Overview of corrugated aluminum sheets and their uses
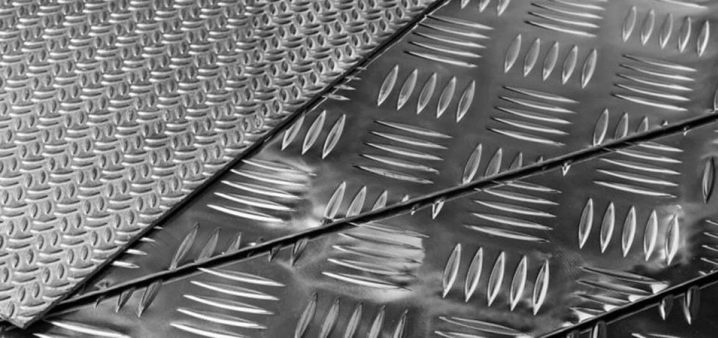
Embossed aluminum sheets (corrugated blanks) are a way not only to update the design of a room, but also a severe necessity in special cases, for example, when there is a danger of slipping during icy conditions around. Sheets with this texture have a repeating pattern.
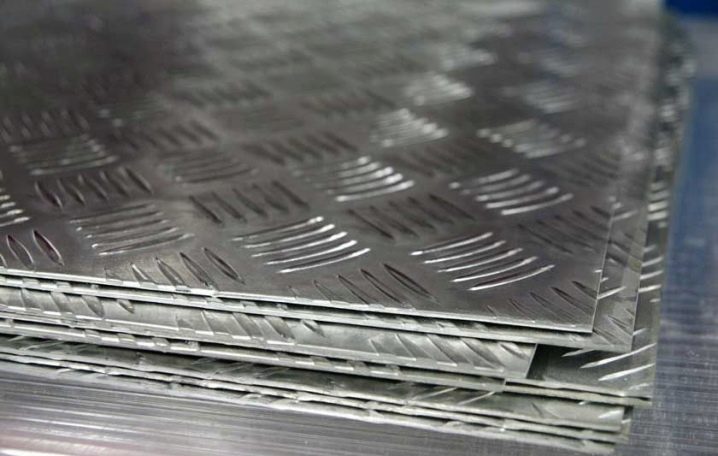
Features and properties
Corrugated aluminum sheets are a product with a number of features. The front side of the sheet is a special pattern that is located throughout the workpiece. This pattern is a repeating pattern of notches. But these bulges are not only decorative. The large-textured roughness created by these bulges prevents people and technology from sliding when moving, despite the smoothness of the rest of the points and areas of the sheet.
Aluminum alloys are environmentally friendly materials.
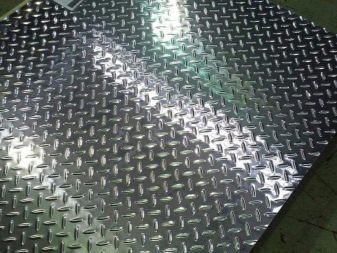
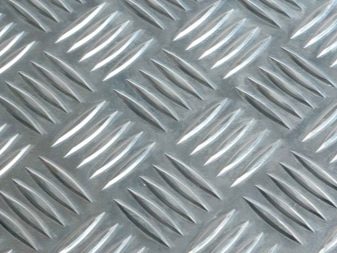
Environmental friendliness is achieved due to the absence of traces of metal damaged by oxidation, which could form, for example, during the rusting of iron... Aluminum forms a strong oxide film, which does not allow moisture and oxygen from the air to destroy the sheet further, significantly reducing its thickness. However, strong in their effect, strong acids and alkalis destroy many metals and their alloys at a catastrophic rate.
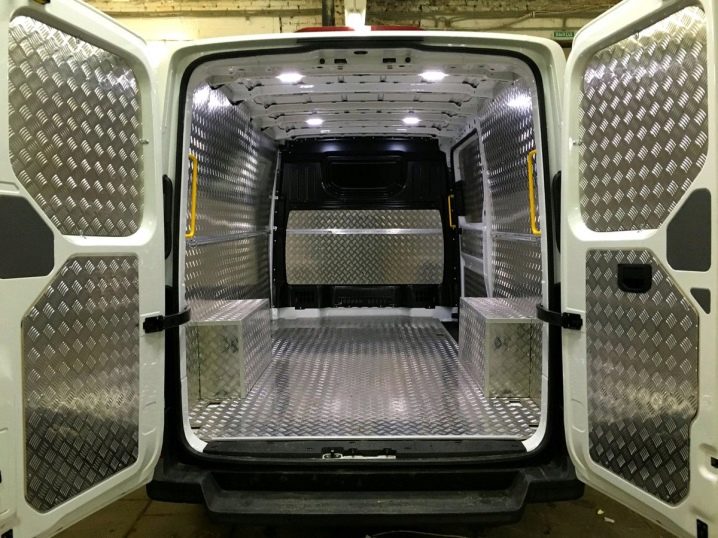
The purpose of sheet corrugation is to give it physical and technical parameters. After corrugation, the consumer characteristics of these blanks increase. Due to corrugation, the horizontal stability of aluminum increases, and with it the list of applications for such a sheet grows. Corrugation prevents the sheet from bending when exposed to it. For example, when passengers and flight attendants actively move on such a surface in the cabin of an airliner every day, the corrugation does not lose its shape and repeatability, since the effort of a person standing on such a surface from his feet (shoe soles) is redistributed over dozens of identical bulges.
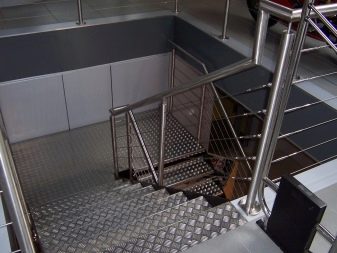
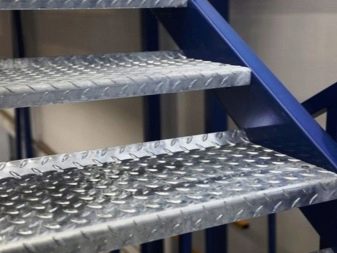
Aluminum is durable primarily due to the absence of acids and alkalis in its threatening strength and thickness concentration, which could get into the cabin of the same aircraft from the airport. Corrugated sheets are not afraid of heat and frost - they can be used in any local weather on all five continents.
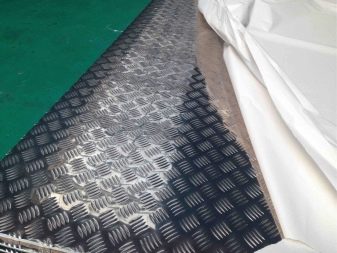
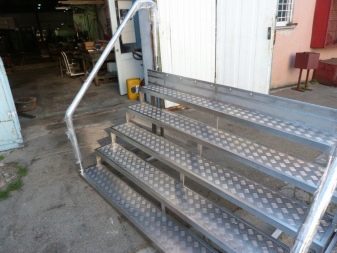
Manufacturing methods
Additional alloying additives are added to the aluminum alloy. But the technique of producing corrugated sheets is not limited to one alloying. Production methods - hot and cold rolling, as well as additional coatings.

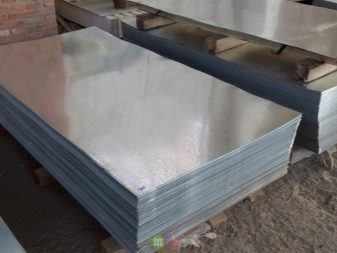
Hot rolled
Hot rolled material is mainly used as sheets produced in a multi-stage production process. First, the alloy, in which all the necessary additives are mixed, is cast in the form of an ingot. Getting under the rolling shafts of the hot-rolling mill, the ingots during melting are rolled out at a very high pressure - tens and hundreds of atmospheres.
The surface of the rolls is such that repeating shapes (riffles) are applied on it in the form of concavities, which imprint corresponding convexities on the surface of the sheets being formed.
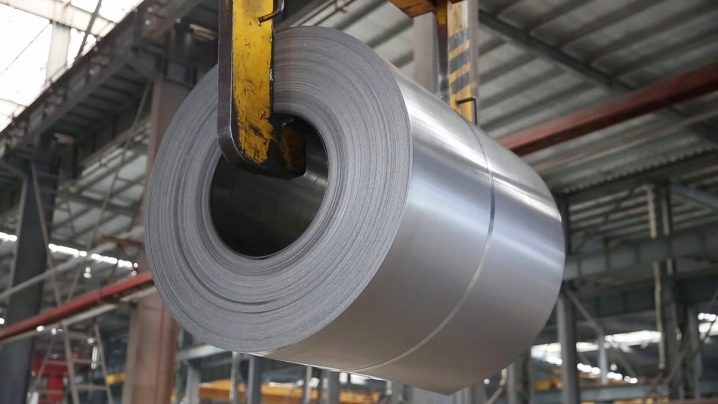
The high temperature makes the aluminum billet highly ductile, but the sheet temporarily loses its original strength. The cost of hot-rolled sheets is noticeably lower, since the shafts of the hot-rolling mill only perform rough processing.The thickness of the successful billet fluctuates noticeably - it depends on the uniformity of heating of the entire thickness of the ingot. It surpasses the three-millimeter threshold - due to significant fluctuations in the value, reaching 300 microns. The production capacity can be adjusted - and completely stop production when the current plan is fulfilled.
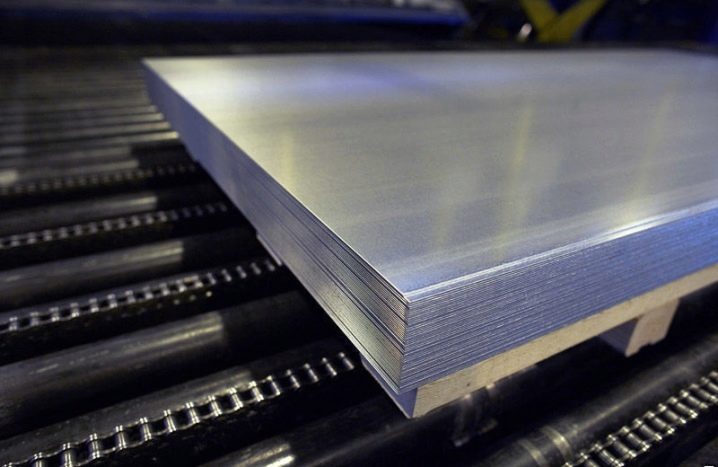
Cold rolled
Cold rolling of aluminum makes it possible to obtain high-precision rolling of sheet with the same bulges. Due to variations in thickness by a few micrometers, which is tens of times better than in a fully hot-rolled production, the thickness of the aluminum sheet can be less than 1 mm. The lack of temperature is compensated for by high-power efforts: a significant amount of energy is consumed, while converting a rough-cut aluminum slab into a high-precision sheet requires prolonged, repeated passing of the hot-rolled sheet through the roll mechanism of the machine. However, the result is not only highly accurate sheet thickness, but also sheet width.

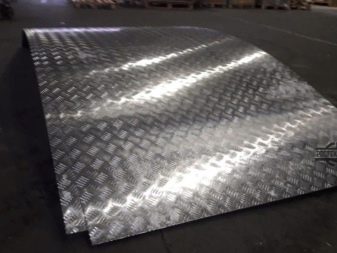
Plating
Cladding - covering an aluminum alloy sheet with a thin layer of pure aluminum. It is pure aluminum that has the greatest environmental safety, largely related to corrosion resistance. For a clad sheet, marker "A" is a regular coating, "U" is a thickened one, "B" is a technological cladding.
If there is no aluminum coating, then this marker is not applied.
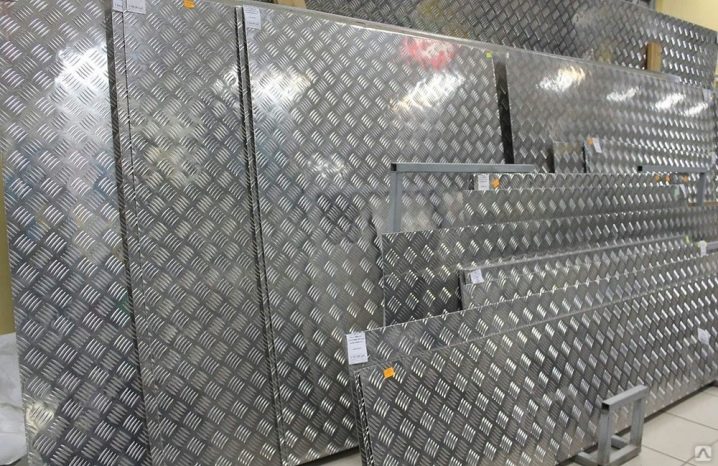
Normal cladding is carried out in the production of duralumin sheets, since duralumin, unlike aluminum, is subject to corrosive processes. Coating - two-sided. Coating thickness - 2% of the total thickness of the successful workpiece. In this case, the sheet must be thicker than 1.9 mm. With a smaller thickness, the coating will already reach 4%: the thickness of the coating itself should not suffer, otherwise it will not last long.
Coverage larger than the usual nominal value retains the same tendency: at 1.9 mm and less sheet thickness, the coverage will be 8%, in other cases - 4%.
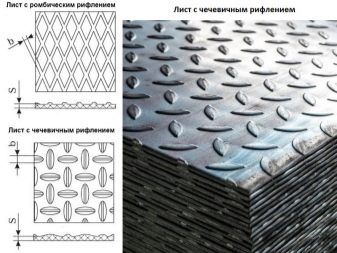
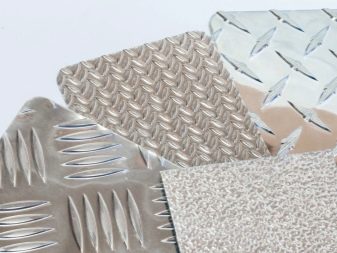
Technological coating - an additional layer that prevents the formation of cracks and chips during rolling. This will not improve the protection against oxidation (deoxidation) of the sheet material. Technological coating does not depend on the sheet thickness - and is always equal to 1.5%.
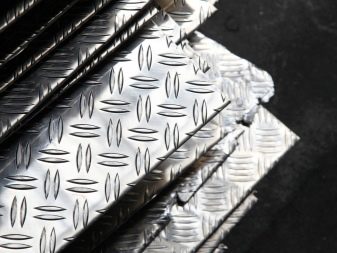
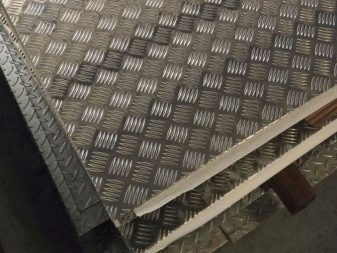
Types by processing method
For the manufacture of corrugated sheets, various methods of mechanical and thermal processing are used. These methods make it possible to raise the indicators of the sheet used to a new level, which has a beneficial effect on the applicability of products in various spheres of the national economy.
Annealing of sheets is performed to eliminate mechanical stresses in the structure of the product. The fact is that aluminum products burst when critically high stresses appear. Heating is carried out for a long time. Excessive hardness of the aluminum alloy leads to the appearance of additional brittleness, and this is unacceptable for responsibly loaded coatings. Annealing marker - "M".
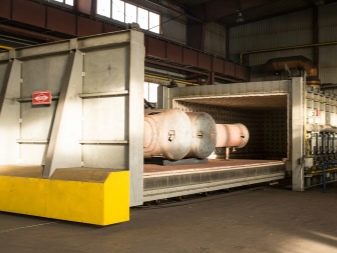
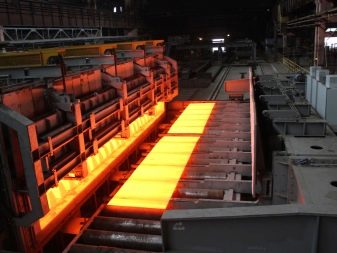
On the contrary, the rolled sheet goes through a stage of low-temperature processing.
The result is greater hardness and strength, but less ductility - the product breaks easily. The garter marker is "H". Semi-fretting - a decrease in the intensity of such processing, the marker is "H2".
Refining, based on electrolysis cleaning of the sheet surface from impurities, improves its composition and mechanical properties. The hardened sheet is resistant to breakage; it heats up to a significant temperature - and cools down in a fraction of a second. The aging effect is carried out at room temperature for 5 days, or in a heating chamber up to 150 Celsius in a few hours. Marker - "T" for finished items and "T1" - for blanks.
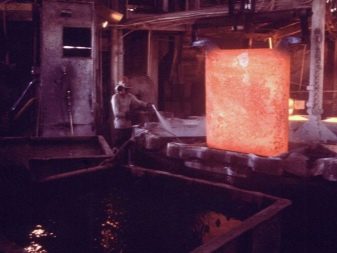
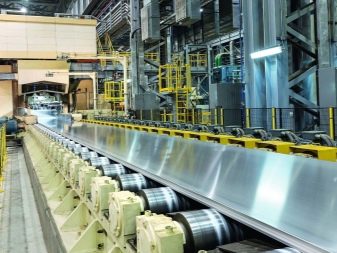
Finally, the sheets can be colored. Dyeing is not used for floor sheets - the paint will wear off the shoes of people walking on it in less than a year, so there is no point in dyeing them additionally.
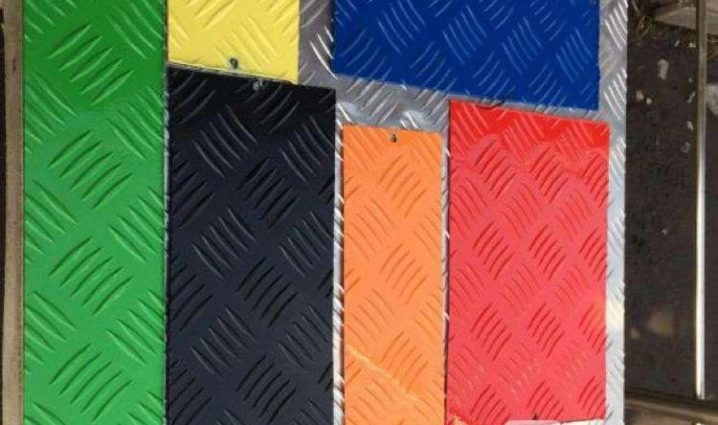
Riffle classification
The bulges are produced in the following shapes.
-
Diamond (or "diamond") - one repeating bulge, for example, in the form of a lenticular or rhombic outline.
-
Duet - two notches, trio - three, quartet - four, quintet - respectively, five.
The drawing is carried out by the methods of heated and cooled deformation.
As a result of the application of all the above measures, the sheets are the most lightweight in weight or installation workpieces.
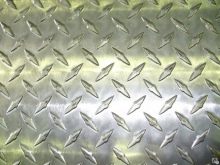
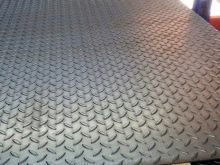
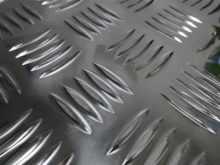
Common brands
The production of corrugated sheets is standardized in accordance with GOST 21631-1976. Acid-resistant assortment is produced in the process of alloying with manganese and magnesium - and is used for tanks. Technical grades bend easily - penofol is proof of this (polyethylene foam and foil), metallization does not crack. Food sheets do not emit any compounds, do not react with food salts and acids, which allows them to be used for the production of milk cans and tanks. Smooth perforation allows these sheets to be used as sieves and grids as part of filters and or ventilation boxes.
Duralumin sheets are used in aircraft, helicopter and drone building, as well as electrically conductive substrates, for example, for processor chips, microcontrollers and other microcircuit assemblies.
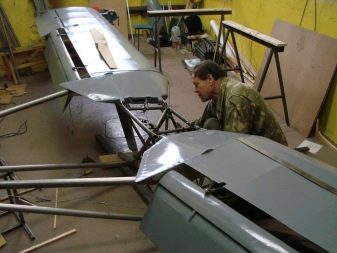
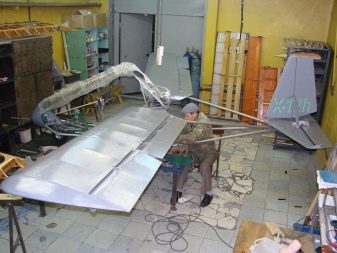
For the production of sheets, the following alloy grades are used: AMg2H2, AMg2, AMg2NR, VD1AN, VD1AM, differing in properties. The letter marker means one of the main impurities, for example, "Mg" indicates the presence of magnesium, the number - tenths and hundredths of a percent alloying. In some cases, the percentage is indicated as an integer rather than a fraction. So, the AMg2H2 alloy is 2% magnesium. Execution - semi-finished.
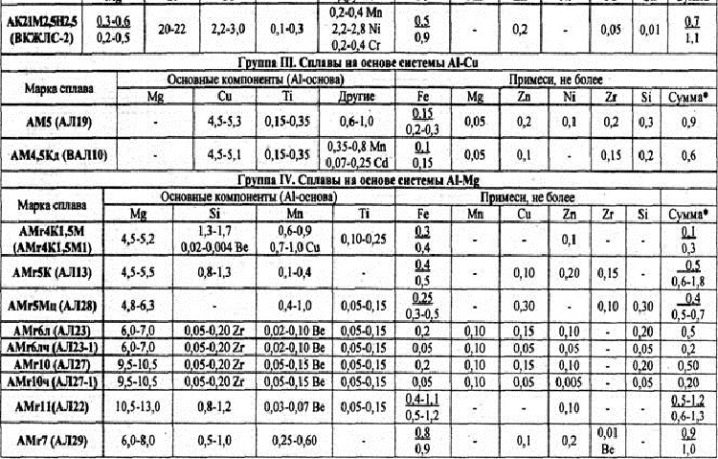
Dimensions and weight
The thickness of the most common types is 1.5, 2, 3 and 4 mm. The sizes of demanded products are 1500x3000, 2x1200x3000, 1200x3000, 2x1500x3000, 5x1200x3000, 3x1200x3000. As you can see, sometimes thickness is attributed to length and width, which nominally indicates volume. Some sheets with standard width and thickness in the assortment indicate only the length of the workpiece: 1000, 2000, 2500, 3000 mm. The weight of 1 m2 is determined based on the knowledge of three quantities: volume, density and correction for the mass of bulges.
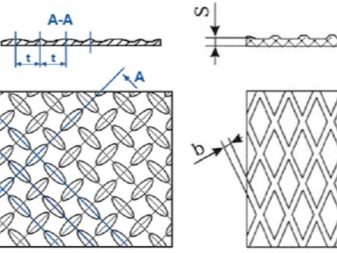
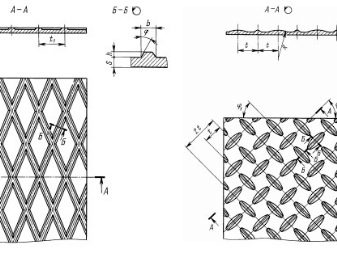
For the production of aluminum sheets, the specific gravity of the composition is normalized. For example, for the same AMg2 it is equal to 2690 mg / mm3. If it is necessary to make a "tiled" cladding from rectangular cuts, then use cuts, for example, 150x300 mm, made of the same alloy, with the same material thickness, but this does not change the essence of determining the density of 1 m2 of the coating.
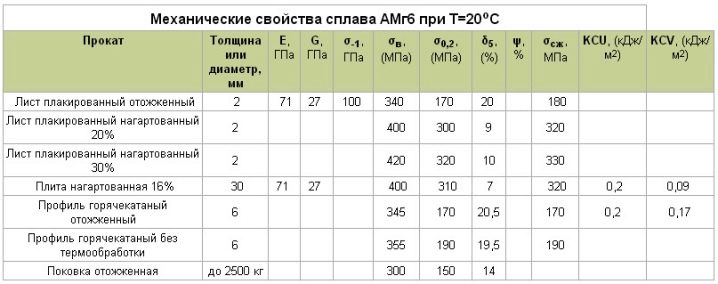
For example, for sheets made of another alloy, the density is 2.85 kg / dm3. To clarify the specific mass, a corrugation conversion factor is used, equal to 0.947 for AB alloy, 0.937 for AMg3, and so on. The practical values of the weight of an aluminum sheet with 5 lines per texture fragment (quintet) are arranged as follows.
-
Sample 1.5х1200х3000 - its weight is 13.6 kg. The first value is thickness.
-
1.5x1500x3000 -19.8 kg.
-
2х1200х3000 - 20.6 kg.
-
2x1500x3000 - 25.2 kg.
-
3х1200х3000 - 30.3 kg.
-
3x1500x3000 - 37.3 kg.
-
4х1200х3000 - 39.6 kg.
-
4x1500x3000 - 47 kg.
-
5x1500x3000 - 66.7 kg.
Corrections in calculations are made according to the parameters of the applied texture.
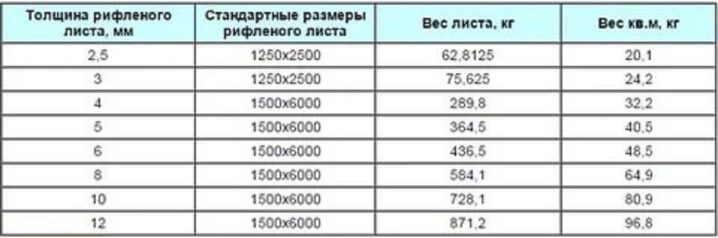
Application area
The properties of corrugated sheets give the green light to these products in a significant number of specific examples.
Anti-slip coating for airplanes, cars, trains, trams, in the rolling stock of the metro and other types of transport. An ambulance van is an example.
The same coating is for hospital rooms. For example, an X-ray room whose room is isolated from the rest of the building by reinforced / shielded wall and ceiling structures may have the same floor covering.
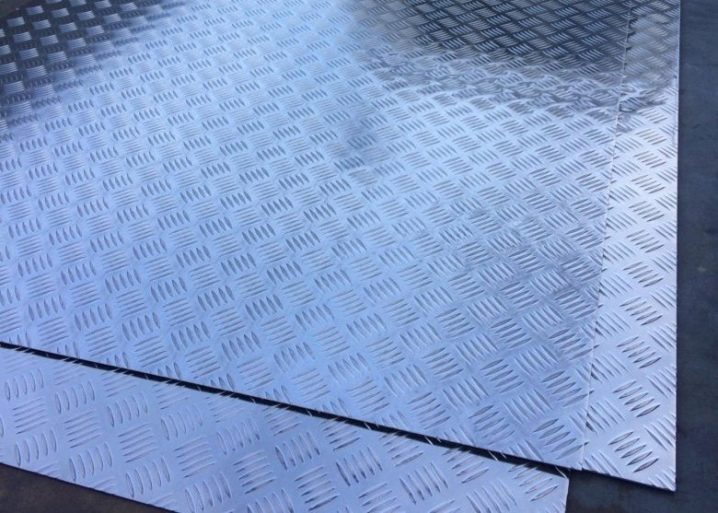
Billboards - artistic decoration: the texture of the billboard on which the advertising picture is applied may contain repeating convexities and concavities of the same design. This attracts the attention of a potential buyer / payer.
Decorative fencing: corrugated sheet is used along with punched sheets. It is also used as a decoration for the ceiling, walls - in the loft style ("attic" style with prominent beams) or high-tech (shiny surfaces, the minimum number of colors, clean lines and functionality, for example, a subscriber call panel mounted in the wall flush with its covering "quintet").
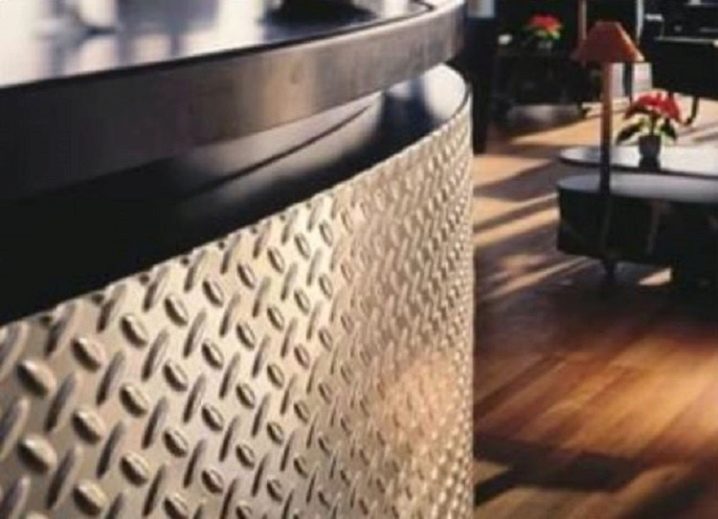
Aluminum and steel suspended ceilings, distinguished by their capital (durability) performance, allowing multiple re-installation, transfer, and also to prevent slipping from hands during installation, are made with a ribbed-convex texture of various designs. There are thousands of options for embodying a texture pattern: they can be changed on one sheet or block in any sequence, while a dozen or more uniform textures are applied to one sheet.
Aluminum sheet with a thickness of 3 mm or more is a material for a store or exhibition shelf-rack.
It is also used as a vertical stand, where on suction cups - for smooth areas lying between the bulges - you can attach, hang any light objects and tools.
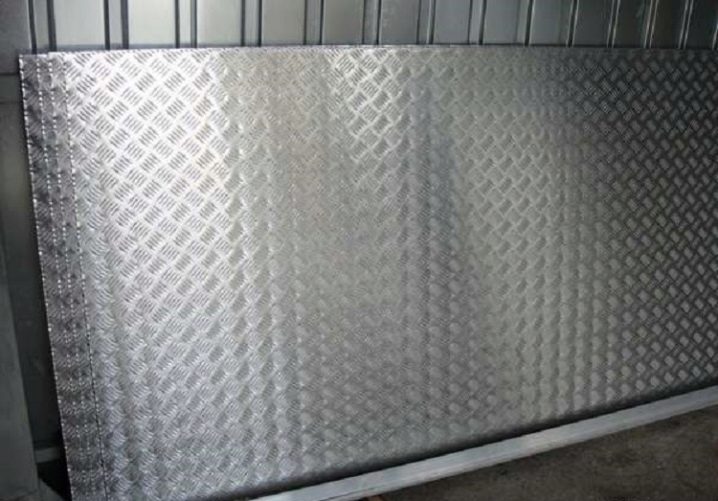
An amateur car tinting implies the manufacture of roofs, hoods, and car doors from steel sheets with a similar texture. A typical example is the tailgate. At the request of the customer, such sheets are coated with zinc, aluminum or chrome to protect the product from rusting.
Aluminum sheets, including those with a corrugated texture, are used as outer skin of ships and tankers. Aluminum is insensitive to the corrosive effects of fresh water in rivers. Salted sea water does not have a noticeable destructive effect on it, since it never reaches high temperatures.
To make sure that there is no corrosive process, look for aluminum pots, pots and pans that last up to a hundred years without a noticeable decrease in the thickness of the material. The corrugated sheet manifests itself similarly.
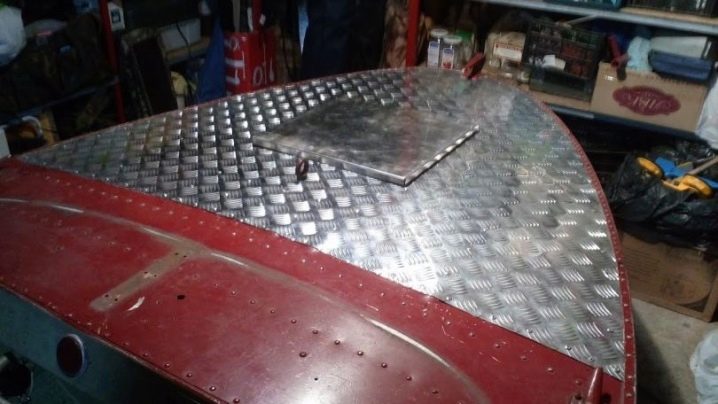
The comment was sent successfully.