Varieties of refractory mixtures and the secrets of their use
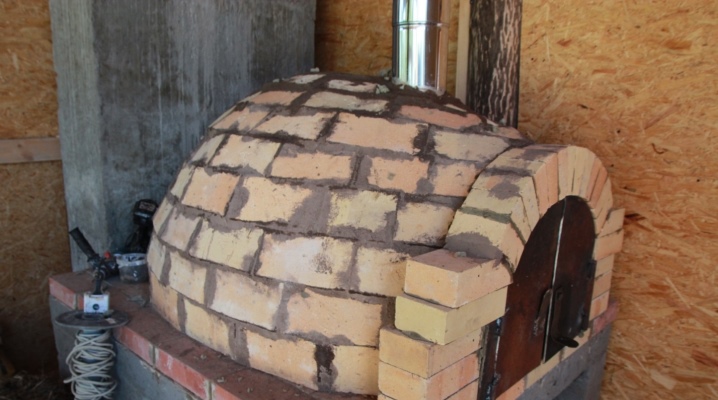
Clay-fireclay and cement-lime, as well as other refractory mixtures for stoves and fireplaces, for masonry and plaster are widely used in the construction industry. They differ markedly from classic solutions, which crack when the operating temperature rises, and are able to withstand direct contact with a source of open fire. An overview of heat-resistant mixtures "Alaks", "BoRoss" and others used by stove-makers and builders will help to choose the appropriate option for a fireplace or hearth.
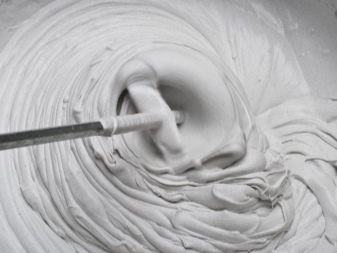
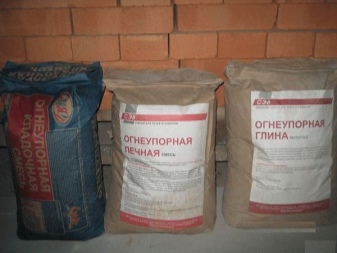
Peculiarities
The main features of any refractory mixture are directly related to its purpose. Dry formulations in this category will withstand significant temperature increases. They are easy to prepare, measured in a certain proportion. The basis of most refractory mixtures is clay - a material that is much more suitable for use in stoves and fireplaces than Portland cement. In addition, such formulations have the following properties:
- high strength;
- weather resistance;
- long service life;
- good adhesion to different surfaces;
- biological resistance;
- impermeability to gaseous substances;
- lack of dust formation.
Refractory mixes are a specialized type of building bulk materials.
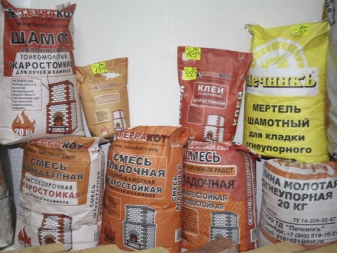
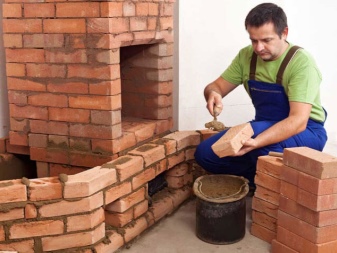
Before use, they must be mixed with water, add aggregates responsible for density and consistency, and bring them to a given density. The main purpose of refractory mixtures is brick laying in ovens and fireplaces.
Description of species
All refractory mixtures presented in finished form are usually divided into categories according to their characteristics, purpose and composition.
According to their purpose, they can be of these types.
- For laying ovens. For fireplaces, tandoor and Russian fireboxes, special clays are used, as well as mixtures based on them. The finished composition is most often called mortar or chamotte, has a common structure with brick. Such an oven masonry mixture does not require complex preparation, it does not dry out, but is baked when heated, gaining strength.
- For plastering. Outdoor mix can be useful in finishing and coating the stove. Heat-resistant plaster lining serves as an additional barrier for the release of carbon monoxide, provides good adhesion to bricks.
- For laying bricks in chimneys. Ordinary clay is not good here. The mixture for chimneys is white, made on the basis of lime and gypsum. Condensation does not form on it.
- For furnace foundations. Here, mortars with a predominance of cement are used, especially if a high load on the base is expected.
- Industrial. For the smelting furnace, for boilers and other heat sources reaching maximum temperatures, types and grades of materials are used that can withstand such exposure. For example, a high-grade chamotte mortar is not afraid of heating up to a temperature of +2000 degrees. Such mixtures may contain coke and graphite.
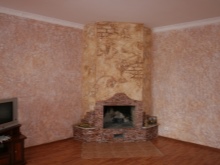
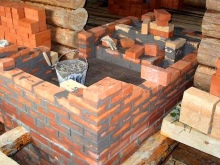
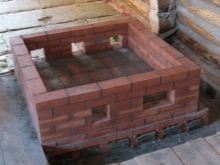
The composition is also of great importance. Most commonly used clay based materials... The presence of additives changes the structure of the solution, affects the rate of its hardening and other characteristics. Multicomponent composition does not have a very favorable effect on the operational properties of stoves, fireplaces, but allows you to eliminate the disadvantages that a particular type of material possesses.
Among the refractory mixtures, the most common are the following.
Clay
They account for up to 80% of all materials in the construction market. The simplest solutions contain only clay and sand mixed with water. Refractoriness is quite high, the masonry can withstand heating up to +1100 degrees.
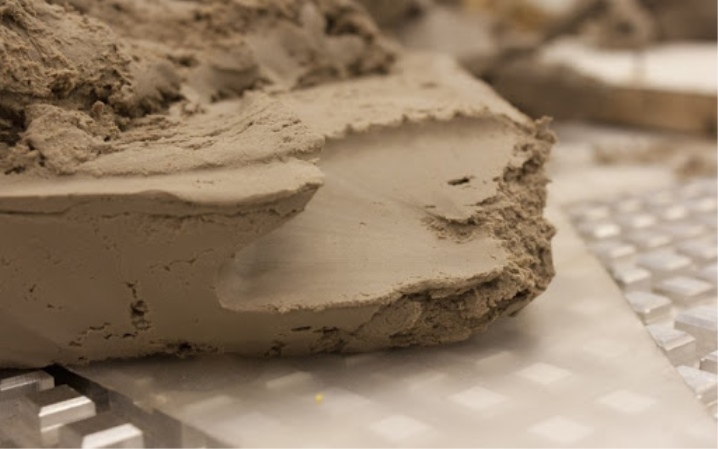
Lime
They are used where there is a high risk of condensation formation, and the heating does not exceed +500 degrees. For faster hardening, they are supplemented with plaster. Mixtures of this type are used in the form of a dough that holds the masonry of stove chimneys and pipes together. When creating such solutions, boiling lime and sand are used.
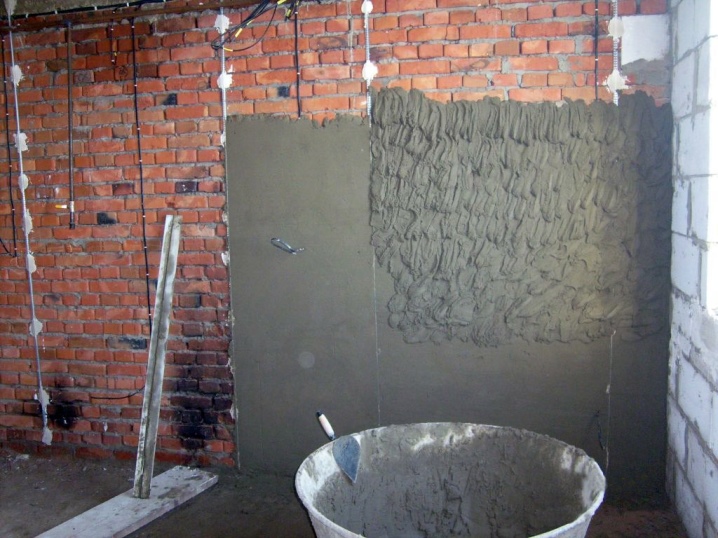
Clay-fireclay
Heat-treated and crushed into powder, such mixtures are closest in composition to fireclay bricks. That's why they are considered the best option for forming masonry using it.
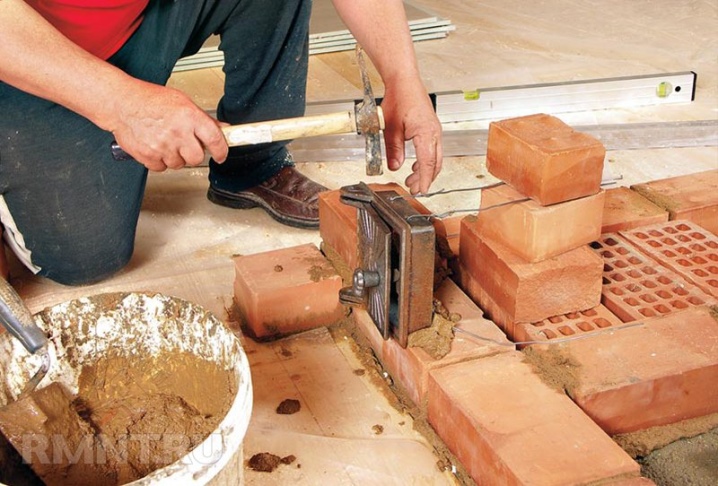
Cement-lime
Compositions with low refractoriness. Suitable for heating no higher than +250 degrees. They can be used when laying out furnace foundations, they harden quickly.
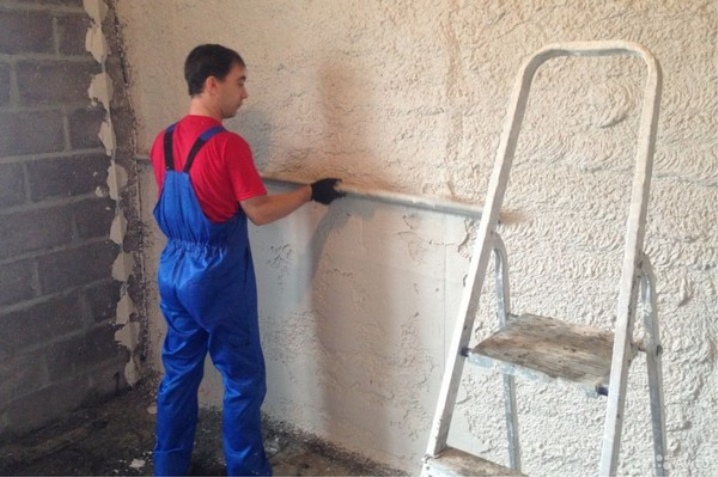
Cement-fireclay
They are optimal in their composition, have high strength, quickly harden, and form heat-resistant seams. Such mixtures are widely used for laying out the furnaces of household stoves.
The choice of a suitable composition directly depends on its purpose, conditions of use, strength requirements and degree of refractoriness.
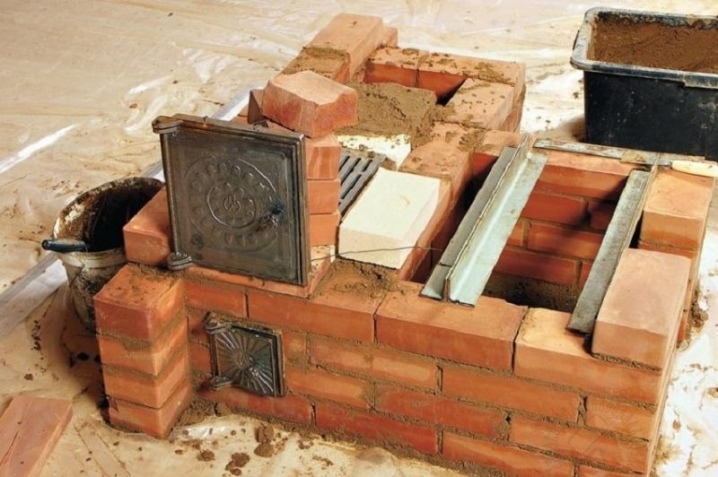
Popular manufacturers
Among the enterprises producing refractory mixtures, local brands prevail on the Russian market. Among the leaders are companies that have already established themselves as reliable suppliers of products. When choosing such dry formulations, the following brands should be preferred.
- BoRoss. The manufacturer of these mixtures is located in the town of Borovichi, Novgorod region. The product range of the plant includes ready-made masonry mixtures for stoves and fireplaces, refractory clay, highly plastic mortar, and kaolin fireclay powder. Products are packed in bags of 5 and 25 kg.
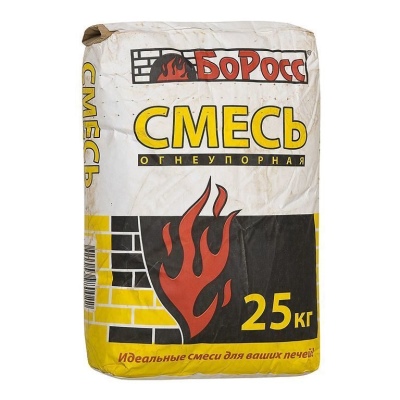
- "Alax". The enterprise produces ready-made mixtures based on lightweight fireclay. Heat resistance reaches +1400 degrees. The main specialization of the brand is industrial concrete.
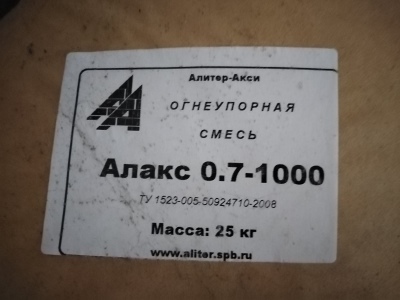
- "Hermes". One of the leading manufacturers of refractory mixtures under the Terracott brand operates in the Podolsk District of the Moscow Region. Under this brand, not only dry mixes themselves are produced, but also coating materials - mastics in packages of 1.5, 5 and 9 kg. Loose compositions are in the form of clay-chamotte powders for masonry, repair of stoves and fireplaces.
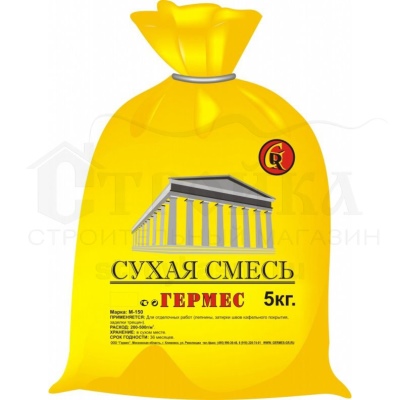
- "Real". Manufacturer - Remix company. The refractory mixture is specially designed for oven masonry. The assortment includes compounds for external finishing.
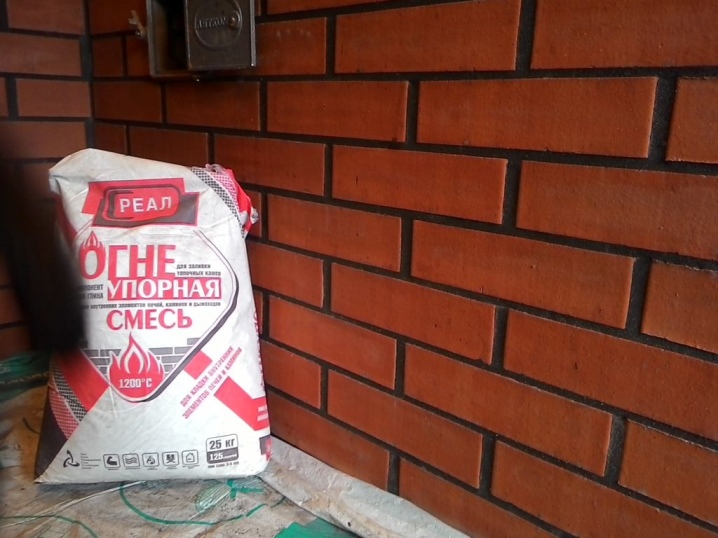
- "Pyramid". The company produces mainly mixtures on a cement-sand base. Refractory compositions in its range are represented by dry powders for oven masonry, including aluminosilicate mortar and chamotte clay.
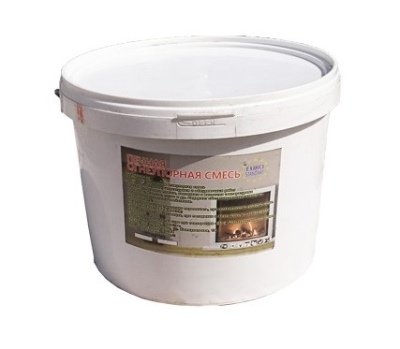
Refractory mixtures for domestic use are usually packed in bags of 20 and 50 kg. For the implementation of masonry on an industrial scale, packages up to 1 ton or more are produced.
How to work with refractory mixture?
Refractory mixtures are prepared taking into account certain recommendations. They need to be diluted according to the instructions, ensuring that all components of the solution form a homogeneous mass, sufficiently plastic, viscous. It is unacceptable to use a heat-resistant mixture, which exfoliates, crumbles, spreads during use. The optimum thickness of the joints during installation should be 1-3 mm.
The drying time of refractory mortars largely depends on their composition. It is possible to dilute the mixture correctly, taking into account the size of the fractions. With a grain diameter of not more than 1 mm, sand is mixed with clay in a 1: 1 ratio.Putting clean compounds can be used when arranging stoves and fireplaces. Clay dries and gains strength under the influence of high temperatures. The use of additives in the form of cement or salt is undesirable, but if necessary, the volume of impurities is no more than 1/10 of the total volume.
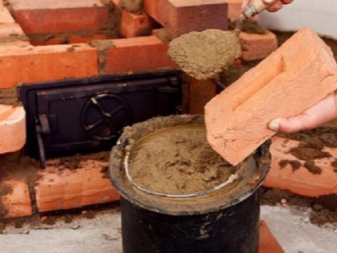
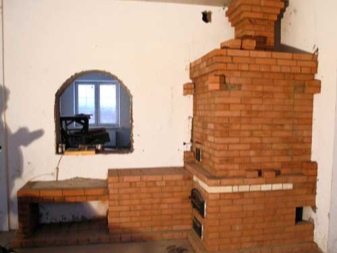
Making refractory masonry mix is fairly easy. It is enough to follow the instructions.
- Clay is poured into the container, filled with water. Leaves for 5-48 hours, stirring occasionally.
- Water is added to the swollen clay. The normal volume is up to 25% of the available volume.
- Seeded sand is introduced.
- The composition is thoroughly mixed.
- Checking readiness is easy: the mixture should slowly slide off the trowel or shovel.
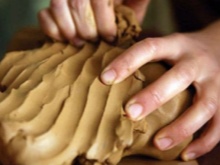
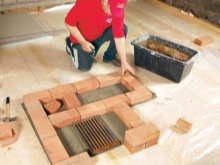
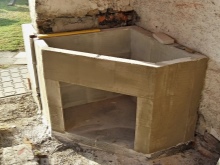
When working with masonry mortars with refractory properties, it is important to pay attention to some of the features and secrets known to the masters. Among the important recommendations that you should remember when starting to create stoves, fireplaces, it is worth highlighting the following points.
- Do not use classic chimney clay. Condensation formed will lead to cracking. Here, mixtures based on lime dough are always used, sometimes with the addition of gypsum for accelerated hardening.
- Maintain the recommended time before the first heating. Violating this rule, you can face warpage of the masonry, its cracking.
- The foundation is laid out using cement-lime or lime compositions.
- The furnace body is formed only on the basis of refractory mixtures impermeable to carbon monoxide. Heat-resistant and heat-resistant options are not suitable here.
- It is recommended to work with masonry mixtures only at atmospheric temperatures not lower than +10 degrees Celsius.
- The hardness of the water must be controlled. At high rates, it cannot be used in the preparation of masonry mortars.
- Pay attention to the color of the sand. Yellow is not suitable for the preparation of solutions used in the construction of the firebox. White - universal, has no restrictions on use.
In the absence of experience in preparing solutions, it is worth purchasing a ready-made composition, which already contains all the necessary ingredients. It is sufficient to dilute such a refractory mixture with water.
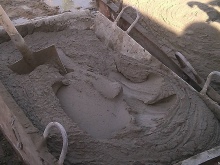
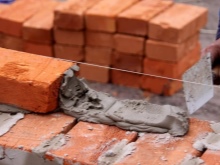
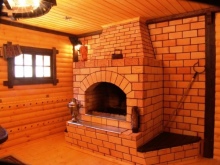
For the varieties of refractory mixtures and the secrets of their use, see the video below.
The comment was sent successfully.