Features of glue for tongue-and-groove plates
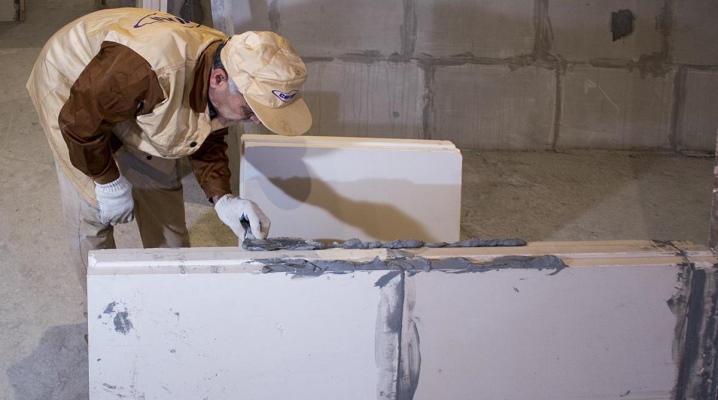
Glue for tongue-and-groove plates is a special composition designed for joining partitions, creating a monolithic seam without gaps and other defects. Compositions for GWP of different brands are presented on the market - Volma, Knauf and other specialized mixtures that have a high hardening rate and other indicators necessary to form a strong assembly joint. It is worth talking in more detail about what consumption of gypsum glue is necessary for a tongue-groove, how to use and prepare it.
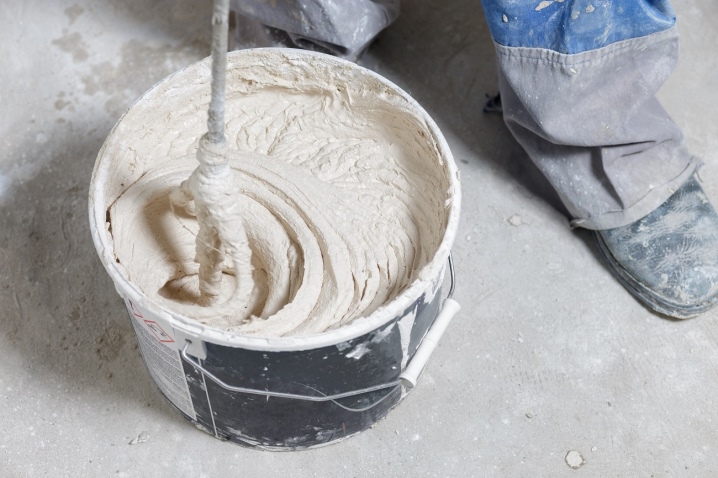
What it is?
Tongue blocks are a popular type of building board used for the construction of internal partitions in buildings and structures. Depending on the operating conditions, ordinary or moisture-resistant elements are used, butt-connected, with the combination of a protruding edge and a recess. Glue for tongue-and-groove slabs produced on a gypsum basis has a structure similar to them, therefore, it ensures the creation of a monolithic assembly connection.
Most formulations for GWP are dry mixes. In addition, on sale there is a glue-foam for a tongue-and-groove, with which you can connect structures indoors.
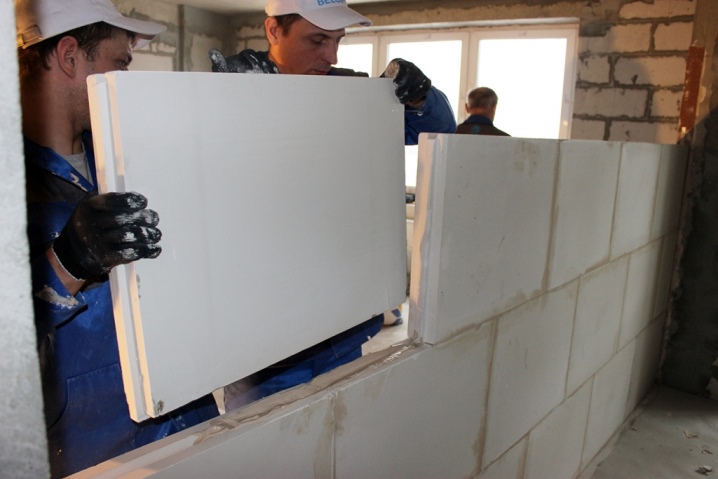
Almost all mixtures for GWP are also suitable for working with drywall. The use is allowed for frameless installation, for leveling, improving the soundproofing characteristics of the surface of the main wall, partition. It is necessary to glue tongue-and-groove plates on a gypsum and silicate base with different mixtures. The former are most often mounted with gypsum-based compositions, the latter with polyurethane foam adhesives, which give a quick connection that is resistant to moisture, fungus, and mold.
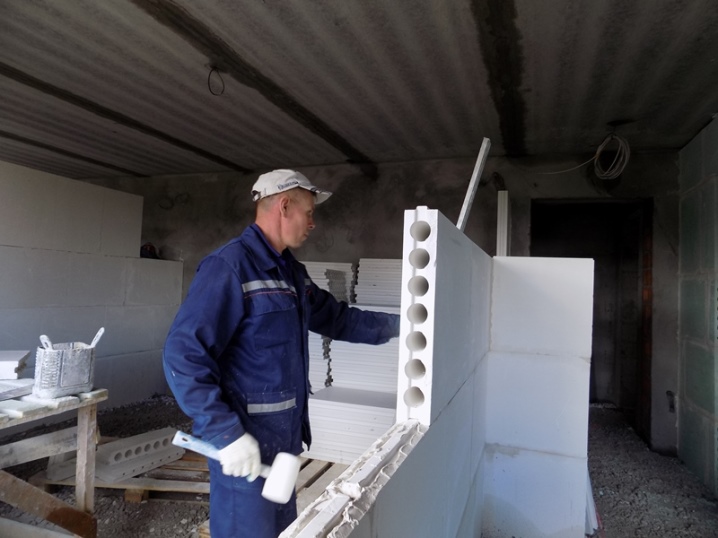
Distinctive features of mixtures for fixing tongue-and-groove plates can be called high adhesion characteristics. Binders do not just cover the material, but penetrate into its structure, making the split seam inseparable, providing it with strength. Such an internal wall turns out to be soundproof, reliable, and is built quickly. The average speed of hardening of liquid mixtures is only 3 hours, until the complete formation of the monolith takes twice as long. The master has only 30 minutes to position the blocks - he has to work quickly enough.
In fact, the GWP glue replaces the usual masonry mortar, making it possible to securely fix the blocks to each other. Most of the gypsum mixtures are with the addition of plasticizers, polymer binders, which improve the characteristics of the base substance. Sale is carried out in bags of 1 kg, 5 kg, 15 kg and in larger packaging.
The composition is also suitable for filling walls made of gypsum plasterboard, tongue and groove for painting, which is why small packages are in demand.
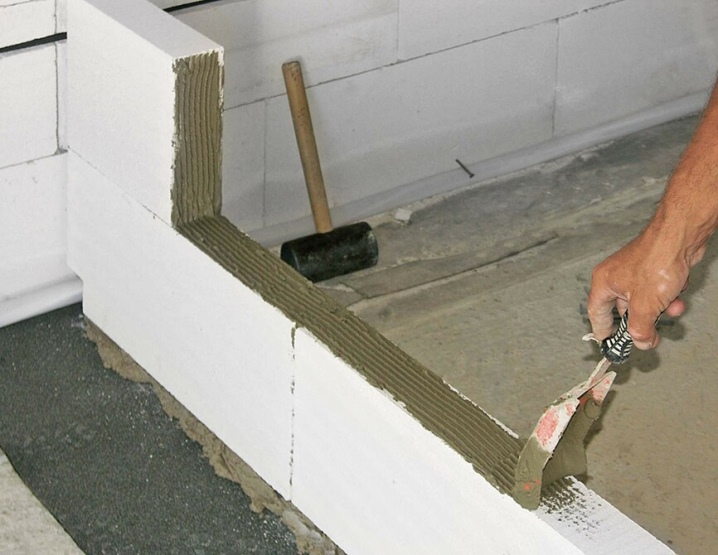
Advantages and disadvantages
Adhesive for tongue-and-groove plates has its own characteristics that make it the optimal solution for use in the installation of lightweight blocks. Gypsum formulations have their own advantages.
- Ease of preparation. Mixing glue is no more difficult than ordinary tile.
- Fast setting. On average, after 30 minutes, the seam already hardens, holds the material well.
- The presence of frost-resistant components. Special formulations can withstand a drop in atmospheric temperatures down to -15 degrees, and are suitable for unheated rooms.
- Non-flammability. The gypsum base is fire-resistant and safe to use.
- Resistance to external influences. After hardening, the monolith is able to withstand shock loads, does not crack under the influence of temperature extremes.
- Moisture resistance. Most mixtures after hardening are not afraid of contact with water.
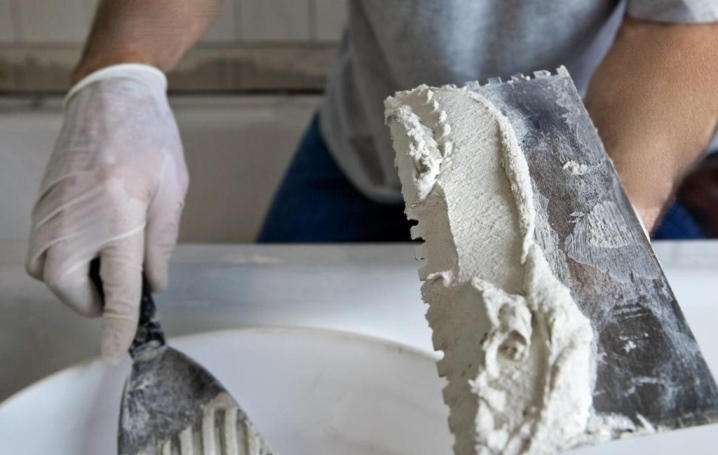
There are also disadvantages. You need to be able to work with adhesives in the form of dry mixtures. Failure to comply with the proportions, violation of technology leads to the fact that the connection is weak, destroyed during operation. In addition, this type of work is rather dirty, splashes can fly, the tool has to be washed. Fast hardening requires high speed of work, precise positioning of blocks, preparation of a mixture in small portions.
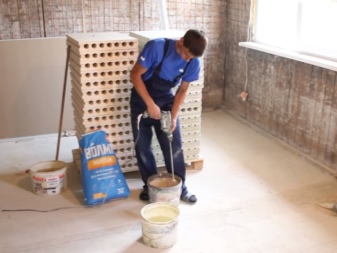
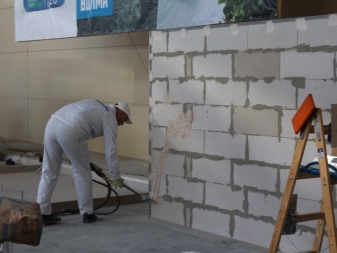
Adhesives for silicate GWP, produced in the form of polyurethane foam in a cylinder, also have their pros and cons. Their advantages include:
- high speed of construction of structures - up to 40% time savings;
- adhesive strength;
- frost resistance;
- moisture resistance;
- preventing the development of fungus and mold;
- low thermal conductivity;
- seam tightness;
- full readiness for use;
- ease of use;
- relative cleanliness of work.
There are also disadvantages. Glue-foam in a balloon is not very economical, it is more expensive than classical gypsum compositions. The correction time is no more than 3 minutes, which requires fast and accurate positioning of elements.
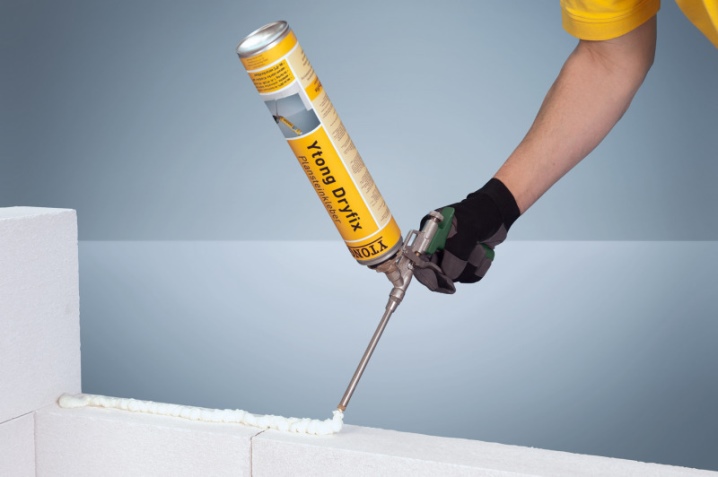
Brand overview
Among the manufacturers producing adhesives for tongue-and-groove plates, there are both well-known Russian brands and large foreign companies. In the classic version, the formulations are supplied in bags, it is better to store them in a dry place, avoiding direct contact with a humid environment. Package sizes may vary. For novice craftsmen, 5 kg bags can be recommended - for preparing a single portion of the solution.
Volma
Gypsum dry glue for installation of Russian-made GWP. It differs in a democratic price and availability - it is quite easy to find it on sale. The mixture is produced in the usual and frost-resistant version, withstands a drop in atmospheric temperatures down to -15 degrees, even when laying. Suitable for horizontal and vertical slabs.
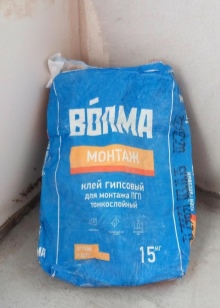
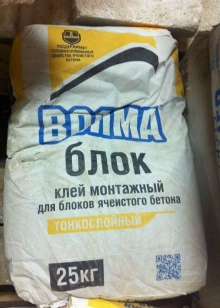
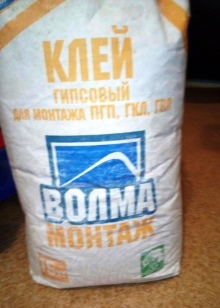
Knauf
A German company known for the high quality of its building mixtures. Knauf Fugenfuller is considered a putty compound, but can be used for laying thin partitions and non-stressed structures. Has good adhesion.
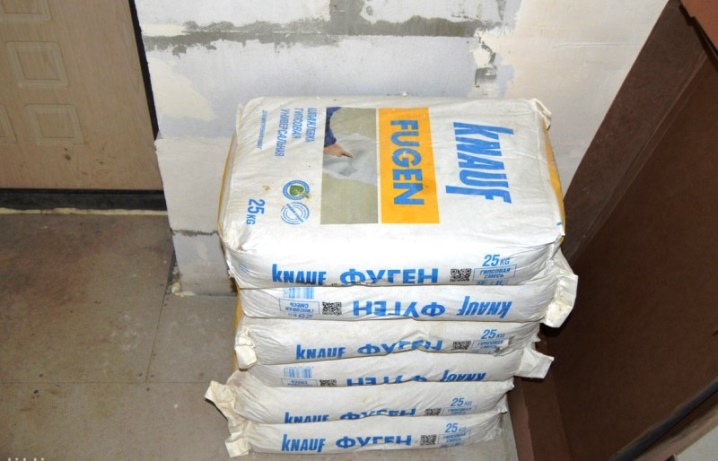
Knauf Perlfix is another adhesive from a German brand. It is focused specifically on working with building gypsum boards. Differs in high bond strength, good adhesion to the material.
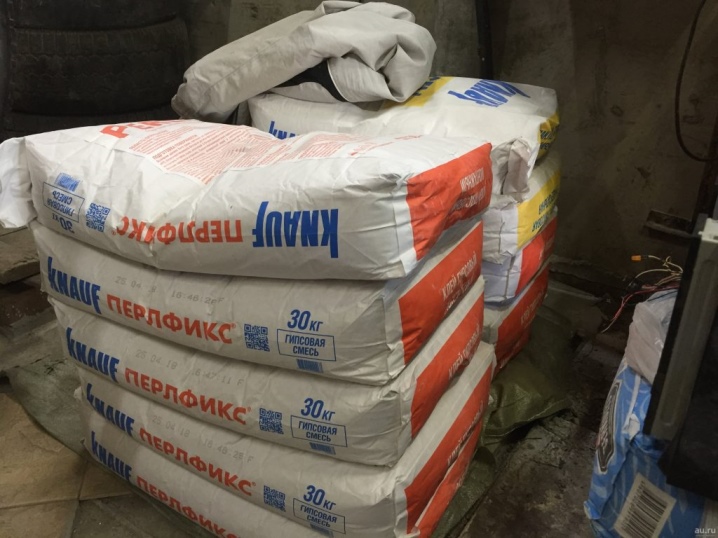
Bolars
The company produces a special glue "Gipsokontakt" for GWP. The mixture has a cement-sand base, polymer additives. Produced in bags of 20 kg, economical in consumption. The adhesive is intended for indoor use outside of a humid environment.
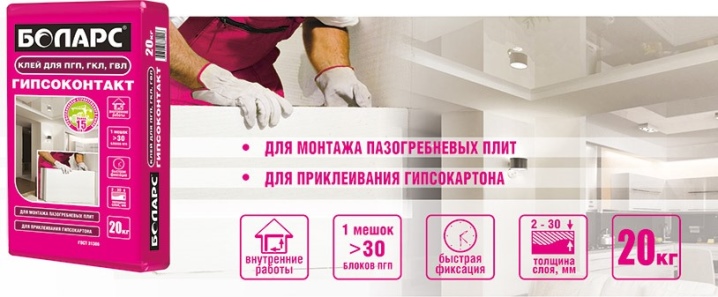
IVSIL
The company produces compositions in the Cel gips series, designed specifically for the installation of GWP and drywall. The product is quite popular, has a gypsum-sand base, good adhesion rates, and quickly hardens. Cracking prevents the addition of polymer additives to the composition.
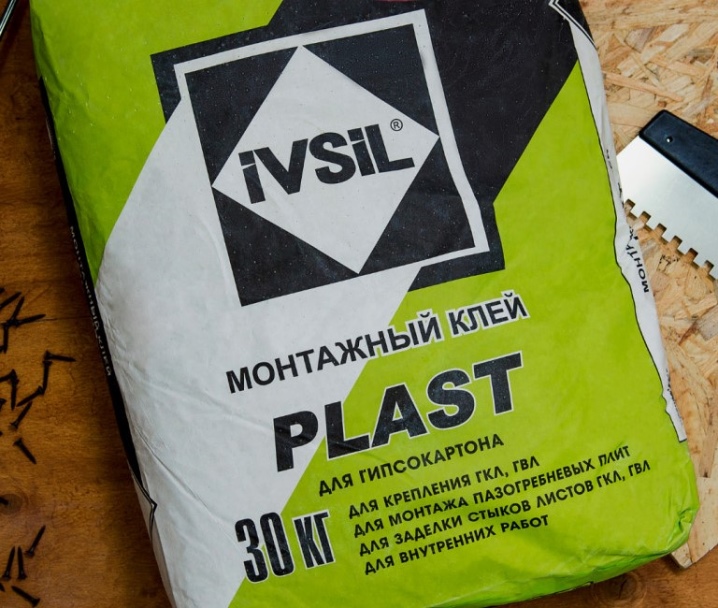
Foam glue
Among the brands producing foam adhesives there are leaders. First of all, this is ILLBRUCK, which produces PU 700 compound on a polyurethane basis. Foam holds together not only gypsum and silicate boards, but is also used when joining and fixing bricks and natural stone. Hardening occurs in 10 minutes, after which the glue line remains reliable protection against any external threats, including acids, solvents, contact with a wet environment. 1 cylinder replaces a 25 kg bag of dry glue; with a seam thickness of 25 mm, it provides coverage up to 40 running meters.
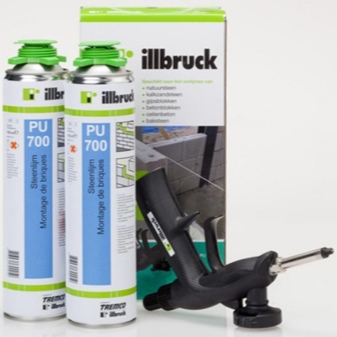
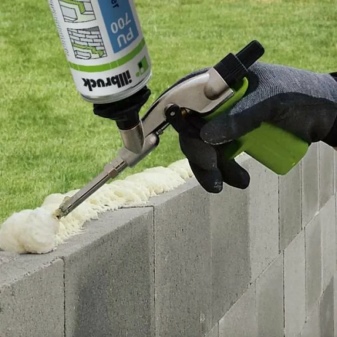
Also noteworthy is Titan with its Professional EURO foam adhesive, which is optimal for working with silicate GWP. The Russian brand Kudo produces a composition with similar characteristics to Kudo Proff. Among the universal foam adhesives, the Estonian PENOSIL with its StoneFix 827 product is also of interest.The connection acquires strength in 30 minutes; you can work with both gypsum and silicate boards.
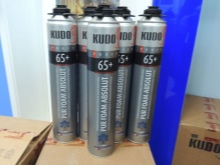
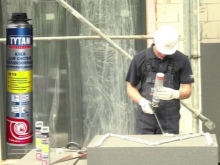
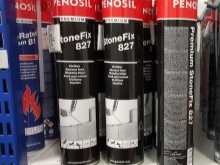
Usage
Average consumption of glue-foam for silicate and gypsum boards: for products up to 130 mm wide - 1 strip, for larger-sized 2 strips for each joint. When working, you should follow some recommendations.
- The surface is carefully prepared, cleaned of dust.
- The can is shaken for 30 seconds, placed in a glue gun.
- 1 row of blocks is placed on a classic mortar.
- Foam is applied from the 2nd row. The balloon is held upside down, the nozzle of the gun during application should be 1 cm from the surface of the GWP. The optimum jet thickness is 20-25 mm.
- When applied horizontally, the strips are not made longer than 2 m.
- The leveling of the slabs is carried out within 2 minutes, the position adjustment is possible no more than 5 mm. With a greater curvature, installation is recommended to be repeated, as well as when the elements are torn off at the joints.
- After a break of more than 15 minutes, the gun nozzle is cleaned.
Installation is recommended in heated rooms or in warm dry weather.
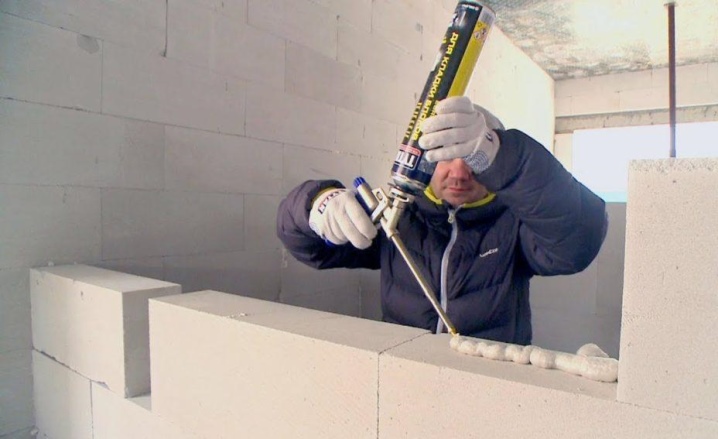
Working with dry mixes
When installing PPG on ordinary glue, proper cleaning of the surface and its preparation for installation are of great importance. The base should be as flat as possible, without significant differences - up to 2 mm per 1 m of length. If these characteristics are exceeded, an additional screed is recommended. The finished base is removed from dust, impregnated with primers and primers with a high level of adhesion. After drying of these compounds, you can glue damping tapes made of silicone, cork, rubber - they must be present along the entire contour of the abutment, to reduce the effect of thermal expansion and shrinkage of the house.
A dry mixture for tongue-and-groove slabs is prepared in the form of a solution immediately before installation, taking into account the proportions recommended by the manufacturer, - usually there is 0.5 liters of water per kilogram of dry matter. The average consumption for a partition of 35 slabs up to 5 cm thick is about 20 kg (2 kg per 1 m2). The composition is applied in a layer of 2 mm.
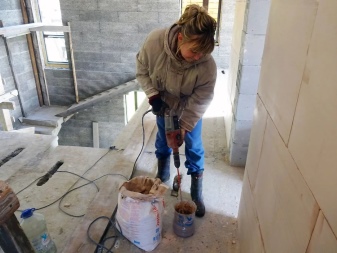
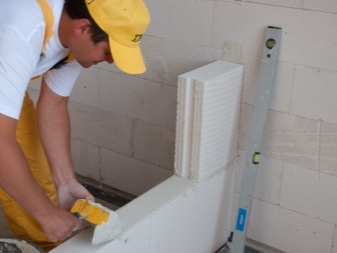
It is necessary to prepare the solution in a clean container, using cold or warm water, depending on the air temperature, let it brew for about 30 minutes. It is important that it be homogeneous, without lumps and other inclusions, ensure uniform distribution over the surface, and be sufficiently thick. Apply it with a trowel or spatula, spreading it over the contact surface as evenly as possible. About 30 minutes remain for positioning. You can increase the planting density of the slabs using a mallet.
During installation, the surface of the floor and walls in the area of contact with the GWP is marked out, covered with a layer of glue. Installation is carried out strictly with the groove down. The position is corrected with mallets. From the 2nd plate, installation is carried out in a checkerboard pattern, horizontally and vertically. The joint is strongly pressed.
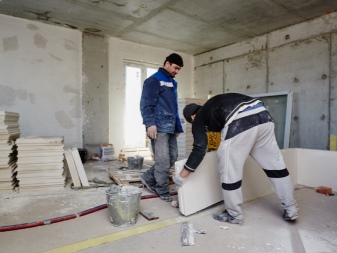
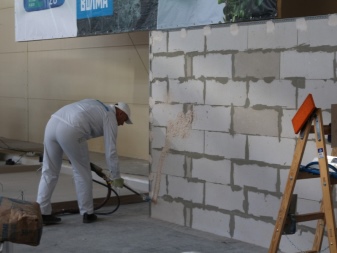
For information on how to use assembly adhesive for tongue-and-groove plates, see the following video.
The comment was sent successfully.