Styrofoam formwork
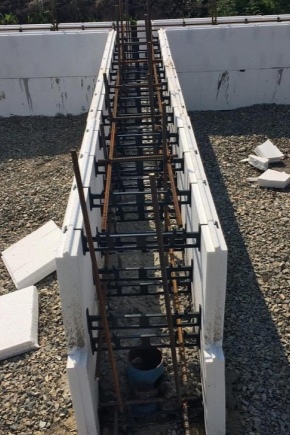
Monolithic construction, where non-removable formwork is used, despite its long history, has become popular relatively recently. At the same time, this method of erecting buildings has not yet gained its full popularity, and the number of such buildings continues to increase.
Formwork today is made of different materials, but the most practical solution would be polystyrene foam formwork, although, in fact, we are talking about the fact that it is made of polystyrene foam. True, now it is more fashionable to say that such a formwork is made of polystyrene foam, because this is the name of the expanded polystyrene trademark. Let's try to figure out what this structure is and how to mount it yourself.
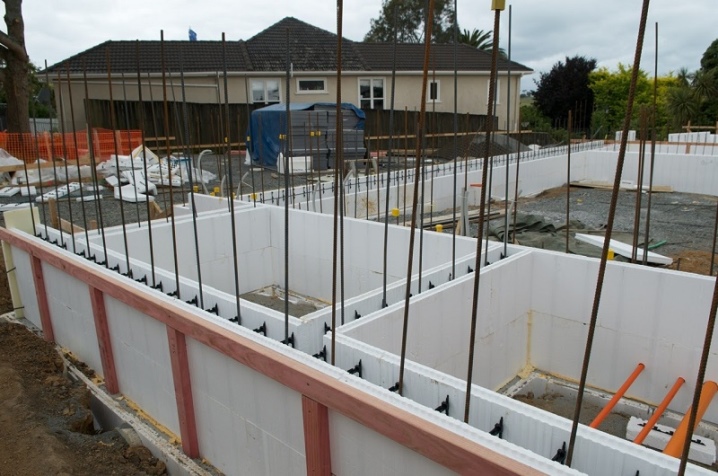
Advantages and disadvantages
If we talk about the advantages that a non-removable foam formwork has, then the following factors should be mentioned.
- The main advantage of all structures of a non-removable nature, which are made of materials with a low weight, will be the presence of an auxiliary type function. In addition to creating a space where concrete can be poured, formwork of this type will also carry out an insulating function. The bases and walls, which are made in one piece, do not need to be insulated yet, which will save money. And if, instead of the mentioned material, you use the most ordinary wooden formwork, then you simply will not get such an effect. With a reduced thickness of monolithic-type floors, polystyrene foam plates will make it possible to store one third more heat than if the walls are made of brick of ordinary size or concrete.
- The fixed formwork made of the mentioned material not only retains heat, but also provides moisture protection, which will be important in winter and when the seasons change. This allows you to increase the durability of the monolithic type base, even in difficult conditions, by at least 15-20 percent.
- Reducing the cost estimate for the construction of the facility. If we take into account that a fairly significant percentage of the estimate is made up of the costs of creating walls and foundations, then the use of this category of formwork allows you to reduce the thickness of the wall due to additional thermal insulation and make the costs of the base lower. In total, you can save about 30 percent in money.
- The use of a material such as expanded polystyrene allows concrete to gain strength evenly in all places, even at temperatures up to +5 degrees Celsius. Thermal insulation makes it possible to keep the temperature of the solution, which is inside and at the edges of the pour, at the same level. For this reason, the hardening of the material occurs more evenly, which increases the strength characteristics of the concrete solution. In timber formwork, the mortar will quickly become at the edges, and inside the temperature drops much more slowly. Because of this, the quality of concrete decreases, and the increase in strength is carried out unevenly.
- It is not difficult to assemble this type of formwork. This does not even require any special skills, thanks to which everyone can do it.
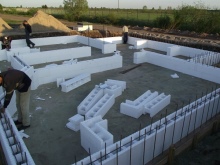
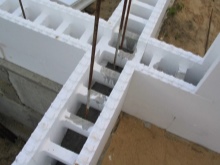
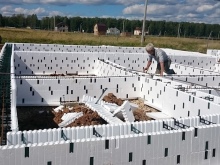
Cons of this design.
- A building that was created using non-removable formwork cannot be reconstructed or rebuilt in any way. When planning a construction, especially an individual one, you should remember this and immediately make the building plan so that it is final.It will also be extremely important to mark everything as accurately as possible and carry out the laying of communications when pouring monolithic walls.
- A serious drawback will be the fact that it is impossible to pour the solution if the temperature is below +5 degrees. In addition, at high temperatures, there are also difficulties, because if it is too hot, then you will have to additionally humidify the solution.
- The protection made of expanded polystyrene plates does not allow the walls to "breathe". To solve this problem, even at the design stage, it is required to foresee the installation of forced ventilation in advance. Only such a solution makes it possible to eliminate the greenhouse effect inside the building without reducing its thermal insulation benefits.
- It will be important to carefully adjust the blocks so that there are no breaks. If the formwork is loose, moisture will begin to get inside the base, which will cause the formation of fungus. It is especially important to pay attention at the moment to builders without experience who assemble formwork from such material on their own.
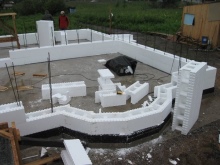
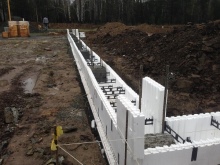
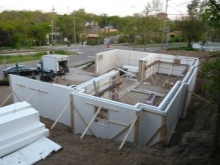
Main characteristics
It should be said that this method makes it possible to create monolithic structures. And due to the use of reinforcement, the strength of the structures being erected increases significantly. The characteristics of the structures make it possible to install such houses even in seismically hazardous places. All parts of the structure will have the highest possible resistance to vertical-horizontal loads.
Moreover, if any miscalculations were made during the formation of the foundation, monolithic walls allow them to be compensated without problems. And the walls themselves, with serious shrinkage or seasonal movement of soils, will simply not be covered with cracks.
At the same time, expanded polystyrene itself is a light and rather delicate material that should be stored in a place protected from wind and ultraviolet radiation.
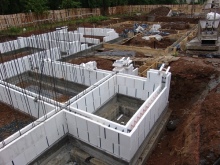
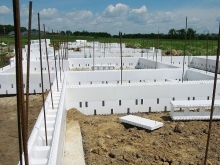
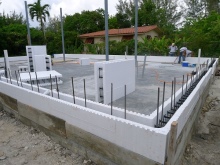
Species overview
It should be noted that formwork can be of various types:
- removable;
- non-removable type.
It is the latter option that is increasingly being used. It should be added that expanded polystyrene is also divided into groups according to two criteria:
- by type of construction;
- by scope.
Let's say a few words about this in more detail.
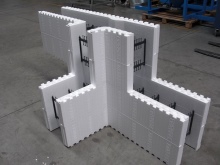
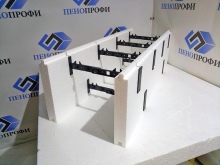
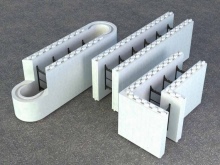
By construction type
According to this criterion, polystyrene foam formworks are:
- cellular;
- classic;
- advanced.
The first category is a large number of single blocks that are hollow inside. They are fixed with each other according to a special technique, which is somewhat reminiscent of a children's construction set of a honeycomb type. The cavities between them allow the solution to freely enter the formwork. Then the reinforcement is carried out with ties of vertical and horizontal type, which are mounted inside the cells of expanded polystyrene.
Such blocks are created only by an industrial method.
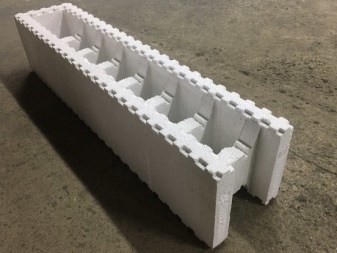
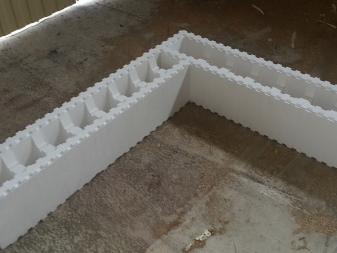
The second category differs in that for the fencing of the future structure of a monolithic type, plates of extruded polystyrene foam, mounted on 2 sides, are used. Metal ties are used to fasten them together. This option is similar to a conventional formwork for pouring concrete, made of plywood or boards.
The third category is similar to the classic version, but instead of the usual metal screeds, the slabs are fixed with wood or metal beams. This compensates for the mortar forces, which are aimed at crushing the mold.
To improve the indicators of the strength type, stops and struts are used.
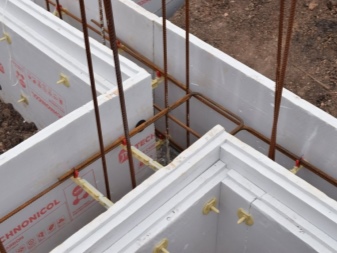
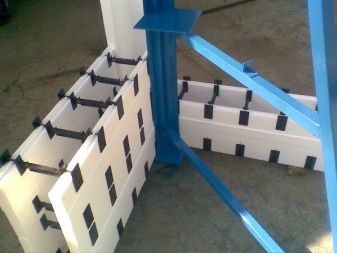
By area of use
According to this criterion, formwork from the mentioned material is used:
- for walls in residential premises;
- for the pool (we are talking about the insulation of the walls of such structures);
- for strip foundations;
- to create so-called warm basements;
- for warming warehouses, as well as various heated rooms that will be used for industrial purposes.
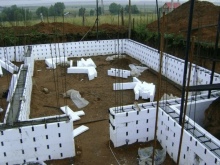
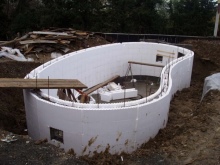
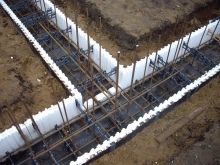
What do you need for work?
It should be said that the formation of monolithic structures with non-removable forms does not require any serious qualifications. Even an inexperienced person can do this kind of work. For work on a small object, only a couple of people are enough.
If we say what is required for the work, then these are the following materials:
- necessary fasteners;
- blocks of expanded polystyrene;
- the required amount of concrete;
- kneading equipment;
- drawing documentation, thanks to which it will be possible to check the amount of required materials.
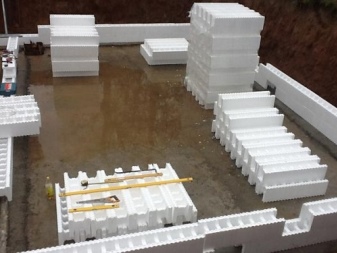
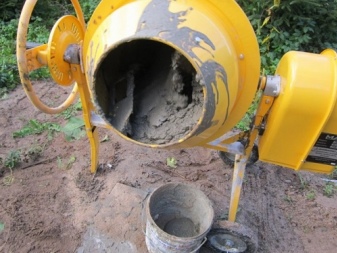
DIY installation
Speaking about the installation of polystyrene foam formwork with your own hands, it should be said that its installation can be divided into several parts:
- assembly of formwork;
- reinforcement strapping;
- pouring concrete solution.
Work begins with the fact that for the installation of the first row of blocks, it is necessary to make a base of a waterproof type. In advance, vertical reinforcing bars should be installed, which will tie the formed wall to the foundation into a single structure. It is on them that you need to "string" blocks, as it were.
When assembling the aforementioned series, you need to carefully check the dimensions with the design ones so that there are not even the smallest deviations.

The rest of the rows should be assembled with an offset of about 50 percent of the block so that the seams can be tied. This will give the structure additional rigidity.
In addition, the vertical type reinforcement serves as an attachment for the base with the wall. Horizontal ties are also called upon to ensure the strength of the monolith. In each row, horizontal rods should be overlapped. They need to be tied with steel wire. This device also needs to be connected to the rods located vertically.
Note that the reinforcing mesh of high rigidity does not allow concrete, which has a heavier mass, to squeeze the blocks out, despite the fact that they are much lighter.
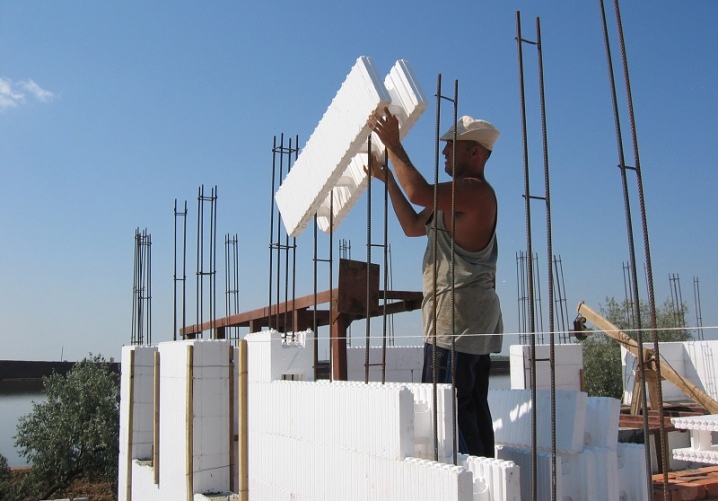
Now work should begin on pouring concrete into the formwork. But before that, it is required to lay the necessary communications. To do this, you need to lay transverse pieces of pipes in blocks. Moreover, the passes must be done in different places. When the concrete gains the required strength, it will be impossible to install plumbing wiring and pipes inside the walls.
For pouring monolithic walls into expanded polystyrene forms, concrete is used only with fine-grained fillers. In addition, in no case should more than 3 rows of formwork be poured. When the mortar is poured, it needs to be compacted with a vibrator and smoothed. Gradually, the formwork should be built up by pouring concrete until the parameters that are contained in the project are achieved.
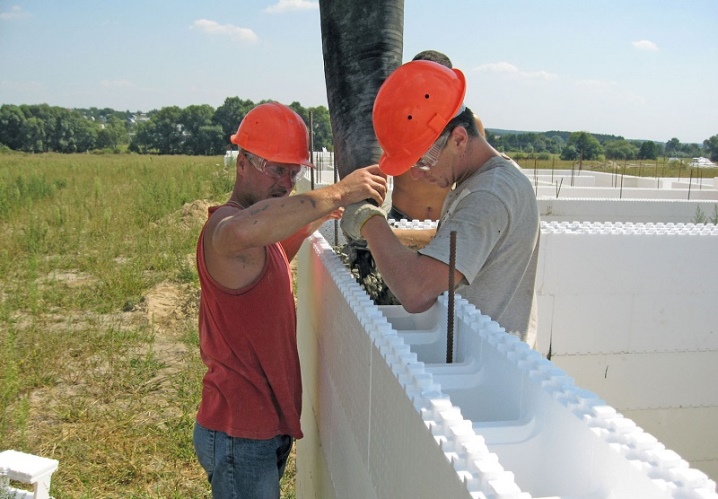
Instructions for adjustable fixed formwork made of expanded polystyrene in the video below.
The comment was sent successfully.