Varieties of expanded clay concrete partitions and their masonry
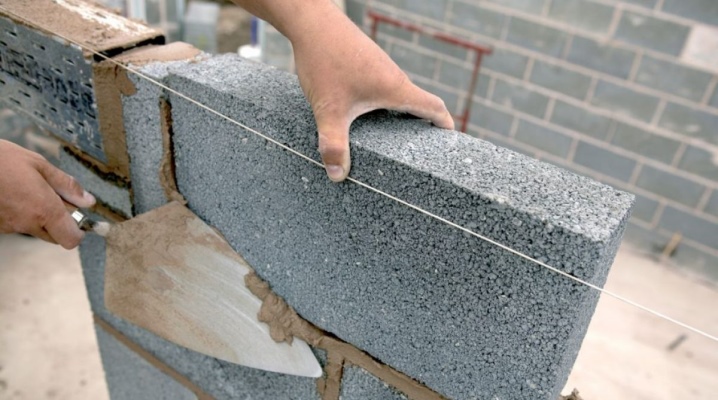
Expanded clay concrete partitions are a reliable solution, a popular building material used in the construction of buildings. They are quickly assembled, widely used to divide the space inside residential buildings, industrial facilities, garages and outbuildings. Compounds that do not contain harmful impurities are called biological blocks or eco-blocks.
Primary requirements
Blocks with a base of expanded clay concrete are manufactured for industrial purposes according to strict regulations. A sand-cement base, water and expanded clay as a solid filler are used as ingredients. The solidified mass is formed into block structures using a vibrating press.
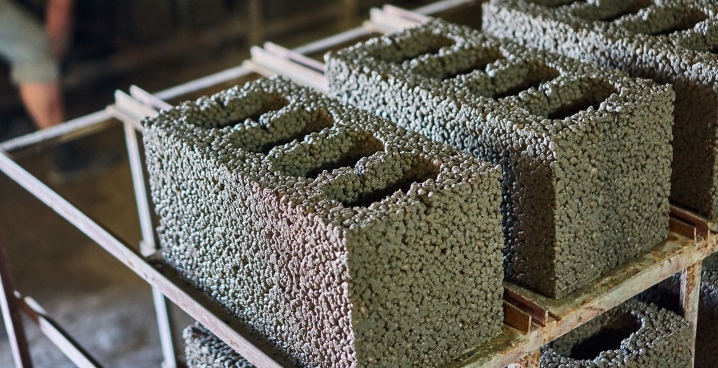
When forming the mixture, a proportional ratio in the amount of consumables is observed, although individual manufacturers allow changes in the recipes. Strengthening the strength is achieved due to the prevalence in the composition of the cement. The density of the block depends on the choice of filler. For example, fillers such as gravel, shungizite, aggloporite can be selected.
Plasticizers are a valuable ingredient that can improve product quality. The addition of plastics and ceramics to the mix minimizes the risk of further cracking.
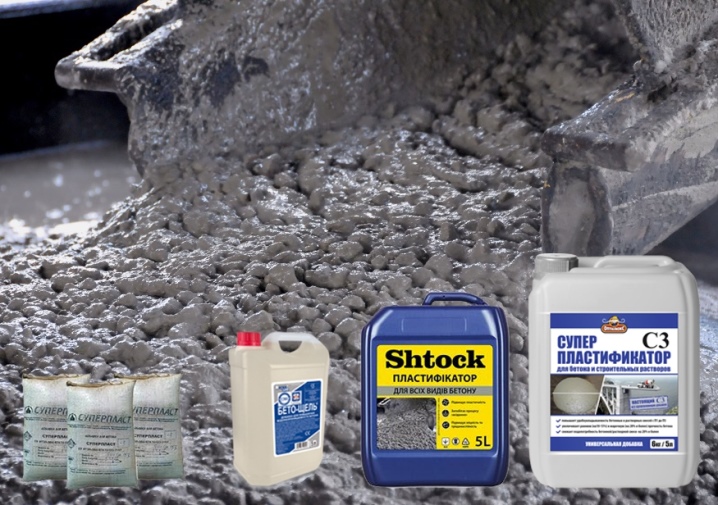
Let's analyze the main technological requirements that apply to partitions in residential premises.
-
Ease, no significant additional pressure on the structure. To achieve this goal, the weight and thickness of the baffle are minimized during manufacture.
- Strength. It is important when reinforcing the block into more massive parts, installing the finishing of the building.
- Heat insulating and sound insulating properties. These properties are at a high level in all types of expanded clay concrete structures, especially in hollow blocks.
- Ease of installation. Finishing with all types of coatings and materials.
- Fire safety. The partition must not ignite, even if other parts of the building are on fire.
- Environmental friendliness. The components of the blocks cannot contain harmful impurities, emit dangerous vibrations for human health.
- Low price. The calculations take into account the cost of work and the cost of materials.
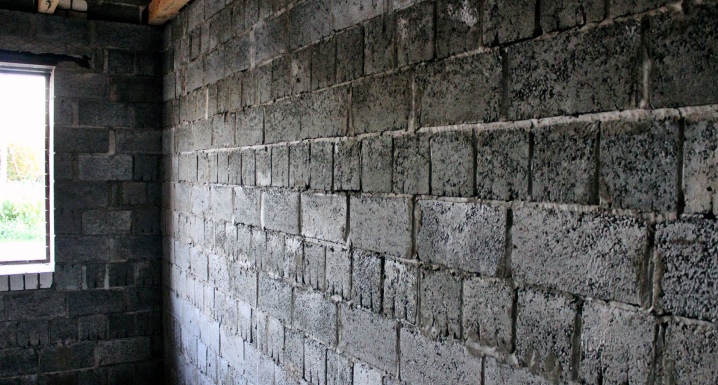
Ecoblocks with expanded clay concrete meet all the requirements of sanitary standards. The base granules contain more than 85% air, so any vibrations are damped inside. The thermal conductivity of the material due to the voids is extremely low, which ensures excellent thermal insulation of the building. The disadvantages of experts include high porosity, inaccurate dimensions during manufacture.
Frost resistance of expanded clay concrete is in practice lower than that of some solid types of bricks. Due to the high fragility, a significant amount of connector is required, the seams are wide.
Species overview
According to the principle of manufacturing technology, partitions are divided into several types.
Monolithic
The most difficult execution, high strength. For casting, it is necessary to fill the formwork with expanded clay concrete composition, the installation of which requires additional time. Therefore, builders use monoliths less often than other types. The advantage is that the product can be given any size and shape, reinforced, further increasing its strength.
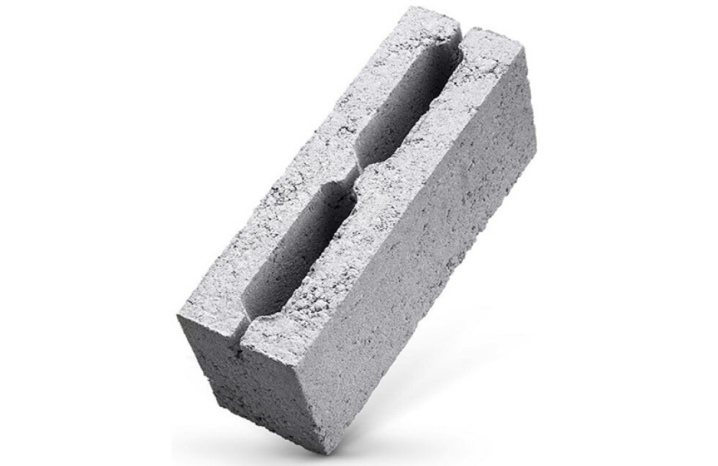
From solid blocks
The masonry is made of elements that do not contain voids, except for natural pores in the aggregate material. In small one-story buildings, even load-bearing walls can be erected with their help. The application significantly reduces the thickness of the walls and saves space, while the structure is able to withstand the significant weight of hinged furniture and technical equipment.

Hollow
They are built from blocks containing significant voids inside. The voids are used for laying highways, as boxes for ventilation, for laying heat-insulating compounds. Hollow partitions are lightweight, easy to move, and especially convenient in design. As well as full-bodied, they can be stacked in half a block. This is how they mainly build summer houses or garages; permanent housing is erected from monoliths with reinforcement.
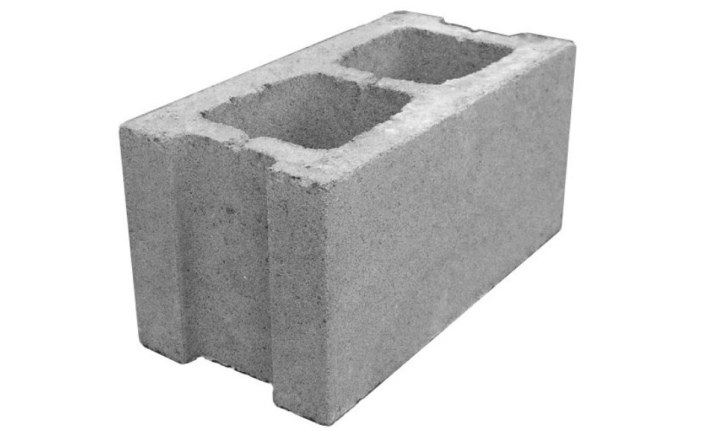
Block selection
The popularity of blocks among builders is reaching record levels. It is much easier to work with them than with bricks. The masonry technique for these two materials is almost the same, while the block structures are easily decorated with various types of plaster. The decor not only looks beautiful, but also protects the walls from negative environmental factors. Blocks for housing construction are chosen for several important characteristics.
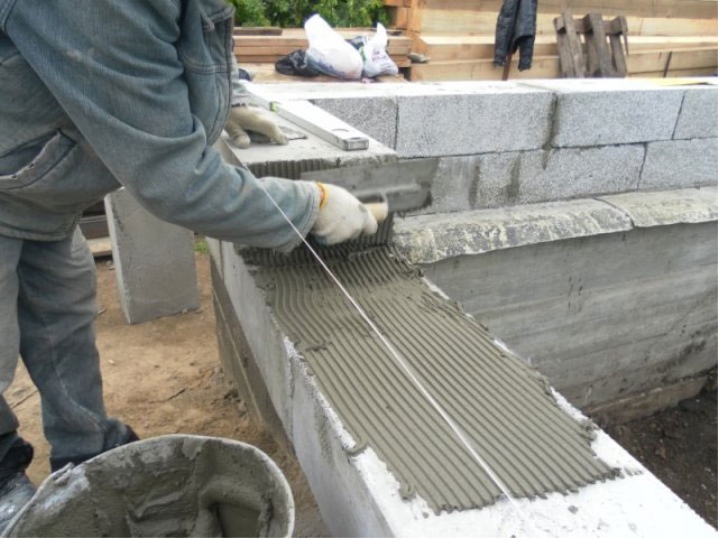
In terms of the shape and structure of the main material, partition blocks are:
-
tongue-and-groove;
-
ordinary or simple;
-
corner;
-
straight lines.
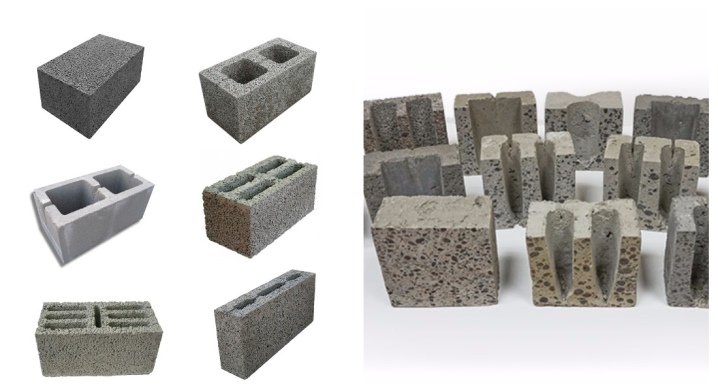
The tongue-and-groove panel is a building module capable of replacing up to 15-20 blocks. Grooves are laid inside it for communications. In terms of height, the workpiece is 2.5 m, and in terms of strength it exceeds other structures made of expanded clay concrete. The use of the panel significantly reduces the construction time. At the same time, there is an obvious saving of joint solutions. It is mainly used in the case of large-scale construction, which requires the participation of an entire team. One person cannot cope with such work.
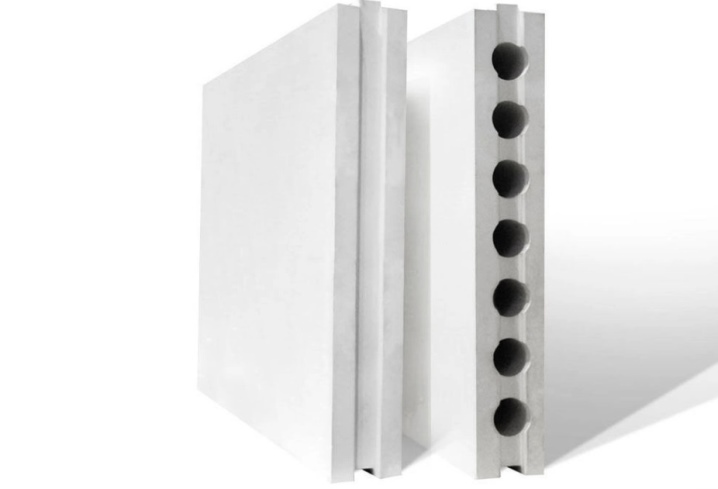
The manufacturing parameters are set based on what the structure is intended for. Expanded clay or Portland cement are pressed in accordance with accepted standards. Lightweight blocks are marked as follows:
-
wall - "C";
-
intended for hollow partitions - "P";
-
finishing front ones are designated by the letter "L", privates - "P";
-
corner products are marked with "UG".
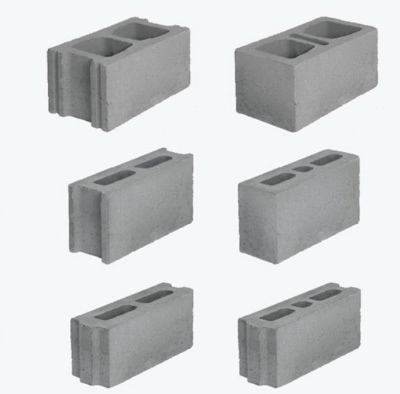
Density is determined by the numbers indicated on the product after the letter "D". The bulk of types of lightweight concrete blanks fit into the D500-D900 range. A standard block with dimensions of 390x90x188 mm, with the minimum density of the material, weighs about 13 kg, and with the 900th - 17 kg. Industrial expanded clay concrete modules are produced up to 40 cm in length, up to 18 cm in height and up to 19 cm in width.Panels for interior partitions are mounted from narrow blocks 88 cm wide.
The next indicator is frost resistance. Defined by the letter "F". The number following it indicates how many freezes and thaws the product can withstand. It varies from 15 to 100; for construction in cold areas, blocks with a number of cycles of at least 70 are chosen.
Construction stages
It is necessary to prepare for work, having in stock:
-
roulette;
-
an empty container and a shovel;
-
reinforcing bars or fiberglass;
-
grinder;
-
plumb line and level;
-
jointing for aligning the seams;
-
rubber mallet.
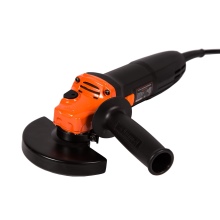
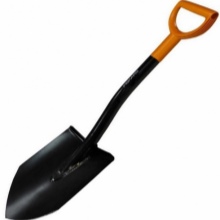
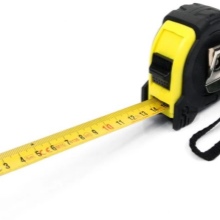
- To carry out masonry with your own hands, first of all, you need to prepare a joint solution. You can also buy a ready-made mixture. Usually, detailed instructions are written on the package. A homemade mixture is made from the highest grade cement and refined sand. The ratio for reliability is usually kept at least 1: 3. Cold water is filtered, added to sand and concrete at the rate of ¼ of water from the total weight of the solution.
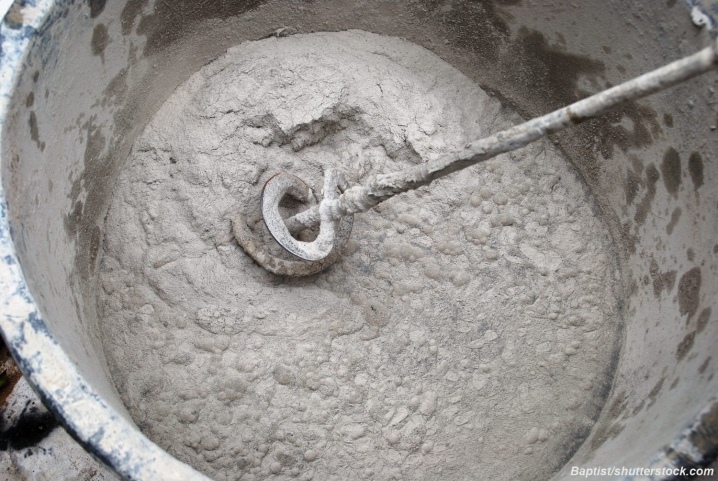
It is best to use a stationary concrete mixer nearby. If not, use a container and a shovel. First you need to pour a small amount of water, and then add sand and concrete for one batch. After mixing thoroughly, add the remaining water.The solution is used fresh - in order to prevent solidification, the connector is prepared immediately before work.
- In the next step, the foundation for the masonry is provided. The working area must be thoroughly cleaned. An even surface is achieved by applying a layer of screed. A waterproofing material is placed on top - along the perimeter and where the partition will be located. As a rule, for these purposes, roofing material or a similar roll insulator is taken.
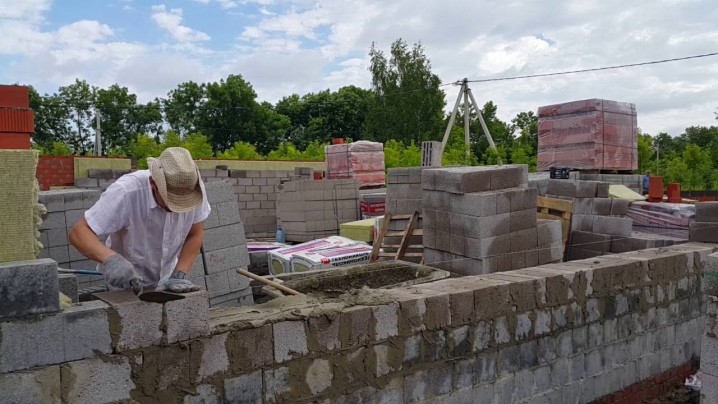
- The workpieces are laid out for work according to the size. They choose an installation scheme - as a rule, in residential buildings, panels are erected in one block.
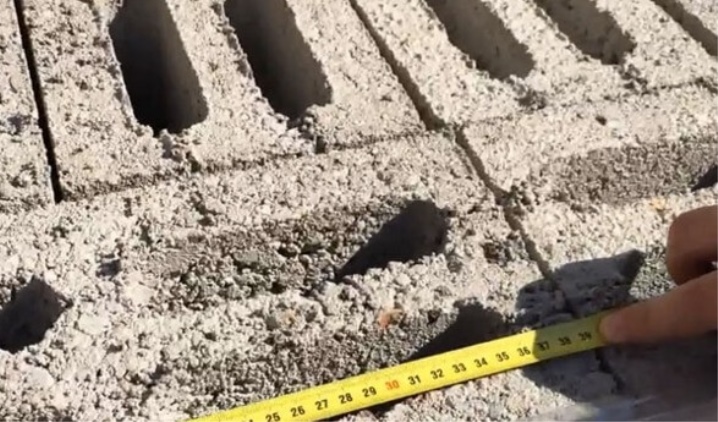
- The corners are put first. Then the accuracy is controlled by pulling a string between the elements. After that, the first row is laid, fastening with a solution. The beginning of the movement is the highest point of the base, from which work begins. The voids are gradually leveled, increasing the width of the seam. Remove excess, perform jointing
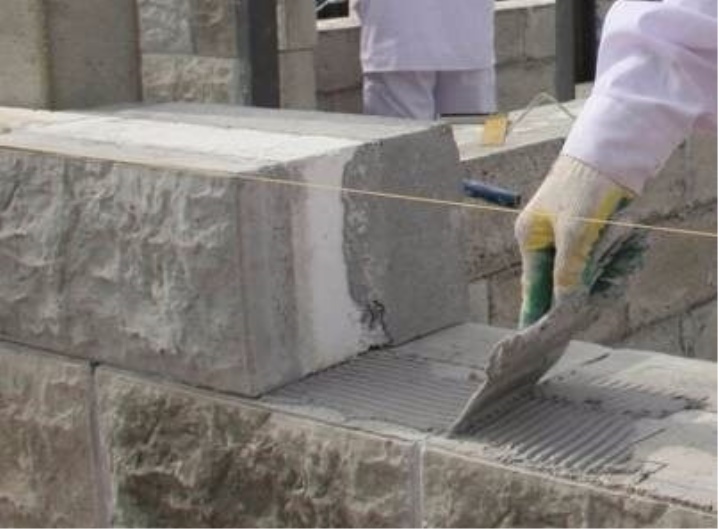
- The subsequent rows are fixed starting from the second, keeping a slight offset. When laying, they keep a wide seam, not less than a centimeter. As soon as the row is completed, it is checked whether it is evenly laid, as there may be size mismatches. Reinforcement with mesh, if necessary, is carried out at least after three rows.
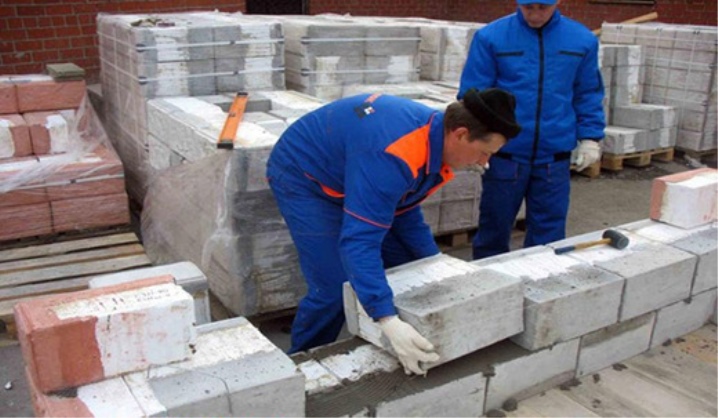
- Care should be taken to tie the structure to the load-bearing walls. This is done using rods made of reinforcement with mortar, which are inserted into pre-drilled holes.
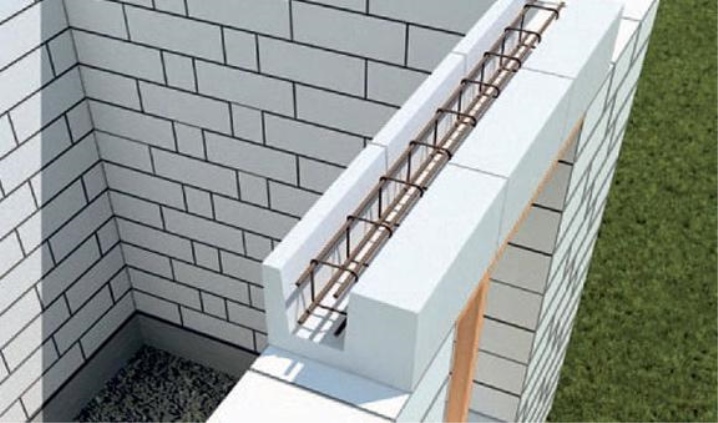
- In a private house or apartment, a doorway is needed in the partition. The openings are formed not only in rectangular shape, but also in the form of arches. In the case of hollow products, the modules are additionally strengthened along the edges, filling them with an adhesive or mortar. Then a steel jumper is placed on the opening. The use of tongue-and-groove panels allows you to fix the opening by placing the reinforcement in the grooves. A ring of wire is created around the opening, which reliably holds the structure.
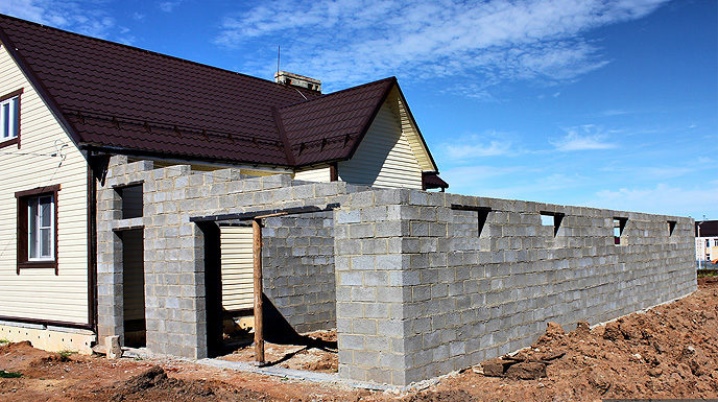
- A space remains between the partition and the ceiling, which is filled with foam. Foaming enhances vibration reliability.
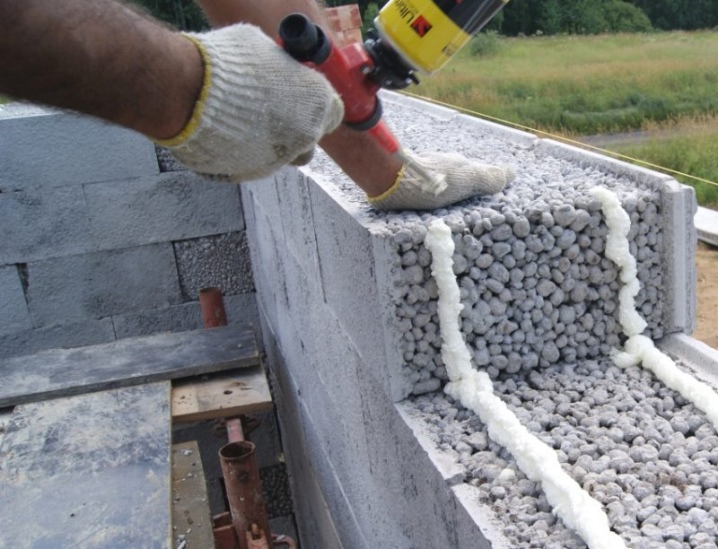
- You can decorate blocks in an apartment after filling the surface. Wallpaper is pasted on the panel, or other decor is made.
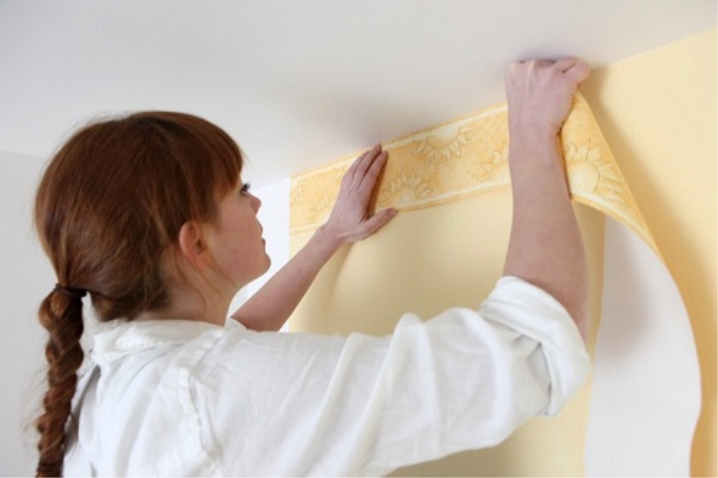
In the next video, you will see the masonry of kermzite concrete walls.
The comment was sent successfully.