Which is better - chipboard or MDF?

Chipboard and MDF - 2 popular materials that are used in furniture production and construction. Visually, they are very similar, but there are significant differences in technical characteristics and properties.

What it is?
MDF gets its name from the English abbreviation MDF, which translated into Russian means "finely dispersed fraction". Decoding laminated chipboard - laminated particle boards. Materials are manufactured using different technologies, due to which they have different properties.


Chipboard
This is a common particle board (chipboard) covered with a laminated film. The main raw material for its production - waste from wood processing enterprises. It can be:
- crooked trunks;
- knots;
- branches;
- scraps generated in the process of sawing logs and when trimming sawn timber.
The wood is cleaned of bark and fed to shredding units, for example, rotary knife shredders. This is how shavings are obtained. Its average thickness is 0.5 mm, its width is no more than 5 mm, and its length is about 40 mm.
During the production process, the shavings are subjected to drying in special cells, and then calibration... After preparation, the raw materials are fed into the mixers that work continuously. There it is mixed with binders. Next stage - entry of viscous mass into molding equipmentwhich forms a 1-3 ply carpet. He goes to pressing. At squeezing the workpiece a pressure of 40 kg / cm3 and a temperature of up to 220 degrees are applied.

Formed and dried this way slabs go to cooling chambers... After that, the edges of the material are leveled, the cut is made according to the specified dimensions. Chipboards polished, thanks to which they become even and smooth.
Next stage - lamination. It is performed in a specific sequence:
- gluing 1-2 layers of paper onto the base (the first should have a maximum thickness of about 0.5 - 1 mm, so that in the future it will be possible to push the drawing);
- laying a layer of transparent paper and mixed resinous substances;
- applying the main layer to the chipboard plate and pressing it with a stamp with a pattern, gluing the decorative layer in the same way;
- gluing with a stamp of a protective layer that protects the product from various contaminants.


MDF
For the manufacture of MDF boards, raw materials are prepared in the same way as in the production of laminated chipboard.
- Chips are made from wood waste, dried to a moisture content of 9%.
- Then it enters special cyclones, where large chips are screened out due to air separation.
- The calibrated chips are heated and pressed under high pressure.
- In the process, due to the strong heating of the wood fibers, natural resins (lignin) are released. Thanks to these substances, the chips adhere firmly to each other.
- The MDF boards obtained after pressing are cooled and polished to give the surface smoothness.
- After that, the products undergo further processing - they are sanded, laminated or varnished.
And also manufacturers produce more expensive material - veneered... It involves gluing a thin layer of natural wood to the surface of the slabs.


Pros and cons of materials
MDF and chipboard have several similar advantages.
- Variety of colors. Both materials can have a variety of colors, from light delicate to bright. They imitate natural and artificial stone, wood and other natural materials.
- Versatility. These 2 types of slabs are used for the manufacture of furniture, they are used to decorate the facade of building structures, and are used for interior cladding.
- Hygiene. Both plates are resistant to the formation of fungus, microorganisms that can destroy the base of the material will not start in them.
To their disadvantages include easy flammability. Products made of MDF and laminated chipboard are capable of catching fire upon prolonged contact with hot objects, with short-term exposure to open fire sources. Often the cause of fires is faulty wiring near particle board furniture. Another "common" drawback is poor resistance to mechanical damage. If heavy objects are hit or dropped onto the slabs, dents will form on the slabs.
Cons inherent in laminated chipboard - impossibility of milling, low strength, risks of chipping during processing.
The disadvantages of MDF are its complex processing.


How to distinguish visually?
MDF and chipboard are outwardly different from each other. If you look at them in section, then the fine fraction will look homogeneous and more dense. Small voids and large fragments of chips are visible in laminated particle board.
The main differences in characteristics
Despite the external similarity, chipboard and MDF have a significant difference in some technical parameters and performance characteristics. To find out the differences, you need to make comparison by various indicators.


Strength and density
Chipboard is lighter than MDF. It has a low density - from 350 to 650 kg / m3. The value of the indicator is influenced by the type of raw material and the percentage of sawdust mass to adhesive components. MDF boards have a density of 700 to 870 kg / m3.
Due to their higher performance, they are stronger and stronger than laminated chipboard.
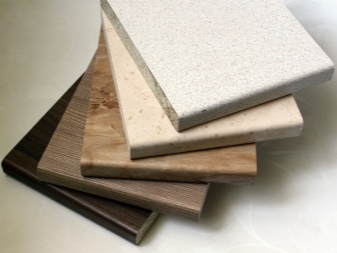

Moisture resistance
Chipboard without an outer protective shell is not resistant to high humidity. Upon contact with water, the material gets wet and swells - in this case, its volume can increase up to 25-30%. The deformed material practically does not recover when it dries. Laminated chipboard is more resistant to moisture, however, if the protective layer is damaged and it gets wet, damage to the product cannot be avoided... MDF has better moisture resistance.
Untreated material can get wet and not swell due to the high volumetric content of natural resinous substances.

Durability
Furniture made of laminated chipboard and MDF differs in terms of service life. Products made from finely dispersed slabs will last longer. They withstand high humidity, short-term exposure to hot objects and various adverse environmental factors. When furniture is made of laminated chipboard, joints are formed between the laminate film and the edge of the board.
Over time, in these places, furniture crumbles, which may require replacement.


Environmental friendliness
In production Laminated chipboard adhesives are used, which contain formaldehyde... This substance releases harmful components into the environment, and when heated, the intensity of their vapors increases. MDF is made using natural resins, making the material safer for health.


The last compared indicator is price... MDF is of higher quality, denser and stronger than laminated chipboard, respectively, more expensive.
What is the best choice?
For furniture manufacturers, laminated chipboard and MDF are in almost the same demand. However, when choosing products from a particular material, it is necessary to take into account the upcoming operating conditions (expected power loads, humidity, temperature effects).

For kitchen
Modern kitchens can be made from particle board or wood fiber panels. Furniture made of laminated chipboard is considered to be of poor quality. Under the influence of moisture, it will quickly lose its visual appeal. Fine grain kitchens are more reliable, stronger and more durable, but they are too expensive.
To make the headset cheaper, it is recommended to purchase a combination product. It is best if the facades, vanity units and sliding doors were made of MDF.
Such material will not deform and will last a long time.


For bathroom
MDF and laminated chipboard are wood-based boards from which budget furniture is made. For this reason, they are often used in the manufacture of bathroom products. However, neither MDF nor chipboard panels are suitable for use in the bathroom. Too difficult conditions are noted in this room - excessive humidity, temperature drops, regular exposure to water. Even a moisture-resistant fine-grain stove in such conditions can soon lose its perfection in appearance.
If there is no other choice, experts recommend opting for MDF furniture... At the same time, it is worth giving preference to high-quality products with processed edges and ends. Products with a thin melamine tape are not suitable for the bathroom - during use, cracks are easily formed on it, through which moisture penetrates. Getting under the protective film, it leads to deformation of the furniture.
Conscientious manufacturers in the production of quality furniture use a thick and durable PVC sheath, which is difficult to damage. If the budget is limited, you can take a closer look at the chipboard models, but in this case you need to pay attention to the labeling. Bathroom products should be made of chipboard with increased moisture resistance. Such materials are marked "B". They are made using paraffin wax.
The component helps to create a protective film on the surface of the board, the task of which is to protect furniture from water penetration.


For the nursery
Arranging a children's room, it is best to stay on furniture made of safe MDF material. Chests of drawers, wardrobes, shelves, desks, beds or sofas are made from it. Due to the evaporation of formaldehyde, furniture made of chipboard can cause allergies, dizziness and other health problems in a child. It is not recommended to purchase furniture made of particle board for children under the age of 7.
If the child is over 7 years old, you can equip the room using combined furniture items.


For bedroom
In this room, a person spends a lot of time at night, therefore, when choosing furniture, it is worth first of all taking into account its safety for health. MDF products are more environmentally friendly, which is why they are preferable. However, to save the budget, many people prefer chipboard furniture. In this case, you need to look at the quality certificate of the slabs. They can have 2 classes - E1 and E2.
Furniture with an E1 class is considered safer due to the lower formaldehyde content.
In the production of E2 panels, a larger volume of formaldehyde compounds is used, which is why they more intensively emit harmful substances into the environment.


For the living room and hallway
In these rooms, wardrobes, tables, slides and furniture for relaxation made of MDF or chipboard are often installed. If there is no need to save money, you can furnish the corridor and living room with furniture made from MDF panels.
With a limited budget, it is worth taking a closer look at combined options or products from laminated chipboard with class E1.


Review overview
Furniture made of MDF and laminated chipboard is popular due to its budget and good performance properties. Such products, in comparison with analogues made of natural wood, will cost significantly less. Other benefits for consumers include:
- a good range of colors of PVC films, juicy and bright colors;
- easy assembly (fasteners are screwed into the material without effort using a screwdriver);
- quick installation;
- easy care - to maintain cleanliness, it is enough to wipe the dust from the surface with a soft cloth; in case of heavy dirt, it is allowed to use detergents without abrasive particles;
- lack of unpleasant odors.
From disadvantages consumers highlight the fragility and unreliability of too cheap furniture. For example, many people note that the shell, which is pasted over the facades of budget kitchen sets, peels off when exposed to high temperatures and quickly absorbs dirt. Another disadvantage is the impossibility of making furniture with convex surfaces. Facades made of laminated chipboard and MDF are flat, without concave or wavy facades.


You can find out about the difference between MDF and chipboard in the next video.
The comment was sent successfully.