Adhesive for foam blocks: characteristics and consumption
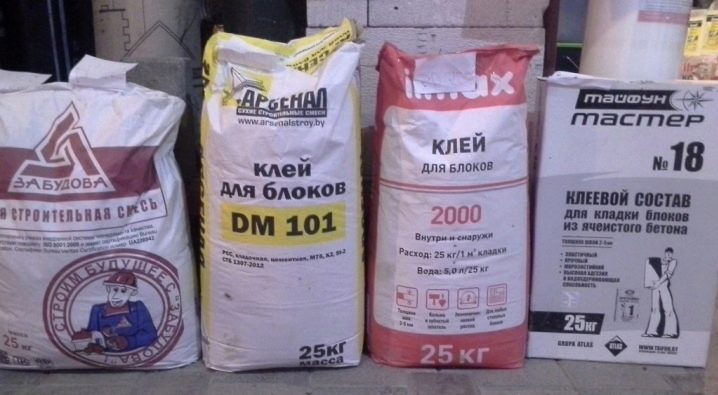
Foam concrete blocks are considered easy to work with and a truly warm wall material. However, this is true only under one condition - if the laying is done with special glue, and not with the usual cement mortar. The glue has a viscous structure, it sets faster, does not give any shrinkage, but the most important thing is that the stones do not draw moisture out of it. Accordingly, the adhesion points of the blocks do not dry out and do not crack over time.
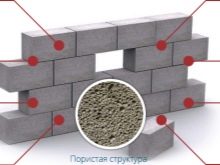
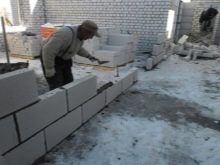
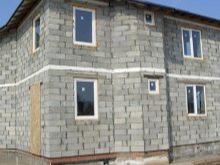
A pleasant bonus is the ease of installation - it is much faster and easier to glue the blocks than to form seams and joints between masonry elements.
It is very important to choose the right adhesive base., since the strength and stability of the entire structure depends on it.
Peculiarities
Disputes about what to prefer - a sand-cement composition or a special glue for adhesion of foam blocks - have not subsided for many years. Both options have their pros and cons.
You can stop at a cement mortar in the following situations:
- the dimensions of the foam blocks are approximately 300 mm;
- blocks differ in the wrong geometry;
- the laying is carried out by builders of average qualification.

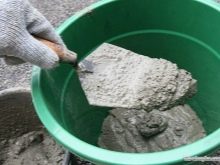
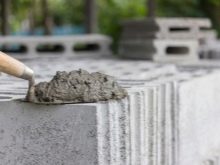
Feel free to choose glue if:
- the blocks differ in the correct standard sizes;
- all work is carried out by professionals with experience of similar work;
- the size of the foam blocks - up to 100 mm.
The active component of the adhesive is the highest quality Portland cement without additives and impurities. The solution necessarily includes fine sand with a grain size of no more than 3 mm, and to improve adhesion, all kinds of modifiers are introduced into the glue.
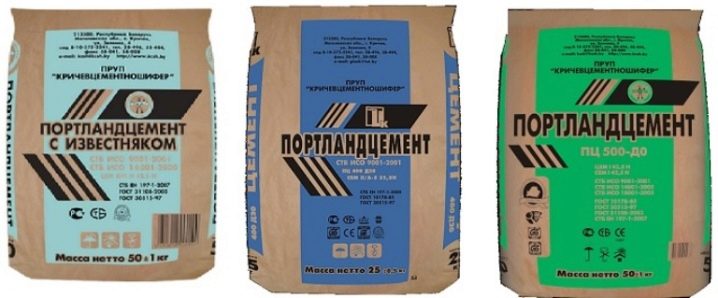
The mixture has high consumer characteristics:
- hygroscopicity;
- vapor permeability;
- plastic;
- good adhesion to foam concrete.
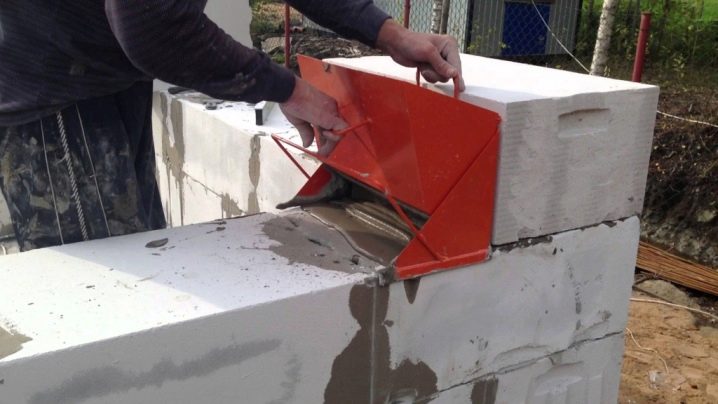
Another indisputable advantage is economy. Despite the fact that 1 kg of glue is more expensive than the cost of cement mortar, its consumption is two times lower. That is why using glue is not only practical, but also beneficial.
The glue contains all kinds of additives, components for protection against mold and mildew, moisture retaining compounds. Special additives make the mixture elastic, which prevents the seams from deforming over time under the influence of temperature changes.
A distinction should be made between mixtures intended for use in different weather conditions. If any mixture designed for t from 5 degrees is suitable for above-zero temperatures, then in the cold season it is worth giving preference to frost-resistant compositions - they can be recognized by the snowflake on the package. But even such frost-resistant formulations are not recommended for use at temperatures below -10 degrees.
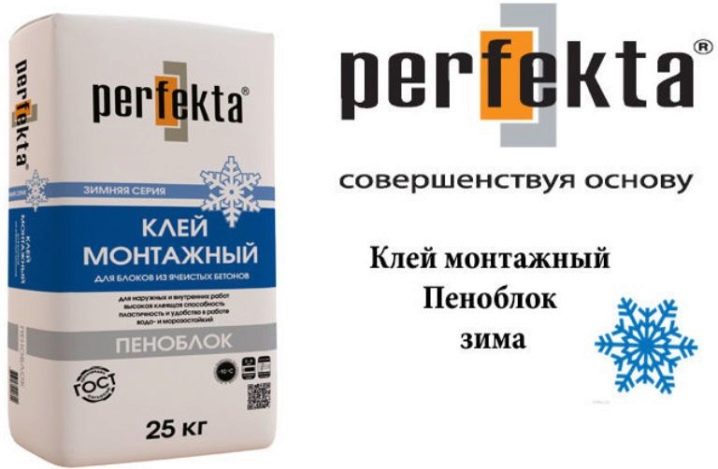
Adhesive for foam blocks is sold in bags of 25 kg.
Advantages and disadvantages
The glue-based composition was not developed by chance - its use has a number of advantages in comparison with the traditional masonry mixture:
- the presence of fine-grained sand in the mixture of Portland cement significantly reduces the thickness of the coating, and, consequently, reduces the consumption of material;
- it is evenly distributed over the surface to be treated, fills all the free space, this significantly increases the adhesive properties of the composition and the effectiveness of its use;
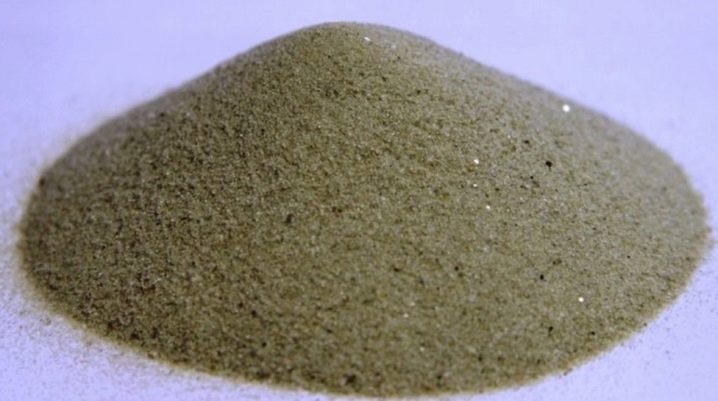
- the water consumption per 25 kg bag of glue is approximately 5.5 liters, this allows you to maintain the standard humidity content in the room and contributes to the formation of a favorable microclimate;
- glue has the ability to retain heat, which is why the likelihood of the appearance of cold surface areas is reduced;
- glue provides strong adhesion (adhesion) of the foam block to the working surface;
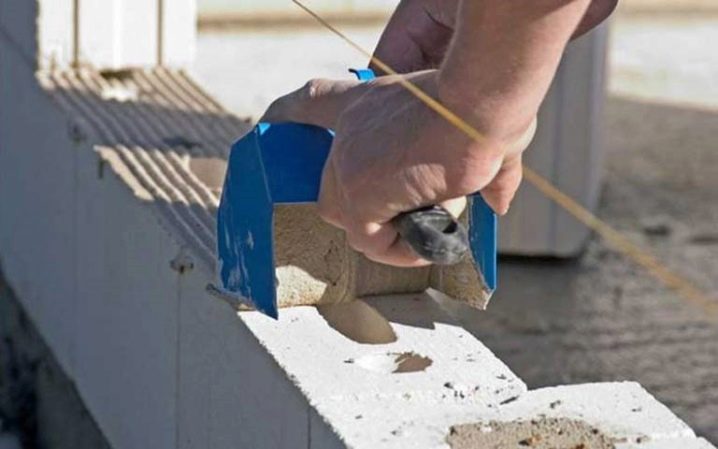
- glue-based solution is resistant to adverse weather conditions, temperature extremes and fluctuations in humidity;
- the composition sets without any shrinkage;
- glue is often put instead of putty, while maintaining all its functionality;
- ease of use - however, this is with certain construction skills.
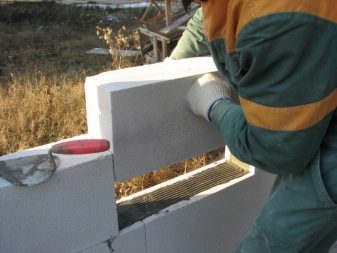
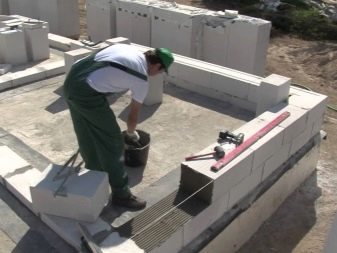
The disadvantages of using glue for foam blocks, many refer to its high cost. Nevertheless, if you look at it, then in terms of 1 sq. m of glue surface leaves 3-4 times less than cement-sand mortar, which ultimately allows you to save on the total amount of work.
Modern compounds are applied in a smaller layer due to the high adhesion strength. An experienced tiler is able to make a joint up to 3 mm in size, while a grout will require a thickness of 10-15 mm. Thanks to such a difference in the output, a gain is obtained, of course, you should not expect significant savings, but at least you will not have to overpay.
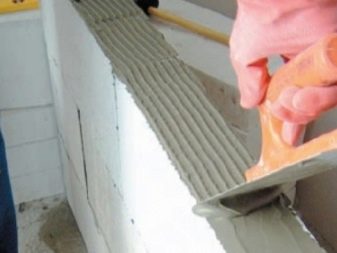
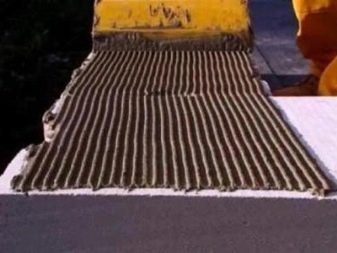
The mortar market offers two typical glue options:
Summer - has a working temperature of + 5-30 degrees Celsius. Its basic component is white cement, the mortar is used within two hours after dilution.
Winter - valid at t from +5 to -10 degrees. Includes special antifreeze additives, requires dilution with hot water and is used within 30-40 minutes after dilution.
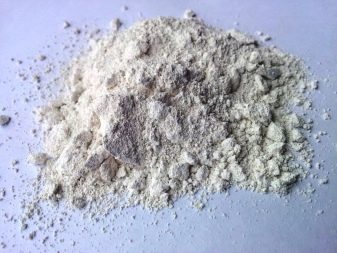
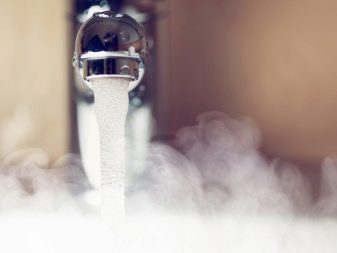
Consumption
Mounting glue for foam concrete is a mixture in dry consistency, which is diluted with water right before the installation of foam blocks. Using a drill or a construction mixer, the solution is stirred until a homogeneous consistency, after which the glue must be allowed to brew for 15-20 minutes so that all components are finally dissolved. Then the solution is mixed again and you can start working.
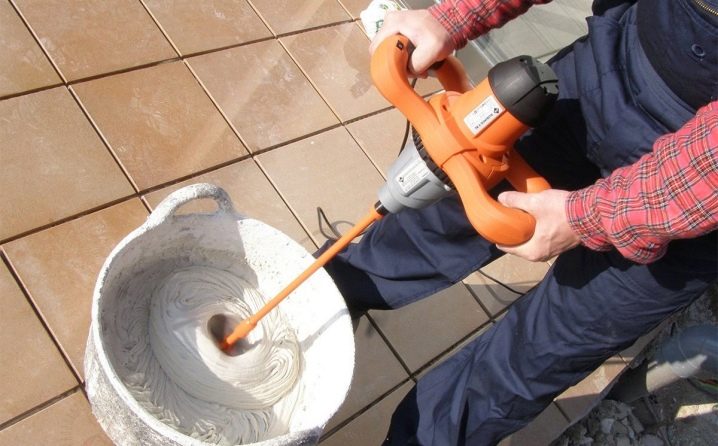
When planning construction work, it is necessary to calculate the required amount of glue, for this they proceed from its standard consumption per cube of surface.
For calculations, builders recommend starting from a seam thickness of 3 mm. In this case, the consumption of glue per cubic meter for foam concrete masonry will be approximately 20 kg. In practice, most inexperienced finishers cannot evenly spread the mortar in a thin layer, and the thickness of the coating is about 5 mm. The same is observed in the case when the foam blocks are not of high quality, have few defects and irregularities. As a result, the consumption of glue will be higher and will amount to 30-35 kg / m3. If you want to translate this indicator into m2, then the resulting value must be divided by the wall thickness parameter.
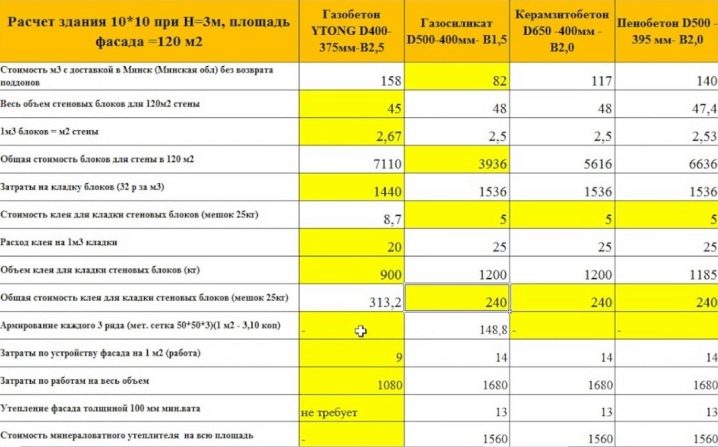
Can you save money? You can if you buy gas foam blocks with profiled edges. Such blocks are joined in grooves, and only horizontal edges need to be covered with glue, the vertical seams are not greased.
It is possible to reduce the consumption of the glue mixture by 25-30% if you use a notched trowel to apply it.
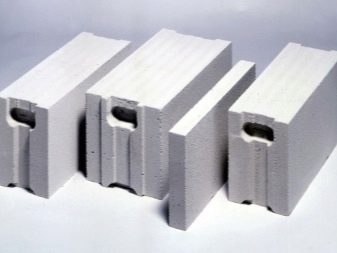
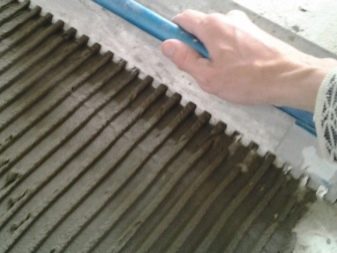
Manufacturers
A wide range of adhesives for foam block masonry often confuses finishers. How to choose the right composition? How not to make a mistake when purchasing a mixture? What should the foam blocks be attached to?
First, remember a few simple rules:
- avaricious pays twice - don't try to chase cheapness
- buy goods from a well-known manufacturer with a good reputation in the building mixtures market
- when making a purchase decision, take into account the season and temperature conditions under which the work will be carried out - it is advisable to purchase a frost-resistant composition for the winter
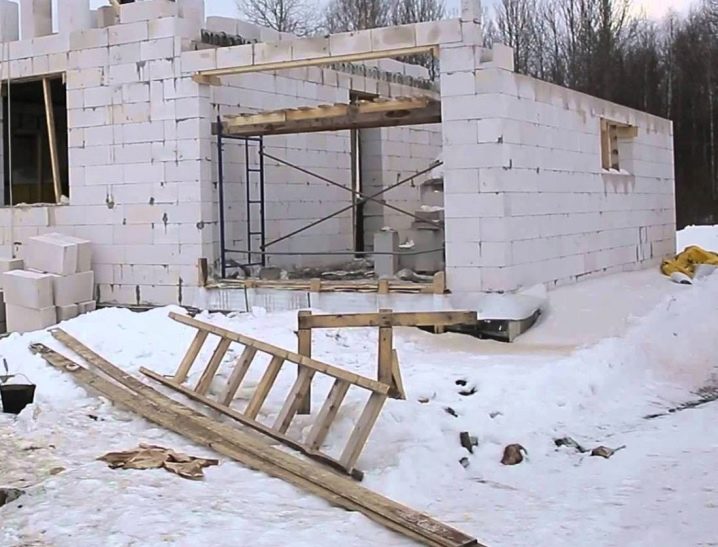
- always buy glue in reserve, especially if your experience in laying foam blocks is small.
And now let's get acquainted with the creators of the most popular adhesives that have earned positive reviews from professionals around the world.
Volma
Volma is one of the leaders in the construction market, which has won the recognition of consumers in Russia and abroad. The adhesive of this brand consists of selected cement, fine sand, filler and pigments of the highest quality. This compound is used for joints of 2-5 mm.
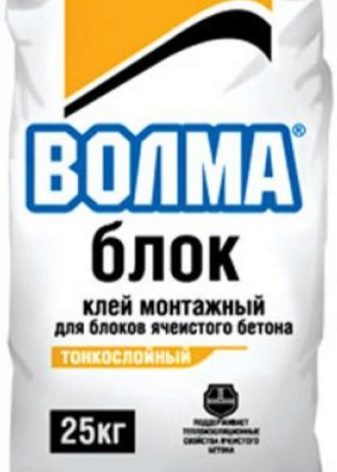
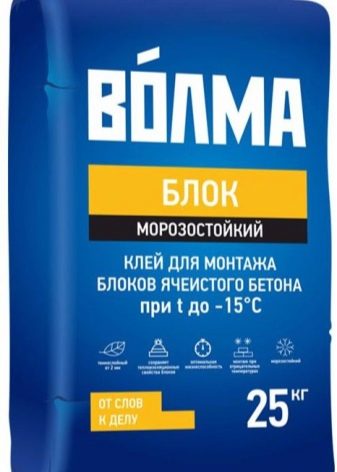
This glue is used by finishers when assembling slabs from aerated concrete blocks.
It is sold in 25 kg paper bags.
Titanium
When the glue-foam from the well-known brand "Titan" first appeared on the market, most professionals were skeptical about this new product. However, after the first applications, doubts about the quality and exceptional consumer indicators of the composition completely disappeared.
Titan products replace cement mortars, are very easy to use - you just need to apply a strip of composition to the blocks and fix them. At the same time, construction is progressing quite quickly, and the finished structure is durable and stable.
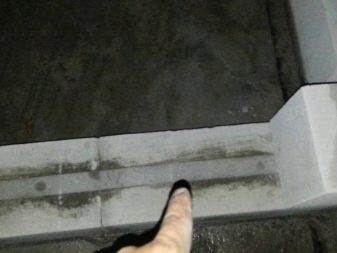
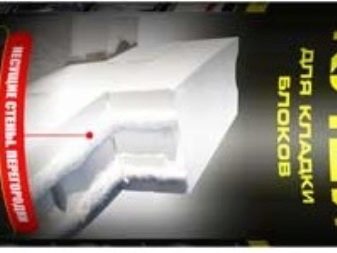
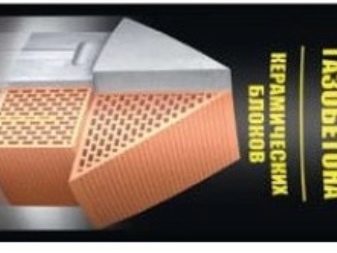
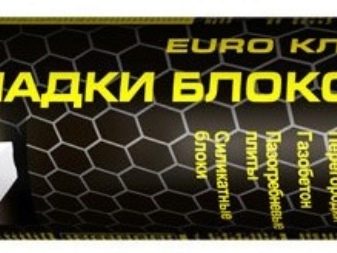
When applying foam glue, it is worth adhering to several rules:
- the surface of the foam blocks should only be flat;
- the layer of glue is applied in accordance with the instructions, do not exceed the thickness recommended by the manufacturer;
- the foam shrinks under the influence of direct ultraviolet rays, therefore, the joints should be sealed outside with cement;
- glue foam is used only for the second layer of foam blocks. The first one should be applied to a cement-sand mortar, otherwise, under heavy weight, the glue will quickly deform.
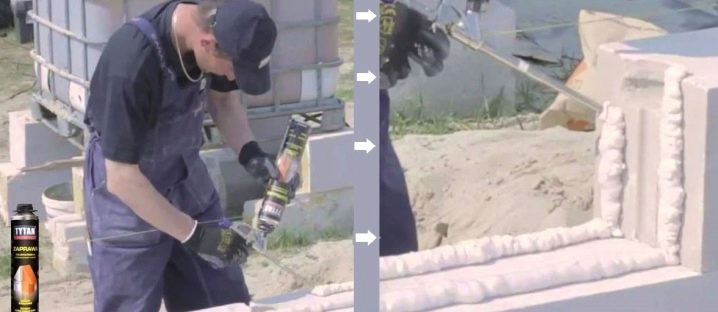
Available in 750 ml cylinders.
Knauf
Knauf Perlfix glue provides a high level of adhesion thanks to a plaster base and special polymer additives.
The use of glue does not require preliminary installation of the frame, the work is carried out quickly, and the structure is stable.
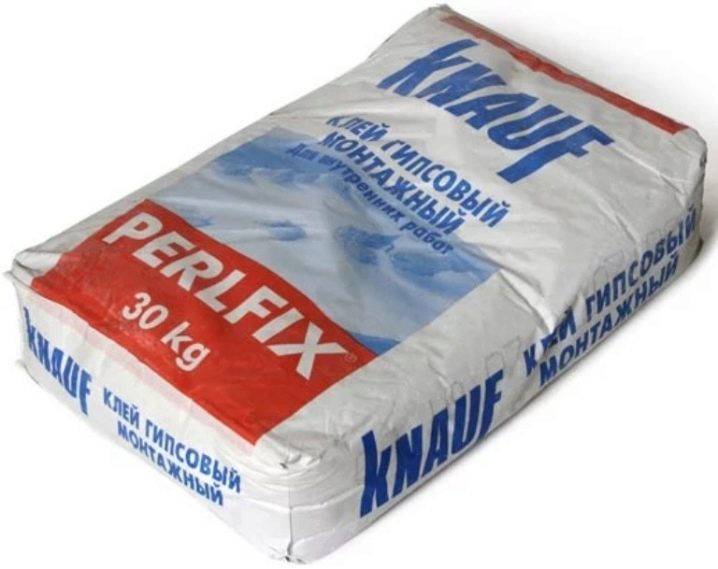
The undoubted advantage of the composition is its environmental safety, therefore it is widely used in private housing construction.
The glue is quite economically consumed - for processing a coating of 1 sq. m. only 5 kg of composition will be required.
It is sold in kraft bags with packaging of 30 kg.
IVSIL Block
The glue of this manufacturer has been widely used when laying aerated concrete and aerated concrete blocks. The mixture is a dry powdery composition based on cement with a small content of additives that increase the adhesion of the surface.
It is used for joints from 2 mm, with this glue consumption will be in the range of 3 kg per m2.
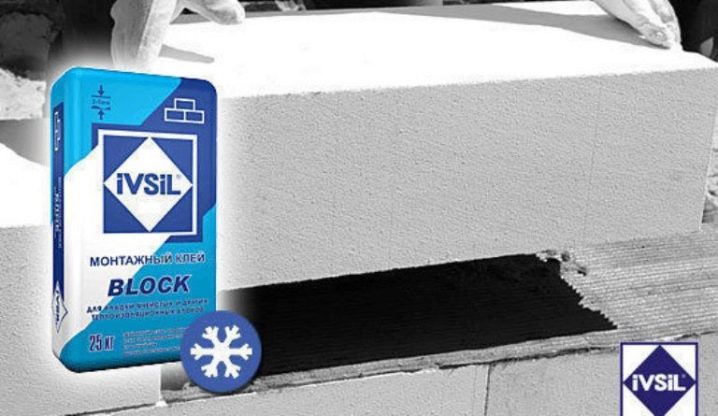
When using glue, the position of the foam blocks can be adjusted within 15 minutes from the moment of fixation.
It is sold in bags of 25 kg.
Osnovit Selform T112
It is a frost-resistant compound intended for use in winter. The formed joints easily withstand up to 75 freeze-thaw cycles - this figure is one of the highest among the winter types of foam concrete glue.
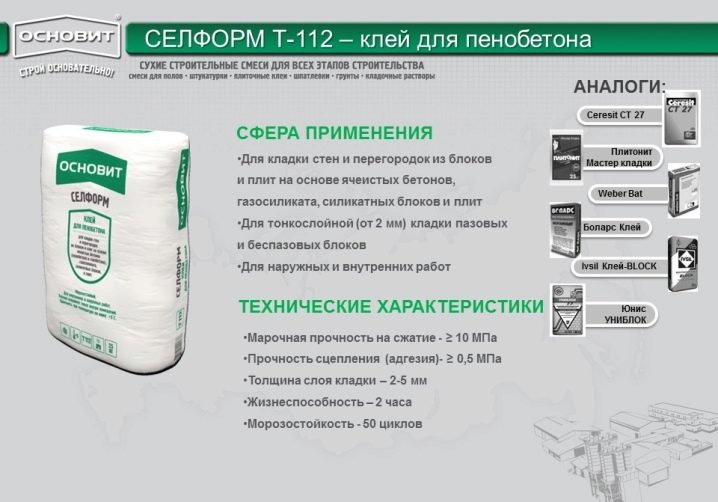
The adhesive mixture is characterized by a fine filler fraction, due to which it is used to obtain thin joints from 1 mm. This leads to a decrease in the total consumption of the composition - only 1.6 kg of dry glue is required for pasting 1 m2 of foam blocks.
The advantage of the glue is its fast adhesion. - the composition hardens after 2 hours, so that construction work can be carried out quite quickly.
It is sold in bags of 20 kg.
Among Russian manufacturers, the Rusean brand is also distinguished as having high quality and cost-effective products.
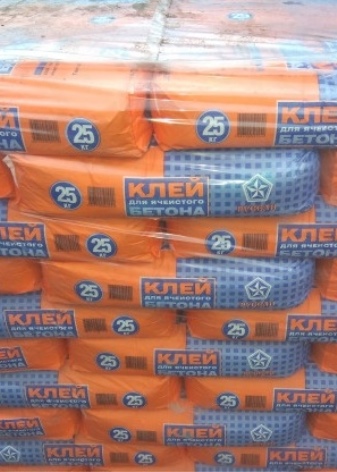
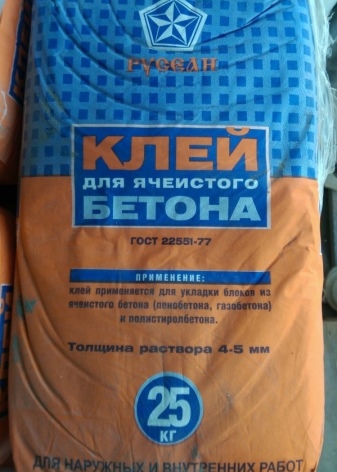
Application Tips
Experienced finishers and builders, who have been installing concrete slabs and panels for many years, recommend a very competent approach to the choice of glue. If you could not find a special glue on sale, then the most common tile composition, necessarily frost-resistant, will do just fine.
There are some general guidelines.
- it makes sense to buy glue only with the correct geometry of the foam blocks - in height they should not deviate more than 1.5 mm;
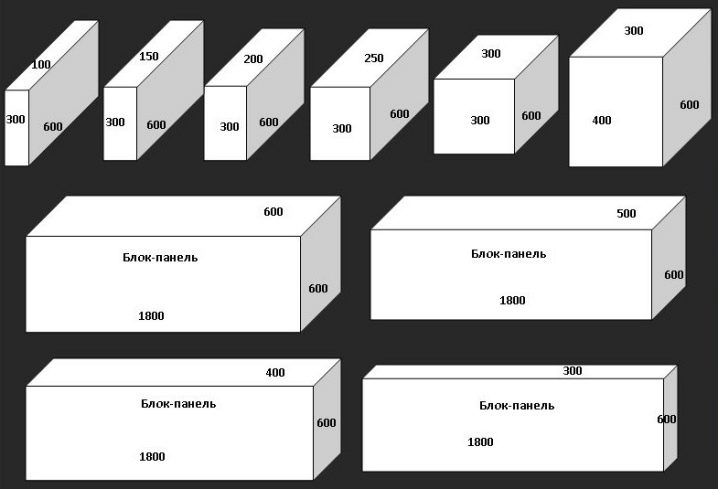
- glue is optimal in cases where the foam block is not more than 100 mm;
- it is better to entrust all the work to professionals - otherwise you can not only "transfer" the glue in vain, but also create a building of weak stability and durability.
It is very important to carry out work taking into account atmospheric conditions. Everything is simple here - at subzero temperatures it is necessary to use a special frost-resistant glue. Naturally, it is bred at room temperature about 20-24 degrees, and diluted with hot water (50-60 degrees). Please note that in the cold, the drying time of the glue is shorter than in the summer heat, so all work must be carried out as quickly as possible.
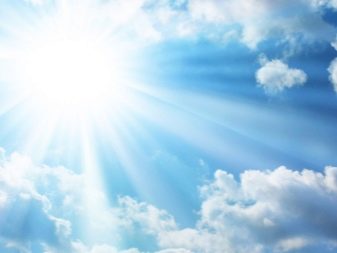
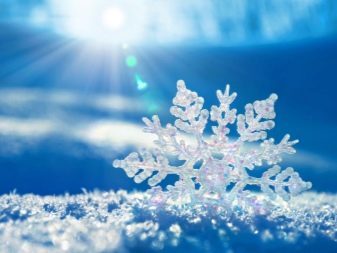
However, if such activity is a novelty for you, it is better to wait for the onset of warmth, then you can safely start building masonry from foam blocks with your own hands.
The way of laying foam blocks on glue is clearly demonstrated in the video.
The comment was sent successfully.