Characteristics of minerite slabs for a bath and their application
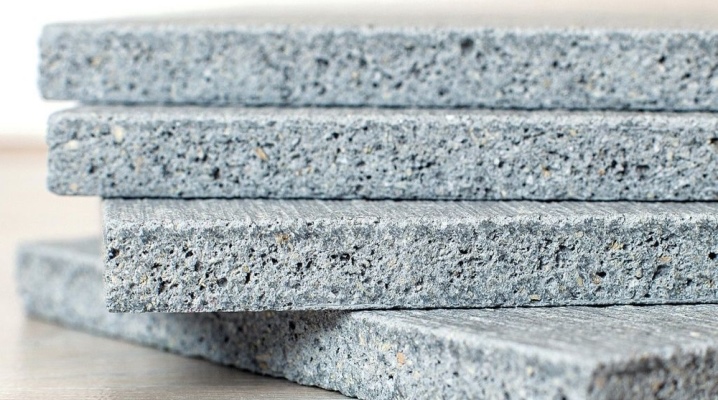
The multifunctional cladding material of the new generation, minerite, was invented at the end of the 19th century by a native of Austria, Ludwig Hatcheck. It is used for finishing facades, insulating wooden walls from fire and high temperatures. It is obtained by pressing from cement mortar, reinforcing fibers and mineral additives.
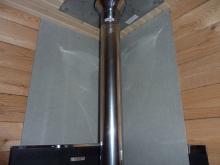
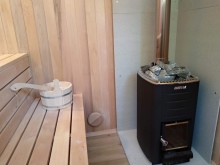
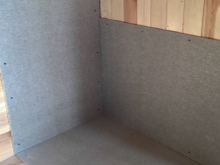
Specifications
The bathhouse can be classified as a fire hazardous facility. As a rule, the walls for the bath are made of wood, a stove is built inside for heating to enhance the formation of steam, a heater is added. In this case, reliable insulation of wooden walls is required. Due to its increased resistance to environmental influences, minerite sheet is an irreplaceable insulating material for a bath.
It has fairly safe properties, since it does not contain asbestos, and when heated, it does not emit substances toxic to humans.
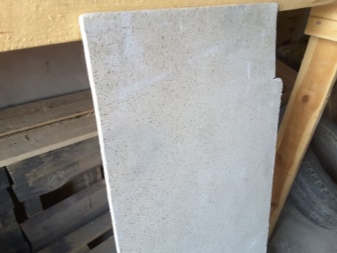
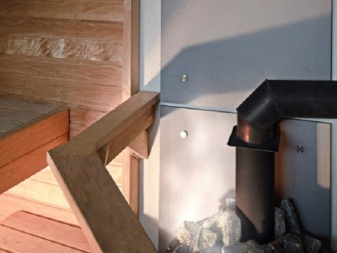
Minerite slabs contain:
-
up to 60% cement,
-
10% cellulose,
-
from 20 to 40% minerals.
Components, fillers and colorants change depending on the required properties.
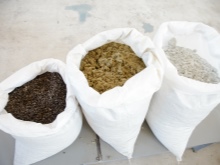
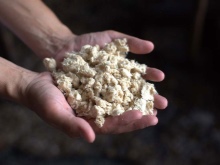
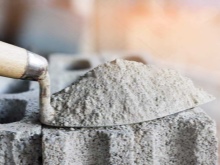
Let's list the main technical characteristics of minerite.
-
Fire resistance. Plates withstand temperatures from 150 ° C to 400-600 ° C, therefore, fire-resistant partitions are installed between the wooden walls and the stove, as well as stoves are mounted on the walls.
-
Lightness, strength and durability. Under the influence of strong loads, the slabs do not deform. They have increased impact resistance.
-
Thanks to the combination of components such as cement and mineral fibers, the material has sufficient moisture resistance. Cement is resistant to attack by fungi and mold, prevents rotting and decomposition.
-
Shows resistance when exposed to aggressive reagents, acids and alkalis.
-
It absorbs sound well, therefore it can be used for sound insulation.
-
Naturalness and environmental friendliness, which guarantees the absence of harmful emissions when heated.
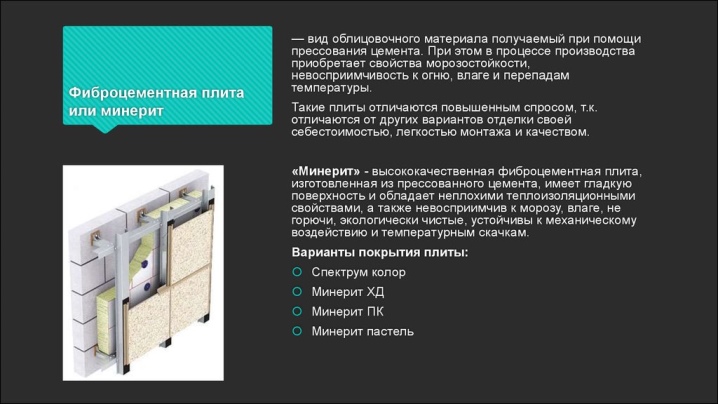
Minerite slabs are used not only as a refractory layer, but also in those places where decorative finishing near fireplaces and stoves is required. For this purpose, textured slabs are made that look like brick or masonry.
Decorative minerite can be of different colors, the standard thickness of the decorative sheet is 8 mm.
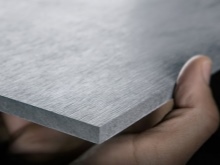
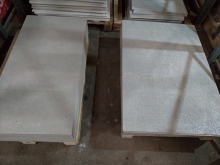
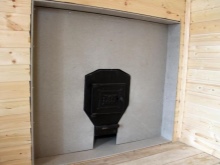
Application
The universal properties of a fiber cement board determine its versatility.
Fire resistance and resistance to high temperatures allows the use of minerite as an insulating material. Protective screens for the LP Sauna minerite stove are installed in baths, saunas, near fireplaces and stoves. They provide complete fire safety in the premises. With the help of minerite sheets, shielding of protected escape routes of people in the event of a fire is carried out, as well as the delimitation of zones in the premises.

There is a more heat-resistant version of minerite - superisol. Such plates can withstand temperatures up to 1000 ° C.
A technology has been developed for mounting the surface of walls, ceilings, chimneys and ventilation ducts in rooms with an increased fire hazard. Plates are installed on a frame made of profiles. When the stove is located quite close to the wall, the protective screen is installed directly on the wall, leaving a small gap of 30 mm using ceramic bushings.This will be a portal for air circulation between the protective board and the wood of the wall, preventing overheating of the wood.
Resistance to impact and mechanical stress is used in the construction of ventilated and non-ventilated facades. In this case, VZ minerite slabs perform a dual function of wind and water protection. These are the most dimensional sheets, usually they are produced in two categories - 90 and 120 centimeters wide and 2 m 70 cm long.
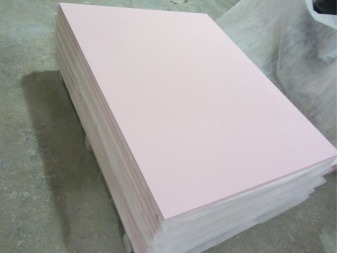
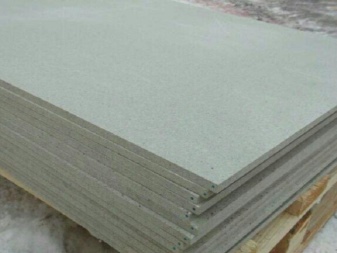
Universal plates with the designation HD are characterized by moisture resistance, strength, they are not afraid of temperature fluctuations.
Can be used for interior decoration of buildings and exterior cladding. The boards have a smooth surface on which finishing materials are easily applied. Along with polyurethane foam polyurethane, minerite slabs are used, if necessary, to create a very durable facade. The thickness of the HD minerite can vary from 3.5 to 10.5 mm. The most demanded sheets are 8 mm thick.
Facade slabs are designated PC. This is a universal minerite board, on one side it is applied with a layer of finishing primer, on the other side, acrylic paint is applied. Facade minerite is produced in 4 sizes.
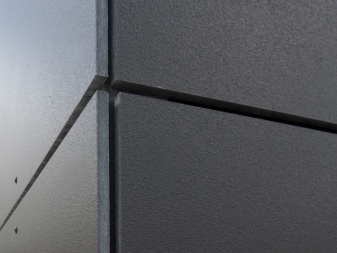
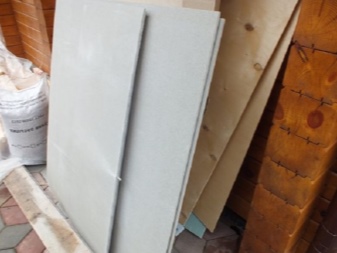
For cladding of facades, fiber cement boards "Pastel" are also used, which have a completely flat surface, processed by grinding, and painted in different colors.
To protect balconies and loggias, an MK plate is used, the main characteristic of which is increased strength and durability, moisture resistance and a self-cleaning surface.
The ability to retain moisture and prevent the development of fungal infections of the Aquablock SP slabs is used for waterproofing in shower cabins and swimming pools.
The installation of minerite can be accompanied by additional finishing with tiles or moisture-resistant wallpaper, or it can be used as an independent finishing material. Has many different colors.
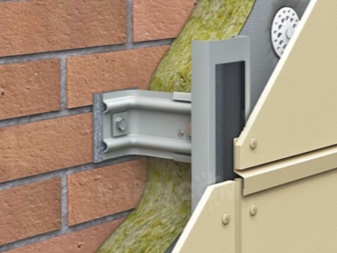
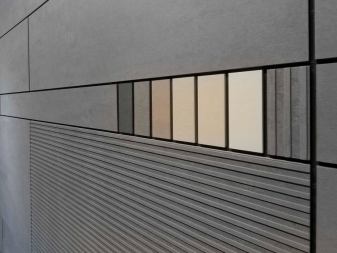
What can be replaced?
It is not always possible to purchase minerite slabs, especially for summer cottages and remote villages. Accordingly, the question arises: how to get out of the situation, and what can be used to replace the fiber cement slab.
For a long time, in the construction of baths, they used local materials that were found in the place of the settlement. The main characteristics for the materials separating the stove from the wooden wall should be:
-
low thermal conductivity,
-
security.
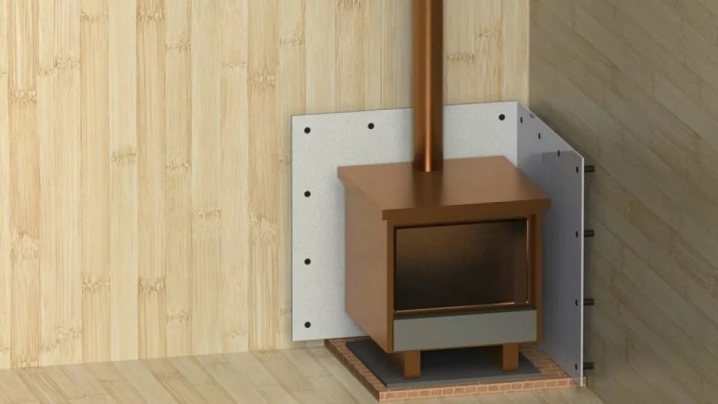
Among the home budget replacement options are natural stone, brick. Among the more common materials, you can use:
-
refractory gypsum board, penetrated with fiberglass, keeps the plate heating for 25 minutes, and fire up to 55 minutes;
-
a reliable option would be to install a stainless steel screen using a basalt wool interlayer;
-
fiberglass is characterized by the absence of harmful resins that evaporate when heated, easy to install;
-
another option is heat-resistant terracotta tiles, which are made from kaolin without dyes and chemical additives. It has good vapor permeability and can withstand temperatures up to 1100 ° C.
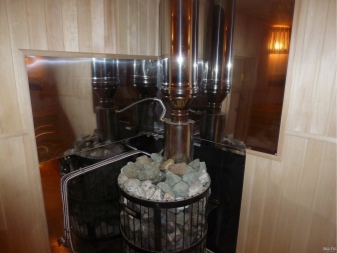
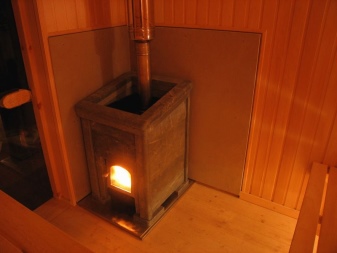
How to fix it?
Do-it-yourself installation of minerite slabs does not require special training. This requires a conventional screwdriver and self-tapping screws. Let's consider how the installation diagram of the protective screen looks like.
-
To install the minerite slabs in the protective screen, a metal profile is fixed to the wall both vertically and horizontally. The minerite sheet is fixed to the metal profile using self-tapping screws. For them, holes are drilled with a screwdriver larger than a self-tapping screw. Ceramic bushings with a height of about 3-5 cm are installed under the plate. Self-tapping screws are not completely clamped. Leave a little free play to increase when warming up. Fully self-tapping screws can be fixed only after almost a year of use of the screen.
-
The second sheet of the future screen is fastened with the same self-tapping screws, and again through the ceramic bushings. A small void should form inside the two sheets to prevent overheating of the wooden surfaces.
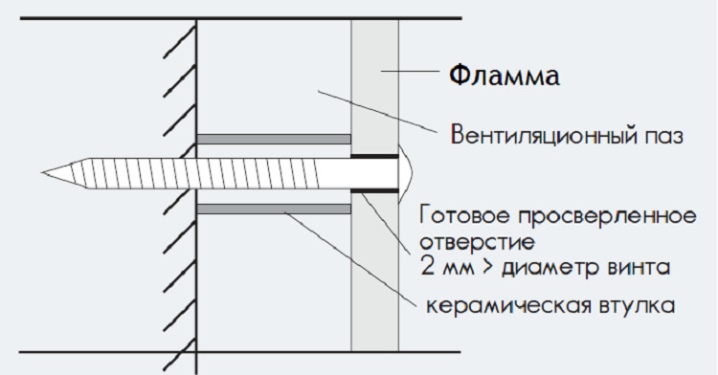
It must be remembered that it is impossible to install the stoves in the bath closer than 0.5 meters from the wall.
Installation of the stove in the bathhouse directly on the wooden floor is possible only with complete insulation of the wooden floor slabs. It is possible to install a minerite slab on a brickwork, when the bricks are not laid in a continuous layer, but with gaps through which air ventilation goes.
The comment was sent successfully.