 70-90 degrees for thick workpieces.
It is better to bend the plexiglass after thorough heating in the required place; This is achieved with the help of a soldering iron, a construction hair dryer, and in their absence, with the help of a hot metal tube.
Ideal drills:
- have a groove with a rise angle of 17 degrees;
- sharpened on the front corner by 3-8 degrees;
- sharpened at the back angle by 0-4 degrees.
A tapered drill will produce a tapered hole. The stepped tool will assist in the boring of cylindrical channels. A milling drill is taken to make an elongated hole.
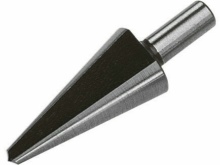
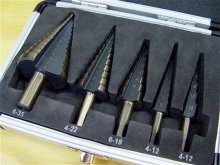
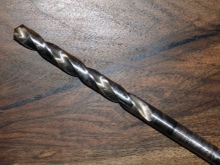
Important: regardless of the type, the tip must be in perfect condition. It is necessary to start drilling at minimum speed, then, when a notch appears, they go to medium speed.
Only in the last third of the material does it make sense to drill as quickly as possible.... But even then we must not forget to periodically drop the speed to a minimum. Having found burrs, drill them with a mineral stone drill at the lowest speeds.
Important: you can drill plexiglass with a drill, but you cannot use a drill-screwdriver. Holes longer than 10 mm and wider than 7 mm are recommended to be machined on stationary machines with water heat dissipation.
How to cut plexiglass, see the video.
The comment was sent successfully.