All about mini tractor axles
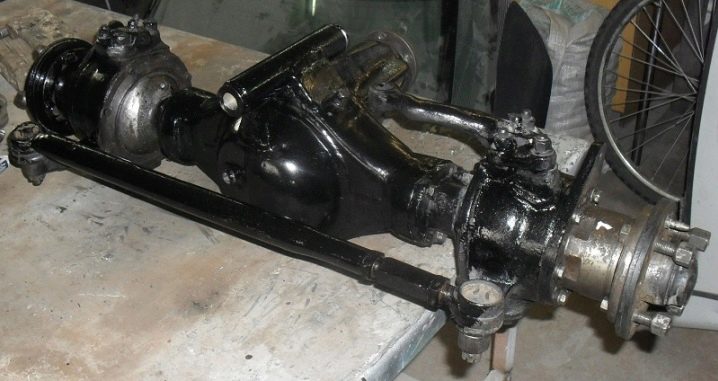
When making or modernizing your agricultural machinery yourself, you need to know all the intricacies of working with its bridges. A professional approach allows you to guarantee the elimination of all difficulties during work. Let's try to understand this topic deeper.
Peculiarities
The front beam on a mini-tractor is most often made from a hub and brake discs.
The work of this beam must be consistent with the action:
- pendants;
- lifting apparatus;
- steering column;
- hind wings;
- brake apparatus.
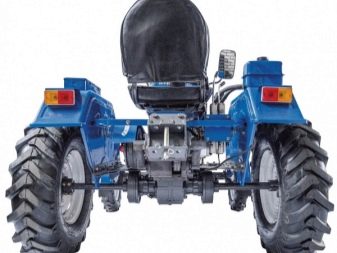
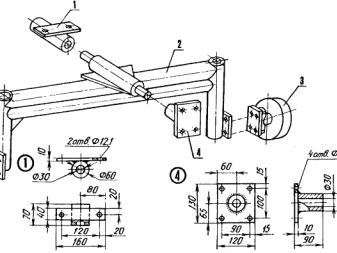
But much more often, instead of self-assembled beams, special bridges from VAZ cars are used.
The advantages of this solution are:
- almost inexhaustible possibilities to customize parts;
- a wide range of available models (you can put any Zhiguli rear axle);
- the choice of the type of undercarriage is entirely at the discretion of the farmer;
- simplification of the subsequent purchase of spare parts;
- cost savings compared to manufacturing from scratch;
- obtaining a reliable and stable machine, even in difficult conditions.
Important! In any case, drawings must be drawn up. Only having a diagram, it will be possible to determine the required dimensions of the parts and their geometry, to choose the correct methods of fixing.
As practice shows, mini-tractors made without drawing up drawings:
- unreliable;
- break down quickly;
- do not have the necessary stability (they can tip over even on a non-steep ascent or descent).
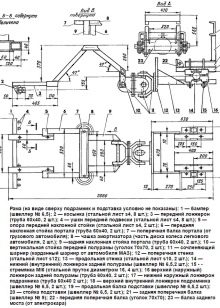
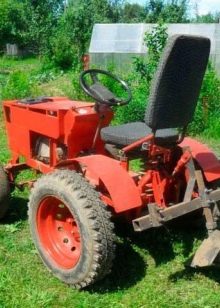
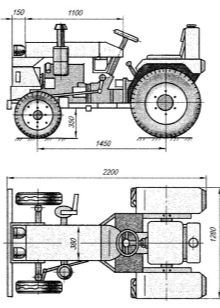
Each change affecting the chassis is necessarily reflected in the diagram. The need to shorten the bridge usually arises when the frame parameters change. This solution can significantly improve the consumer characteristics of the vehicle. Importantly, energy is additionally saved. It is also noted that shortening a standard bridge improves flotation, and the shorter the bridge, the smaller the turning radius becomes.
According to a similar scheme, you can make a bridge, even a leading one, for any mini-tractor. But if you use a beam, then you can refuse to install a gearbox. As a result, the design will be simplified and cheaper. After all, the Zhiguli beam already contains the required gear assembly by default. Crossbeams for miniature tractors are made using steel angles or square tube sections. When creating a driving axle, it must be remembered that it is with it that the motor and the pair of wheels are connected, and that the force generated by the engine is transmitted to them. In order for this bundle to work normally, an intermediate cardan block is provided. The quality of manufacturing of the drive axle depends on:
- cornering;
- stabilization of wheels;
- receiving by the frame of the mini-tractor, created by the driving wheels of the pushing force.
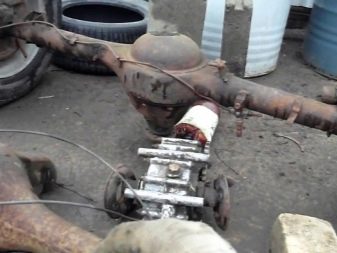
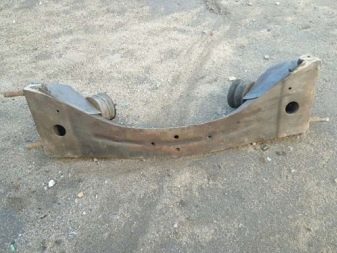
This design consists of a number of parts. Both the bolting and the sturdy crossbeam are just a few of them. Bushings of the main and pivot axles, wheel axle shafts, ball and roller bearings are also used. The corners and pieces of pipes will serve as the basis for the beam. And to make bushings, any structural steel part will do.
The slewing rings, however, are already made from profiled pipes. Sections of such a profile are being finalized with the expectation of installing bearings. Covers made of CT3 steel are useful for tight closure. The segment containing the roller bearings and the cage is welded to the center of the crossbeam.Special bolts will allow you to fix the bridge to the bushings of the same beam. It is very important that the bolts are more powerful, otherwise they will not hold the structure - therefore the backlash must be calculated carefully in advance.
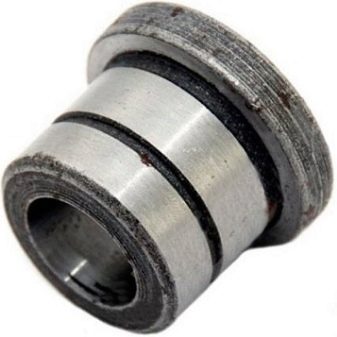
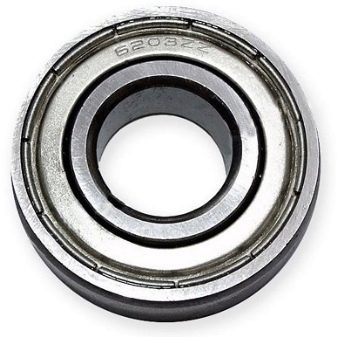
Shortening a part
This work begins by cutting off the spring cup. The end flange is removed. As soon as it is released, you need to measure the semiaxis by the value indicated in the drawing. The required part is sawn off with a grinder. It must be left alone for now - and proceed to the next step. The section is provided with a notch, along which a groove is then prepared. A passage is made in the inside of the cup. Next, the semiaxes are joined together. They must be welded strictly according to the applied markings. As soon as the welding is completed, the axle shaft is inserted into the bridge and welded to it, this procedure is repeated with the other axle shaft.
Once again, we emphasize that the thoroughness of measurements is very important. Some DIYers ignore her. As a result, the elements are shortened unevenly. After installing such bridges on a mini-tractor, it turns out to be poorly balanced and loses stability. Swivel fists and brake complex can be safely removed from the same VAZ car. The rear axles of mini-tractors must be protected from impacts.
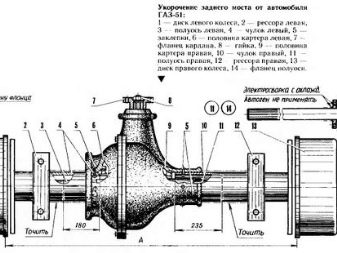
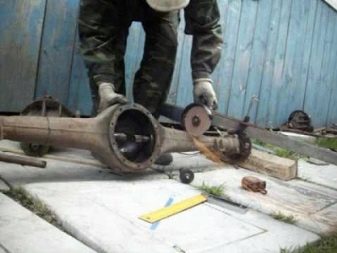
The protective element is most often a steel corner (support). It is laid out along the seams formed during welding. Judging by the operating experience, in the first 5-7 days after assembling the product, it is undesirable to conquer strong off-road conditions and conduct other risky experiments. Only after running in, you can safely use the mini-tractor as you like.
The correct operation of the mini-tractor after assembly is also of great importance. Axles can fail quickly if the oil is changed irregularly. It is advisable to use exactly the type of lubricant recommended by the gearbox manufacturer. Having made it yourself or shortening the bridge, you can use it not only in an independently assembled miniature tractor. Such a part is also useful as a replacement for deformed parts on serial devices.
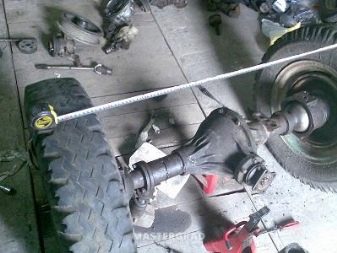
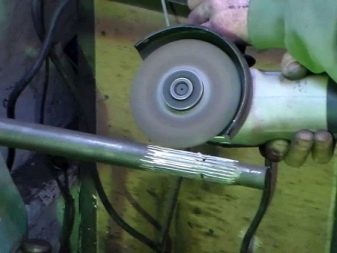
Working with other machines
In order to maximize the cross-country ability, preference is given to working parts not from VAZ, but from UAZ. Regardless of the specific model, the fewer changes are made to the suspension design, the more stable and reliable the mechanism will be. After all, amateurs-mechanics will not be able to calculate and prepare everything as accurately and clearly as experienced engineers. But it is quite acceptable to assemble a mini-tractor from dissimilar parts. There are known solutions in which the rear axle is taken from the UAZ, and the front axle from the Zaporozhets 968 model, both parts will have to be cut.
Now let's see how to properly shorten the bridge from the cars from Ulyanovsk, connected to two wheels back. Due to some design differences, the approach that is used for components from the VAZ is not suitable. After removing the axle shafts, you need to cut the "stocking". A special tube is placed at the incision site to help align. The pipe must be carefully scalded so that it does not fall out.

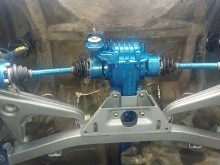
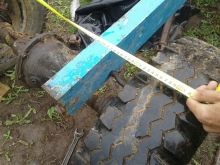
The half shaft is cut off. The required hole is made in it using a lathe. Having welded on both sides, cut off the excess metal. This completes the manufacture of a self-made bridge. It remains only to put it correctly and fix it. You can also make a mini-tractor with your own hands with a bridge from Niva. Importantly, the wheel arrangement of such a vehicle is 4x4. Therefore, it is ideal for working on difficult terrain. Important: it is worth using, whenever possible, parts from one mechanism. Then the assembly will be noticeably easier.
It is strictly forbidden to use spare parts that are worn out or cracked. But the installation of bridges from "Niva" on the frame of the same car is quite acceptable and even desirable. It will be even better if they take the transmission and the dispensing mechanism from there. The support structure in front is usually equipped with hubs from the front wheels.This solution allows the bridge to be displaced in two planes at once.
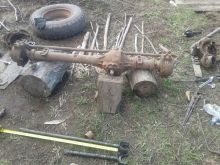
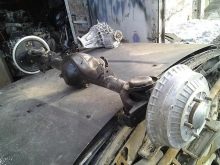
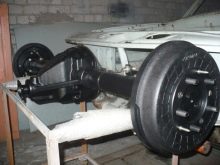
It is quite possible to take bridges from the GAZ-24. But it will be necessary to strengthen the structure. If the car very rarely runs into something, because it does not make a track, then for a mini-tractor this is the main mode of operation. Inattention to such a moment threatens to destroy the bridge and even other parts of the chassis.
Concluding the review of the options, we can say that home-made mini-tractors of the classic scheme are sometimes equipped with bridges from combines, however, more often only steering knuckles are taken from there.
For how easy it is to shorten bridges and cut splines, see the next video.
And I made a tractor without drawings - it has been working for 12 years and does not fall apart.
The comment was sent successfully.