How to make a harrow for a walk-behind tractor with your own hands?
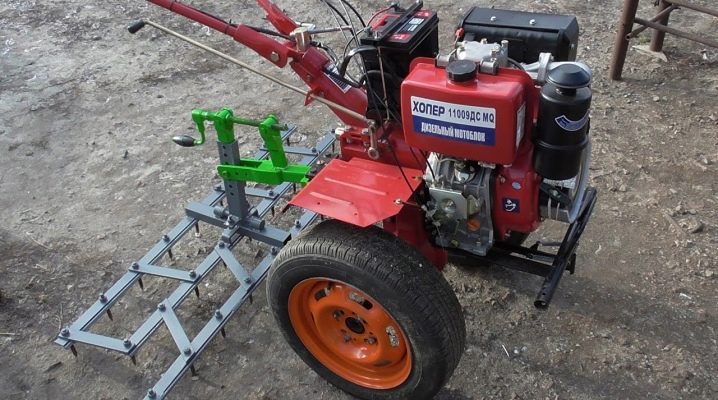
To increase work efficiency and increase productivity, special attachments are used - a harrow. In the old days, horse traction was practiced to carry out work on the ground, and now the harrow is installed on a mobile power unit - a walk-behind tractor (if the plot is small) or attached to a tractor (when the area of the cultivated area is decent). Therefore, a harrow for a walk-behind tractor becomes an extremely significant device for every understanding agrarian, and when it is made with your own hands, it is also an object of pride.
Varieties and their structure
There are several options for loosening the soil, differing in design and having a number of characteristic properties.
Harrows are divided into the following types:
- rotary (rotary);
- disk;
- dental.



Rotary agricultural equipment
If we talk about a rotary harrow for a walk-behind tractor, its main advantage is the optimal removal of the upper layer of soil. To level the ground with her participation is also not a question. The depth of loosening the soil ranges from 4 to 8 centimeters, it can be adjusted, taking as a basis the feature of the work.
The size of the harrow in width is also very important, here not only the resource of the walk-behind tractor is taken into account, but also the area of the cultivated area. As a rule, this value is equal to 800-1400 millimeters. Such parameters are explained by the ability to work comfortably, maneuvering in areas with a small area.
Industrial rotary harrows are made of a quality metal alloy, which makes it possible to actively use the equipment for decades (with appropriate care and maintenance).
On quality agricultural implements, the blade has an oblique configuration, and the teeth are at an angle to the ground, having an ideal invasion angle for high-quality cutting of the soil, leveling it and eliminating weeds.

Disc fixture
A disc harrow is used on dry soils, it performs the same function as a rotary harrow, but is completely different in structure. Here, the key components of loosening are discs, which are similar in configuration to stars. They stand on the same shaft at a specific slope, guaranteeing maximum soil penetration.

Tooth harrow
Cultivation with a walk-behind tractor with a similar device is practiced if it is necessary to obtain a uniform and loose layer of soil. The teeth are arranged evenly and can have all kinds of configurations and sizes: square, knife, round, and so on. The height of the tines depends directly on the weight of the agricultural implement: the higher the weight, the higher the tines. Basically, their parameters vary from 25 to 45 millimeters.
This equipment can have several methods of aggregation with the chassis. In one embodiment, by means of a spring rack, and in the other, hinged.


The tine harrow is subdivided into:
- general direction tooling;
- specialized (mesh, meadow, articulated and other).


How to do it yourself?
In order to start independently creating a harrow for a walk-behind tractor, first of all, you will need sensible drawings. And it is recommended to learn how to compile them on a sample of the most uncomplicated agricultural equipment - a tooth harrow, which, in synthesis with a walk-behind tractor, will safely cope with the plowing of small seed and other material,as well as pre-planting loosening of the soil. In appearance, it will look like a lattice frame with welded teeth or bolts attached to it.


- It is imperative to equip the front side with a hooking device. The hook can also be a conventional bar with a hole, which is placed in the tube of the towing device with fixation by means of a cylindrical or conical rod. Between the hook and the chassis, after complete assembly, the moving chains must be welded.
- So that the tool for loosening the soil for the walk-behind tractor turns out to be reliable, it is preferable to cook the grate from reliable corners or tubes with a square cross section and a steel thickness of more than 3 millimeters. You can give it a finished look with a cage with elements located across and along. In the process of assembling the structure, it is necessary to monitor that each segment of this lattice is at an angle of 45 degrees to the straight line along which the walk-behind tractor moves in order to reduce bending stresses. Additionally, you need to take into account that the entire supporting base must fit into the boundaries of the handles of motor vehicles. In terms of dimensions, it is acceptable to make it at most one meter - only a real tractor will master it wider.
- Next, you need to prepare fangs 10–20 centimeters high. Reinforcing steel with a diameter of 1.0–1.8 centimeters has shown itself to be excellent in this capacity. The most important thing here is to follow the principle: the longer, the thicker. In addition, the teeth are hardened and sharpened before being welded to the grid. There they should be placed 10 centimeters apart (a more rare arrangement is ineffective). It is possible to install the teeth with a slight offset across the row, so that they are more comfortable to cook and they make the necessary loosening depth possible. Along with this, it is necessary to balance so that their counteraction is oriented symmetrically to the thrust shaft, otherwise the walk-behind tractor will start to “wiggle its tail”, as a result of which they will not be able to harrow.






Disc agricultural equipment is the most advanced modificationcarrying out more activities in the cultivation of the soil. At home, a disc harrow can be created exclusively for cultivator type motor vehicles (cultivator). 2 pipes are made, they must be securely fixed on the axis of the cultivator. Due to the complexity of the implementation of this work at home, you will need to give it to the enterprise to a turner or use shafts from a faulty cultivator. The total length of the pipe should be no more than one meter - the cultivator cannot handle an overly heavy device.


Discs with a diameter of approximately 25 centimeters are mounted on the axle. In order to reduce the resistance on them along the edges, cuts are made with an angle grinder every 10 centimeters of the circumference.


The holes for seating the discs are made slightly larger than the diameter of the axles. The discs are mounted with a slight slope towards the center of the shaft. On the left side of the axis, the slope is in one direction, on the right - in the other. The number of disks is taken so that they mutually replenish each other along the slope - they are mainly installed every 5 centimeters.
Making a disc harrow in-house is much more difficult than making a toothed specimen. A self-made device requires the most precise adherence to the dimensions of the elements (in strict accordance with the diagram). It is easier to purchase an inexpensive Chinese one and subject it to revision, having welded all the welds conscientiously, which, as a rule, is not performed at the factory.
Conclusion
It is easy to make a harrow for motor vehicles on your own, but for this purpose, according to the rules, developed diagrams, drawings, source materials and tools are required. The choice of the device directly depends on the skills of the craftsman and the intentions of using the device.
To learn how to make a harrow for a moloblock with your own hands, see the video below.
The comment was sent successfully.