Everything You Need to Know About Tap Holders
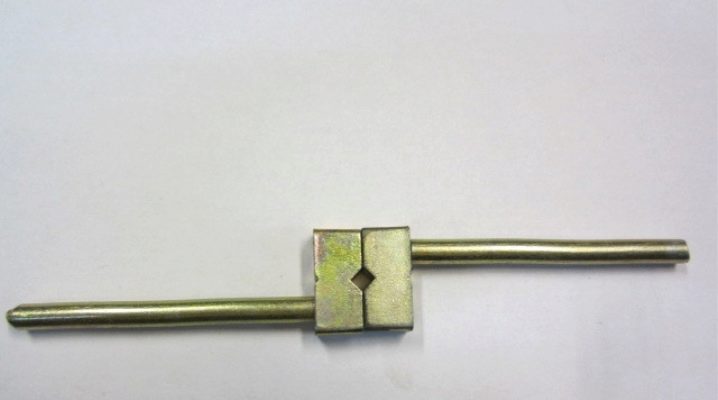
For connoisseurs of various types of tools and those organizing personal workshops, everything there is to know about tap holders is extremely important. Noteworthy is the universal tap holder with and without ratchet, models M3-M12, M6-M20 and other sizes. It is also useful to figure out how to make it yourself.
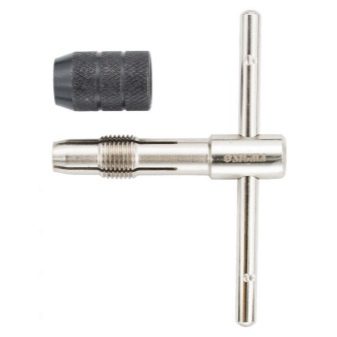
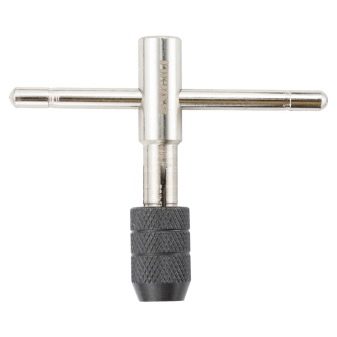
general description
There are many hand tools available. But even against the general background, the tap holder stands out. This device is designed to attach the tail of the tap, so that you can then cut the threads properly. The threading block is mounted just in the holding unit. Following this, it is set in motion (rotates).
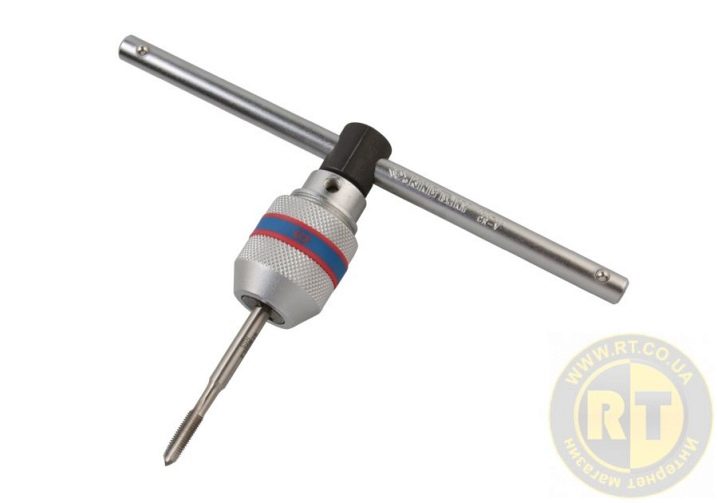
In this case, threading is quite easy and confident. Most often, this tool belongs to the universal category. The device is suitable for manual calibration work (with the creation of internal threads). Without such an auxiliary element, it is very difficult to exert the necessary effort and at the same time not disturb anything. Tap holders guarantee smooth, without the slightest distortion, twisting of those same taps, keeping it in a normal position with respect to the axial plane.
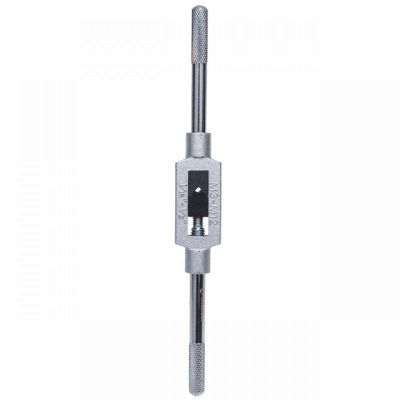
A factory tap holder is generally better than a self-made similar. There are various kinds of nuances in its design. However, the general standard of components has been worked out quite confidently, and their more or less typical composition is found in any product. We are talking about:
-
fixed handle;
-
moving rusks;
-
frames in the form of a prism;
-
retractable handles, sometimes supplemented with a ratchet;
-
goujons (blocks allowing to fix crackers).
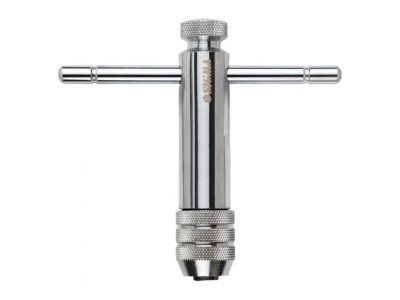
Typical geometric shape of the tap holder is a square. The size of the tap shank is specified in GOST 3266 from 1981. Formally, however, this standard refers to the taps themselves - but it is quite logical to link it with the holding devices. Tap holders sometimes have 2 or 3 pockets for a variety of tool options, but there are also models with 1 socket.
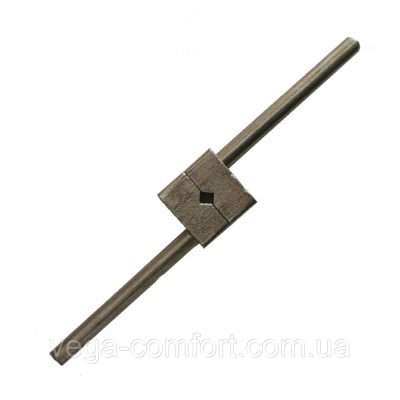
What are they?
By form
The geometric features of the tap holders make it possible to distinguish flat and angular models among them. The standard structure described above is for radial rotation models. End T-shaped devices are distinguished by the fact that increasing the depth of the thread must apply more and more force. All such fixtures are made by default with a ratchet, which guarantees a stable position of the tap holder when repositioning the rotary handles; this solution is suitable for working in confined spaces.
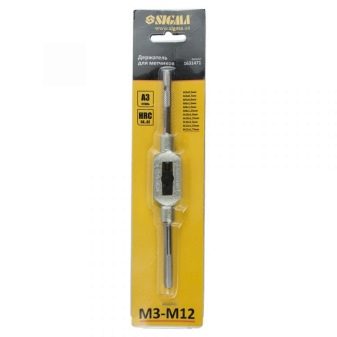
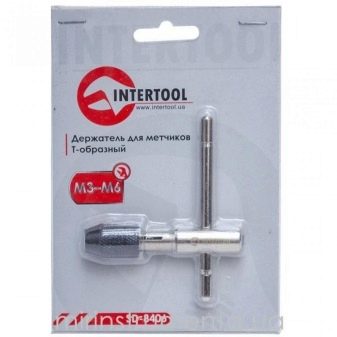
In the direction of rotation of the tap
It is not a question of radial or axial movement of the working part of the tap holder during operation. The taps themselves can move clockwise. Their main feature is the raising of the threads from the left to the right direction. If it moves in the opposite direction, then the twist should go counterclockwise. On this, however, the gradation of the produced tap holders is far from being exhausted.
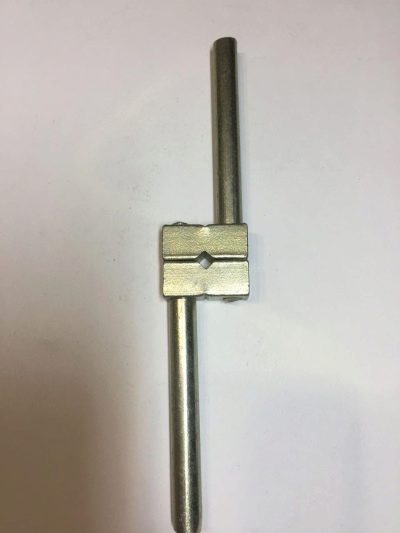
In some cases, it is important to maintain a stable torque. For this purpose, tared-type manual cranks are ideally suited. There will be no problems even with the wrong choice of the cross-section of the holes or the processing of particularly hard parts. The tool will simply slip and the tap will be reliably insured against damage.The composition of the calibrated device includes a body.
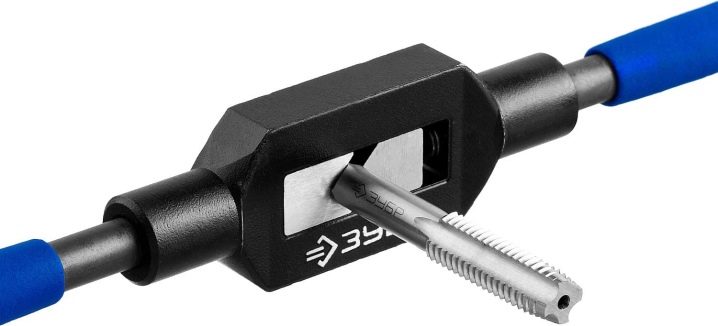
This housing has a through passage for attaching handles. The handles themselves are curved. Medium-carbon steels or steels saturated with a large amount of carbon are released for their manufacture. The pressure sleeve is movable. A square opening for the shank is placed on one of its ends.
A return spring is also provided. It adjusts to a strictly defined torque. Crackers are divided into 2 or 4 elements. The second type is characterized by increased functionality and ease of customization. Since the parts of the crackers are moved sequentially, all the faces of the square will change in the same way.
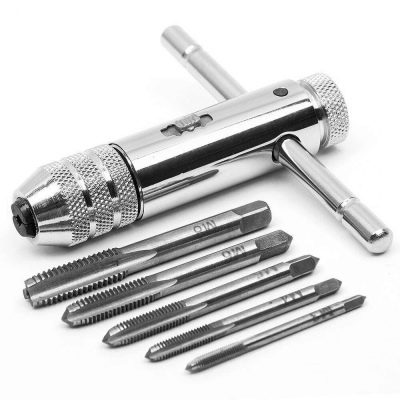
The accuracy of work is influenced by the proportion between the section of the tool and the length of the seat. Flat widened wrenches do not allow scrupulous adherence to the direction. Particularly precision tools are made from hardened tool steels. How well the spring has been calibrated can also be critical. If it is too thick, the torque is overestimated, and when thinning, it will take too long to cut the thread, exposing the tool to severe wear.
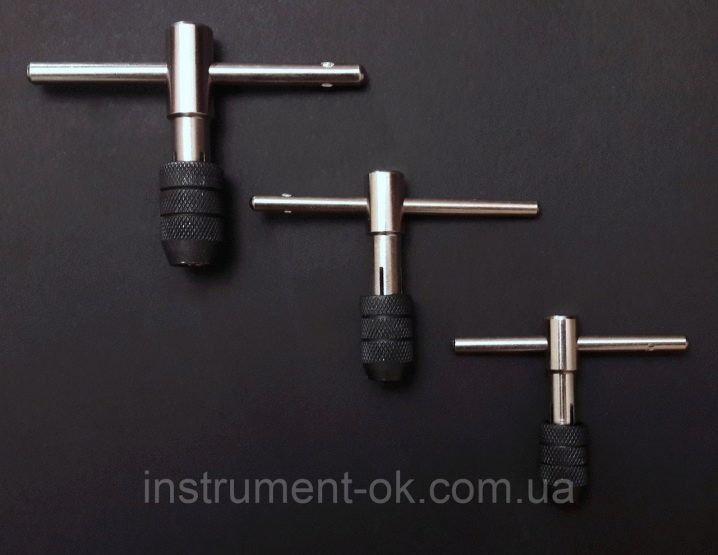
A universal tap holder is one that is designed to cut any thread. Normally, it moves in a circle. The state standard provides for the use of especially strong tool steel in a universal fixture. A substandard apparatus may be made of inferior metal. Along with manual models, there are also models for a lathe.

Such devices are manufactured by many companies. In some cases, it is more correct to use models with a torque limitation. A pair of mating cams are inserted into the body and sleeve. Before starting threading, the metal removal amount must be set. When the set value is exceeded, the cams stop engaging and slippage begins.
The ratchet holders already mentioned above can also be made in the collet type. Such products are suitable for forming deep threads in small parts. The reversing apparatus is good in that it allows you to back up a little and refine small omissions, to re-pass through an already worked area.
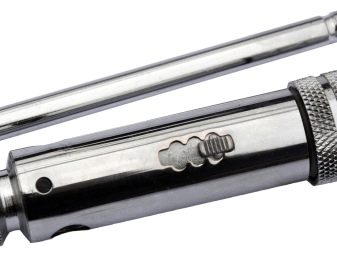
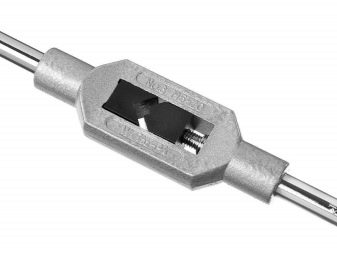
The reinforced holding unit is suitable for particularly strenuous work. He does not tend to break down just like that and works very effectively.
Dimensions (edit)
Tap holders M3-M12 have sizes from 3 to 12 mm, respectively. It is made from structural steel. And also typical ranges would be:
-
M6-M20;
-
M6-M24;
-
M8-M24;
-
M8-M27.
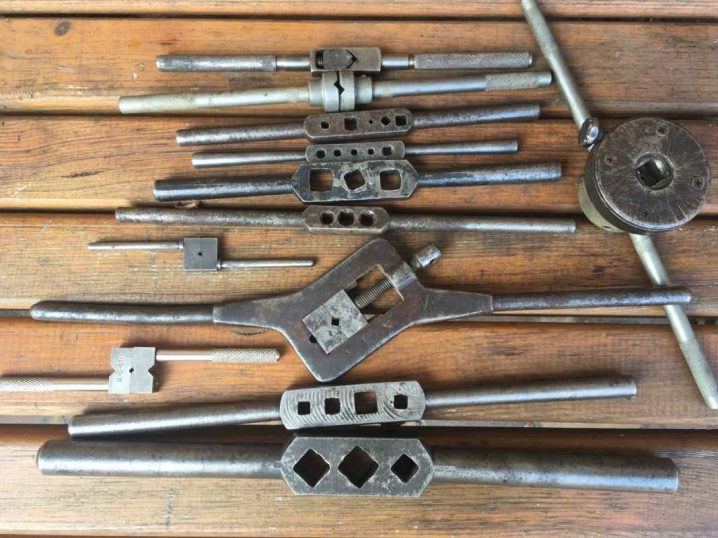
How to use it correctly?
The factory-made holding devices have a removable cover. The mechanism for adjusting the square is hidden under it. Operating with a special screw, the depth of the location of the crackers is changed. The screw has surface notches to eliminate errors. As mentioned, the amount of metal removed is critical.
This indicator depends on the fragility of the material. Cast iron is more fragile - and for it, such allowances are reduced. Violation of this rule threatens with excessive wear and destruction of the tool in one version, and in another development of events - the destruction of the part itself or its partial deformation.
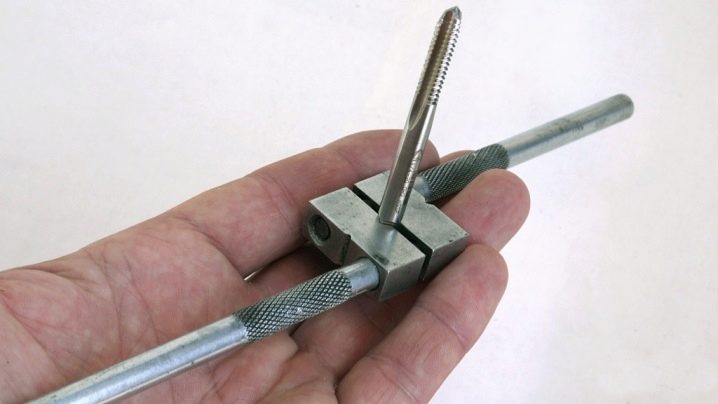
With the correct setting, the cam engagement is lost in time. As a result, the device stops working at exactly the right moment.
How to do it yourself?
In some cases, a home-made tool is still not too bad. And for private needs, it works quite effectively. In addition to the nut, you will need bolts or studs for it. The size of the parts must be proportional, otherwise there can be no talk of any normal work. Holes in the nut (sleeve) are obtained using metal drills.
The required drill size is estimated with a vernier caliper. Then mark the middle parts of the passages using a center punch.When the marking is over, the workpiece is fixed with a vise and holes are drilled. Then they take a tap of a suitable size and lengthen the grooves inside the coupling nut with it.
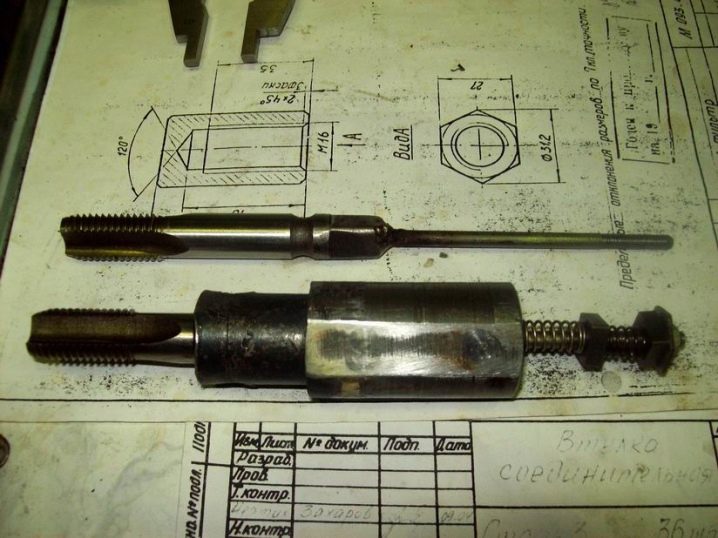
A wrench can be used to keep the cutting tool firmly in place.
Bolts are tightened on both sides. There are a few more nuances that allow you to attach the taps in the wrench more efficiently. It is recommended to tighten the bolts as tightly as possible. At the same time, the marking device must remain clearly in the vertical plane. Another option is to install a pair of locknuts, which tighten when installing the tap; an open-end wrench will help to do this.

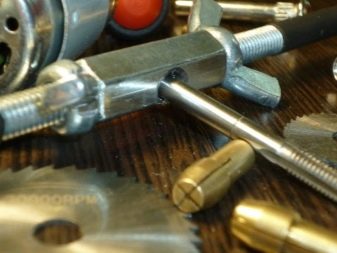
Some craftsmen improve the retention of shanks by using fluted bolts. They are prepared with an angle grinder. With a small amount of work, a household file also helps; the angle of the grooves should in any case be 90 degrees. The threaded projections on the bolts can be easily covered with rubber tubing or heat shrink tubing, which increases the ease of use of the tool. The sharp edges of the heads are rounded; if there is no emery machine, such manipulation is performed on a simple grinder.

An alternative solution involves cutting off a pair of identical segments from the steel square. Their length is 7-8 cm. Then one workpiece is placed on top of another, leaving some overlap. Fixation is done with tape or masking tape. A couple of holes are drilled in the blanks.
Channels need threading. Further, the docking is carried out already rigidly (with bolts). Another passage is being prepared in the middle. The semi-finished product is disassembled again and modified with a triangular file.
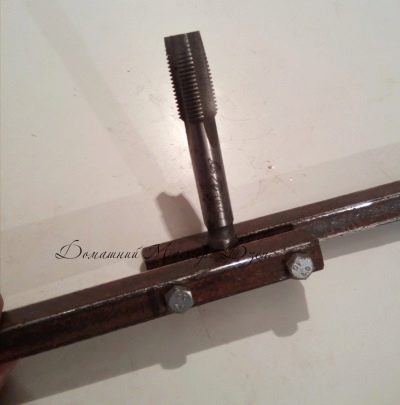
To insert the tap, you must first unscrew the bolts, and then fix them again as expected.
How to make a tap holder with your own hands, see the video.
The comment was sent successfully.