All About Machine Taps
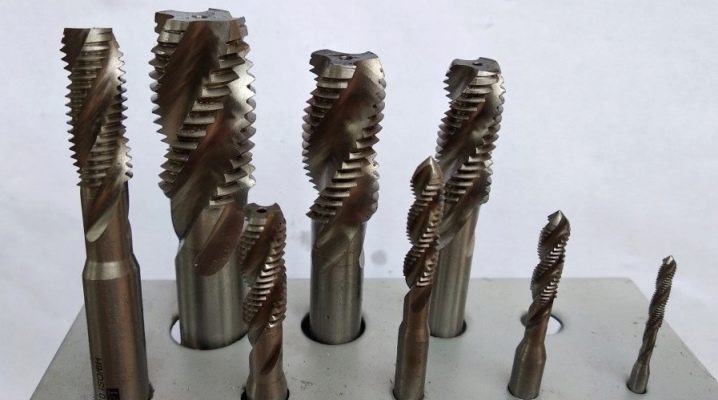
To organize many industries and workshops, you need to know everything about machine taps, about the requirements for them in accordance with GOST, about elongated, complete and supplied with a screw groove structures. It is useful to understand what M6 and M8, M10 and M12, M4 and M3, M5 and other tap sizes mean. And you will also need to familiarize yourself with the nuances of the selection and practical application of such models.
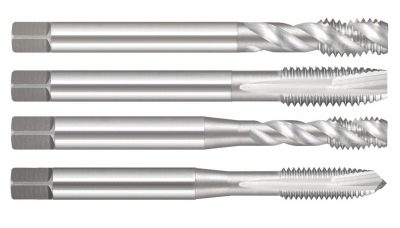
Design features
The main specificity of any machine tap is explained by its name. This device is intended exclusively for use in various machines and apparatus. It differs from manual and machine-manual options in its unique geometry. The shape is changed for a reason - it is designed to achieve the highest possible speeds during processing. Turning fixtures are created purposefully for installation in the centers of the corresponding type of machine; the only difference is in the design of the tail section.
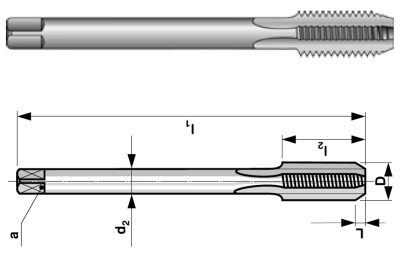
The intake segment for through passages is 5 or 6 turns. To cut a blind hole, even 2 turns are enough. This circumstance is actively used by designers in order to reduce the length of their designs to reasonable limits.
The tail section can be made in a bar or square format. The structure of the groove determines how effectively the thread will be cut, how the chips are completely removed.
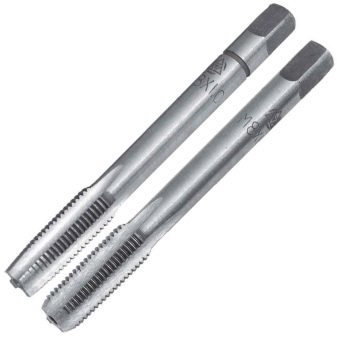
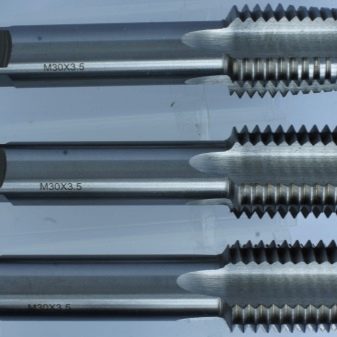
Most popular are taps with 3 or 5 flutes. The rake angle of the product is important. Least of all - from 0 to 5 degrees - it should be for working with cast iron. To machine steel, you need values between 5 and 10 degrees. Manipulations with non-ferrous metals and alloys based on them are easiest to carry out with a front angle of at least 10 and no more than 25 degrees.
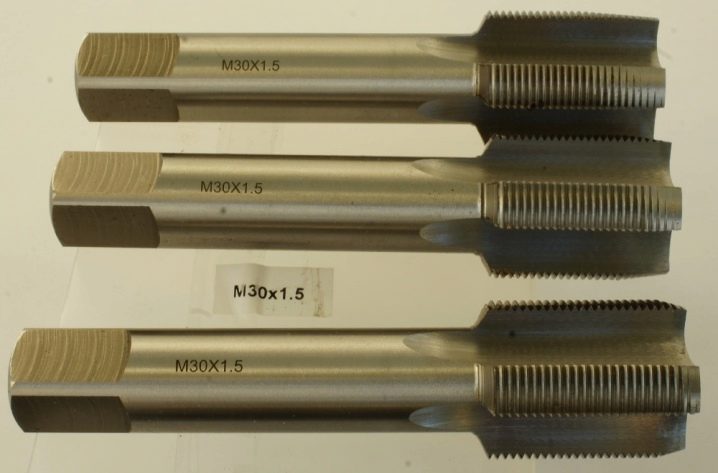
Rear angles range from 4 to 12 degrees. Most often, the grooves run straight. But if ideal chip evacuation is critical, then the slope should be between 8 and 15 degrees. Long shank models are usually designed for metric grooves from M3 to M10 inclusive. The standard for their development and production is obtained by direct translation of the global standard ISO 8051-89.
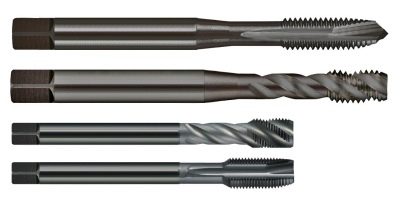
Complete versions are also designed for metric threads by default. Both complete and single tap models can be designed for through and blind holes. In some cases, the striper has a long shank, which is very practical and convenient for serious work. As for products with a helical groove, they must all comply with GOST 17933-72, which retains its relevance.
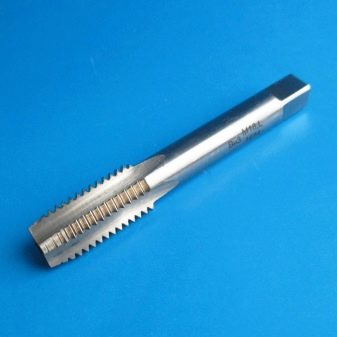
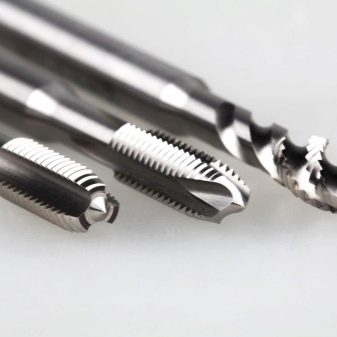
The standard specifies:
-
orientation of the grooves themselves;
-
angles of their inclination for different cases;
-
dimensions of the squares;
-
basic dimensions tolerances;
-
nominal thread cross-sections.
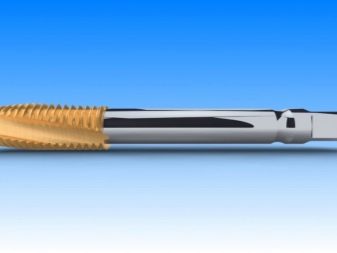
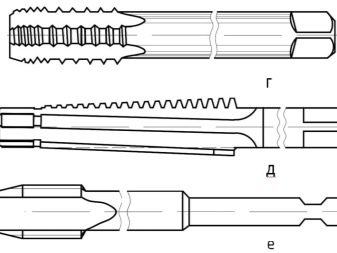
Dimensions (edit)
These values are set in accordance with GOST 3266-81. The product of category M3 has a main cutting pitch of 0.5 mm. At the same time, it is able to punch a hole 5 times larger - up to 0.25 cm. I must say that such proportions are not always maintained. So, taps of the M4 type with a thread pitch of 0.7 mm prepare holes with a size of 0.37 cm (coefficient 5.28). For M5, the ratio will be 0.08 and 0.42 cm (coefficient 5.25).
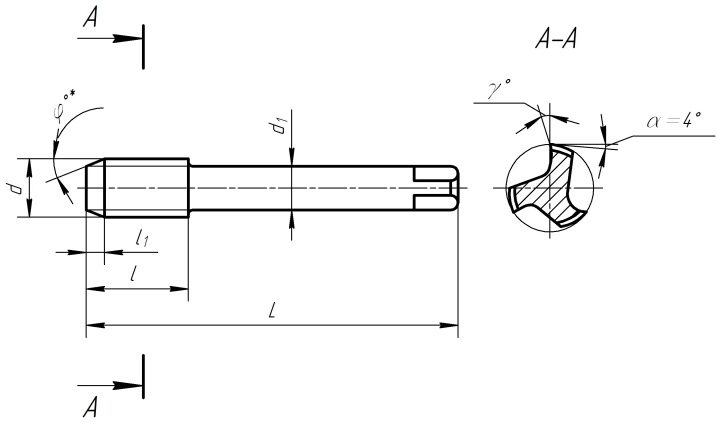
Other sizes (cm):
-
M6 - 0.1 and 0.495;
-
M7 - 0.1 and 0.595;
-
M8 - 0.125 and 0.67;
-
M9 - 0.125 and 0.77;
-
M10 - 0.15 and 0.843;
-
M11 0.15 and 0.943;
-
M12 - 0.175 and 1.02;
-
M16 - 0.2 and 1.39;
-
M20 - 0.25 and 1.735;
-
M30 - 0.35 and 2.63.
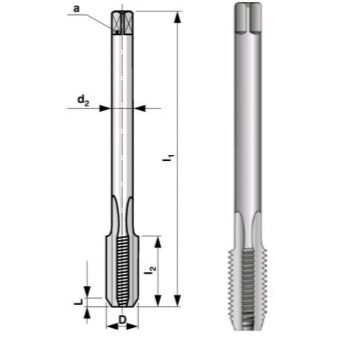

Criterias of choice
First of all, you need to clarify what kind of metal you will have to work on. Some features of taps for different types of metal are described above, and it makes no sense to return to them. But there are other points that are also worth considering. It is necessary to take into account the number of grooves through which the chips exit and the special fluid enters. This number can be from 2 to 6 pieces, and it is chosen after careful technical analysis.
It is worth analyzing both the profiles of the valleys and the direction of the groove travel. Straight grooves are predominantly used in typical universal taps.

The left direction of the helix allows you to make a "through" thread. In this case, the chips are grouped in front of the tap itself, and the cut does not deteriorate. The right-hand position of the grooves is recommended for blind canals; with this option, the chips are retracted and not compressed (if they were squeezed, the tool would deteriorate very easily).
The intake block is shaped like a cone. This makes it possible to significantly facilitate the entry of the teeth into the most stubborn material. The tilt angles can be 3-20 degrees. They are determined by whether the tap will insert a primary or a finishing thread. It is also necessary to evaluate the calibrating part, which is designed to reduce the friction force.
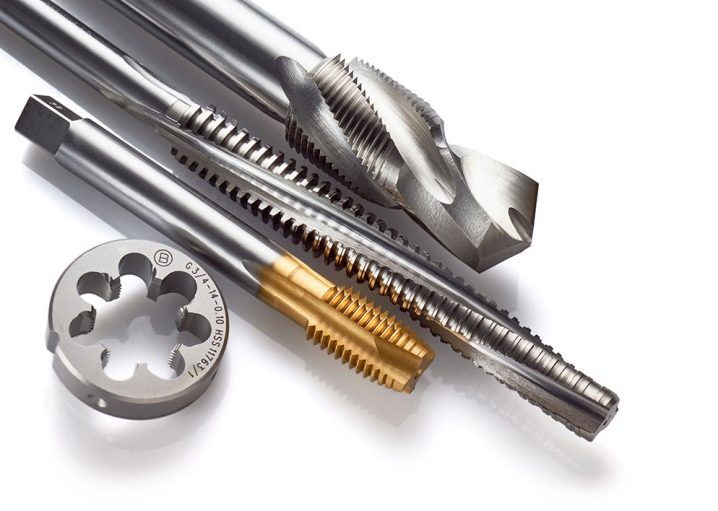
Some taps have short flutes or no flutes at all. Such devices are good for making threads in an aluminum alloy of various compositions. They are also suitable for tough steels with a low carbon content. But this device is also useful for especially strong steels with a high level of alloying additives. The helical flutes allow the tap to be used successfully as a component of a machining center, producing excellent blind threads.
In some models, the teeth are staggered. This means that they are sheared off one after the other in the sizing section. With this approach, the friction is less.
As a result, the handling of viscous materials is simplified. Step taps are used if it is necessary to process individual zones with a special shaping scheme.
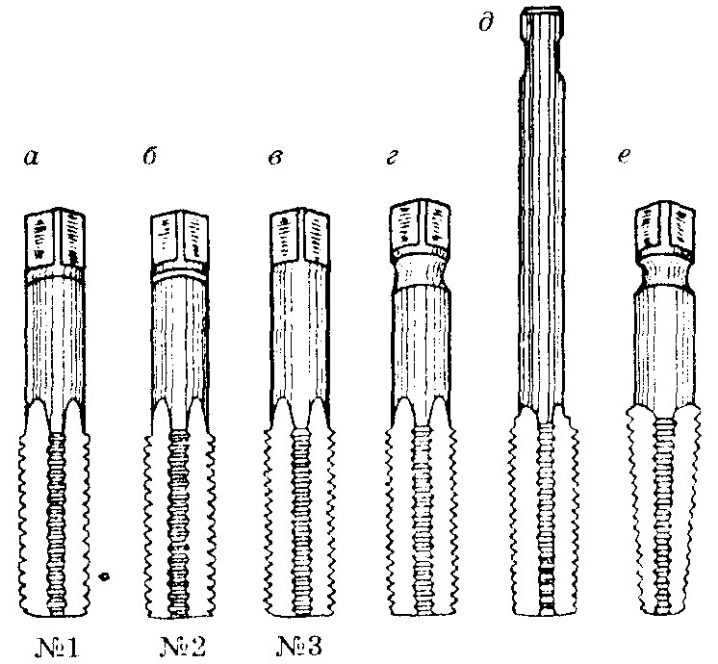
Combined marking devices have a drilling step or, more simply, a conventional drill. Broach taps are used to cut threads of arbitrary section and pitch on lathes. If you need maximum productivity on modern machine tools, taps with an internal channel for supplying a lubricating and cooling fluid are used. They are suitable for both universal and specialized machine tools.
Sometimes the task is to prepare a through thread of an especially large section (from 5 to 40 cm). In such cases, bell taps are needed. It is an assembly tool, divided into separate cutting segments. Cooling fluid also flows into the housing. Provides 16 working pens; The absorption of large amounts of swarf is also a useful option.

By the type of thread formed, in addition to traditional metric ones, there are also:
-
inch;
-
pipe conical;
-
pipe cylindrical taps.
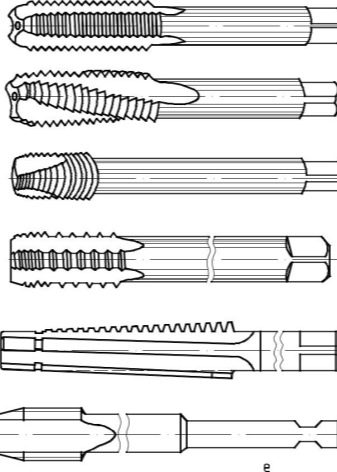
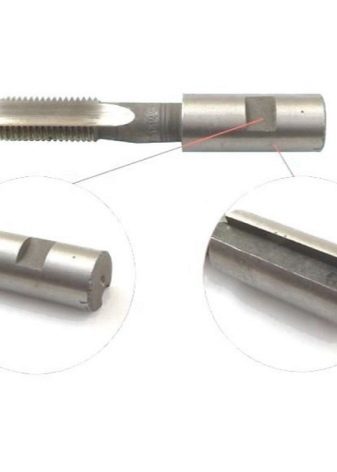
Machine line markers operate at high speeds. Therefore, they get very hot. As a result, normal operation is only guaranteed when using high quality high speed steels. Among them, the most preferred alloy is P18. If the loads are slightly less, you can also use P6M5 or P6M5K5 (K8); the machines with the highest productivity always have carbide tooling.
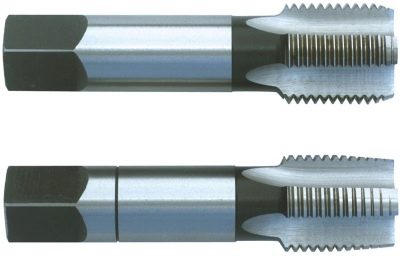
Application
Even many non-specialists know that the tap is for threading. But there are some subtleties here. For proper operation, you need to accurately determine the cross-section of the hole - this is easiest to do by referring to technical standards. The key step in thread preparation is drilling a hole of the required cross-section.Errors in this phase either lead to an insufficiently tight thread or to breakage of an overloaded tool.
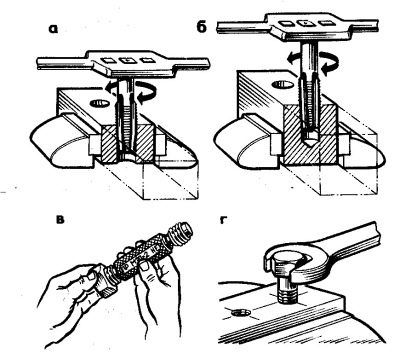
Most often, the work is divided into two stages. First, the grooves are formed with a rough tap. Then they are finalized with a finishing tool. If the thread is to be formed in a deep channel, the procedure is interrupted periodically to clear the chips. And also in such cases, you cannot do without lubrication.
Many people recommend using special emulsions. But the use of kerosene or linseed oil can also be a good option.
When laying blind channels, their depth must be made greater than the length of the cut segment. If the tap during operation does not go beyond the required length of the thread, it will be incomplete. The grooves themselves are formed only if the workpiece is clamped in a vice.
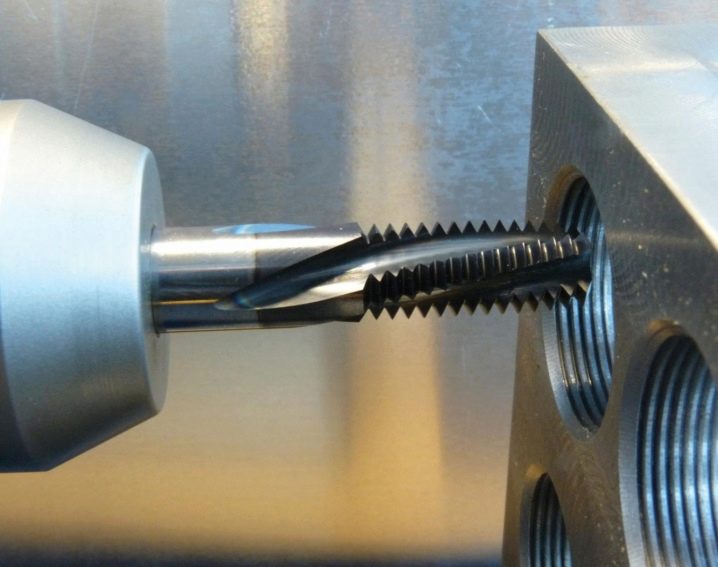
The correct selection of cutting fluid for a particular application is very important. Linseed oil is used when working with brass and steel billets. A diluted emulsion is relatively versatile. Dry operation is permissible for cast iron and bronze structures. If you need to make threads on aluminum parts, you will have to use kerosene; machine oil and other mineral oils should not be used.
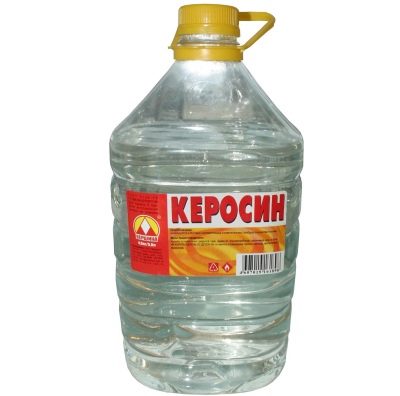
Periodically removing the canal cleaning tool is useful when working on tough and soft metals. This rule must be observed, even if the hole itself is shallow there. It is imperative to check the correctness of the insertion of the tool, the absence of distortions. The most critical in this regard are blind notches of shallow depth. The speed of work is selected taking into account the type of material and the resulting loads; the feed should be uniform and smooth.
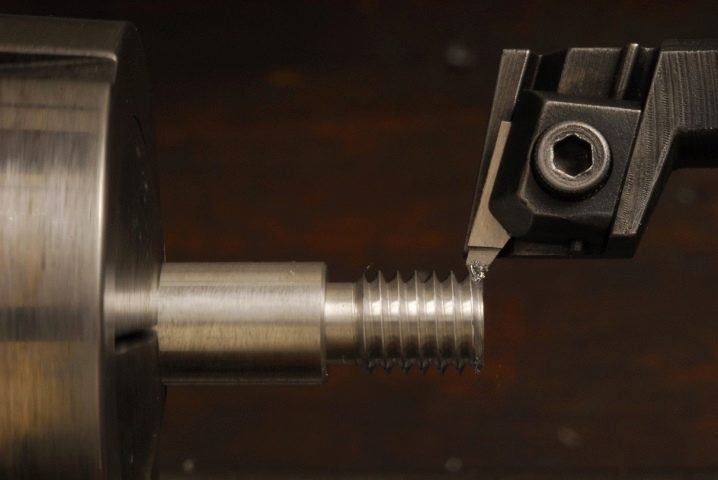
The comment was sent successfully.