Types and application of beams for formwork
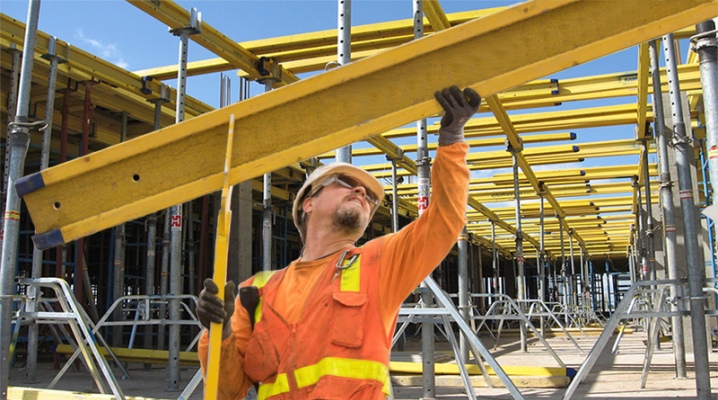
By its design, an I-beam consists of 2 parallel flanges and a rack separating them. The shelves are mainly made of coniferous wood, and the racks are made of laminated veneer lumber or plywood, there are products from other materials. During installation, the beams are attached to each other using a special thorn-groove connection and are additionally coated with adhesive. Systems of varying complexity and configuration are assembled from them, therefore, before installation, it is very important to study the types and methods of using beams for formwork.
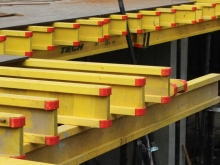
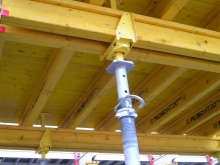
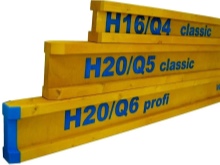
Types of beams for formwork
The most popular domestically produced beams are called BDK-1. The shelves for them are made from pine or spruce, less often from hardwood. For the production of racks, special birch veneer plywood is used, which withstands well the effects of dampness and moisture.
Beams of European production are of 2 main types:
-
UNI - the rack is made of plywood, and the shelves are made of softwood, mainly spruce;
-
OPTI - the shelves are also made of coniferous wood (spruce or pine), and for the production of racks, LVL is used from glued veneer.
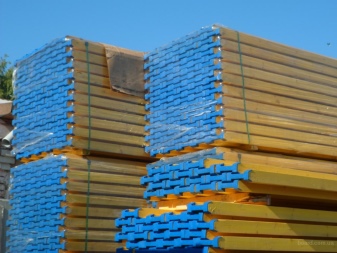
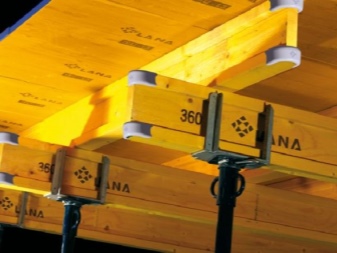
There are also other types of products.
-
Metal and plastic beams. Most often they are used in the construction of formwork for pouring the foundation, as well as when creating floors.
-
Solid ledgers and beams with different sections (rectangular, T-shaped, lattice). Versatile products, among professional builders, are considered more durable than standard wooden I-beams.
-
Leveling I-beams. They are used in order to change or set the correct form of the formwork structure. In addition, they are used for leveling walls, corners, floors, partitions.
Almost all types of beams, regardless of the manufacturer, are yellow. The humidity level ranges from 9 to 13%, and the density of the products is 460-680 kilograms per cubic meter. The weight of a running meter of a standard Russian-made wooden beam is 6 kilograms, European - from 5 to 5.5 kilograms.
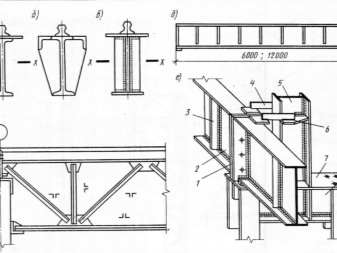
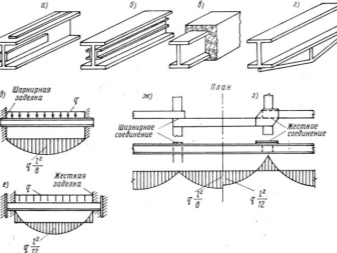
Manufacturing materials
The material of manufacture is selected depending on the type of construction, the type of construction work and the conditions for their implementation. As a rule, specialists determine the necessary modification of the profile on an individual basis, since each material has different technical characteristics.
Formwork beams are made from different materials.
-
Wood - a budget universal option that is suitable for many types of work. Formwork systems made of wooden beams provide minimal shrinkage, fully comply with all basic standards and requirements. During the manufacturing process, wood undergoes a special treatment - it is thoroughly dried and impregnated with special chemical compounds.
-
Metal. Such products are much more expensive, but they are highly durable and reliable. Metal beams are not subject to deformation even after prolonged use, they have more cycles of use. However, due to the high cost, they are most often used only by large construction organizations when performing large-scale work.
-
Aluminum. Basically, only leveling beams are made of aluminum. They are easy to install and lightweight, despite this, they have a very high margin of safety, are reliable and durable.The only drawback of aluminum products is that in case of breakage and deformation, they cannot be repaired and restored.
-
Plastic. Plastic I-beams are used, as a rule, only by private developers and small teams - for the construction of auxiliary structures and outbuildings in the household, in the construction of country houses or summer cottages. Plastic beams are more expensive than wood, but they are more convenient to install - they are lighter in weight, assembled faster, and are not subject to deformation. Monolithic structures created with plastic harden faster.
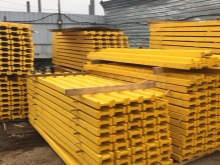
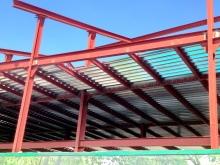
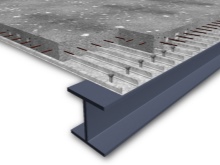
Regardless of the material, all I-beams are manufactured with a longitudinal section, and when installed, they assume contact with at least two anchor points.
Applications
I-beams and other types of beams are used not only to create formwork systems, but also to erect various building structures in the form of walls, partitions, floors or columns.
Formwork beams are used for many types of general construction work, systems of these elements are used for construction:
-
residential buildings;
-
auxiliary buildings in the subsidiary farm;
-
large and small industrial facilities;
-
warehouses and hangars;
-
tunnels and bridges;
-
various designs of complex configuration.
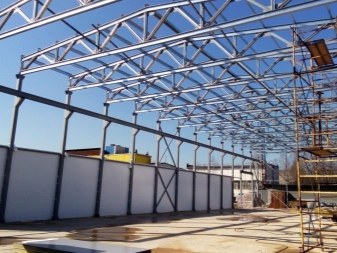
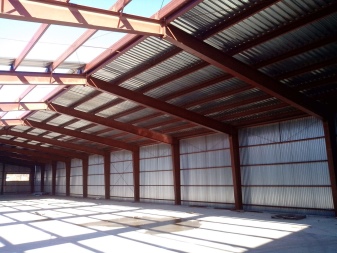
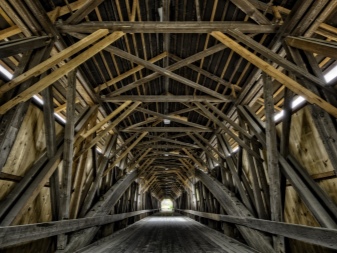
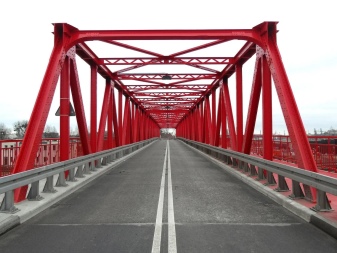
The wide popularity of their use is explained by the ease of transportation and installation, duration of use, versatility. The use of beams allows obtaining flat and smooth surfaces, guarantees a high level of load-bearing capacity of the assembled structure.
Mounting
When assembling formwork structures, all technological requirements should be strictly observed, as well as the rules of installation work should be taken into account, depending on the type of product and the material of its manufacture.
The procedure for installing the formwork system from beams:
-
the site is being prepared - garbage is removed and the surface of the site is leveled;
-
supporting tripods are installed - the distance between them will depend on the complexity and weight of the entire system, but in any case it should not exceed 1.5 meters;
-
racks with holders are exposed, on which the beams will be directly attached;
-
first longitudinal crossbars are mounted, and on top of them are transverse ones, while it is important to maintain the same installation step - 50-60 centimeters;
-
vertical side shields are fixed on the beams, the grooves between the individual elements are closed with plastic wrap;
-
horizontal shields are laid, with the help of the building level, their plane is adjusted and leveled.
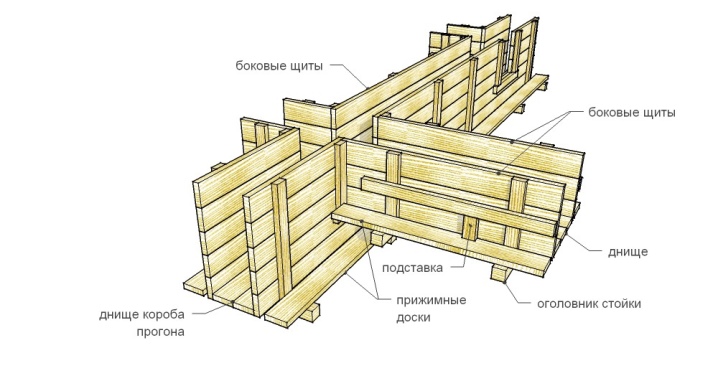
When installing, it is important to take into account that each structural element is designed for a certain load. When pouring the concrete mixture, non-compliance with the standards can lead to deformation and failure of the entire system.
How to properly lay beams for formwork, see the video below.
The comment was sent successfully.