Polyurethane foam: features and scope
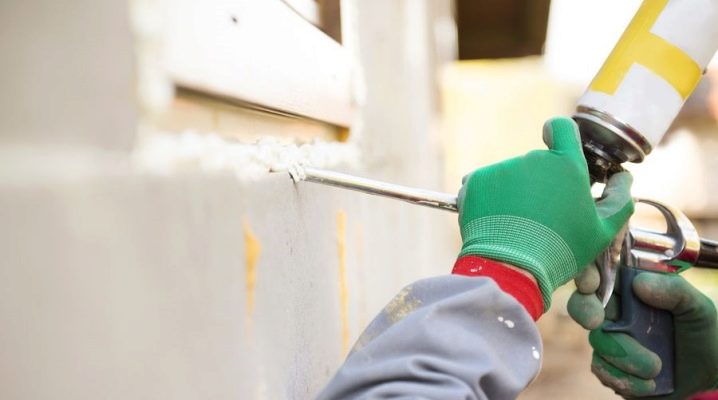
Fire safety is one of the main indicators of the quality of buildings. To achieve the required parameters that meet all regulatory documents, non-combustible materials are used. Mounting fire-resistant foam serves as an excellent fire insulator, as it can become a reliable protection of the premises from the penetration of poisonous gases and asphyxiant smoke.
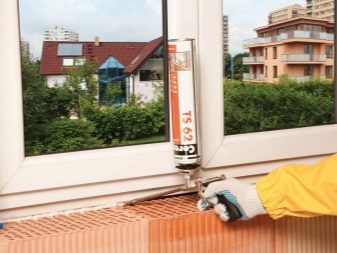
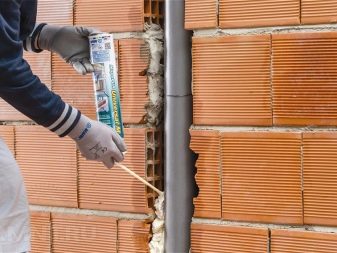
Peculiarities
Fire resistant foam is a relatively new material. When applied to vertical surfaces, the sealant does not run down under its own weight. It penetrates perfectly into cavities, filling them up to 100%. Refractory polyurethane foam adheres tightly to all types of surfaces: glass and polymers, wood and cement, brick and metal, natural stone and cement blocks.
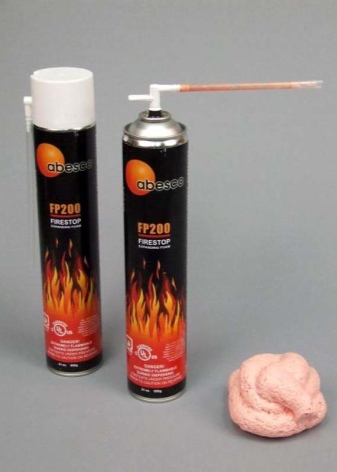
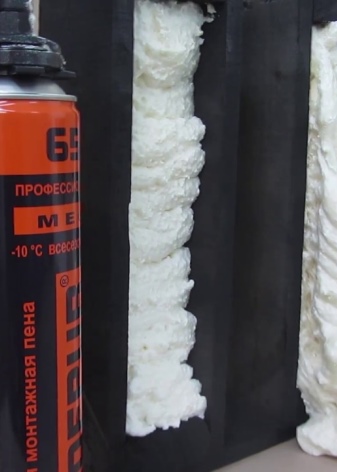
After insertion into cavities, grooves or cracks, the volume of the sealant increases, and upon completion of the solidification process, the mass acquires rigidity. A similar property is used to fix in a certain position various frames, boxes, door and window blocks. Building elements, enclosed in a tight sealant ring, do not change their position in any direction. The foam space does not allow gas and moisture to pass through. In addition, the sealant serves as an excellent sound insulator.
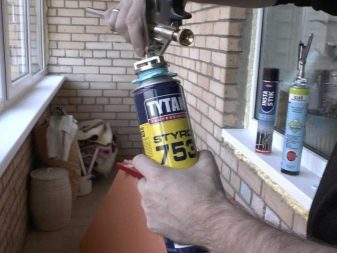
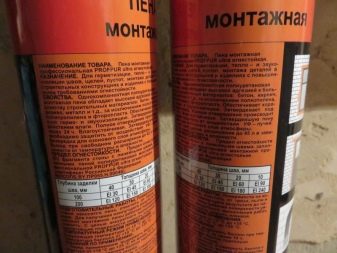
When considering the characteristics in detail, the following points are highlighted:
- Preservation of useful properties after final polymerization in a wide temperature range (from -60 to +100 degrees).
- Complete inertness to moisture. Neither fungus nor mold takes root on the cured fire retardant substance.
- Increased strength in relation to other polyurethane foams.
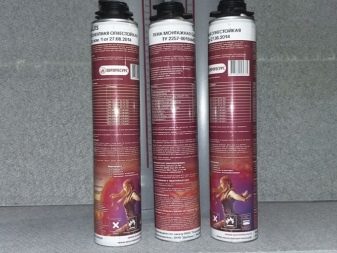
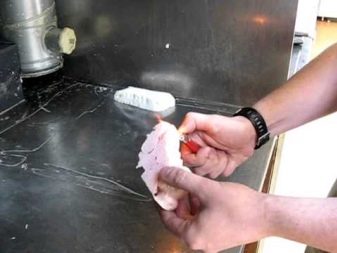
The main advantage of this type of sealant is its resistance to fire. After prolonged exposure to open fire, the foam will still ignite. The time until the moment of fire is indicated on the packaging. Different manufacturers have different periods, for example, Soudal brand foam will start burning after 360 minutes. In addition, the material does not flow when heated, does not fall in drops, and if it does catch fire, then after the cessation of exposure to open fire, it extinguishes on its own.
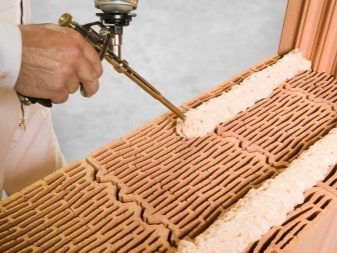
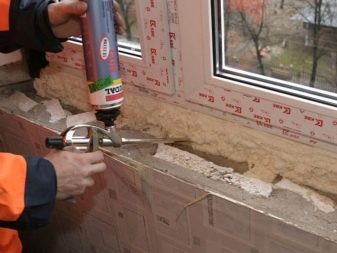
The disadvantage of this material is the inability to resist the sun's rays - ultraviolet light has a destructive effect on open assembly seams. To ensure the reliability of the foam, the seams must be protected, therefore they are often treated with putty or cement mortar, less often they are painted.

Views
Firestop foam is widely used. Its unique properties allow it to be used in various types of construction. Heat-resistant foam is required when equipping baths and saunas, various stoves, boilers, fireplaces and other heating devices, that is, wherever there is significant heating or an open fire is present.
Refractory foam is highlighted in color - it is either red or pink. The color will tell you what type the polyurethane mixture is, which will avoid confusion with applying a less resistant mass to where a fire retardant option is required.
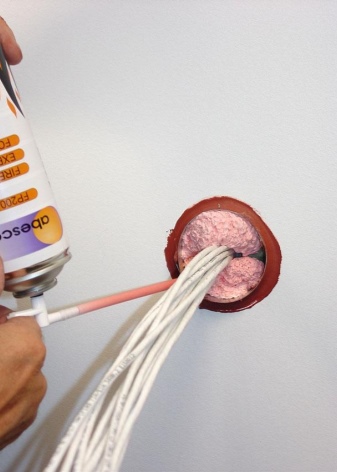
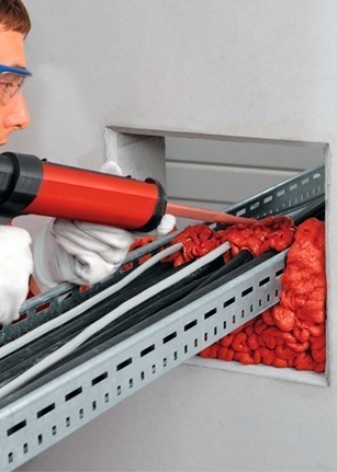
Not all fire resistant foam is created equal - it is divided into several types.
By the time of use, heat-resistant foam can be all-season and winter. The first one can be used in summer and with frosts not lower than -10 degrees. Winter foam can also be applied at lower temperatures. The lower temperature limit for this type of fire resistant sealant is indicated on the packaging. Sometimes it reaches -18 degrees.
It should be borne in mind that in the cold, the foam loses volume: the colder the air, the less the volume of the sealant.
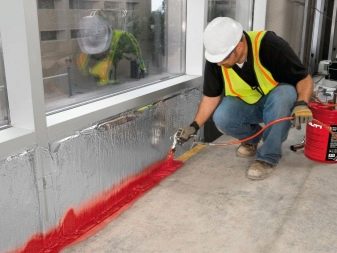

The composition of the foam is divided into the following categories.
- One-component. The composition hardens under normal humidity conditions. Manufacturers recommend spraying treated surfaces with water to improve adhesion.
- Two-component. It contains reagents that make the mixture harden. At negative temperatures, only two-component mixtures can work.
According to the method of use, foam can be used for household and professional purposes.
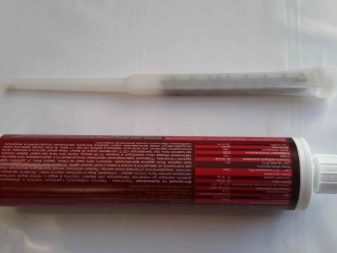
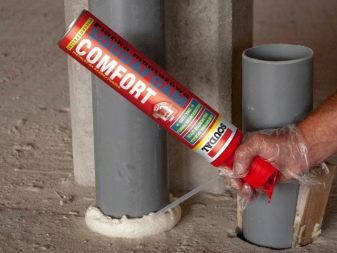
The household option is used in small quantities exclusively for small-scale local repairs. The substance leaves the container through the tube.
The professional mixture is squeezed out using a special pistol. Differs in increased strength and heat-resistant qualities.
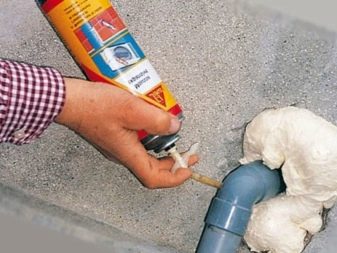
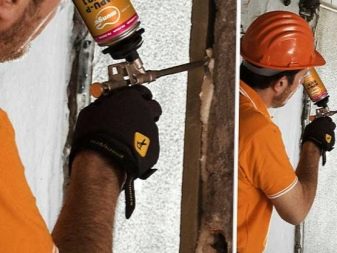
The material includes:
- Catalysts responsible for accelerating foam expansion. They are the ones that allow you to work in the cold winter time.
- Foaming agents that create foam, which determine the consumption of foam and the rate of setting.
- Gas, under the influence of which the thermally expanding polyurethane foam is pushed out of the tube.
- Stabilizers affecting the uniformity of foaming. The stabilizers work correctly if the can is shaken well before opening.
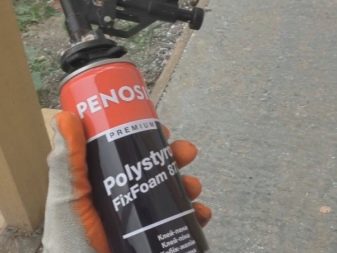
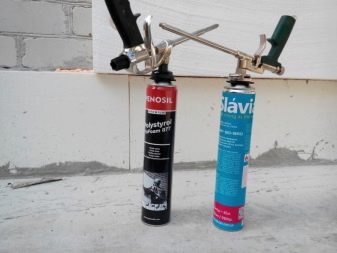
Polyurethane foams are divided into three classes of fire resistance. The most reliable material is assigned class B1. It is used in rooms with maximum human traffic.
Material with this marking has the following properties:
- resists open fire for a long time;
- does not support the combustion process;
- after removing the fire, it goes out by itself.
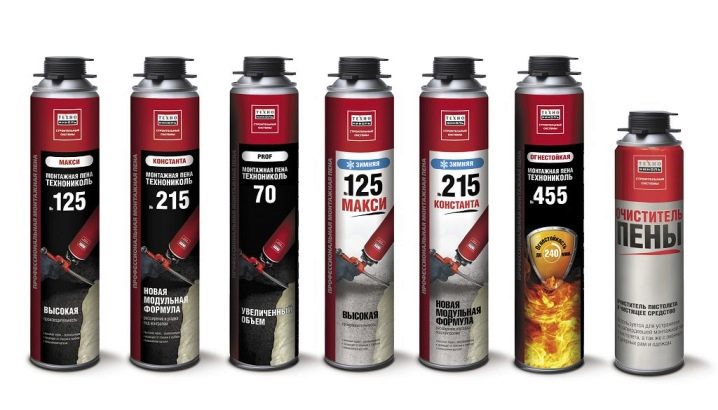
Less reliable foam of the second class - B2. It cannot withstand the "attack" of the fire element for a long time and begins to melt. In this case, an uncritical amount of toxins are released. It fades out on its own. Foam is appropriate in rooms with medium traffic.
Flammable sealant belongs to class B3. Its use is limited.
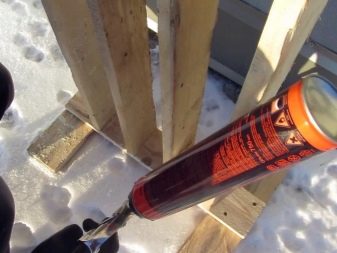
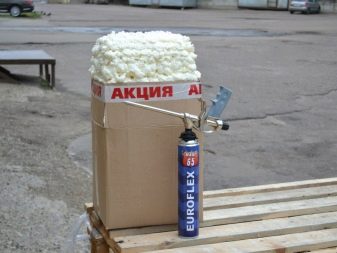
Consumption
Approximate material consumption per 1 sq. m is indicated on the sealant container. It is not worth taking the manufacturer's data as a panacea - the foam stock will never be superfluous. Not all foams will give the same results when applied to surfaces.
The flow rate varies depending on the following factors:
- components included in the mixture;
- the sizes of slots, grooves, recesses, that is, on the parameters of the space to be filled;
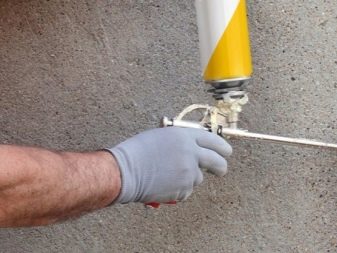

- method of applying the sealant (professional gun or special tube);
- presence or absence of foam handling skills;
- the presence of a dosing device;
- temperature and humidity in the working area.
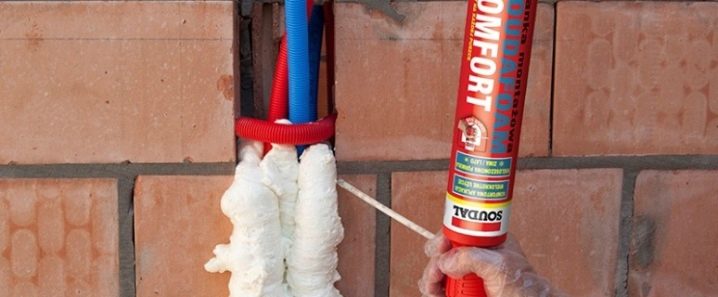
In construction organizations, when calculating the need for polyurethane foam, estimators proceed from the fact that work is carried out exclusively by qualified workers, professional pistols under normal climatic conditions.
The following circumstances are taken into account:
- obligatory moistening of the treated cavity;
- periodic shaking of the container;
- even application of the material from bottom to top.
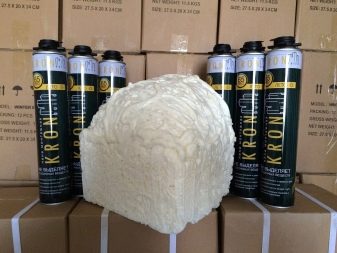
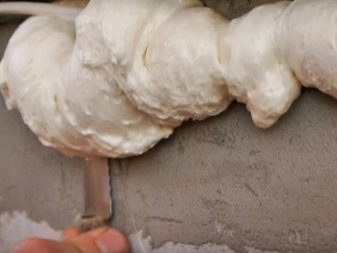
When determining the number of cylinders of sealant for treating a window frame, it is assumed that the thickness of the seam is about 35-40 mm. It is believed that for laying block insulation for 1 sq. m account for about 10 liters of foam. As a rule, builders lay a decent stock, referring to certain specific conditions.
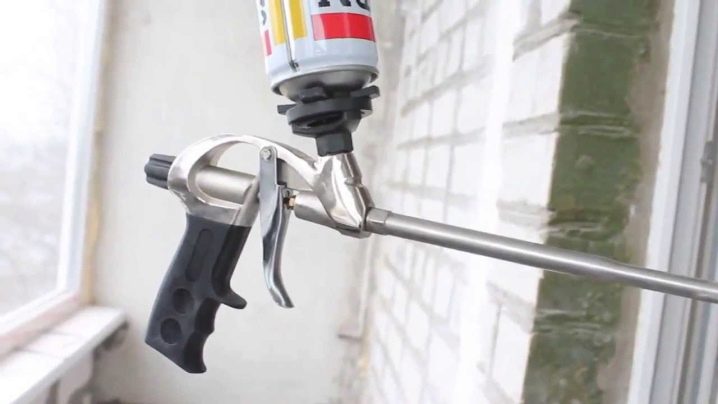
None of the instructions give an accurate determination of the consumption of sealant. All instructions are calculated approximately, averaged, adjusted to ideal parameters for all possible indicators. Therefore, the manufacturer's data can be taken as approximate test results. In each case, you need to remember that only a starting point is given, and the "extra" balloon will never be truly superfluous.
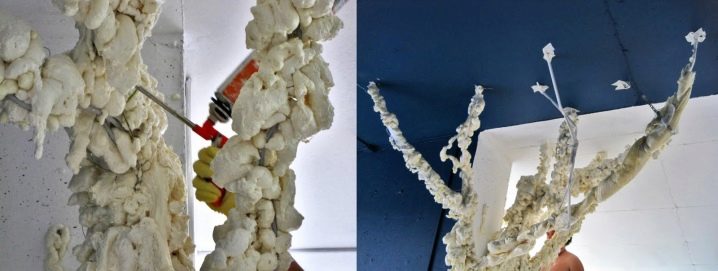
Parameters such as the depth and width of the joint to be treated have a significant influence on the consumption of the sealant.If the seam is uneven, and its width in places increases up to three times, then the foam consumption can increase several times. A decrease in consumption will follow with additional filling of the seam with other materials.
We must not forget about the expansion capacity of the foam itself. Strong, medium and weakly expanding species give results that are very different from each other. Some in the process of polymerization can increase fivefold, others - only three or only two times.
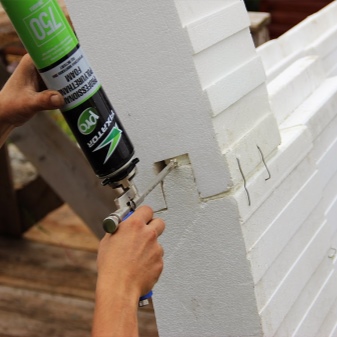
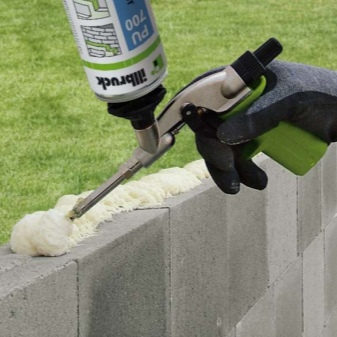
Expandability depends on foam producers. In some cases, even one package is enough to process a whole window, while in others, two cylinders are not enough.
Scope of application
The use of fire-resistant polyurethane foams is justified in places where standards require strict adherence to fire safety.
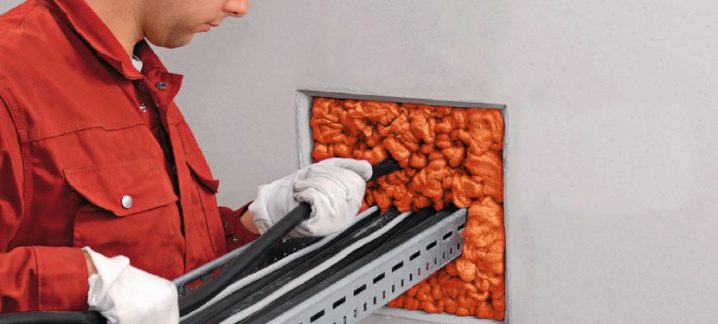
Seams, gaps, including blind ones, in fire partitions are filled with foam.
In order to impart smoke tightness and fire resistance to structures with foam:
- seal window and door frames;
- fill voids in walls and ceilings;
- Foam holes around electrical conductors, switches, plugs and sockets;
- used as a gap sealant when installing a chimney and dormer windows.
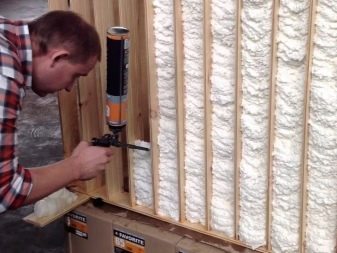
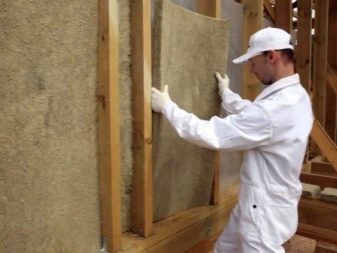
With its help insulating materials are glued. It absorbs noise and sounds, improves the quality of heat insulators in air conditioning systems, as well as in cooling networks. The fire-resistant mixture is used for cable penetrations, it is used to process the seams when installing furnaces and other heating equipment.
Regardless of what material the foam is applied to (concrete, brick or wood), the preferred joint width should be in the range of 3 to 10 cm. The optimum temperature of the treated surface for high-quality sealing of cracks and gaps is considered to be a positive temperature range of 5-30 degrees.
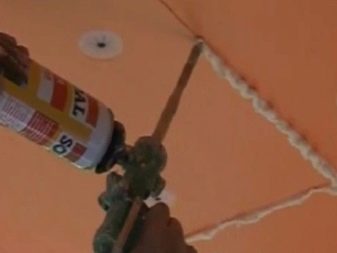
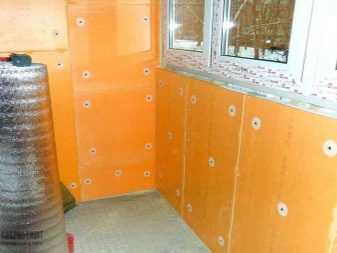
Persons who have started repairs on their own need to know that they cannot use foam until the cylinder and its contents have warmed up to +10 degrees. The sealant will perform the functions assigned to it if its temperature is established within 10-30 degrees.
If the foam was brought from the cold, then you need to keep it warm for some time. Forcing the cylinder to heat up will damage the mixture.
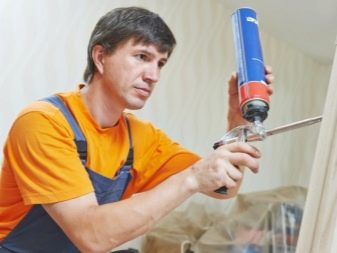
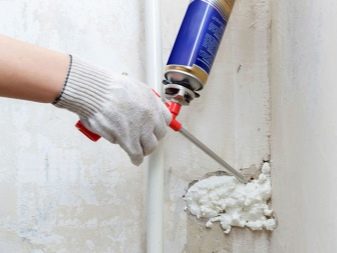
Manufacturers
The presence of a large number of manufacturers contributes to the appearance on the market of an abundance of polyurethane foams with different characteristics. For example, DF foam (article DF1201) is classified as combustible with a fire resistance of 150 minutes. It has a pink color, packed in a 0.740 liter can. At the exit, it forms about 25 liters of foam.
Unlike DF foam, CP 620. This material is thermally expanding, two-component. The foam output is 1.9 liters. It is used in hard-to-reach places and where it is necessary to create reliable insulation from smoke, steam and water. It is used for insulating cables.

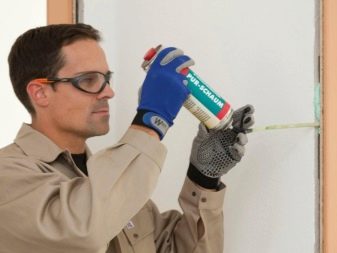
Nullifire - professional foam with a red tint, has the highest fire resistance class B1. The period from the moment of exposure to open fire to fire is 4 hours. Formed on modified polyurethane and non-combustible gas.
It is used for arranging chimneys, pipe and cable wiring, fire doors. It adheres perfectly to all surfaces. The mixture yield is about 42 liters.
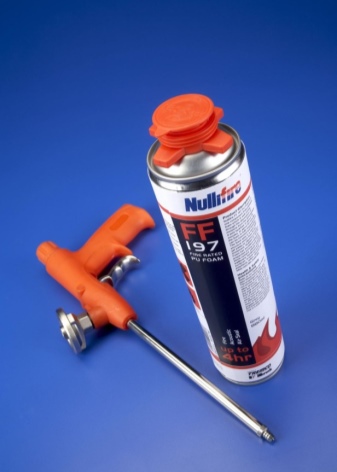
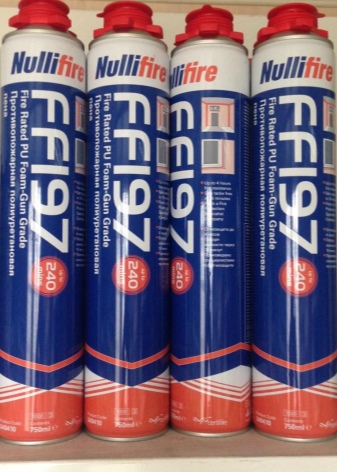
Two-component foam Hilti 660 applied in various cases. It is versatile, capable of protecting any penetrations from fire and smoke. Fire resistance is maintained for three hours. The thermally expanding mass is red and is supplied in 325 ml cartridges. The material yield is 2.1 liters.
Rush Firestop Flex 65 - moderately flammable foam, one-component. Differs in the uniformity of the mixture exit from the container, high heat-insulating properties of the seams.
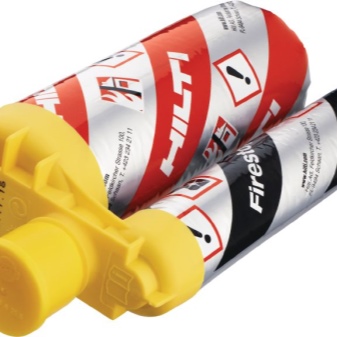
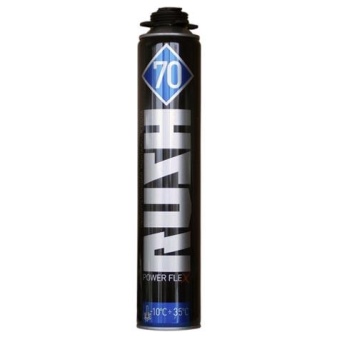
The scope of this composition is translucent structures. Used for sealing building structures. Low adhesion to fluoroplastic, polyethylene and propylene. High adhesion to brick, stone, concrete, wood.
Estonian foam Penosil brands designed for sealing and insulating joints of fire-resistant structures. The product is suitable for sealing tiled roofs. The material retains its tightness when heated for three hours. Recommended for installation of fireproof doors.
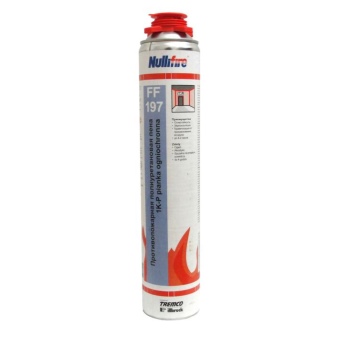

Nullifire FF197 - one-component mixture of B1 flammability class. It is used for insulation, sealing, filling and insulation of joints and seams of fire-hazardous structures. Suitable for surfaces made of plastics, including foam, cable sheaths, plastic. Perfectly adheres to stone, concrete, metal, brick, wood.
Profflex company - Russian manufacturer. The polyurethane foam of the same name is intended for both domestic and professional use. The material is all-season, can be applied at sub-zero temperatures (up to -15 degrees).
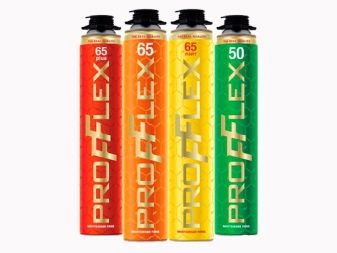
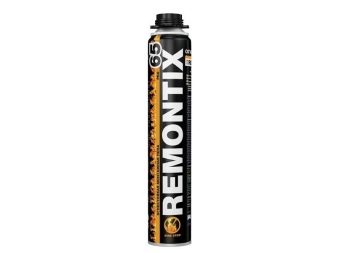
Remontix flame retardant material with a flammability limit of 240 minutes. It hardens in 10 minutes, completely polymerizes after application in a day. Requires processing, as it is afraid of ultraviolet radiation. Output at a temperature of +23 degrees can reach 65 liters.
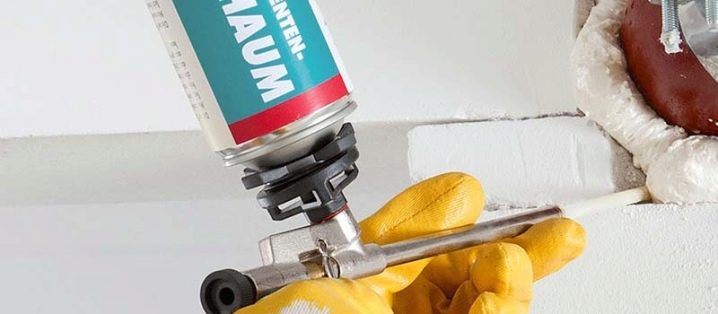
Advice
When choosing foam, preference should be given to well-known trusted manufacturers.
You need to pay attention to the cost of the goods and the volume of the container. The volume differs significantly from manufacturer to manufacturer, while the price may be the same.
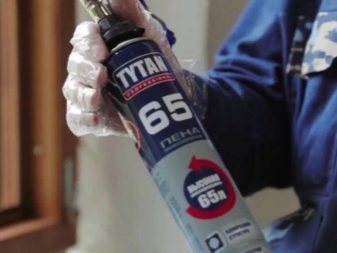
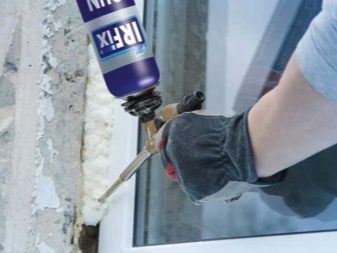
The better the foam, the longer it is able to withstand a fire. For the installation of fireplaces and stoves, it is worth purchasing foam of the flammability class B1. If foam is required for insulation of heating, water supply or sewer networks, you can limit yourself to the flammability of B2.
Work surfaces must be cleaned before applying foam. Adhesion will be better if the foaming spots are moistened with water. However, the presence of water droplets is unacceptable. Priming the surfaces will also help the sealant adhere better.
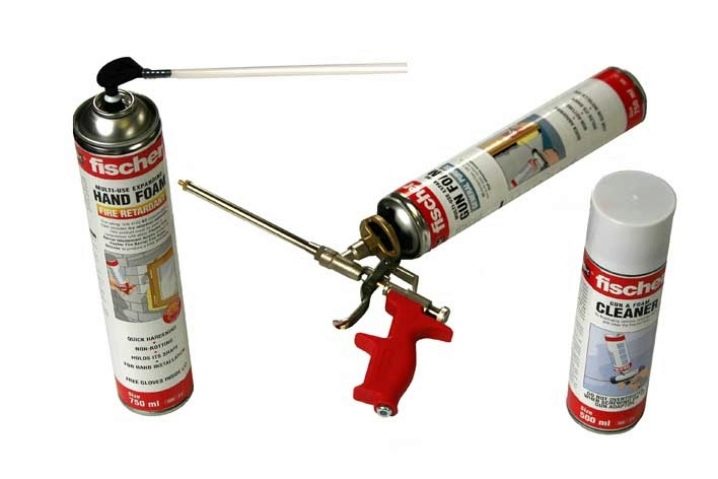
You need to store cylinders in an upright position, you also need to monitor the expiration date. Shake the package before use.
The first foam outlet is a trial one. When the supply of the mixture is leveled, you can start sealing, while the cylinder should be at an angle of 90 degrees to the surface to be treated. The groove needs to be filled one third, two thirds will be filled when the foam expands.
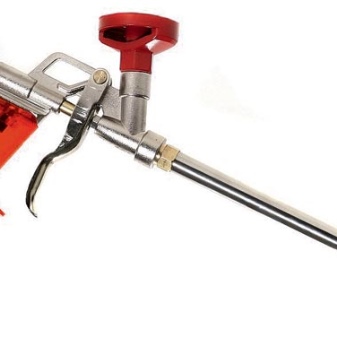
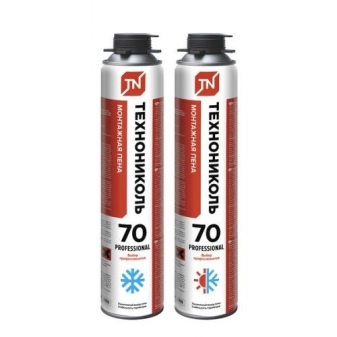
Using a professional pistol instead of a tube allows you to perform work efficiently, while the foam is fed into the grooves more evenly.
You should not engage in sealing in cold weather, if this is not absolutely necessary, because winter work is much more expensive. In warm weather, costs are reduced due to the fact that the foam expands much better at positive temperatures. The optimum temperature for work and foam is in the range from +20 to +23 degrees.
For information on the difference between ordinary polyurethane foam and fire-resistant, see the next video.
The comment was sent successfully.