Characterization and application of metallurgical slag
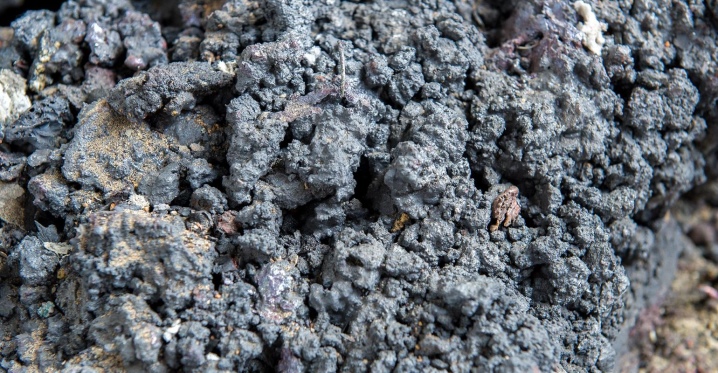
Metallurgical slag finds its application as a bedding for the road and in other fields of activity. Its composition and density, production features are of particular interest to industry. It is worth talking in more detail about what it is in metallurgy, how it is used.
What it is?
There are many by-products left over from the smelting of ferrous and non-ferrous metals. Slag is the main waste product. It is a decomposition product of ore, it can have a heterogeneous composition, different properties and characteristics. Metallurgical slag is obtained on a par with the ash remaining after smelting steel and pig iron. It remains in production after processing, requires subsequent disposal or reuse as an independent material.
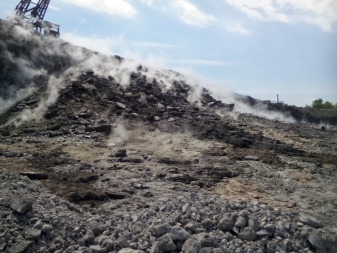
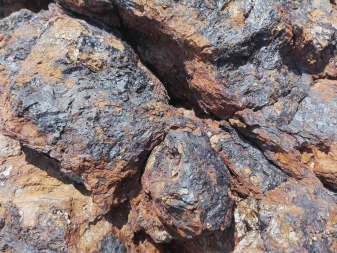
Metal slags are products of high temperature processing. It is a silicate type waste with a multicomponent structure. For a long time, the slags were simply disposed of, not of particular interest. Everything changed in the second half of the 20th century. From that moment on, metallurgy wastes began to be actively used in construction, the agricultural industry, and when laying road networks.
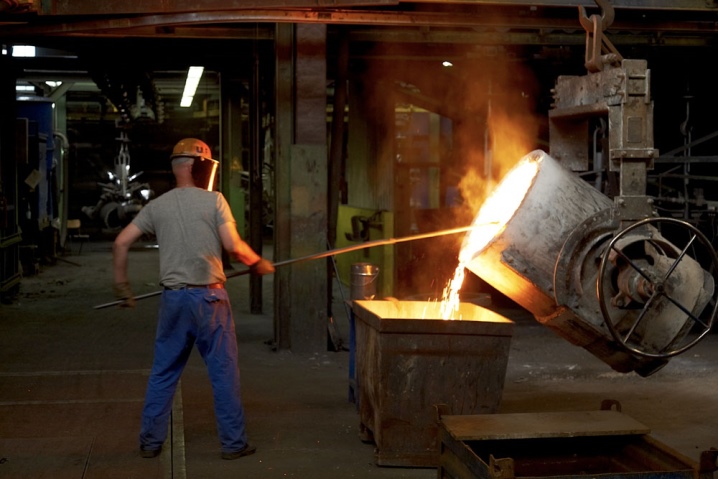
Composition and properties
The composition of the metallurgical slag is not uniform. In fact, it is a chemical alloy of oxides, occupying from 90 to 95% of the volume. The rest is sulphides, sulphates, halogen compounds. Depending on the content of oxides, slags are divided into basic (up to 1%), monosilicates (1%), bisilicates (2%), acidic (up to 3%).
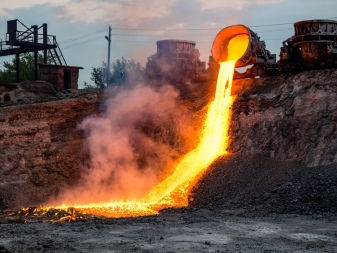
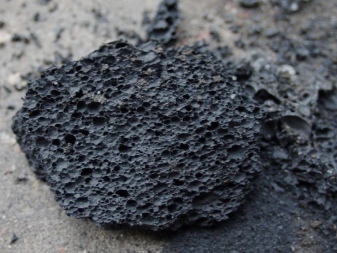
Let's list the rest of the characteristics.
- Specific gravity of the cube. It is 0.7-1.9 tons for a bulk product, and for a lump product - 0.7-2.9 tons.
- Hazard Class. Grade IV is established for all metallurgical slags. This means that metallurgical waste is harmful to the environment and requires proper disposal and recycling.
- Density. Its performance ranges from 750 to 1100 kg / m3.
- Output for 1 ton of metal. For ferrous metals, it ranges from 100 to 700 kg. Modern production involves the use of different metal smelting processes. In a blast furnace, the average is 80 kg / t, in an open-hearth furnace - about 30 kg / t, with a converter technology - does not exceed 18 kg / t. Non-ferrous metallurgy produces up to 200 tons of slag per 1 ton of metal.
All these indicators are taken into account in the further use of waste from the metallurgical industry.
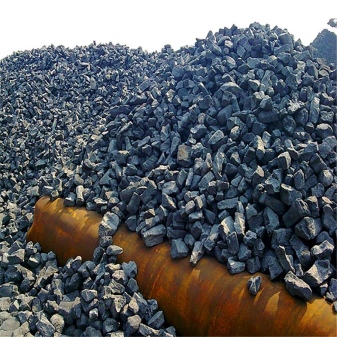
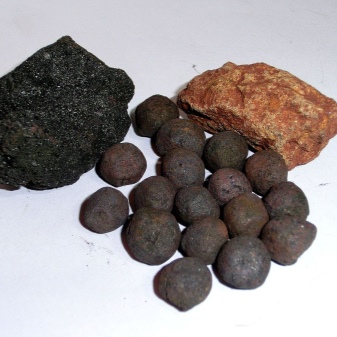
Features of production
According to the method of production, slags in metallurgy are divided into several groups. In a plant, waste processing occurs simultaneously with other processes. For example, the separation of converter slag in steelmaking is carried out in the process of blowing molten ferrous metal. All foreign inclusions are oxidized and then removed.
When smelting ferrous metals, the predominantly cupola method is used. These are shaft-type furnaces originally used in the production of cast iron. The method has a high efficiency, unlike blast-furnace treatment, it does not change the chemical composition of the alloy. Slag goes down through a special tap hole.
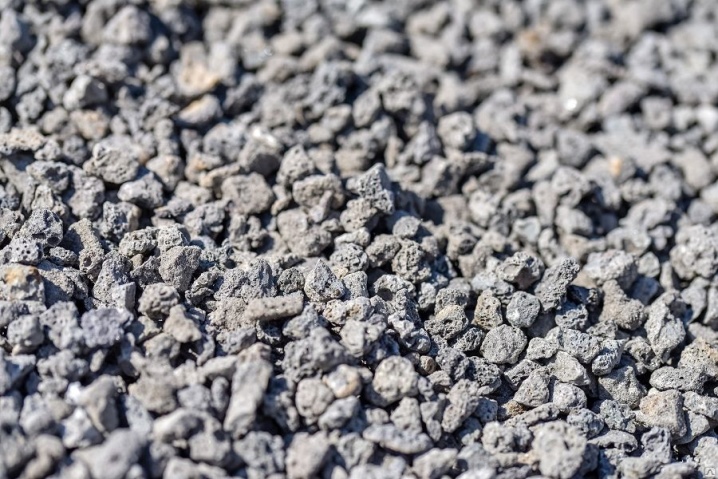
Other types of furnaces are used to melt non-ferrous metals. The resulting slag, covered with a film, is processed in a special way.
To achieve the most complete extraction of valuable substances from the material, their depletion by chlorination, centrifugation or electrical action helps.
Despite the improvement of technologies, the main method of obtaining slag in ferrous metallurgy is the process of metal melting in a blast furnace or open-hearth furnace. In this case, waste collection is carried out due to the lower specific gravity. Slag floats above the surface of the cast iron and is removed through a special taphole. With the open-hearth smelting method, the waste also accumulates above the steel liquid mass, their collection is not difficult.
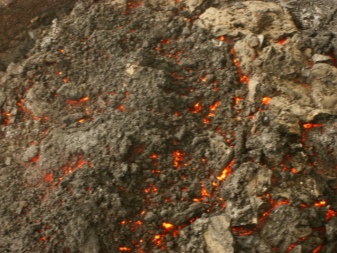
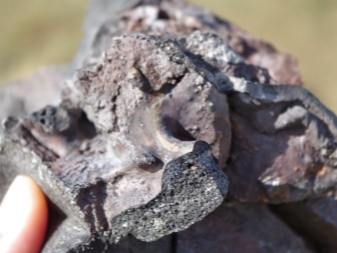
Views
The main classification of metallurgical slag is based on the methods of its production and composition. It is they who determine what the further use of the material will be. The basic division distinguishes between wastes of ferrous and non-ferrous metallurgy. The second group is not too numerous, contains a significant amount of iron oxides with impurities of calcium and magnesium, and more valuable impurities are also present in the composition.
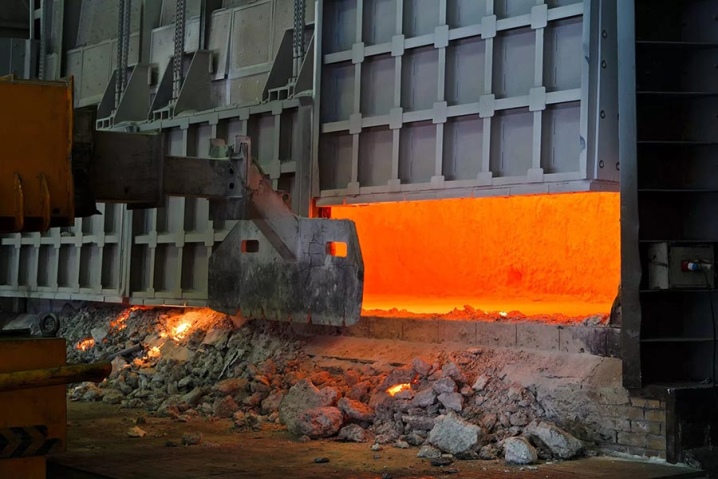
The specific weight of such wastes is much higher, they require additional depletion.
The groups of slags obtained in the production of ferrous metals are more diverse. They are divided into 4 types.
- Ferroalloy. Formed during the manufacture of the corresponding alloys. In addition to iron, such slags contain silicon, manganese, chromium, and other types of impurities.
- Cupola. Obtained by smelting pig iron in cupolas - special furnaces. They consist of the formed flux, coke, burnt-on, ash and metal oxidation products. The proportion of oxides in them reaches 90%. The resulting product has an acidity above 3%, releases minerals, aluminum-silicon glassy particles.
- Steel-making. They are obtained by open smelting of steel, regardless of the type of unit. These are oxides of low density, free of volatile compounds, often with a significant proportion of contaminants. Slags of this type are characterized by a high content of oxidation products of iron and manganese.
- Domain. The most common type has a silicate or aluminosilicate structure. Depending on the chemical composition, upon cooling, the slag acquires a stony structure, from which crushed stone or other building material is subsequently obtained, but it can also crumble into powder. To determine the subsequent purpose of the material, a special quality control system is used.
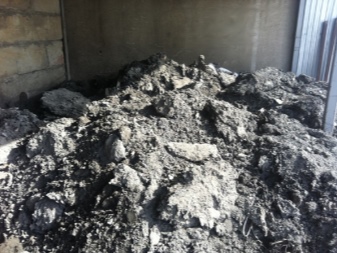
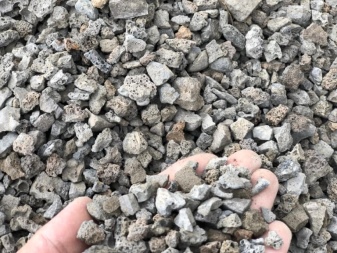
According to their composition, ferrous metallurgy slags after cooling are divided into decaying and non-decaying rocks. The second group takes the form of rocky formations. Decaying variants are usually divided into categories according to their mineral composition.
The most common options are:
- silicate - when recycled, they disintegrate into fine powdery particles;
- calcareous - crushed into crumbs of different sizes;
- manganese - dissolving in a humid environment;
- ferrous - prone to cracking under the influence of moisture.
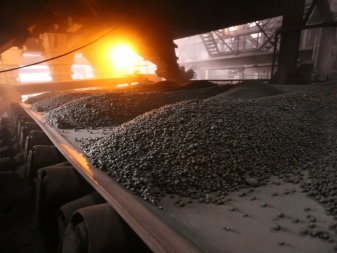
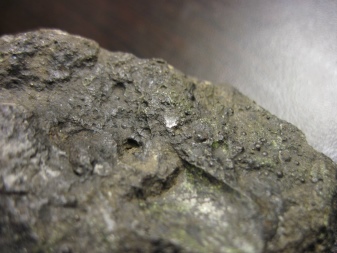
Slags, which do not decompose under the influence of the external environment, are used as a basis for the production of crushed stone and other types of building stone. Depending on the method of processing, they are cooled and crushed by a semi-dry method in special drums or subjected to a "wet" effect of a strong stream of water.
In this case, the material is immediately crushed in the process of leaving the blast furnace, and then only blown for drying and final cooling.
Scope of application
Granulated slag - waste from blast-furnace smelting of ferrous metals - is the most accessible for further processing. Their role in the construction industry can hardly be overestimated. The material is a source of crushed stone - cheaper than natural stone. The finished product is used:
- for road construction - as bedding;
- in the production of concrete products;
- in agriculture, as a drainage for the soil;
- in the manufacture of concrete, as an aggregate.
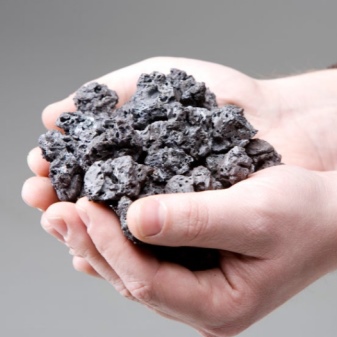
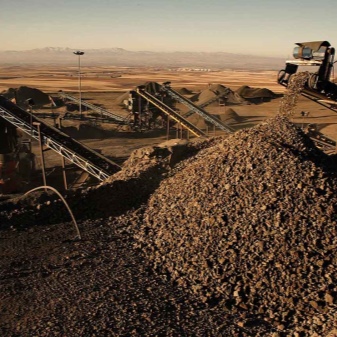
Slags obtained in the production of ferroalloys and in steel production are added to cement in the form of powdery impurities. Such a composition acquires increased chemical resistance. In combination with Portland cement clinker, it is possible to further improve the physical properties of the material. Granular slags mixed with water glass or soda are used in the manufacture of concrete mixtures capable of hardening at low temperatures.
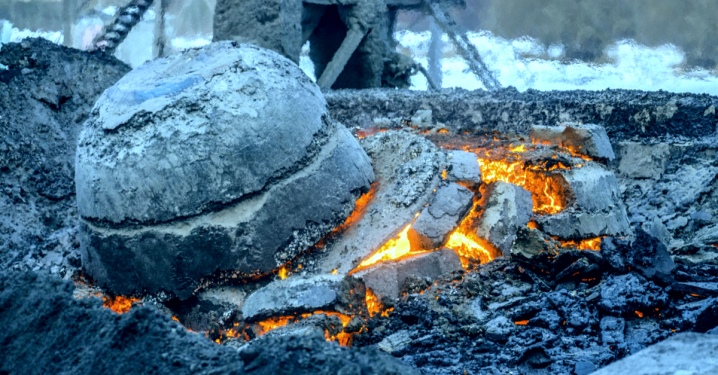
When casting slag, you can get finished products: paving slabs and curbs, interior floor coverings. Also, this method allows you to create pipes and fittings for them, facade decoration. Production costs are significantly reduced, and in terms of its characteristics, the finished material is not inferior to traditional counterparts made of metal or reinforced concrete. Casting is done by molding molten slag.
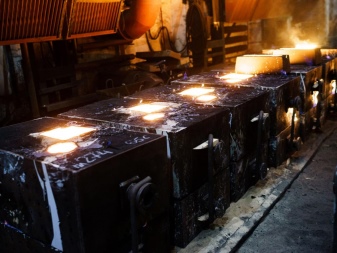
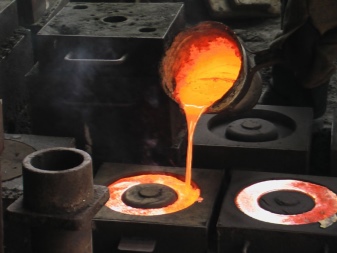
Mineral wool can be obtained from the viscous blast-furnace, steel-smelting, cupola raw materials. For this, the composition heated to a liquid state is sent to drawing machines to form fibers.
The plates obtained in this way can be very hard or rather soft, have an elastic, dense structure. Due to synthetic polymers and bituminous binders, they retain their properties for a long time.
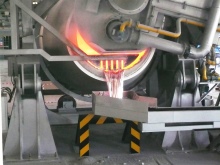
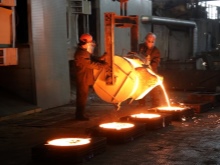
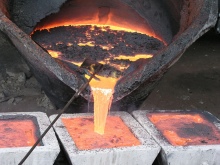
The comment was sent successfully.