All about sand concrete blocks
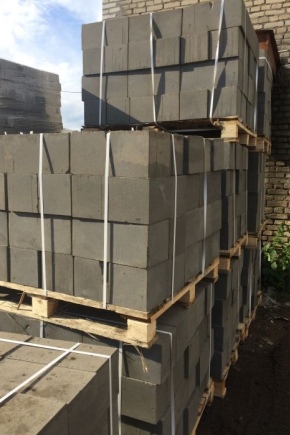
Sand concrete blocks - solid wall and hollow, 200 × 200 × 400 and other sizes - are widely used as a material in low-rise and commercial construction. Their weight allows not to increase the load on the foundation too much. About how the selection and laying of sand concrete blocks is carried out, about their advantages and disadvantages, it is worth learning in more detail before choosing this building material for work.
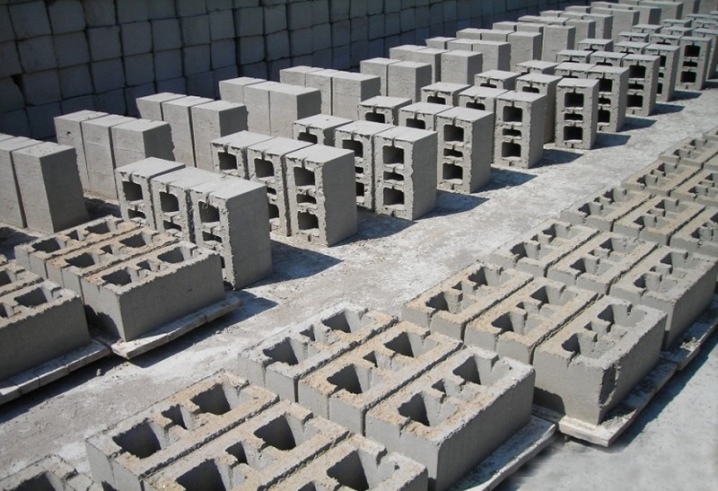
Advantages and disadvantages
Sand concrete blocks belong to the category of molded building materials with clearly defined geometric parameters and characteristics. They have many advantages that determine the choice of builders in favor of just this type of artificial stone.
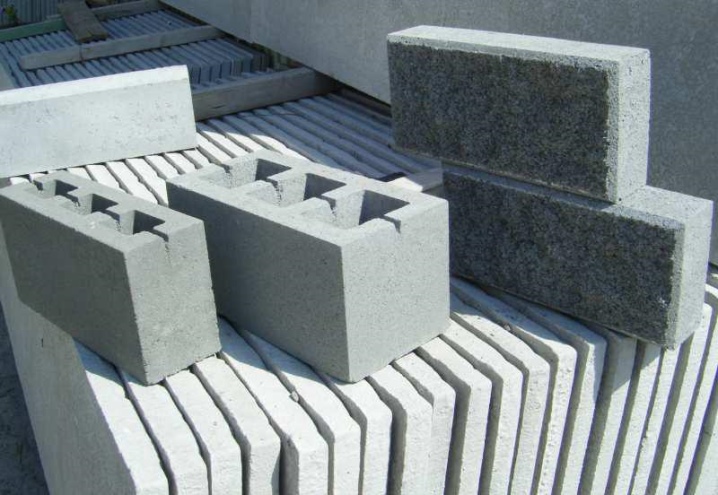
Let's list its obvious advantages.
- Resistant to moisture. It allows you to guarantee the protection of the structure from the influence of external factors.
- Excellent strength characteristics. This even applies to building blocks. In addition, improved sand concrete products, reinforced with polypropylene fibers or fiberglass, are on sale.
- Life time. Manufacturers guarantee the preservation of the characteristics of the material for 60-100 years from the date of its release.
- Heat insulating and sound insulating properties. They are higher in hollow variants, monolithic in this indicator is quite comparable with ordinary concrete. When choosing a suitable option, it is important to find a compromise between the thermal insulation properties of the material and its strength characteristics. In addition, hollow blocks have better sound absorption properties.
- Biological resistance. Sand concrete products are not subject to deterioration under the influence of fungus, mold.
- Fire resistance. Upon contact with an open fire, the material retains its properties for 10 hours.
- Eco-safety. The sand blocks do not use components that have a negative impact on the environment. During operation, the structure remains completely safe for health.
- Economic benefit. A structure made of sand blocks during construction is 2-3 times cheaper than a brick analogue.
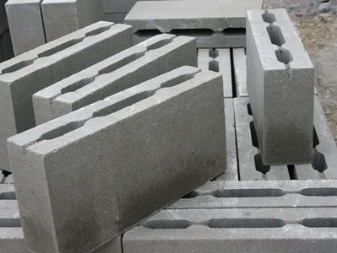
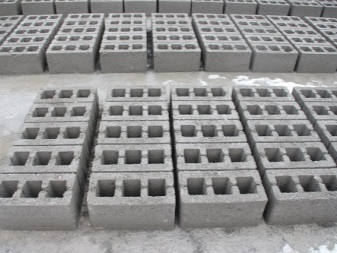
Like any other material, sand blocks also have certain disadvantages. The blocks are pretty heavy - this can complicate the masonry process, affect the design loads exerted on the surface of the foundation. The blocks contain no porous fillers, therefore, they retain heat worse than expanded clay concrete. When used in residential construction, additional thermal insulation will be required.
Low vapor permeability. It affects the air exchange in the room. In the absence of properly organized ventilation, the premises will be stuffy, moisture will begin to accumulate, and the microclimate will worsen.
In addition, the lack of strict quality control leads to the fact that the material from different manufacturers differs markedly in their properties.
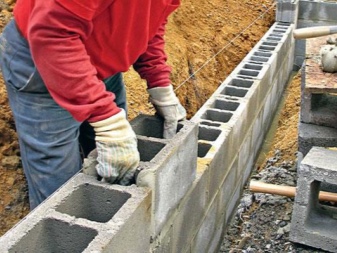
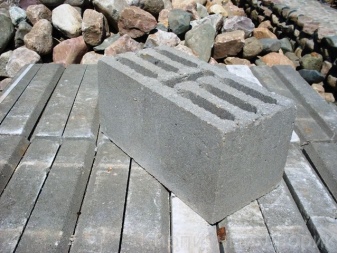
Main characteristics and dimensions
Sand blocks are a material made from a mixture of cement, sand and water. In addition, the composition may include additional ingredients that modify it, providing greater plasticity of the mixture. Production is carried out by vibrocompression of the solution.Depending on whether sand concrete is intended for walls or masonry foundations, it is made hollow or solid.
The weight of the products depends on their size and composition. On average, a molded artificial stone has a mass of 23 kg per element. The standard block sizes are:
- 390x190x188 mm;
- 200x200x400 mm;
- 100x200x400 mm.
The density of sand blocks reaches 1300-2200 kg / m3, they are quite heavy, while the compressive strength is also high, reaching 100-150 kg / cm2. The material is quite attractive for construction work, but it is not often found in multi-storey construction. This is due to the significant associated costs for the arrangement of ventilation, vapor barrier.
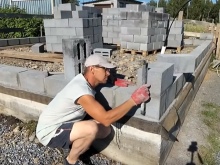
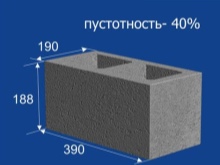
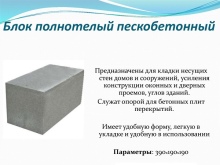
Views
All sand blocks are classified based on their purpose and characteristics. The manufacture of these materials is not as strictly standardized as is the case with bricks or other elements. General requirements are determined based on GOST 13579-78 and GOST 6133-99. They have only functional significance - no colored or decorative varieties are produced.
By their structure, all sand blocks are divided into two types.
- Hollow. They have cavities inside that reduce the weight of the product, affecting its heat-insulating, sound-insulating properties. Double-hollow blocks can have through or incomplete holes in the form of slots, cubes, cylinders. And also the number of holes can be 4, 6 or 8.
- Corpulent. These are classic blocks formed by vibrocompression. The structures of these products are more massive and require additional insulation. That is why they are more often used for the construction of utility buildings - garages, sheds.
Another method of classification involves the division of elements according to their purpose. The options presented here are more varied.
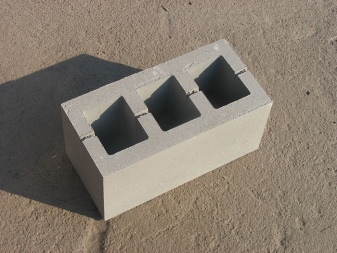

Wall
The main group of sand blocks used for masonry of external walls bears this name. They are also called ordinary ones, since on top of the masonry, the structure is necessarily covered with decorative trim. These blocks have the simplest form and are cheaper than the others. The structure of the material can be hollow or solid.
This does not in any way affect other properties and characteristics of the product, its purpose.
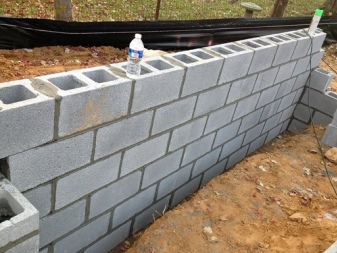
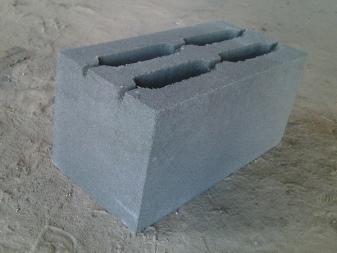
Partition
Sand blocks for partitions inside buildings and structures are produced with a thickness of only 10 cm. They have the same shape as ordinary ones, they can include voids, but more often they become full-bodied.
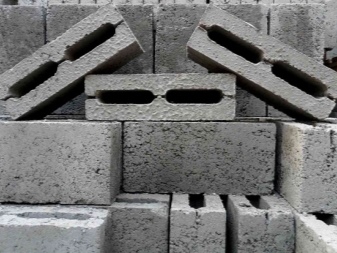
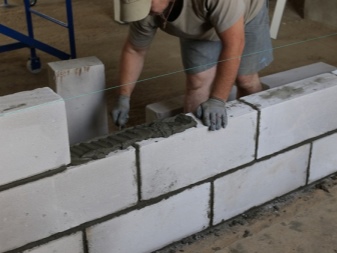
Facing
These sand blocks are also referred to as front sand blocks. They can have 1 or 2 sides without finishing. Usually this is a sidewall and an end. Masonry from such blocks does not need additional work. By the type of finish, the coatings can be rough or sanded, smooth and grainy.
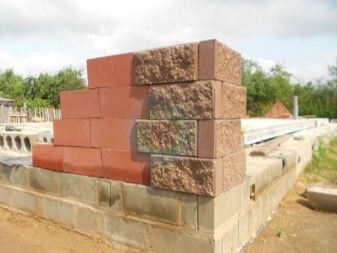
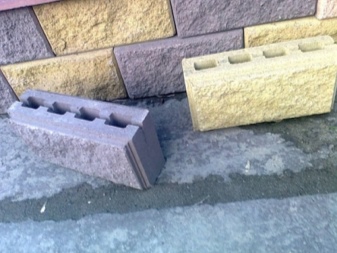
Fundamental
Sand concrete blocks of this type are intended for laying plinths and foundations. They are produced both in full-bodied and in a hollow version, marked as FBS or FBV. They provide the necessary strength and reliability of the base, they can have additional polymer or reinforcing additives in their structure.
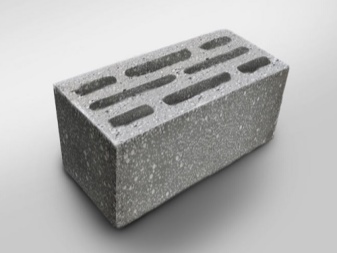
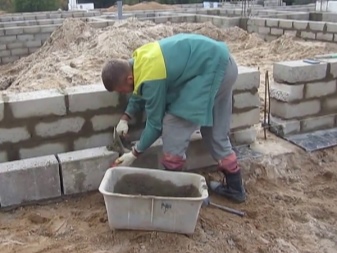
Manufacturers
Many large enterprises, as well as private companies, are engaged in the production of sand concrete blocks on the Russian market. In the Moscow region, you can purchase the products of the plant "Stroma"producing hollow and solid products. Partition and foundation modules of this type can be found from the company PC "MosCentreStroy". You can also find the right product from the companies "Osnova-M", "Pushchinsky plant".
In the regions with the production of sand concrete blocks, everything is also in order. One of the major suppliers is considered Ecostroy LLC from Kineshma in the Ivanovo region. It has its own factories in Moscow and Kaluga Trust-Snab... No less known to builders and Tula precast concrete plantproducing blocks of different types.
The SIBIT company is of particular interest among the Siberian suppliers.
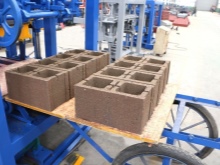
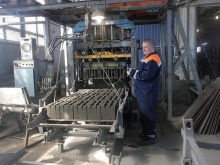
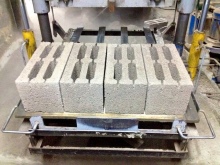
Scope of application
Sand concrete blocks are versatile. Products with a thickness of 200 mm are suitable for the erection of external walls of multi-storey buildings, thinner ones are used as internal partitions. Among the structures, the construction of which can be carried out from this material:
- fences and barriers;
- low-rise houses, cottages;
- separate parts of buildings - basement, foundation;
- gazebos with a barbecue area;
- agricultural buildings;
- supply ventilation systems;
- garage boxes and complexes.
Regardless of where and how exactly the sand concrete block is used, it provides high structural strength. The material is suitable for the construction of large hangars, commercial buildings, multi-storey business complexes.
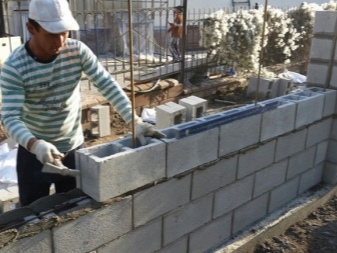
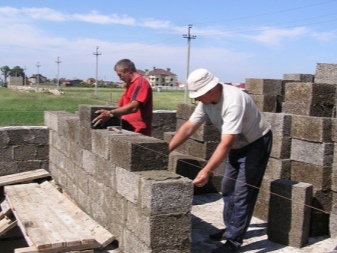
Masonry tips
You also need to be able to put sand concrete blocks correctly. It is important to prepare the tools that you may need: trowels, mallets, trowels of a suitable size. You will need measuring devices, a plumb line and a cord to check the level. Laying can be carried out on a conventional cement mortar based on the M400 grade. When mixing it yourself, you need to ensure the homogeneity of the mixture, remove all lumps from it.
The material is purchased and delivered to the place of work. After preparing the solution, you can proceed to its laying.
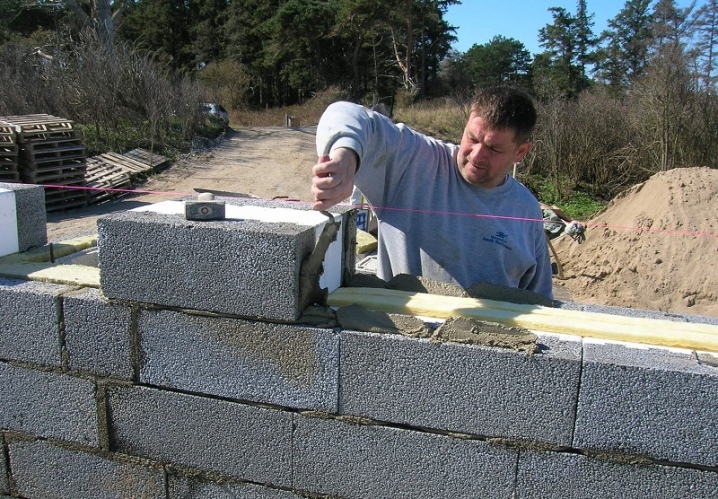
The procedure in this case is the same for all types of concrete blocks.
- Marking. It is carried out using a cord. It is necessary to mark the corners, as well as the horizontal line of the walls.
- First row masonry. A solution is placed on top of the waterproofing material. A block is installed on it, pressed against the base.
- Joining. Its type is determined by what kind of finishes are chosen for use.
- Continuation of the masonry. Adjacent elements in the same row are laid on the mortar, fastened with it. Subsequent levels are located without offset. In every 3rd row, polyurethane foam is used instead of a solution; after 5 levels, reinforcement with metal rods or mesh can be performed.
- Formation of an armored belt. It is done on the last row, in the formwork, with concrete pouring. The mixture hardens under the film for up to 7 days.
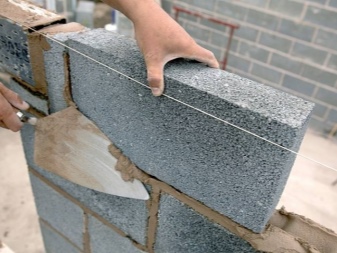
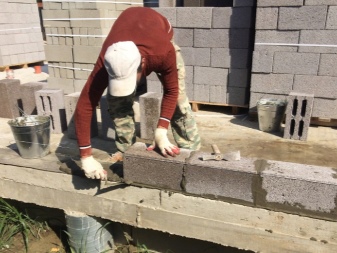
Upon completion of the masonry process, you can start finishing the external and internal surfaces of the erected structures. Experienced builders recommend that before starting the installation of blocks, treat their surface with a damp brush. The fishing line will help to get a clear line in the outer corners - it is pulled between the edges. Jumpers are also better to replace with corners.
It is most convenient to lay the solution on the side surfaces of sand blocks with a trowel, but you can also do this by firmly rubbing the edges of artificial stones to each other. It is possible to cut out individual elements during the laying process with a grinder. To obtain thinner joints, you can replace the cement mortar with a special adhesive.
This will further improve the thermal insulation properties of the finished structure.
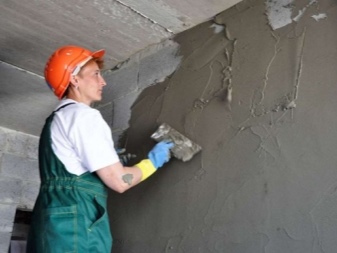
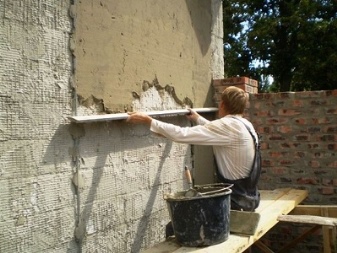
For information on what to look for when choosing sand concrete blocks, see below.
The comment was sent successfully.