Mini tractor clutch: features and DIY manufacturing
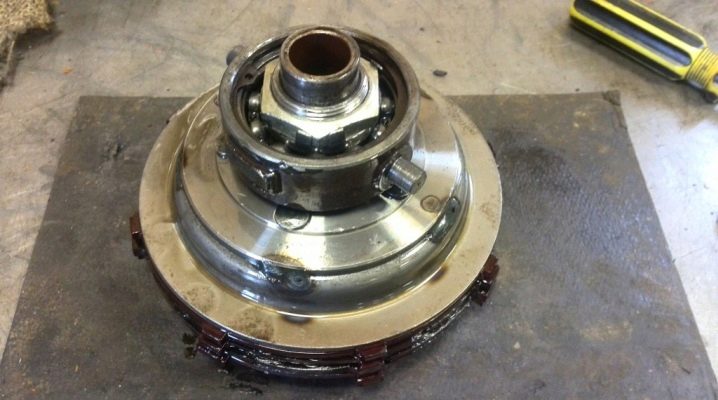
A mini tractor is a good, reliable type of agricultural machinery. But the big problem is often the purchase of spare parts. Therefore, it is useful to know how to make a clutch for a mini-tractor with your own hands.
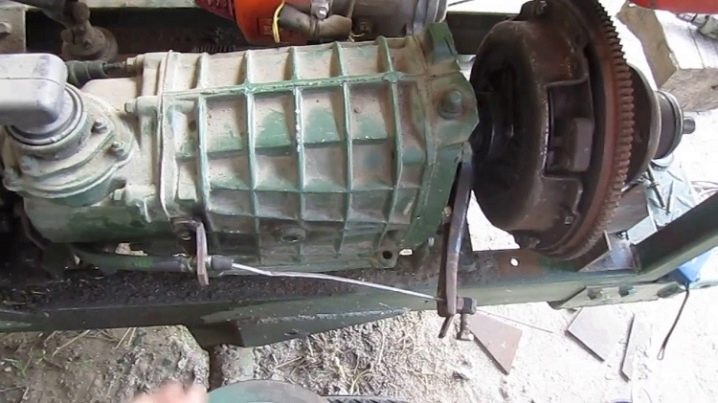
What is it for?
First you need to find out the main nuances of the work ahead. A clutch of any type is designed to solve a very urgent problem - the transmission of torque to the transmission. That is, if such a part is not supplied, normal operation is simply impossible. Moreover, without a clutch, it is impossible to quickly and smoothly disconnect the engine crankshaft from the transmission. Therefore, it will not be possible to guarantee a normal start of the mini-tractor.
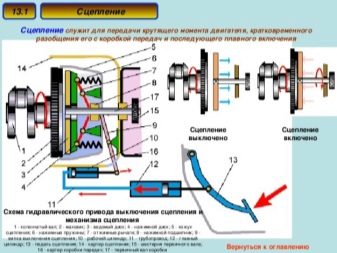
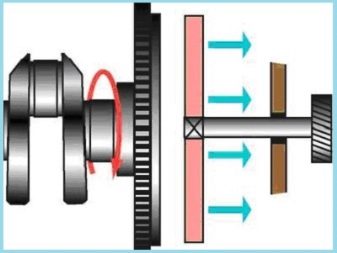
Friction clutches are unambiguously preferred by designers at factories. In them, the rubbing parts provide the transfer of torque. But a self-made clutch can be performed according to a different scheme. The main thing is to understand everything thoroughly before finally deciding something. According to a number of experts, it is much better to use a belt connection on a miniature machine. In this case, its objective shortcomings practically will not manifest themselves. But the benefits will be fully disclosed. In addition, the simplicity of the manufacture of such a part is also important for farmers. The sequence of work is as follows:
- take a pair of wedge-shaped belts (best of all 1.4 m in length, along profile B);
- a pulley is added to the input shaft of the gearbox (which will become the driven link);
- spring-loaded bracket of 8 links connected to the pedal, complemented by a double roller;
- install stops that reduce wear when the engine is idling.
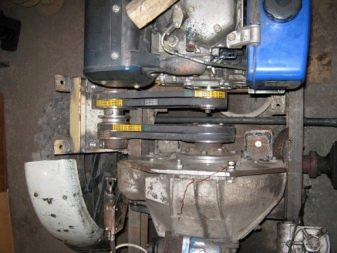
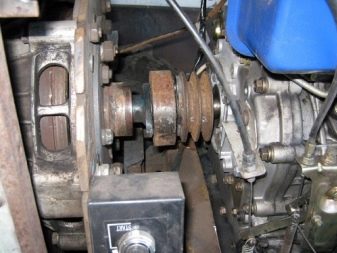
If you put just such a clutch, then the work will become much more efficient. The reliability of the entire system is increased. And in terms of labor costs, a belt clutch is definitely the best choice. Recommendation: you can use an already used gearbox. There is another option for doing the job. A flywheel is placed on the motor. They take the clutch from the car and use a special adapter when installing it. There is no need to pay for this adapter - great products are made from crankshafts. Next, the clutch housing is installed. It must be placed with the pallet facing up.
Important! We'll have to check if the flange mountings of the input shafts and the crankcase are compatible. If necessary, the gaps are widened using a file. It is also advisable to remove the checkpoint in this scheme from the old car. It is best if the distribution box is included in the kit.
To simplify the work, ready-made gearboxes are used.
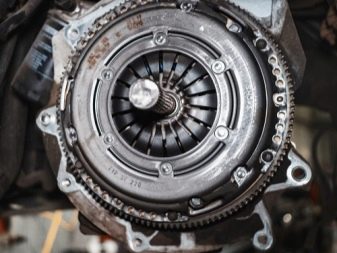
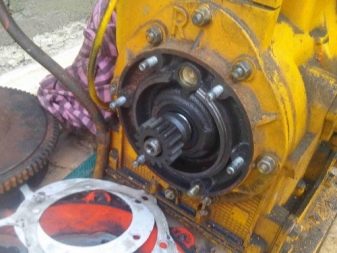
What other options could there be?
In some cases, a hydraulic clutch is used. Its couplings work due to the force applied by the fluid flow. A distinction is made between hydrostatic and hydrodynamic couplings. In products of the second type, the force created by the flow gradually changes. It is the hydrodynamic design that is now being used more and more often, because it wears out less and works much more confidently.
You can also find drawings of a clutch with electromagnetic clutches. The engine and transmission in such a system are connected using a magnetic field. It is usually created by electromagnets, although powder with magnetic properties can sometimes be used. Another classification of couplings is made according to their need for lubrication.
The so-called dry versions work even in an unlubricated state, while wet versions work exclusively in an oil bath.
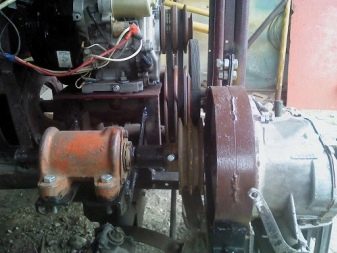
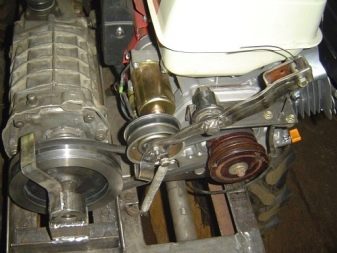
It is also important to remember that a different number of discs can be present in the clutches. Multi-disc design implies a case with grooves inside. Discs with special grooves are inserted there. When they rotate around their own axis, then one by one they transfer the force to the transmission. Can be made without turner and centrifugal automatic clutch.
When designing and manufacturing such products, one should strive to minimize friction. If this force is used for work, the overhead of mechanical energy increases dramatically. It should be borne in mind that the centrifugal clutch is poorly suited for the transmission of significant forces. In this case, the efficiency of the device also drops sharply. Gradually, the centrifugal clutch linings wear off, taking on a tapered shape.
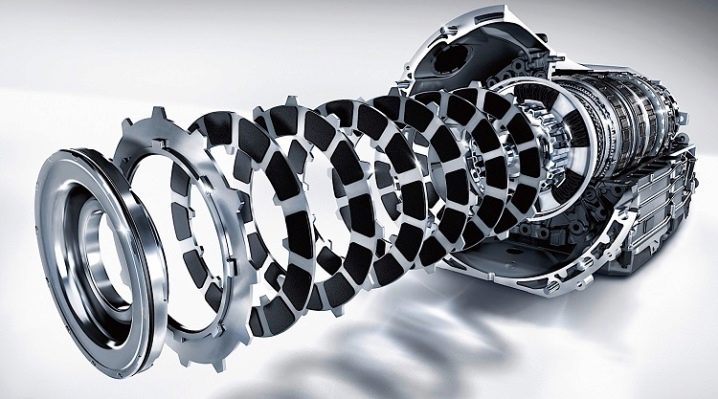
As a result, slipping begins. Repair is possible, but you will have to:
- use a quality lathe;
- grind off the lining to the metal itself;
- wind the friction tape;
- use glue for her;
- keep the workpiece for 1 hour in a rented muffle furnace;
- grind the lining to the required thickness;
- prepare the grooves through which the oil will pass;
- put it all in place.
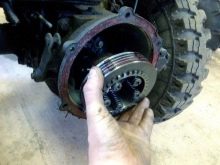
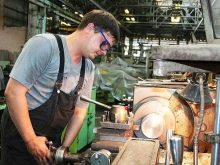
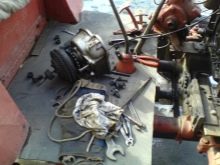
As you can see, everything is quite complicated, laborious and expensive. Worst of all, only conditionally such a clutch can be considered self-made. And the quality depends on too many factors, including those that cannot be controlled. Even a multi-plate clutch is much easier to make. Such products are recommended for equipping agricultural implements with a transverse engine placement.
Important! Parts of the clutch are combined with the transmission and the starter unit. All of this is lubricated with engine oil from a common source. Used clutch from old motorcycles is used as a blank. The sprocket is connected to the outer drum so that it rotates freely on the shaft. A ratchet is added to the drive drum. Driven and main disks are aggregated to a common shaft. At the same time, it is important to preserve their mobility. The structure is secured with nuts. Arrangement of master and dependent disks is performed in pairs. The first ones are joined to the outer drum using projections, and the second ones - using teeth.
The pressure plate is mounted last. It will help to tighten the rest of the parts with special springs. It is imperative to put a friction pad on each of the drive discs. Usually these parts are made of plastic or cork.
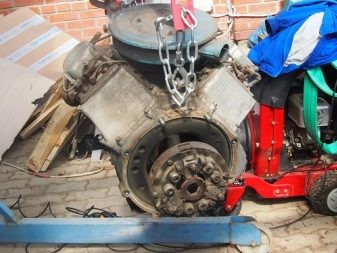
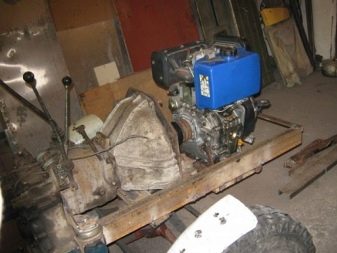
Lubrication, if necessary, is replaced with kerosene, the need for a constant supply of oil is fully justified by a longer service life than that of a belt drive.
Additional Information
An inertial clutch is often used. In it, the levers are connected to the driven shafts and are complemented by cams. The force of inertia drives these cams into the grooves located on the cup-shaped coupling half. In turn, this coupling half is connected to the drive shaft. The levers are attached to a common axis located in the slit of the driven unit.
The leading coupling half is equipped with radial inertial pins. They rotate and simultaneously act on the intermediate element. Such an element communicates through the spline with the driven shaft. Additionally, an intermediate glass with a shank from the slot comes into contact with the axle, fixing the levers in a clamped state. You need to hold them until the driven shaft unwinds.
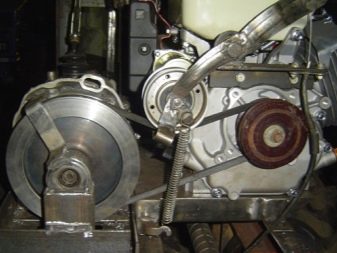
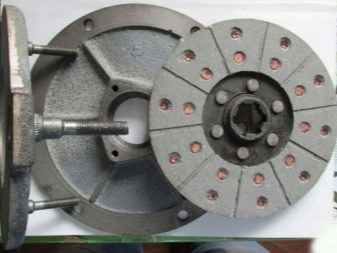
But still, most people prefer the familiar disc clutch. In order for it to work well, you will have to adjust the part immediately after installation. The adjustments are repeated later, already during operation, at approximately the same time intervals. At the same time, make sure that the pedal moves freely. If the adjustment does not help, consistently check:
- technical condition of bearings;
- serviceability of disks;
- possible malfunctions of the cup and springs, pedals, cables.
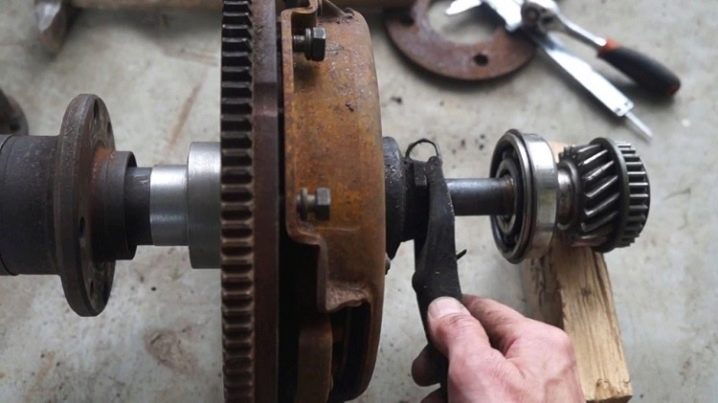
You can learn more about how to make a clutch on a mini-tractor with your own hands.
The comment was sent successfully.