Choosing an adhesive for gas silicate blocks
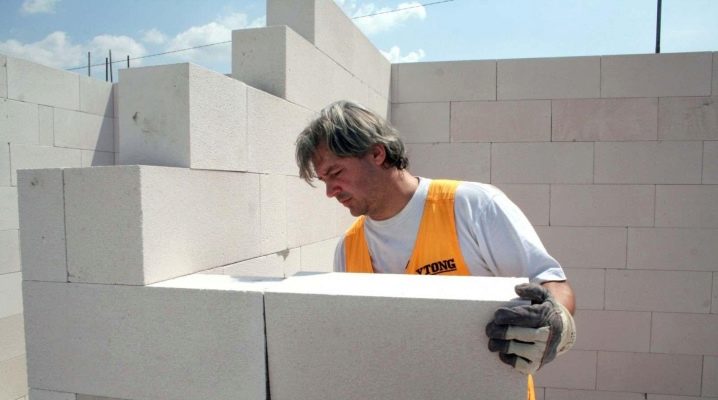
Modern methods of building private houses delight in their diversity. Earlier, thinking about building their own housing, people knew for sure: we take a brick, we select everything else along the way. Today, the situation has changed somewhat, the interest of newly-made developers has shifted towards porous gas silicate blocks. This material is good because it has an almost perfectly flat surface, has good thermal insulation properties, is convenient and easy to install. Another indisputable advantage of it is the use of a special bonding composition, the features of which will be discussed further.
Peculiarities
The glue used for the construction of housing from gas silicate blocks is a versatile mixture of elements that allow the porous building material to be bonded together as simply and quickly as possible.
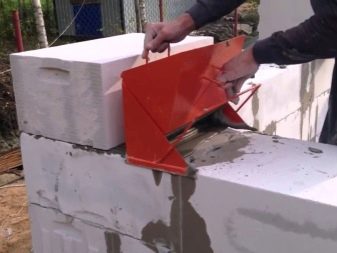
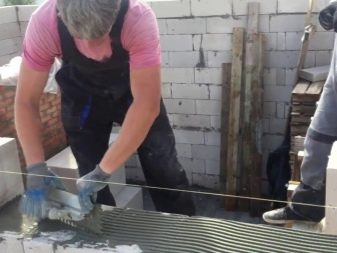
The main features of this glue are its main advantages over the classic cement mortar:
- Low thermal conductivity. This is due to the absence of voids in the seams and the so-called "cold bridges".
- A high percentage of adhesion to any surface. The glue is universal for any blocks: classic and ceramic bricks, foam and aerated concrete and others.
- Economical consumption. Due to the minimum thickness of the layer for setting (no more than 7 mm), the consumption of glue is 6-8 times less than the consumption of cement mortar, which significantly affects the total cost of building materials.
- The versatility of this composition lies in the fact that it can also be used as a means for leveling the surface in the horizontal and vertical directions.
- Operational comfort. The main convenience of the glue for gas silicate blocks is that it is easy to mix, easy to apply, and within 15 minutes after application, the position of the block can be changed.
- The presence of mixtures for work in the cold season.
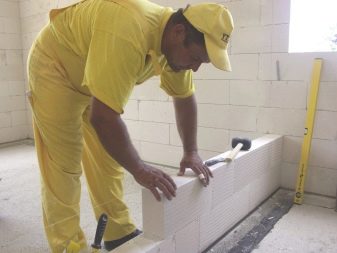
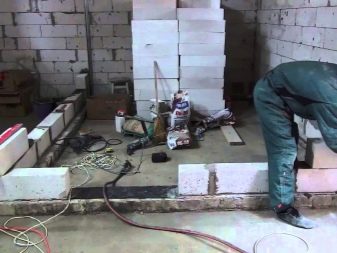
Of course, with so many advantages, it is very difficult not to look at the main disadvantages of the adhesive for porous surfaces. Among others, for example, the requirement for an almost perfect surface evenness is often indicated. And also the high cost of the bag - from 150 to 250 rubles per 25 kg. However, all these disadvantages are offset by the merits of the mixture.
Due to a wide variety of manufacturers and forms of production of glue for gas silicate blocks, you can choose the most suitable option for you.
Views
The production of glue is concentrated on two main groups: winter and summer versions. Since it may be necessary to build a house from gas silicate blocks on the territory of our country at any time of the year, this plus is very pleasing.
Frost-resistant glue should be used at a temperature not higher than +5 and not lower than -15 degrees Celsius... This guarantees maximum effect, without errors, shrinkage and cracks. So, for example, if the glue drying process took place at a temperature of 10-20 degrees, there is a risk of cracks in the seams and, as a result, deprivation of gas silicate of its main advantage - low thermal conductivity. This way, all the heat will escape through the walls.
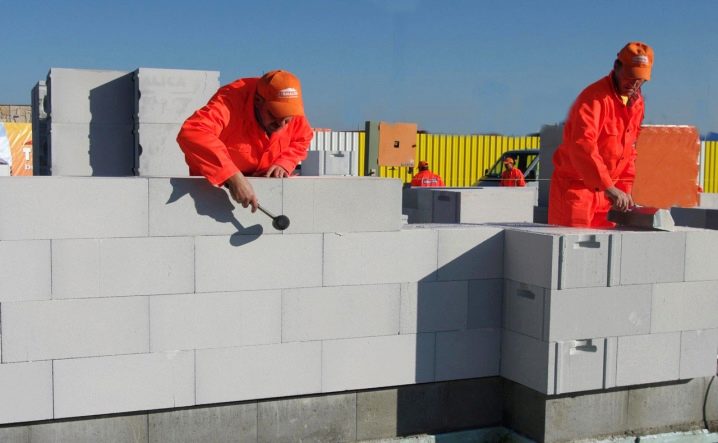
As a rule, aerated concrete and other porous blocks are not afraid of a sharp temperature drop. Here, the correct technology for applying the mortar that holds them together, the use of reinforcement to secure the structure as a whole, that is, the exact following the instructions described on the bag with the mixture, as well as the advice of professionals, plays the main role.
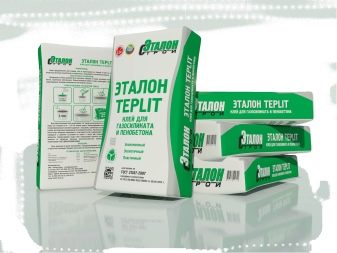
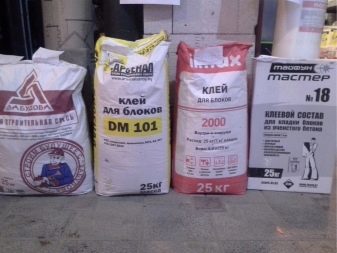
Another pleasant innovation in recent years is the release of glue for gas silicate blocks in foam format. As well as mounting, glue-foam is sold in cylinders, which require a special construction "gun". The only "but" in the use of this type of glue for porous structures is its unfinished approbation. There is no data yet on how long such a ready-made mixture can last and how well it is.
As you know, each sandpiper praises its swamp. The same is happening with the leading manufacturers of building mixtures. There are many of them and they are all very active in distributing their products, calling it the most-most. Let's try to figure it out.
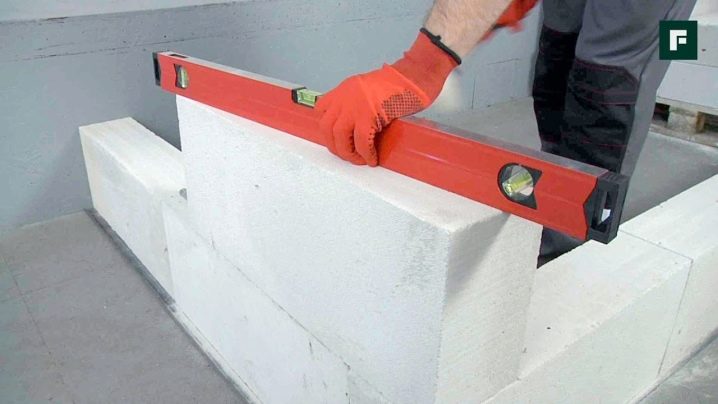
Manufacturers
The ideal option is to purchase gas silicate blocks and glue for them from one manufacturer. This immediately significantly increases the efficiency and durability of the future building. But some companies may be deliberately pricing higher on their mixes. Therefore, experienced professionals know from whom it is better to buy blocks, and from whom - glue. Let's figure it out "by name".
Aerostone - a mixture from the Dmitrovsky plant of aerated concrete products. Available in winter and summer versions. Cement-based product with the addition of water-retaining polymer additives.
"Zabudova". It is considered one of the best adhesives for working in cold weather for a low price - about 120 rubles per bag. It is easy to mix and apply even at -15, does not shrink, does not lend itself to the influence of the environment and atmospheric phenomena.
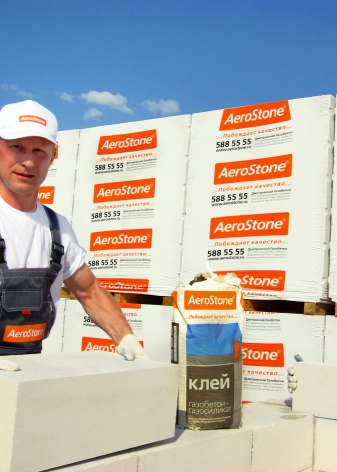
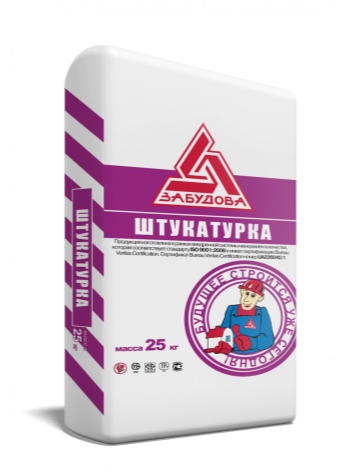
"Prestige" convenient for use not only with gas silicate blocks, but also with other porous plates. It takes a minimum of time to make an adhesive mixture.
Bonolit Nogin company "Bonolit - building solutions". This glue is absolutely environmentally friendly and safe. Does not have toxic artificial impurities. It can be used both for laying blocks outside and for internal work.
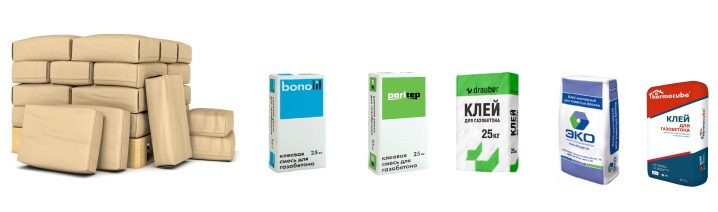
Unic uniblock - one of the most popular manufacturers of glue and gas silicate blocks. The main advantages of this particular mixture are a full set of characteristics that make it possible to make the most efficient, functional and durable building:
- high thermal insulation properties;
- resistant to moisture and temperature extremes;
- excellent plasticity allows you to change the position of the block within 20-25 minutes after installation;
- environmental friendliness;
- middle price category.
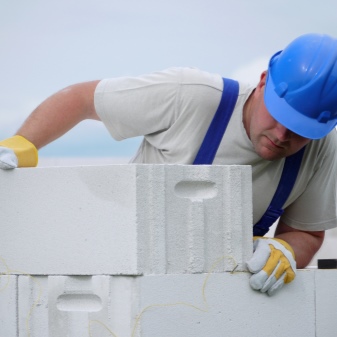
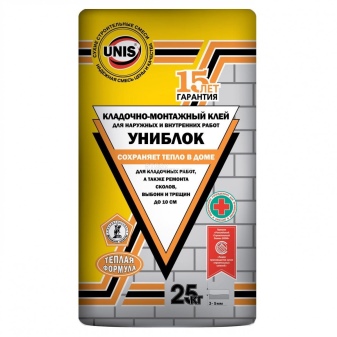
Aeroc produced by the enterprise for the production of aerated concrete "Aerok SPb" in the city of St. Petersburg. The high strength of the finished material and the unique thin layer (up to 3 mm) bring this glue to the leading positions in the building materials market in Russia.
"Win" - multicomponent mixture based on cement, quartz sand and additional polymer inclusions. The composition of this glue almost completely repeats the composition of the main gas silicate blocks on the Russian market today. It is this quality that allows it to adhere to the surface as accurately and quickly as possible, forming a unique monolithic structure that is not afraid of moisture, frost and heat.
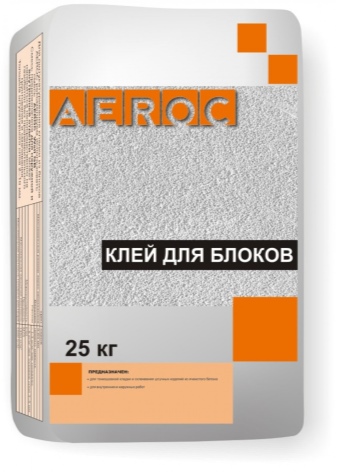
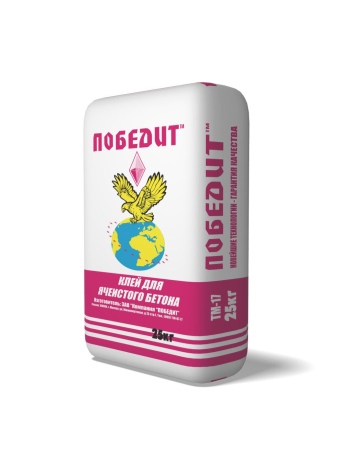
These are the main well-known manufacturers of adhesives for gas silicate blocks, which have confirmed their title of the best years of use. This list does not include mixtures similar in properties: Thermocube (Kostroma), Poritep (Ryazan), Eco (Yaroslavl), which are less popular, but are in no way inferior to their more famous “colleagues”.
Choosing a good mixture is easy. Based on the experience of professionals, your own needs and flair, you can get an excellent result for little money, but of excellent quality. The main thing is to comply with all the necessary requirements and technology.
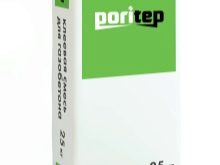
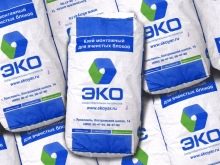
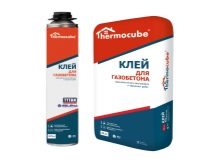
Advice
When choosing a particular brand of glue, you should be guided by the following criteria.
- Manufacturer's name. Very often there are insidious one-day firms that produce low-quality promotional materials that turn out to be fiction and do not bring the desired result, and sometimes harm the building. In order not to be mistaken and not to fall for the bait of scammers, it is better to trust well-known and proven brands, and also remember that a quality product cannot be cheap.
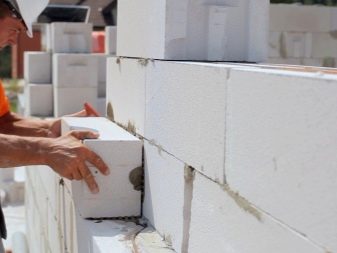
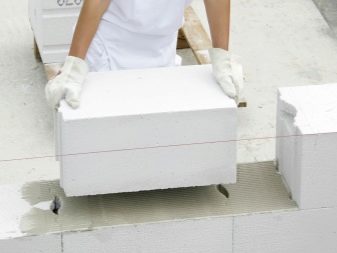
- Packaging and storage conditions. When choosing a product in a warehouse, immediately pay attention to how it is stored. High humidity in the room, a sharp change in temperature, damage to the packaging, a bag with blurry letters and a company logo - all these are clear witnesses of a poor-quality mixture. This material is as good, subject to the rules of its storage, as it is disgusting when at least one parameter does not correspond to reality.
- By weight. Never agree to purchase glue for gas silicate blocks without packaging. Nobody can give you a 100% guarantee that there are no substandard impurities.
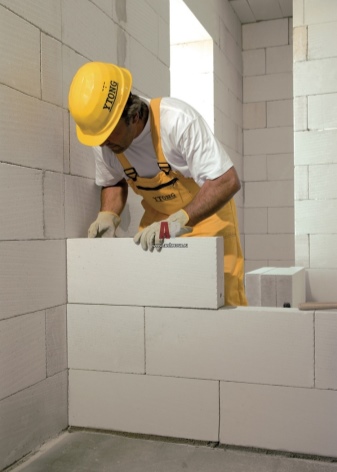
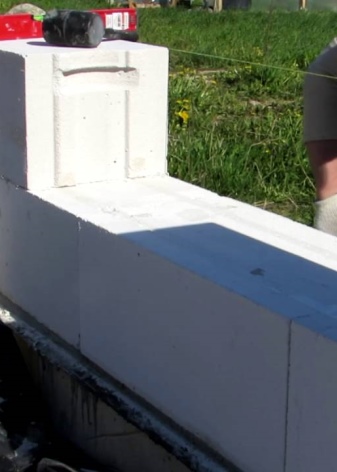
Having decided on the brand-manufacturer of glue for gas silicate blocks, you can start calculating the material consumption. Often, all companies indicate this value on the packaging of their products, however, this information is just a reference, therefore, for each individual case, it is necessary to calculate the consumption of glue per cube of blocks individually.
The main parameter on which the amount of solution consumption per 1 m3 depends is the thickness of the layer. If this indicator is no more than 3 mm, then the amount of glue will average from 8 to 9 kg per cubic meter. With a layer thickness of 3 mm or more, the consumption of the finished mixture increases 3 times and is 24-28 kg for the same surface area.
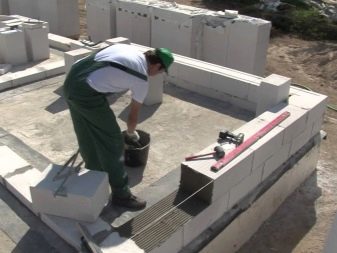
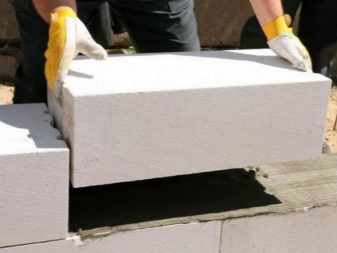
To somehow optimize the consumption of glue, you can resort to the following technological tricks.
- Surface preparation. One of the important criteria when laying gas silicate blocks using specialized glue is perfect evenness. The smoother the blocks, the less the consumption of the building mixture will be.
- Compliance with the technology of preparation of the solution. Just take and knead the glue for laying gas silicate blocks, like dough for pies, will not work. It also has its own system: firstly, the glue powder is poured directly into the water collected in a clean container (a plastic or galvanized bucket is ideal); secondly, stirring occurs in two stages, with a short break (5-7 minutes, no more); thirdly, you should not direct a large volume of the mixture at once, since you may not have time to use it all before the moment of solidification (for most manufacturers, this time is limited to 2 hours).
- Application methods also play an important role in reducing glue consumption. So, for example, the main tool for laying the mixture is a spatula with teeth. It is better to lay gas silicate blocks 10 minutes after applying the glue, pressing firmly and knocking on the surface with a rubber hammer.
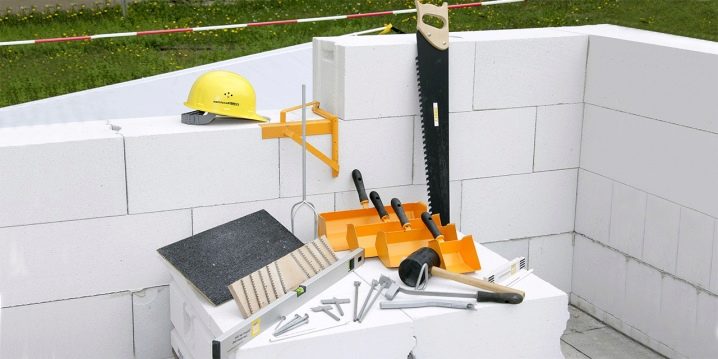
The first row of blocks is never glued. There is always a foundation under the initial "line" of the entire structure: concrete screed, screw piles, and so on. So the whole building will be much more stable and durable.
These are the main tricks that must be used in work in order to minimize the consumption of glue for gas silicate structures without compromising quality.
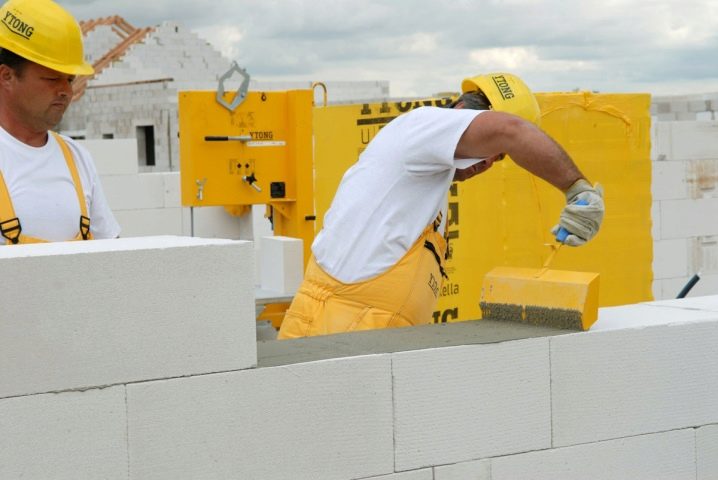
In order to position the blocks as accurately as possible, and between them - layers of glue, it is necessary to use mixtures designed for a specific individual case: for indoor or outdoor work, for laying gas silicate blocks at high or low temperatures.
It is also necessary to remember that the minimum period of glue hardening in a block or panel structure is 24 hours. But the best and final result is observed not earlier than the third day after installation.
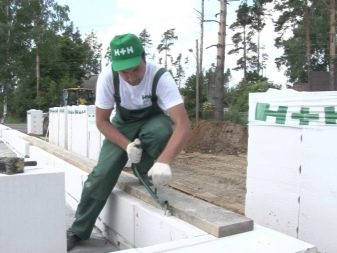
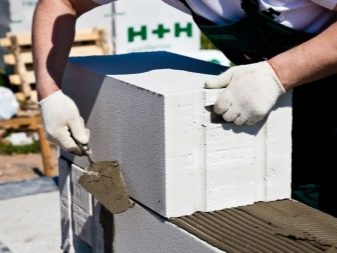
Compliance with the main indicators of temperature and humidity allows the construction of a gas silicate structure using special glue quickly, easily and efficiently, even for a novice builder who does not have additional skills or education. Of course, it is very important to enlist the support of professional bricklayers and experienced builders in this difficult matter, so that later you can only rejoice and enjoy the positive result of your own efforts.
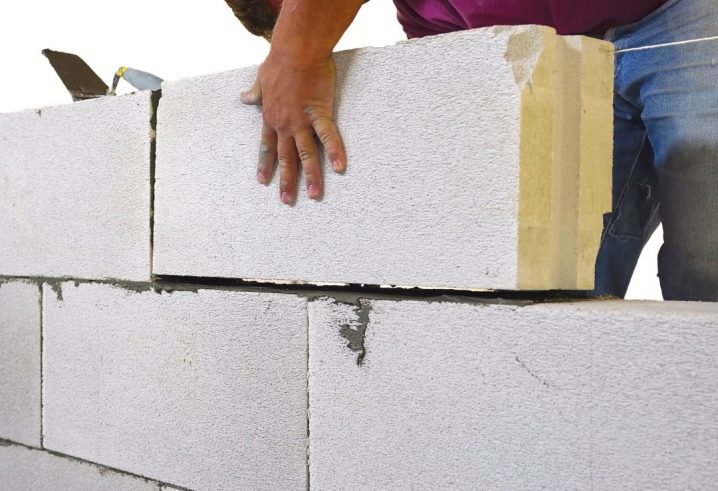
For information on how to choose an adhesive for gas silicate blocks, see the next video.
The comment was sent successfully.