Metal facade panels: varieties and their characteristics
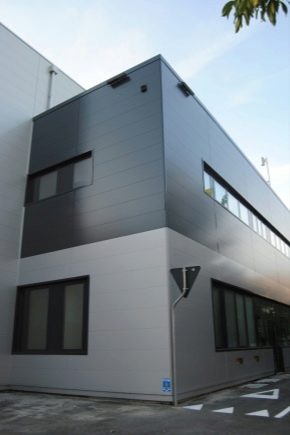
The construction market is filled with many different materials used for cladding the facades of various buildings and structures. This is classic plaster, brick or stone, and special facade tiles, but the most common option is metal panels for the facade. Such structures are most often referred to as "siding".
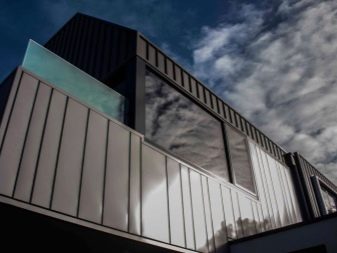
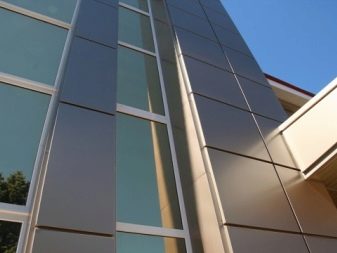
Features and Benefits
Facade panels are most widely used in the construction of commercial real estate: various office buildings, business centers and trade and warehouse sites. However, more and more such cladding panels are used for finishing the facade of private residential buildings and even high-rise buildings.
Such a building material consists of two metal sheets, between which there is a mineral filler. From above, the metal is covered with a protective coating, which allows it to retain its original appearance and characteristics longer.
The filler and the type of alloy used for the metal may vary depending on the manufacturer.
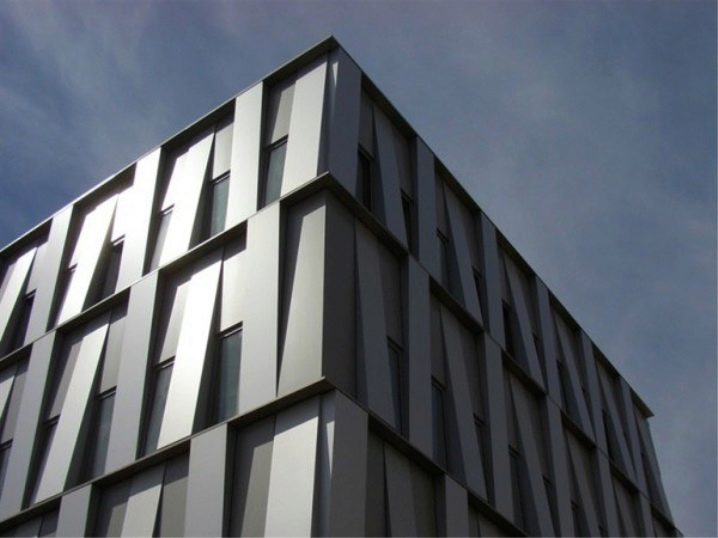
The advantages of these metal structures include the following:
- low weight with increased strength and durability, which minimizes the load on the foundation of the house;
- ease of installation and maintenance;
- the material is not subject to combustion, which means it is safer than plastic or wood;
- resistance to aggressive media and mechanical damage.
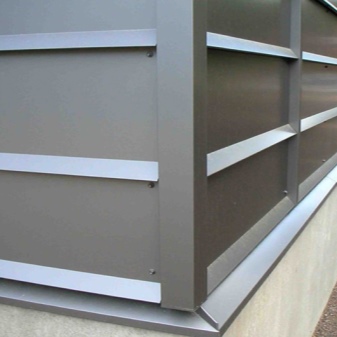
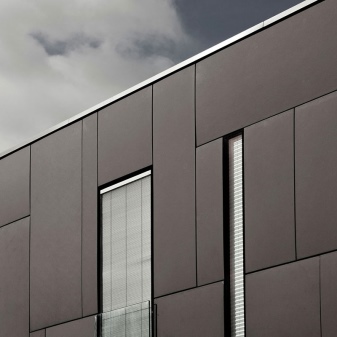
For all its positive qualities, such wall panels still have two significant drawbacks:
- the need to purchase a large number of various fractional elements and special equipment for metal cutting;
- the need to additionally insulate the wall surface before installing the structure.
Such cladding is used both for cladding new and for reconstruction of old buildings, which allows them to give them a modern attractive look. Thanks to the panels, noise insulation is increased, since they create a kind of acoustic buffer. With the help of this material, you can level the facade and make it more ventilated.
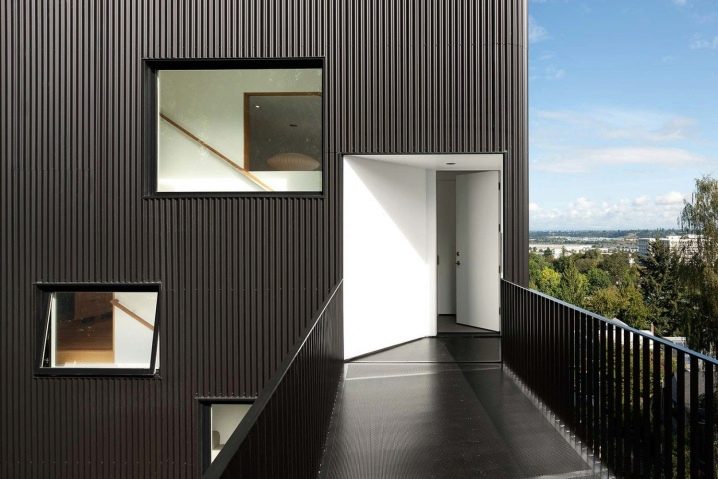
Views
Metal panels are on average 0.55 mm thick. They are waterproof and fireproof. The impact resistance is 50 kg / cm, and the flexural strength is 118 MPa. The classification of panels is based either on their appearance or on the metal used. Depending on the appearance, the panels can imitate wood, stone or brickwork. Profiles can be corrugated, smooth, perforated or various embossing along the edge.
For the production of facade panels, various types of metals and various methods of their processing can be used.
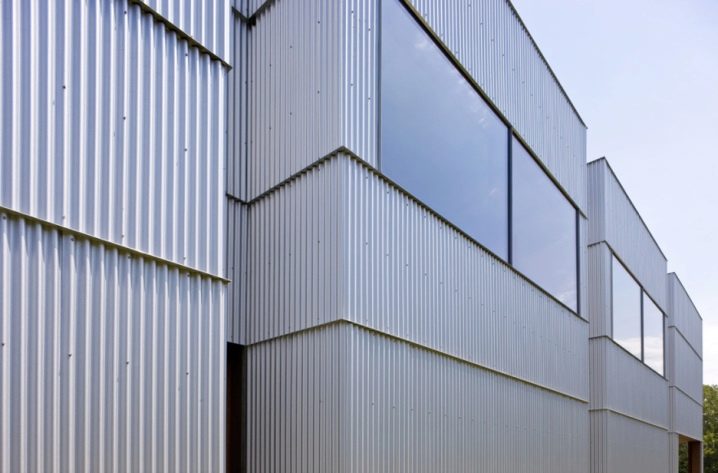
Cink Steel
Metal roofing companies also produce galvanized steel panels coated with polyester. Whether smooth, grooved or patterned, they all have a lock connection and are easy to install. The thickness of galvanized metal is 0.5–0.7 mm, and the coating not only protects the material, but also allows you to give the product different colors and textures.Such material is the most versatile and is used for cladding any facades, from country and country houses to shopping pavilions and sports centers. The length of such panels can reach 5–6 meters and are ordered from the manufacturer. They can be mounted both horizontally and vertically. The panels are lightweight, durable and economical.
Unfortunately, due to their lightness, such structures are susceptible to deformation, as well as accumulate static electricity and require additional thermal insulation.
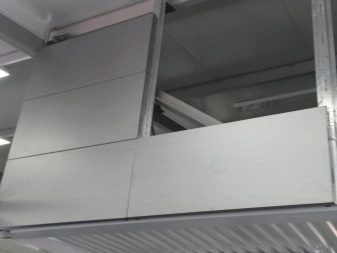
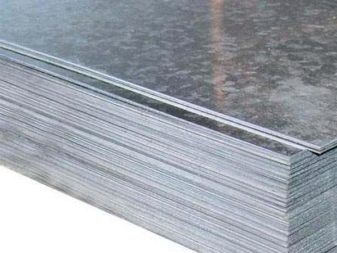
Stainless steel
Stainless steel is another popular material for facade cladding. Coated with a layer of oxide "stainless steel" does not require additional coating with various protective agents. With the right grade of steel, such panels are durable, lightweight and very easy to maintain, despite their rather high price. Like galvanized steel cladding, stainless steel requires thermal insulation and accumulates static electricity, but at the same time it is more resistant to corrosion.
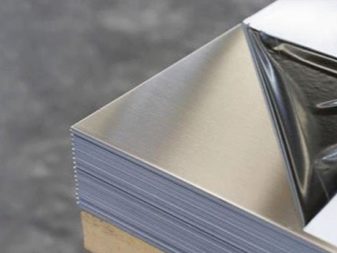
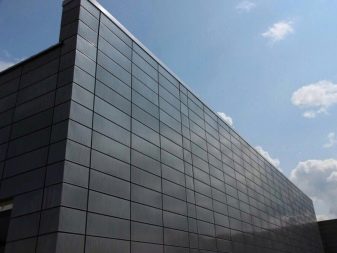
Aluminum
Aluminum panels are also called composite panels. Their total thickness does not exceed 6 mm, and the length is 6 m. From above, the metal can be covered with an oxide film, which will protect the material and give it various shades. With the help of such a film, you can get a mirror effect, imitate a wooden or stone surface.
Composite multilayer aluminum panels, called "Alukobond", are distinguished as a separate type. Either synthetic polymer or high pressure foamed polyethylene is placed between the sheets of durable metal. Such material reliably protects the facade from moisture and mechanical damage, and also allows you to bring to life almost any design idea due to the fact that it easily bends and takes on the required shape.
Unlike galvanized and stainless steel, aluminum does not accumulate static electricity and does not require thermal insulation. However, it is a more expensive and less durable cladding material.
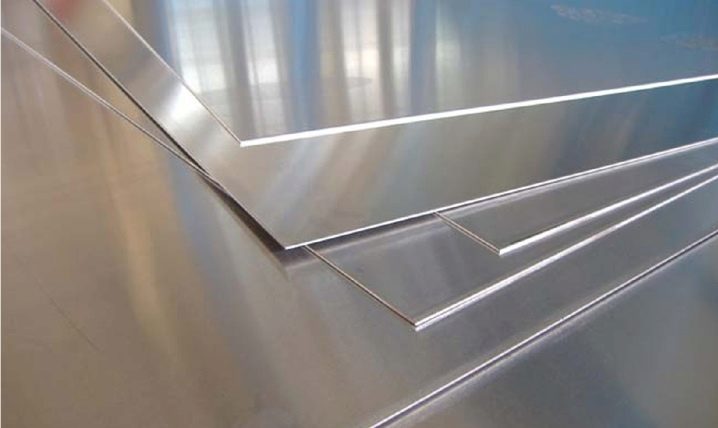
Other types of metals
In addition to steel and aluminum, metal panels can also be made from other materials and alloys: brass, copper and even bronze. These panels are coated with a glossy or matte varnish and are installed using hidden fasteners. Inside, such structures are pasted over with a sound-absorbing material in order to exclude ringing during mechanical stress. They are durable and easy to install and remove. Such panels are used not only for cladding facades, but also for interior decoration.
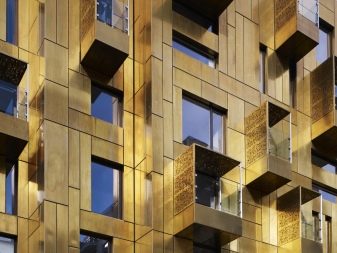
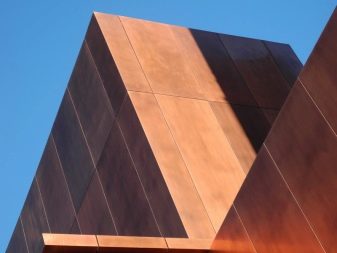
Polymer coated
The basis of such panels is aluminum or galvanized steel, on which a protective polymer coating is applied on top. The thickness of such metal panels is about 0.56 mm. They are smooth, corrugated or perforated. Such panels are moisture and frost resistant, have good sound insulation, and are also easy to install. Before installation, it is necessary to pre-insulate the facade or use more expensive sandwich panels. In order for such a cladding to serve for a long time, it is necessary to correctly mount the battens made of wood or aluminum profiles.
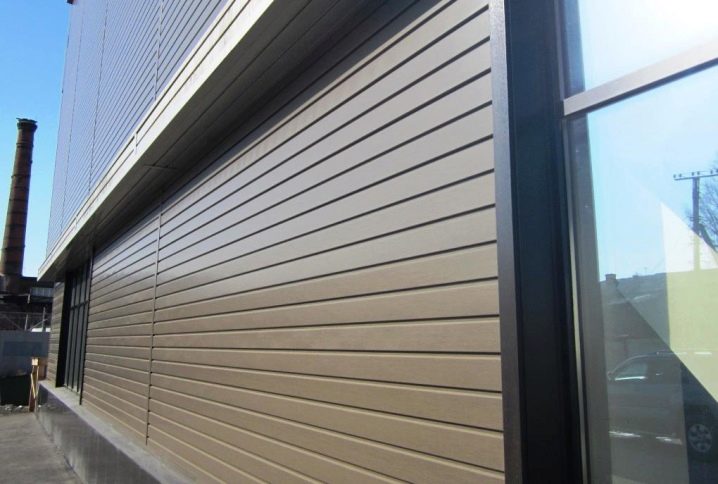
Sintered metal
Such panels are steel sheets that are coated with glassy enamel. The enamel imparts high resistance to aggressive media, high rigidity and durability. Such structures are most often used in the construction of transport infrastructure: various tunnels, crossings and stations. However, today this material is increasingly used for cladding the facades of ordinary residential buildings. Their thickness is 200 mm, the material is non-combustible, withstands temperature drops from -60 degrees to +800. Products made from this material are easy to care for and serve for over 50 years.
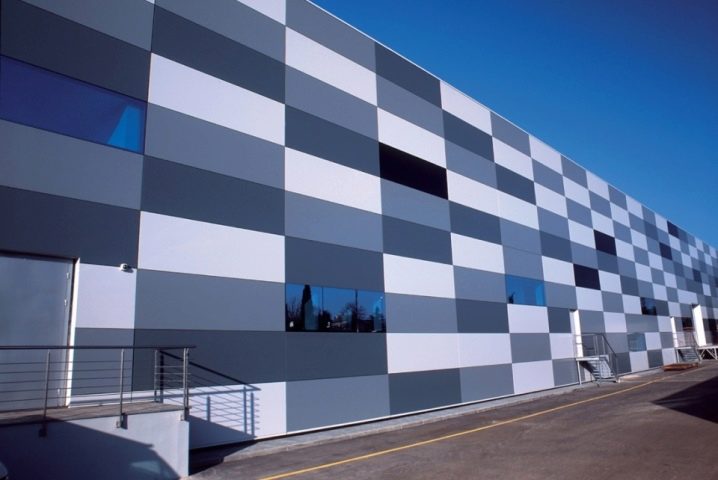
Design
In addition to differences in the material from which facade panels are made, they can differ in surface relief.
- Smooth. Conventional steel panels that differ only in color. They can repeat a wood pattern, make up one large picture from fragments or become glossy, creating a mirror effect.
- Corrugated. Curved by soft wave or hard angular protrusions.
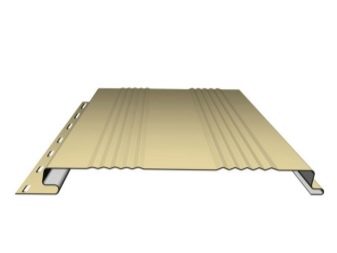
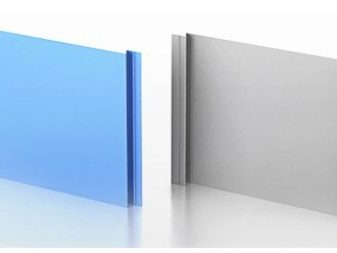
- Perforated. They come in various patterns: from geometric to individual ornaments, made to order. In the dark, such panels let the light emanating from the building pass through and create a whimsical picture, embodying all kinds of designers' ideas.
- With additional decorative ribs. Depending on the distance between such ribs, you can visually expand the facade or make it higher.
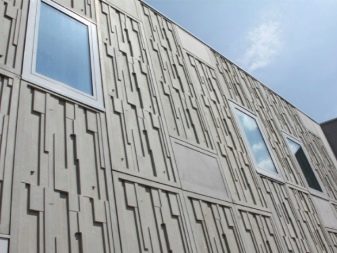
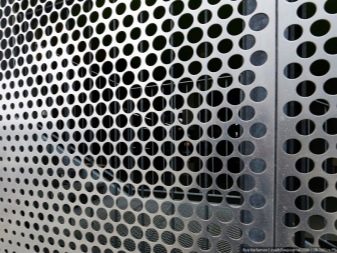
When decorating industrial and public premises, cassette panels are used, as a rule.
Such panels are of several types.
- Cassette - volumetric panels, consisting of aluminum sheet or steel with polymer spraying. Such a cassette has a bend at the edges and is made not only in factories, but also directly at construction sites due to the simplicity of the design. Most often they have a square shape and a smooth surface.
- Linear - elongated panels for exterior and interior decoration. Due to this design, the facade is mounted with a minimum number of gaps at the joints or no gaps at all. Linear designs are similar to long cassettes, but can have a perforated or 3D surface.
With all the variety of materials, most of the facades are cladding with sandwich panels made of several layers of different materials. The simplest products have three layers: two facing (metal, wood board or other materials) and one filler layer (most often it is insulation).
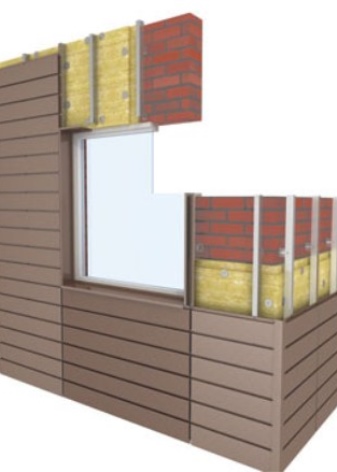
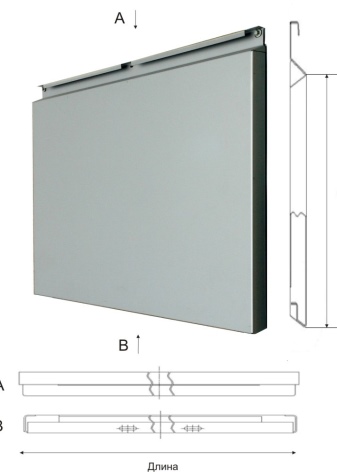
Dimensions and other characteristics
The average dimensions of the steel facade panels are as follows:
- metal thickness ranges from 0.48 mm to 0.65 mm;
- the length of the longest panels (linear) can be up to 6 m, but on average the length of the panels is from 2 to 3 m;
- the width usually ranges from 200-250 mm, but you can order siding of individual sizes - up to 300 mm (however, the large width of the product will increase the risk of deformation during transportation and installation);
- the weight of one square meter of such a cladding weighs on average from 2 to 3.5 kg.
Since the panels are sold per piece, it is necessary to clearly understand how much material is needed to carry out the work.
All calculations are always rounded up, and for beginners it is better to purchase several additional panels in case the first attempts fail.
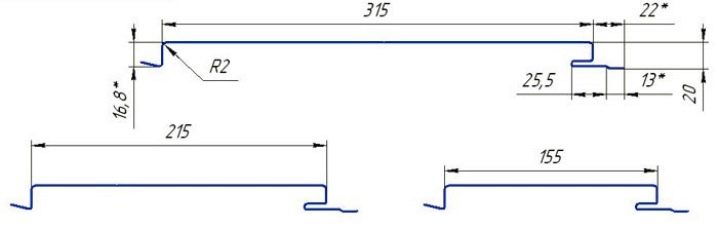
Manufacturers overview
The production of metal panels can be both manual (directly at the facility) and professional (at large factories). Products from foreign suppliers are presented by various companies, among which there are several brands that have received the best reviews: Finnish metal panels brands Ruukki (in the construction market for over 50 years), American siding from the company Alcoamainly made of aluminum, as well as a British-Dutch brand Corus Group.
Among domestic manufacturers, you can designate brand facade panels Grand Line... The products of Lipetsk Roll Forming Equipment Plant and INSI holding are widely represented on the market. And also positive evaluations from buyers received the products of the plant SeverStal... The main difference between Russian manufacturers is that, with the same quality, domestic products have a lower price than foreign ones. This difference is due to the lack of transportation costs.
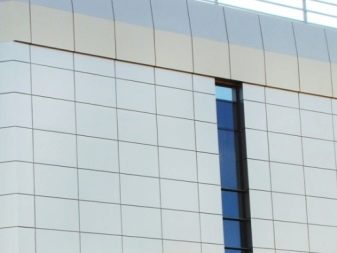
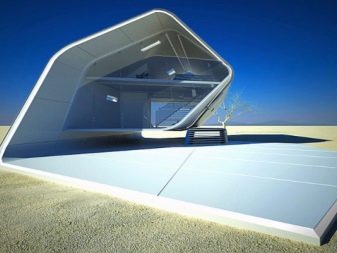
Installation Recommendations
In order to carry out the facing of the facade of any building, it is necessary to consistently perform the following stages of work.
Preparatory work
This stage includes cleaning the entire outer surface of the building from debris and old coatings, dismantling all foreign objects (shutters, gutters, antenna).In addition, it is necessary to remove any defects on the walls, remove all chips and irregularities in the concrete, and treat the wood from decay.
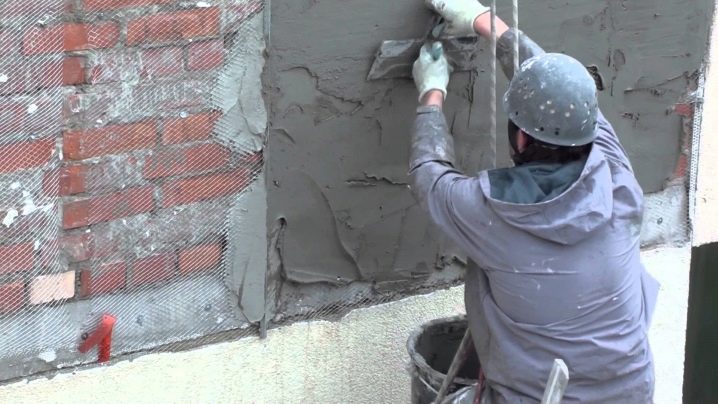
Markup
With the help of a punch, special holes are drilled in the places indicated by the markings. It is better to make the markings with a bright indelible material, so that in the event of a change in weather conditions, you do not have to start it all over again.
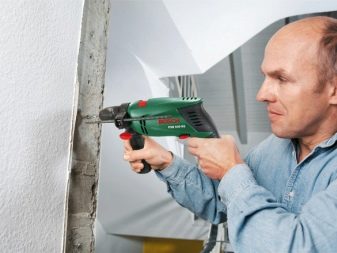
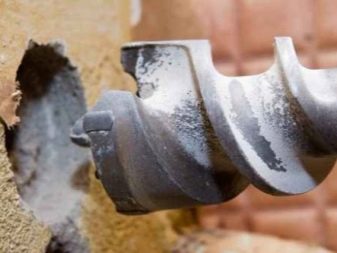
Lathing
At this stage, the construction of a frame from wooden slats or metal profiles is carried out. Insulation is selected so as not to be thicker than the crate, and fit snugly into the resulting "honeycomb". Insulating material is laid from bottom to top on the finished crate or directly glued to the wall surface.
It is important to use only dry insulation, as moisture accumulated under the mounted panel can destroy it.
On top, a layer of insulation is covered with a waterproofing film, which prevents water from entering the already installed panels.
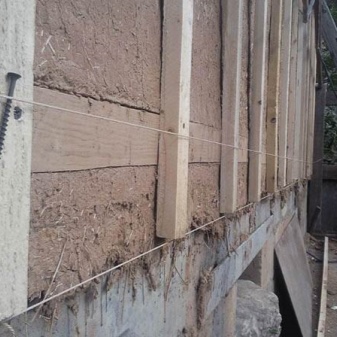
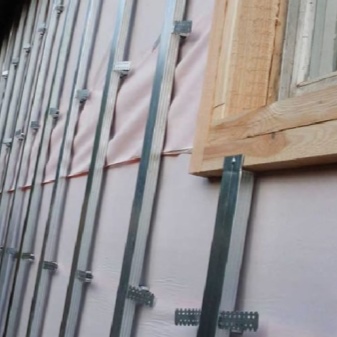
Mounting
Most often, the process begins with the fastening of fractional elements: starting, corner and final planks. Then, sections of the wall next to window and door openings are revetted. In the case of using a finishing strip, such elements are installed, on the contrary, last.
After installing the fractional ones, you can start installing the remaining planks, starting from the lower left side of the wall. Elements are attached to each other using screws or special built-in locks, and you can also strengthen the existing lock with additional screws. After the cladding is finished, all removed elements are returned to their place: slopes, gutters, shutters, and so on.
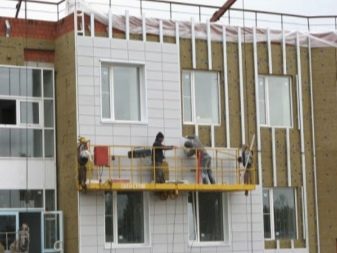
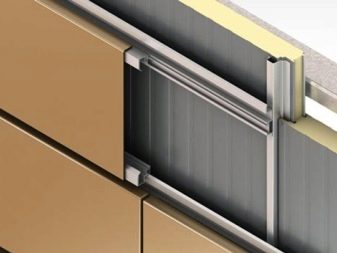
In general, all finishing work on the facade, in which metal panels are used, are carried out according to one simple algorithm - you can not be afraid to spoil and deform durable material.
Panels are a fairly economical solution for a private or country house, and the result will be pleasing to the eye for many years.
For more information on how to install a panel system, see the next video.
The comment was sent successfully.