How and how to glue plastic to metal?
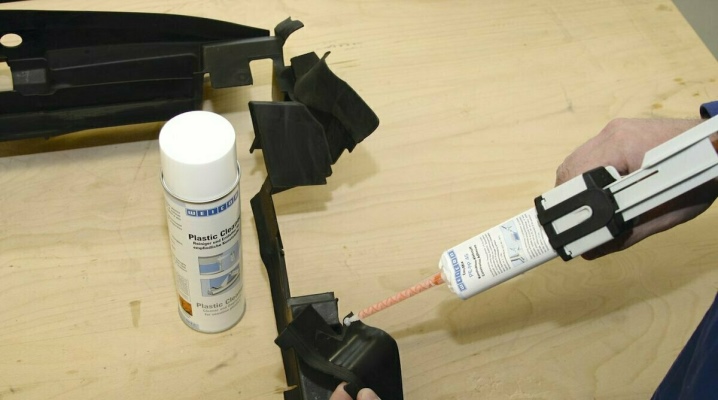
Bonding of plastic to metal is required in areas such as construction, computer technology. Plastic and metal surfaces have different physical and chemical properties. Hence, finding the right adhesive to bond them together can be tricky.
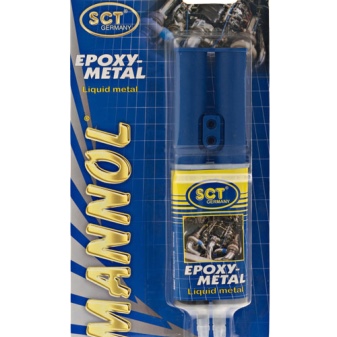
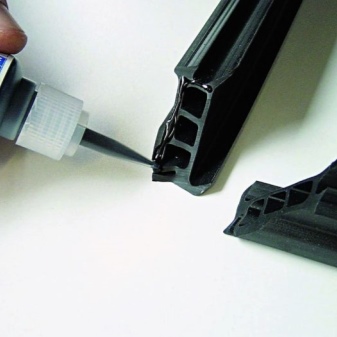
What types of glue can be used?
Many compounds are used to bond plastic to metal. This is a sealant, a two-component waterproof compound, and many others. To protect yourself when working with such a product, you need to know the safety precautions and strictly follow them:
- you need to work in a well-ventilated area;
- when using industrial adhesives, a respirator must be worn to prevent lung damage;
- Always wear gloves to prevent glue and epoxies from contacting the skin;
- it is better to wear safety glasses;
- keep the product away from pets and children.
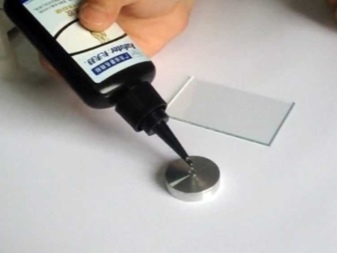
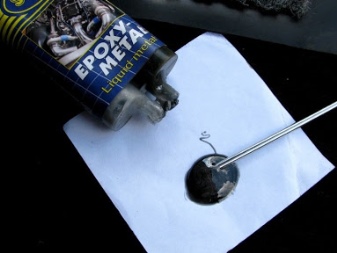
Polyurethane
Polyurethane is a water resistant polymer formed after combining organic units with carbamate bonds. This is the so-called urethane from a certain group of alkanes. It is heat-resistant, therefore it does not melt when heated. Nowadays, the adhesive is produced using polyurethane and is widely used in many industries. It can even be used with wood or paper.
One of the available options would be the moisture resistant and high temperature Loctite PL. This product is easy to use thanks to its convenient packaging. Suitable for both cold and hot work. It can be used for both external and internal work. Does not contain chlorinated solvents. It is one of the highest quality products on the market today.
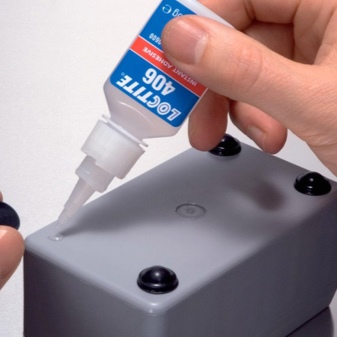
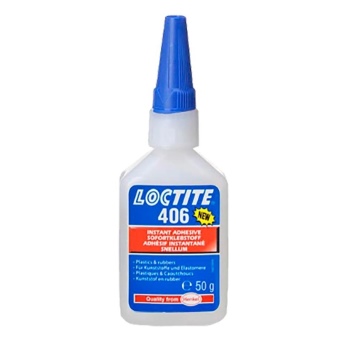
Epoxy
When it comes to glue for bonding plastic to metal, it is best to use a variety of epoxy resins. They usually consist of two components: resin and hardener, which are stored in separate vials or compartments in a syringe. When these components are mixed, a thermosetting chemical reaction is produced that causes the mixture to solidify. Such products, as a rule, have great chemical resistance, water and heat resistance.
The best modern choice is Gorilla 2 Part glue. It creates an inextricable bond between two materials, has the necessary strength, and is also ideal for repairs. Gorilla 2 Part epoxy is perfect for bonding metal to plastic, but it can be used with a variety of other materials as well.
The glue hardens in 5 minutes, but dries completely within 24 hours. The syringe is equipped with 1 push button, which allows you to evenly distribute the components immediately during operation.
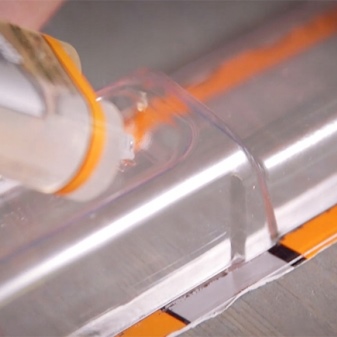
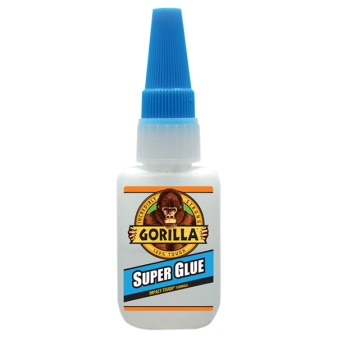
Stirring is required before applying the adhesive to any surface. The glue dries and becomes transparent.
Phenolic rubber
This product was born in 1938. The first brand to release it was Sykeveld. The adhesive was used to bond the car body and the insulating material. Two years later, it was decided to modify the composition. Since 1941, the glue has been widely used in aviation. Any adhesive of this type can be characterized as high strength and powerful.
Let's take the following products as an example:
- "VK-32-20";
- "VK-3";
- "VK-4";
- "VK-13".
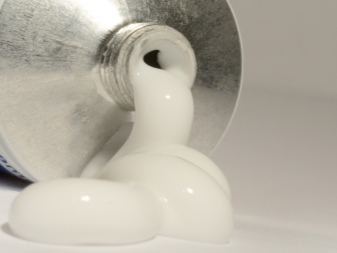
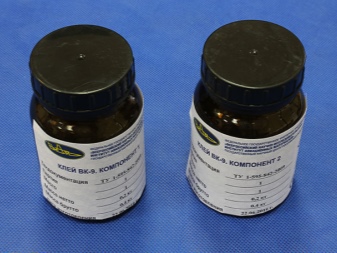
Cold welding
This is another of the options for how you can qualitatively connect different types of surfaces. Cold welding was first discovered by modern society in the early 1940s and was seen as a new phenomenon, but in fact the process has been around for thousands of years. It was found that two pieces of material would stick together in a vacuum until they fuse together.
During the process, deformation occurs, which allows the elements to come into contact. Moreover, the welded seams are much stronger than those that can be seen using other means. Another advantage of cold welding is that there is no need to use intermediate materials.
The principle of operation of this method is not complicated. When two surfaces without an intermediate oxide layer approach each other, the atoms of both penetrate into each other. Research has shown that cold welding can also be performed without excessive force. By applying less pressure for a longer time, a similar result can be achieved. There is another method, which is to raise the surface temperature of the two materials to be joined for a short period of time to speed up the movement of the molecules.
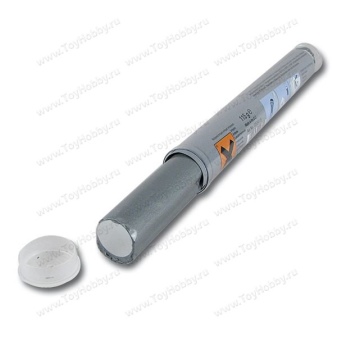
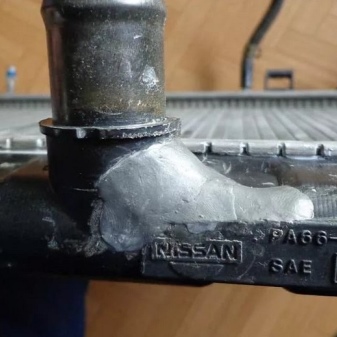
The modern applications for cold welding are numerous. Although it is used according to the situation, and not everywhere, this method allows you to work in many aggressive environments, which was previously impossible. For example, it was impossible to weld underground pipelines carrying flammable gases. But there is one problem: since the weld forms quickly and is considered permanent, it is very difficult to verify its integrity, especially in thicker metals.
Cold welding has some limitations. The connection may fail in a reactive environment or area with a high oxygen content. It is suitable for buried pipes and components located in rooms where there is no risk of exposure to oxygen. For cold welding to be effective, surfaces must be thoroughly brushed and slightly roughened.
If the outer layer of any of the components has a high oxygen content, then adhesion is unlikely. Another important factor is the ductility of the materials used. At least one of the two materials to be joined must be malleable.
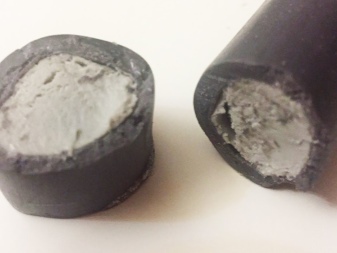
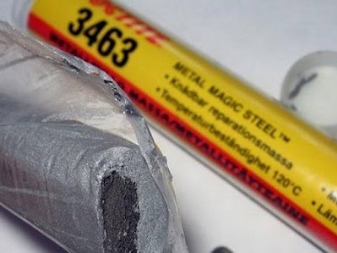
The described method is used in nano- and microprocessor-based industries in high-tech areas. This method is also used in the nuclear field.
Composition selection criteria
When choosing a suitable formulation, it is imperative to take into account the characteristics of the formulations available on the market. It is better to choose a product that does not lose its positive properties on the street, has high durability and has an affordable cost. On the packaging, the manufacturer indicates whether the composition is suitable for gluing metal and plastic or not.
For such products, the mandatory characteristics should look like this:
- sufficient strength;
- peeling can not be observed after gluing the surfaces;
- the glue must be heat-resistant.
For example, the so-called liquid rubber perfectly connects many surfaces. If you need a strong connection that can withstand tensile stress, then this is the ideal solution. The 88-CA has proved itself quite well.
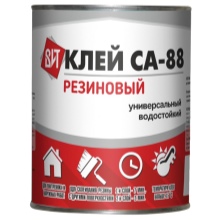
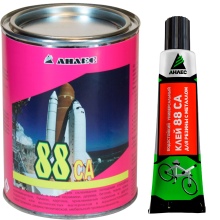

Surfaces that are connected with this tool can be used even under water: both fresh and salty.
Surface preparation
Before gluing surfaces, they must be carefully prepared. Metal and plastic must be cleaned with sandpaper and degreased. This is the only way to increase the adhesive capacity of the adhesive. Moreover, it is sandpaper that quickly and easily removes rust from the metal surface.
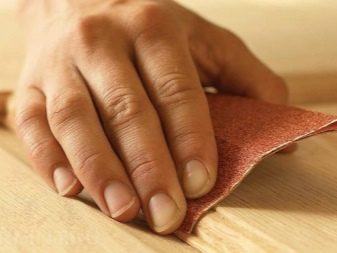
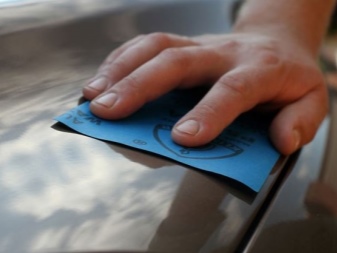
How to glue correctly?
Before starting work, it is advisable to cover the surface of the table with paper so as not to stain it.Next, the surfaces are prepared. Plastic and metal must be cleaned without fail, otherwise it will not work to glue them tightly at home. Both surfaces should be slightly rough.
Next, you should adhere to the following instructions.
- Mix the two components of the epoxy adhesive. The required proportion is indicated on the manufacturer's packaging.
- The mixture is applied in a thin layer to both surfaces. A brush is used for this.
- The glue hardens within two hours, sometimes it takes more time. To improve the result, you can hold the parts under load for a day.
- Excess glue is removed after complete drying. Do not cover the object during the setting period, as the seam requires air circulation.
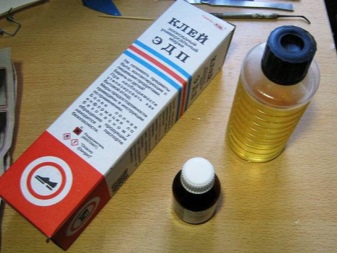
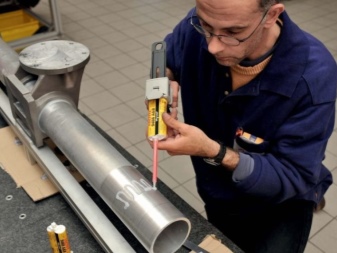
How and how to glue plastic to metal, see the video below.
The comment was sent successfully.