All about Volma tongue-and-groove slabs
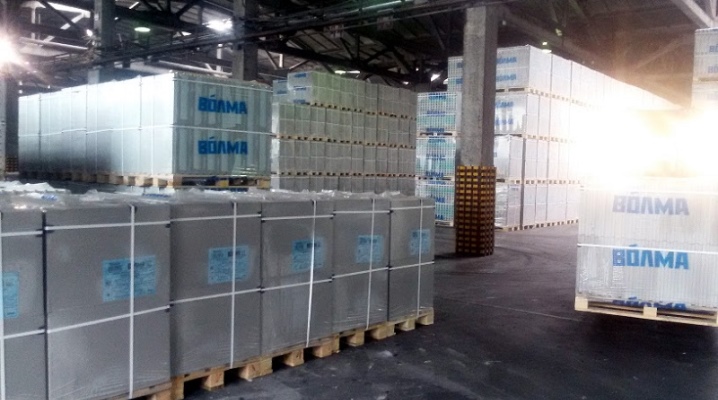
Information about the Volma tongue-and-groove slabs can be important for a person who has decided to start building and improving his own home. The manufacturer can offer full-bodied moisture-resistant PGPs 667x500x80 mm, 667x500x100 mm and hollow ones with a thickness of 80-100 mm. But even if blocks of other characteristics are selected, it is necessary to ask what they are used for and how they are mounted.
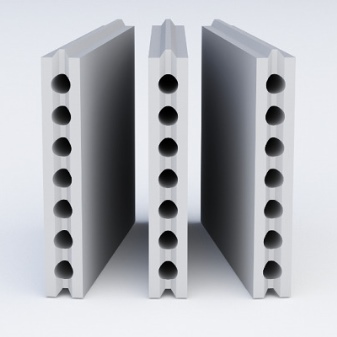
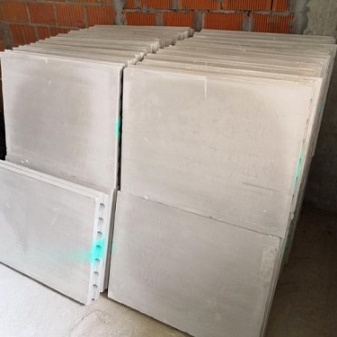
Peculiarities
Volma tongue-and-groove slabs (PSP) are excellent for the construction of interior walls in houses and administrative premises. A typical property of such products is the monolithic design in the form of a rectangular parallelepiped. The accuracy of the dimensional characteristics of tongue-and-groove blocks is very high. Such constructions are processed without any problems. Since the main structural element is gypsum, there is no need to be afraid of any toxic effects.
GWPs do not burn at all and do not contribute to the spread of fire. The acidity of this material is almost the same as the acidity of human skin. Ordinary gypsum plaster from Volma does not emit foreign odors and does not absorb them.
In addition, it should be noted that such a material has dielectric properties, is excellent for air and water vapor permeability. Therefore, the accumulation of static charges, electric shock or disturbance of the microclimate in the room is excluded.
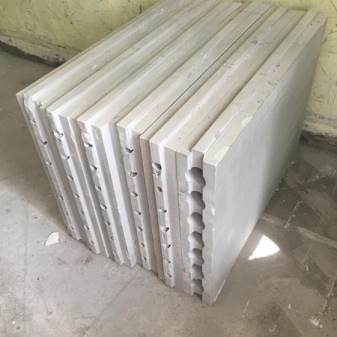
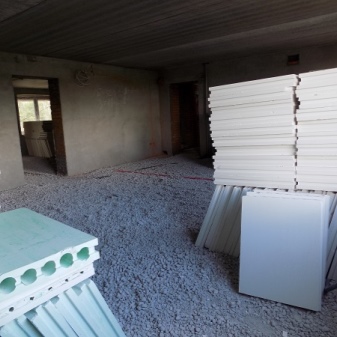
Tongue structures cannot rot - they are absolutely resistant to putrefactive processes. Deformation of the plates is also excluded due to temperature and humidity drops. It is customary to divide these products into hollow and full-bodied types. The decisive difference between the two is only related to mass. There is no particular difference in the quality of sound insulation and the convenience of forming partitions. Volma products are of very high quality. Their front surface allows you to completely eliminate plaster. Such products are compatible with any extraordinary design solutions. Installation and labor costs are kept to a minimum. The installation of the tongue-and-groove plate is mainly carried out by gluing.
The products themselves are made using an injection molding technique. The production technology is fixed in TU 5742-003-78667917-2005. The enterprise uses the latest European devices. In the process, plasticizers and hydrophobic components are added to the gypsum binder. The use of GWP "Volma" is allowed at any facilities with a dry atmospheric regime and complying with the standards of SP 50.13330.
Special branded glue allows for reliable installation even at negative temperatures.
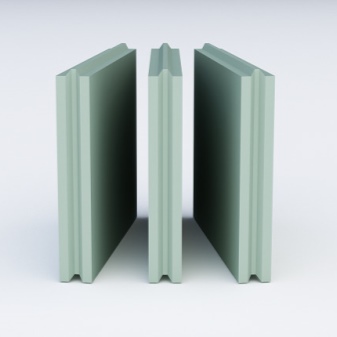
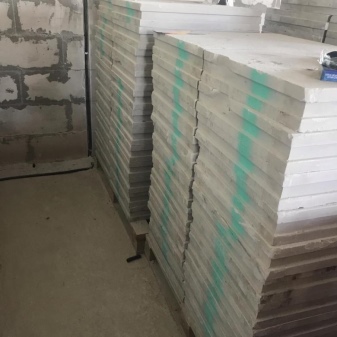
Model overview
Hollow
A good example of slabs with internal voids is the model with dimensions 667x500x80 mm. This product is completely safe. The maximum weight of one slab is only 22 kg. Installation during a shift is possible in the amount of 20 to 30 sq. m (per employee). From such slabs, it is possible to erect both single and double partitions.
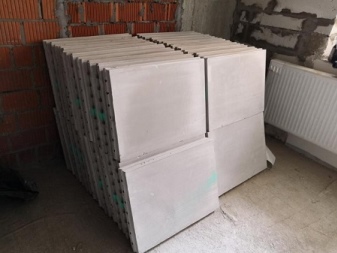
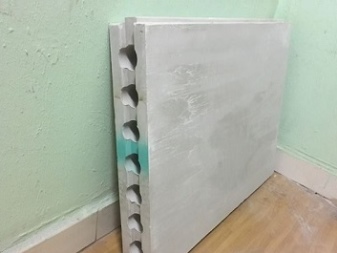
Corpulent
A simple full-size gypsum board with grooves and ridges has a size of 667x500x100 mm. But along with the product with a thickness of 100 mm, an 80 mm block is also supplied. Its weight is 30 kg. Larger specimens weigh up to 36 kg. Both hollow and full-bodied models have an accurate water-resistant counterpart with the same dimensional and weight parameters.
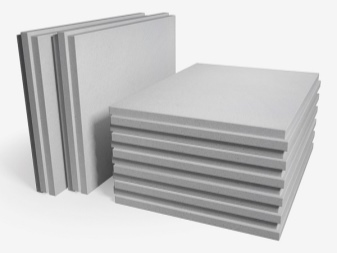
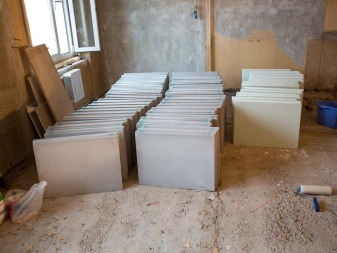
Comparison with Knauf
Comparing the products of a leading Russian manufacturer and a leading German concern is very instructive. Knauf products weigh 27-32 kg in full-bodied version. When using hollow blocks, the weight ranges from 20 to 22 kg. For moisture-resistant modifications, the weight reaches 30-32 kg. The durability of German goods is quite decent, and the level of thermal insulation is also pleasing. The thermal conductivity of the imported board meets all the basic technical requirements. The same applies to the quality of sound insulation. Water absorption fully complies with the standards set for each type.
The fire resistance of Knauf products is quite optimal. Experiments have shown that they can withstand temperatures up to 1200 degrees for 180 minutes. GWP Knauf is slightly heavier than analogues made in Russia. They do not cause any special consumer complaints. But at the same time, German plates are quite expensive if you take into account the cost of adhesives. Volma's products are in no way worse in terms of technological parameters.
If we also take into account the price parameters, the Russian plates turn out to be much better.
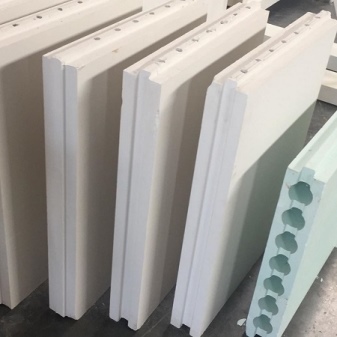
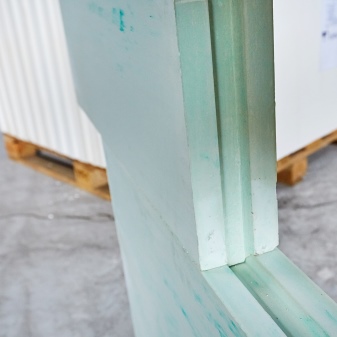
Application and installation
In addition to the partition blanks themselves, for the separation of the premises it is necessary to prepare:
- special primer;
- mounting glue;
- wide spatulas;
- spatulas for external and internal corners;
- gypsum-based putty;
- mounting foam;
- dowel-nails;
- self-tapping screws;
- straight type suspensions or mounting angles;
- mallet hammer;
- building level.
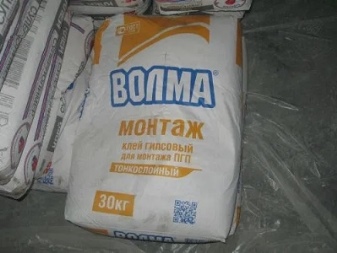
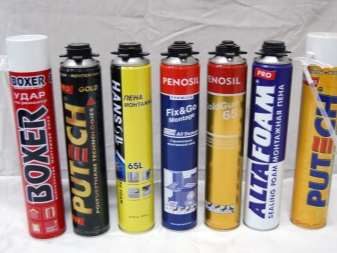
The most important requirement of the technology is a reliable, solid foundation. It is better to spend time and money on filling leveling, than to face problems. But even if there are no problems, you need to at least remove all the dust and dirt. Only after that you can proceed to the installation work itself. The instructions always pay special attention to the level of adhesion of the materials. A primer helps to improve grip. It will have to be applied to all contact surfaces. Next, you will have to wait until the soil layer is completely dry. When this happens, they make the markup, and then prepare the working composition. Any plaster-based assembly preparation is suitable for this purpose.
Taking care of sound insulation plays an important role. It is recommended to attach the partition to the base through an "intermediary" - an elastic material with increased porosity. Cork is a good option. But if protection from extraneous sounds is not important, you can ignore this stage. Installation of tongue-and-groove plates is performed in rows.

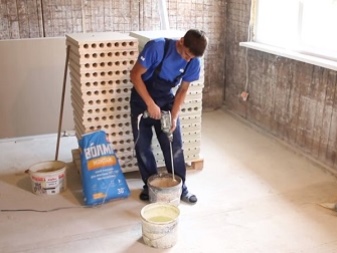
The initial tier is placed from the wall on top of the assembly composition layer. Plates can be positioned by orienting the groove both up and down. In order for the structure to be of high quality, the vertical and horizontal planes are adjusted according to the level. Before installing the next slab, an adhesive layer is placed on its base and on the upper edge of the lower tier. Starting from the second level, the entire masonry is sequentially trimmed with a mallet - this is the only way to finally level everything.
The completion of the formation of the partition usually means the use of part of the slab. You can get it by simply sawing the block with a hand saw. From the very beginning of the installation of the second row, the vertical separation of the joints is monitored. This significantly increases the overall strength of the masonry. Plates are attached to the walls and to the bases (at this moment, corners, screws, dowel-nails will be needed).
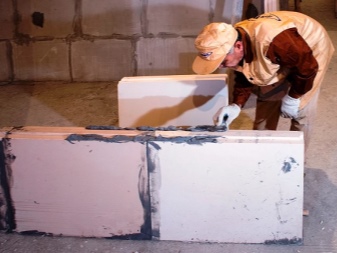
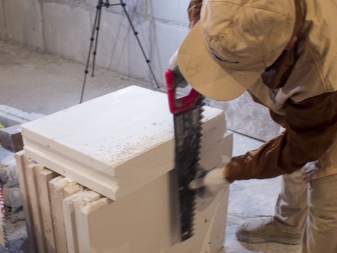
The final row is installed, making a gap of at least 15 mm from the floor slab. The rest of the gap is filled with polyurethane foam. As soon as its excess is cleaned out, the seam is covered with a gypsum-based putty. Finishing is done primarily to protect the outer corners of the partition. The corner profile 31x31 mm with perforation can help in this. The inner corners will be protected by a reinforcing tape. Gypsum plaster is applied to each corner. Its layer will provide the final leveling of the surface. To lay electrical wiring or wiring accessories, use the cavities provided by the designers.As needed, they are expanded with a drill using a crown.
The same tool will allow you to prepare external recesses for the wiring output. Before using paint or other decorative coating, the seams must be cleaned. Both along the seams and along all the differences in the relief, they are covered with plaster putty. Additionally, you will need to prime the surface. Installation of shelves, plumbing fixtures on a slab partition is done in the same way as on other stone walls.
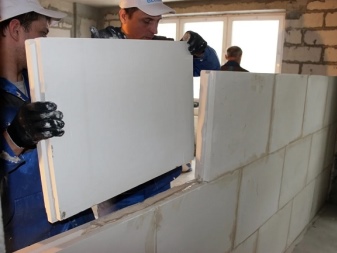
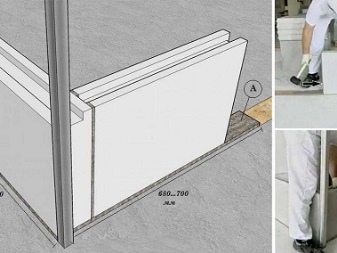
The upper row of slabs above the door opening is formed using a mortgage. To solve many problems with puttying timber, double-sided sheathing with plasterboard sheets helps. The width of the timber-drywall assembly should be slightly less than the GWP. Having prepared the opening in height, the timber is placed directly on the Volma-Montage. Having attached slabs to this beam, you can then go over them with a net and cover with putty.
The final row is usually placed vertically. This is important to reduce the amount of trimming. This approach is practiced in cases where the height allows you to put solid tiles. Additional clearance is 2-3 cm. Plaster can be used to mask the polyurethane foam. First, a small amount of the mixture is applied to the level of the board on one side. Then you have to wait for the mortar to set. When it hardens, the middle of the zone from the stove to the ceiling is foamed.
This leaves a place where you can apply the plaster from the other side. As soon as the foam hardens, the remaining area is finished with plaster.
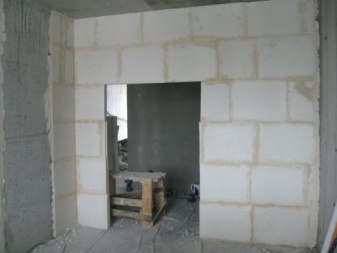
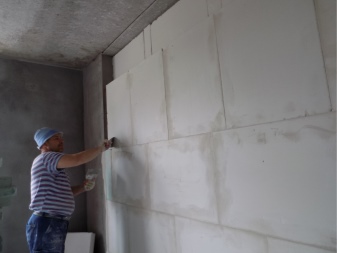
In the next video you will see the technology of installation of Volma tongue-and-groove slabs.
The comment was sent successfully.