Everything you need to know about crushed granite
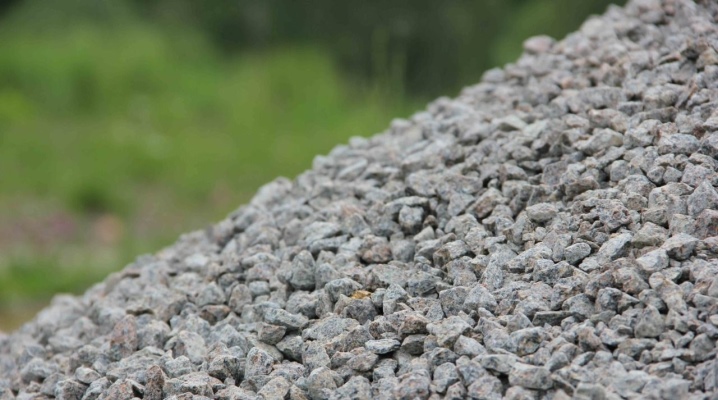
Granite crushed stone is the most common type of building materials, it is obtained from volcanic rock, which has increased strength and has a granular structure. The shade can be almost any, it all depends on the composition. Natural granite is a particularly durable and hard type of stone.
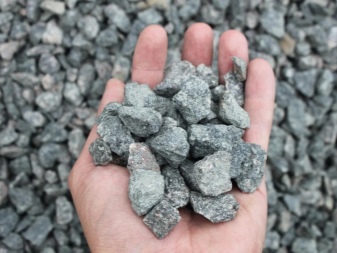
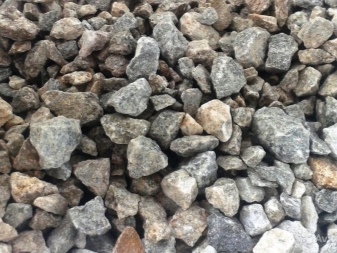
Advantages and disadvantages
Benefits of Granite.
- Increased strength and hardness - this natural stone has the highest coefficient.
- Ease of processing, as it interacts well with various adhesion components.
- Practicality - suitable for use in various fields and industries.
- Appearance - granite crushed stone looks like a stone with many inclusions of black, gray and white colors, such a specific color is often used for decorative work.
- Low water absorption - this property plays an important role in construction, since granite will not deform from moisture.
- Frost resistance.
- Durability.
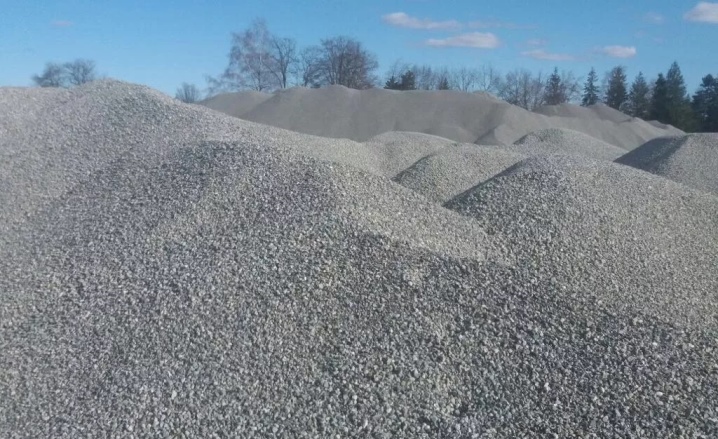
Cons of granite.
- Unlike dolomite crushed stone, the coefficient of hardness and strength of which is identical to granite, the second has a higher price. This is the main disadvantage of the material.
- A laborious manufacturing process, additional steps are required after extraction from a quarry.
- Environmental friendliness - granite crushed stone can contain harmful components, in contrast to limestone, which has a lower level of radioactivity, despite the fact that both rocks are of natural origin. Choosing a specific rubble, you need to look through the certificates and choose 1 class of radioactivity, it is better not to use the granite variety in the construction of residential premises.
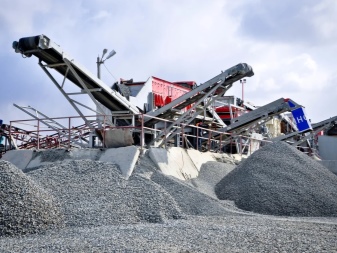
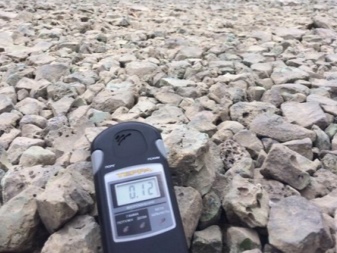
Extraction features
In colloquial speech, such an expression as "crushed stone mining" is usually used - this is not entirely true, in fact, crushed stone is obtained by an artificial method. Only rock is mined - this is the initial raw material. The material itself is made using crushing and screening equipment.
The process itself consists of three stages - this is the extraction of the source material, crushing, sorting.
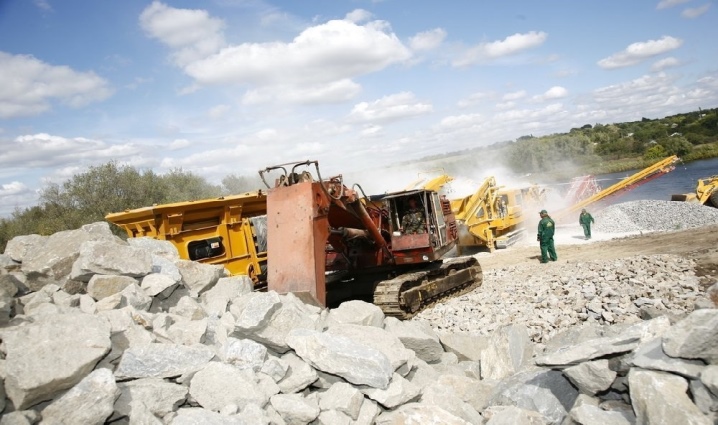
Breed extraction
Crushed stone producers use different raw materials - granite, marble, limestone, etc., depending on what kind of product you want to get at the end. Granite crushed stone is made from centuries-old volcanic (volcanic) material - frozen magma. Before starting work, a quarry is prepared - the top layer of sod with grass is removed, then the top layer of soil. Granite blocks are extracted from the ground using explosions and technology, if necessary, they are divided into smaller pieces.
The production of crushed stone can be targeted or by-product. When manufactured in the first way, the material will be of higher quality and price. In the second case, crushed stone is a by-product obtained during the extraction of any minerals or in the manufacture of any products. The extraction of rock can be carried out in four ways.
- Stone cutting - this method is the most costly, but at the same time one of the most effective. With the help of stone cutting equipment, large blocks are sawn off immediately in the quarry. The machines are equipped with wire saws or disc saws with diamond tips. When working in this way, lumps are obtained of the desired shape and size, microcracks do not form on them.
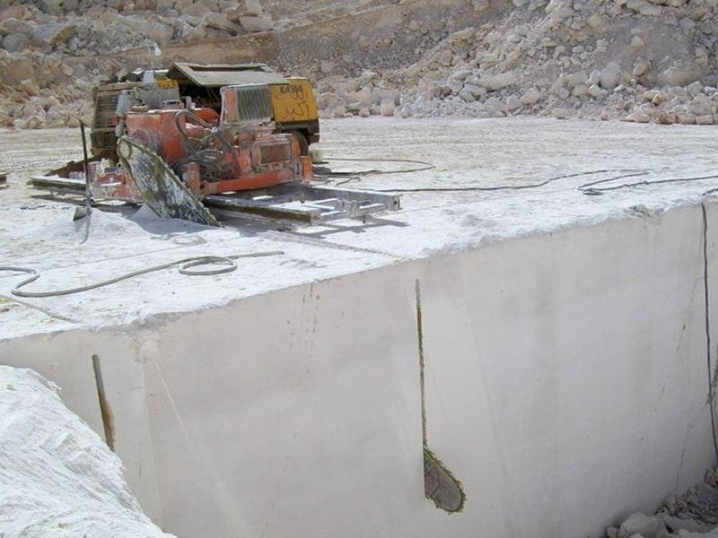
- Buroklinova - this method is one of the oldest and now it is used quite rarely.Here the work begins with the outline of the block, then wells are drilled along this mark. Special pegs are laid in them, upon impact on which the block is separated along a predetermined line. The hardest rocks are usually mined with this method. The only disadvantage of this technology is that it is only suitable for small pieces of rock.
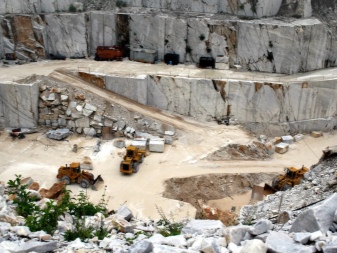
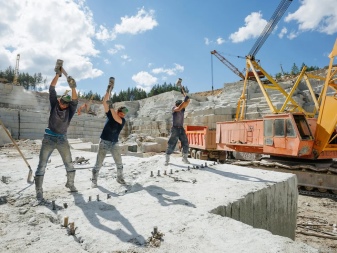
- Burohydrokline Is an advanced borocline technology. The mining proceeds according to an identical plan, but steel wedges are replacing the hydraulic wedges. They are filled with water, which is under pressure, and smoothly expand in the drilled holes. This method can be used to extract pieces of stones of a very large size, in the most inaccessible places. A great advantage of the brown hydro-wedge technology is the complete absence of noise and vibration, so the structure of the rock is preserved as much as possible.
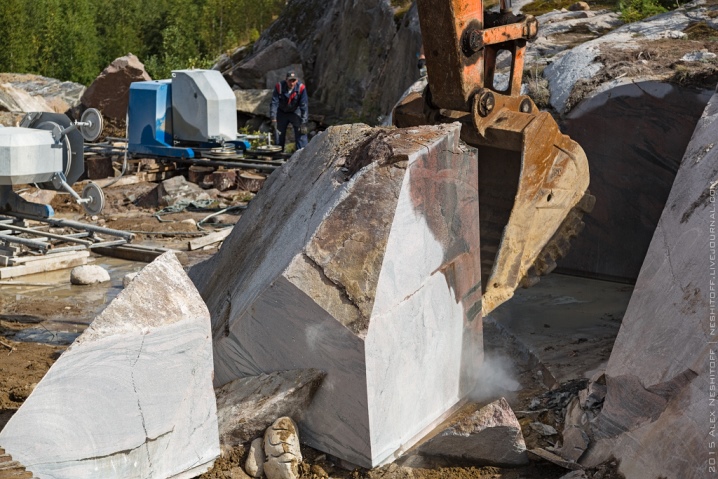
- Drilling and blasting (explosive) - this method is the most popular both in the extraction of rock and in the extraction of ore. Holes are also drilled in the stone, and explosives are placed in them. The explosion breaks off many pieces of stone, the largest are collected and taken away for processing.
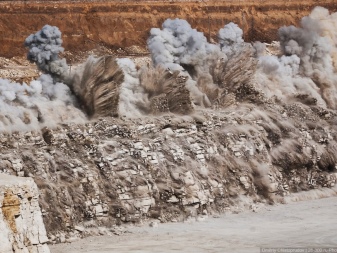
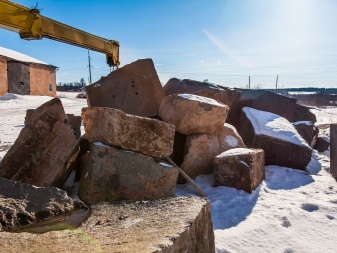
This method requires greater accuracy of calculations, any error leads to an increase in costs. A large amount of explosives will spoil the rock, with a lack of explosives, on the contrary, the pieces will turn out to be too large, they will have to be split again.
The drilling and blasting method is the most economical and at the same time the most destructive, since during an explosion only 70% of the rock remains suitable for further processing, while the remaining 30% goes to screening.
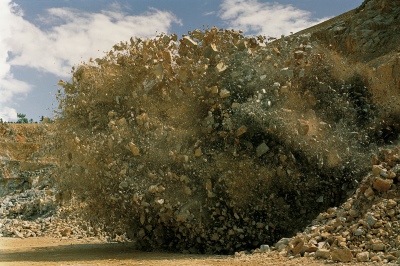
Splitting up
Then pieces of stones are loaded into trucks and taken to processing points in bunkers. From them, the material is sent to the feeders (special devices, thanks to which the supply of raw materials occurs evenly). The initial dimensions of the stones reach 50 - 120 centimeters, and the size of the finished product should be 0.5 - 12 centimeters. In the process of crushing, pieces can be reduced hundreds of times, so the work usually takes place in 2 - 4 stages.
Crushing can be of three types - large (up to 30 cm), medium (up to 10 cm), fine (up to 4 cm). In factories with modern equipment, the crushing process takes place simultaneously with sorting. At each stage, the rock undergoes preliminary sorting, when larger stones are separated from small ones.
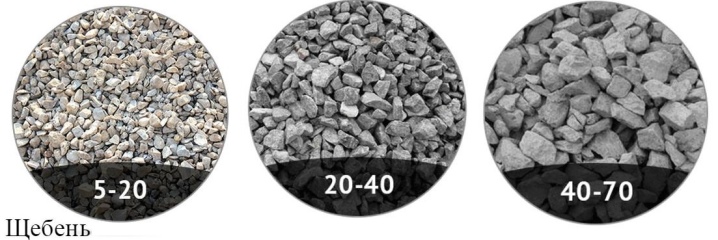
Thus, only those stones that need to be crushed are sent further into the equipment.
To work with crushed stone, 6 types of crushing equipment are used.
- Jaw - used at the first stage of crushing. Their principle of action is non-shock crushing. The equipment includes two slabs (cheeks), between which pieces of granite are placed. Then they begin to approach each other, thus crumbling stones.
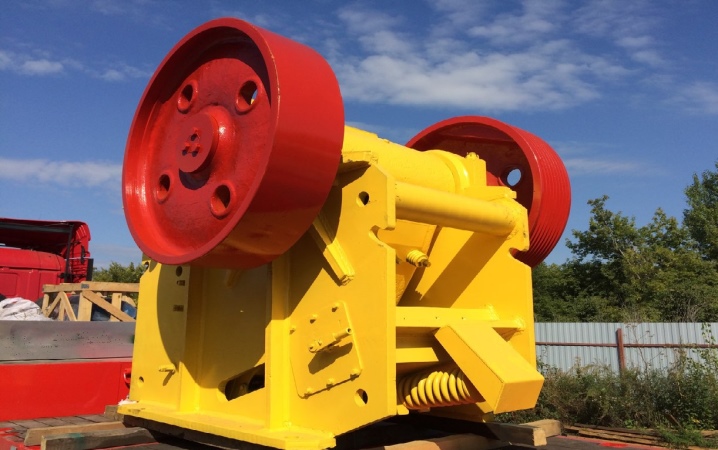
- Roller - the work takes place according to the same system, as in jaw crushers, only instead of plates, special shafts are built here, rotating in different directions. The surface of the shafts can be smooth, toothed or grooved.
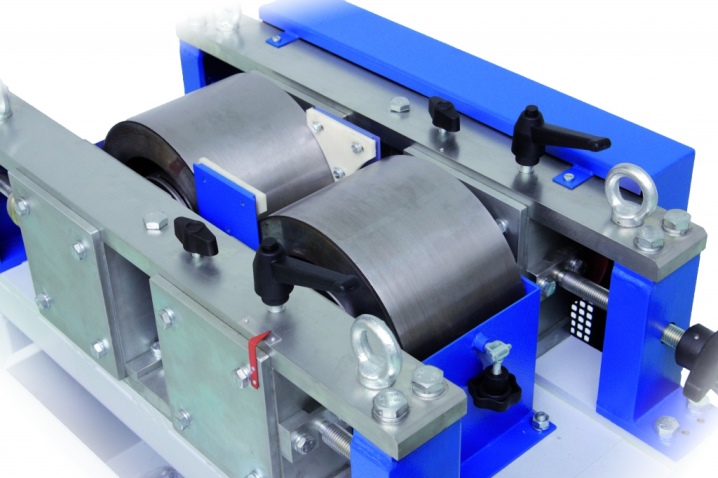
- Conical - used for grinding granite into small and medium dimensions. The design of such crushers is more complicated - in a stationary conical vessel there is a movable cone, the top of which is directed upwards. Through a special funnel, the stones are fed into the thicket, and the cone reciprocates, approaching the stationary base, thus crushing the rock.
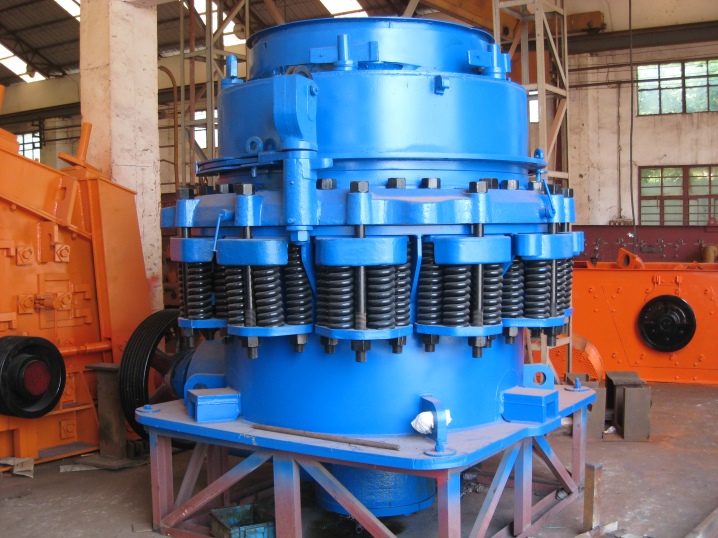
- Rotary - the principle of operation of these crushers is impact action. The device looks like a chamber, along the edges of which there are baffle plates, and in the middle there is a rotor. Beaters (shoulder blades) are attached to it. Granite entering the crushing machine cuts into the impact plates and into each other. The operation of rotary equipment is distinguished by a high level of selectivity - that is, the majority of granite stones are cube-shaped (80 - 85%).
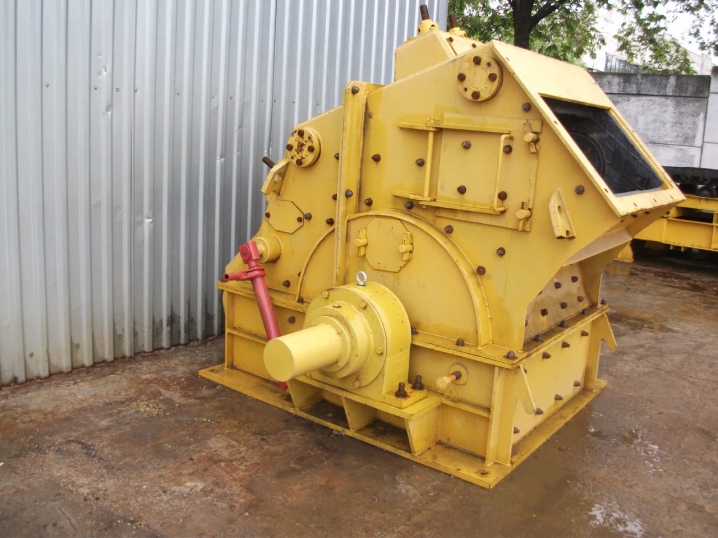
- Hammer crushers - the design of such crushers is identical to the previous type, but instead of blades, hammers work here. Most often, these crushers are used for soft rocks.
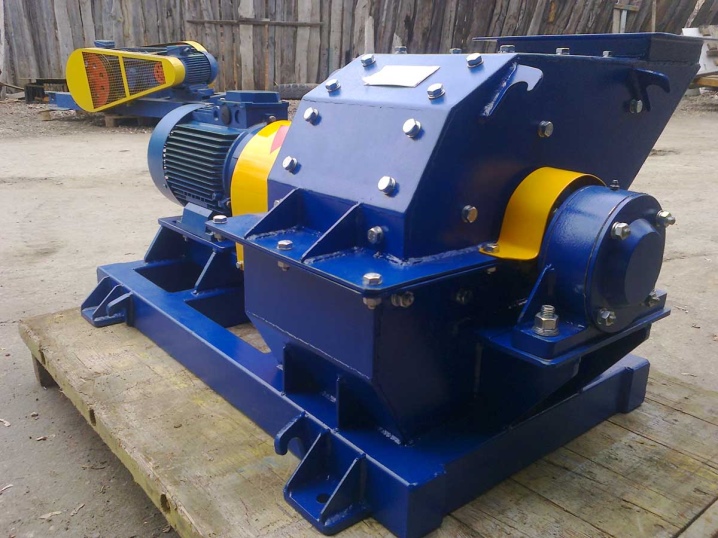
- Centrifugal - the crusher is a centrifuge, in which the rock at high speed hits its walls and against each other. This equipment is allowed to work with granite up to 10 centimeters.
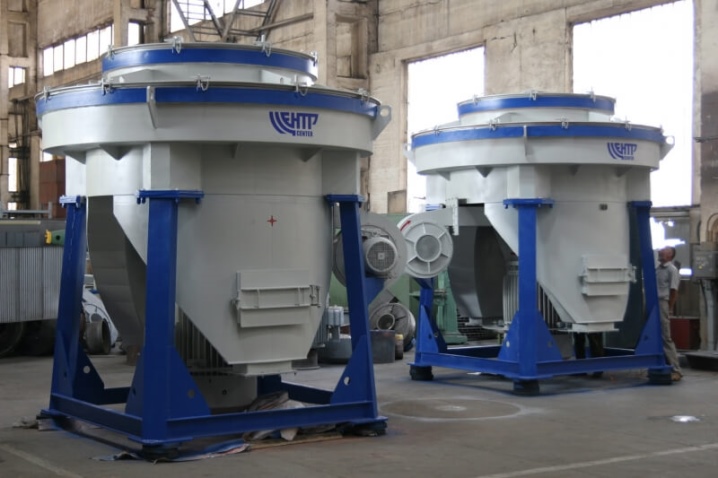
Sorting
After the rock has passed the crushing stage, it enters the screening vibrating screens - screens. They received such a name for the characteristic noise during operation. Sorting can be like this.
- Preliminary - here stones that do not require crushing are separated, and substandard, it is carried out before the crushing process.
- Control - performed after crushing. The process separates granite, which requires re-processing.
- Commodity - this type of sorting, crushed stone passes before being prepared for sale.
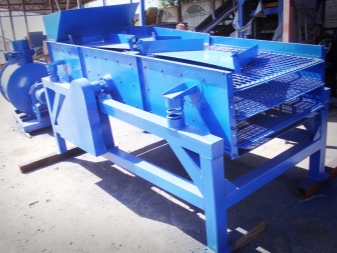
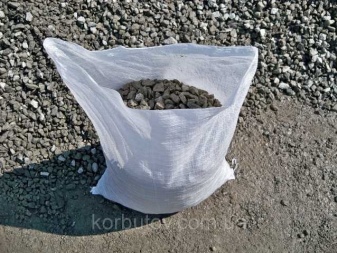
Main characteristics
- Flakiness - the degree of granite plane, the characteristic is determined by the presence in the rock structure of inclusions in the form of needles and plates. The adhesion to various substances will depend on the shape of the crushed stone. A lower flakiness coefficient indicates a high quality of granite.
- Strength - the characteristic is taken into account when erecting overall buildings. When crushed stone is compressed, its ultimate strength is shown. According to the standards of the current GOST, the percentage of stones with a minimum strength should not be higher than 5 units.
- Bulk density - the characteristic determines the specific gravity of 1 m3 in the natural state, that is, the voids and pores between the pieces are taken into account. How much the material weighs directly depends on it. To find out how many tons of crushed stone in a cube, you need to divide 1 ton (1000 kg) by the bulk density coefficient. Many manufacturers pack crushed stone into bags of 25, 30, 35, 40, 42, 45, 50, 55, 60 liters. To find out how many bags of rubble are in a cube, you can use special tables. This property determines how the products will be stored and transported, as well as how much cement mixture will be required during construction. The higher the density coefficient, the less mortar is needed.
- Frost resistance - the property characterizes how many defrosts and freezes the crushed stone can withstand. It is marked with the letter "F", and the number next to it indicates the amount of freeze / thaw repetitions - F15, 25, 50, 100, 150, 200, 300, 400.
- Radioactivity - taken into account when choosing a supplier of products. Crushed stone is a source of radiation; in addition, it can accumulate it. Crushed stone is divided into 3 categories: 1 - less than 370 Bq / kg - for the construction of residential and non-residential premises; 2 - 370 - 740 Bq / kg - for roadbeds and foundations of factories; 3 - more than 740 Bq / kg - permissible only for highways.
- Adhesion - this is an indicator of how tightly the crushed stone adheres to various substances. The highest adhesion of the breed is gray.
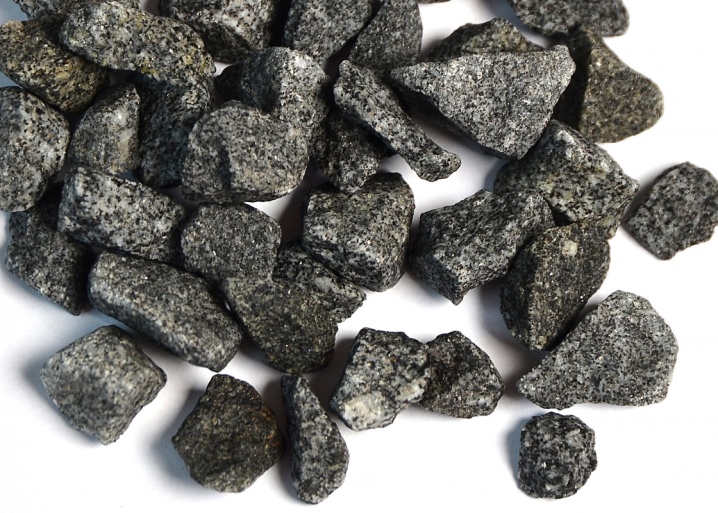
Types and brands
There are five varieties in total.
- М1200 - 1400 - high strength.
- М800 - 1200 - durable crushed stone.
- М600 - 800 - medium strength.
- М300 - 600 - weak strength.
- M200 - very weak strength.
The shade of granite depends on the area where the volcanic material was mined. It can be white, gray, pink, red, etc.
The color palette is determined by the abundance of inclusions in the structure of the granite stone.
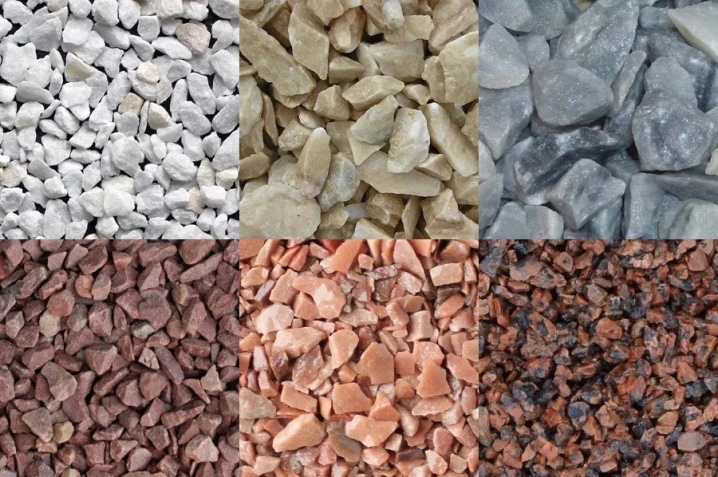
At the factories, crushed stone is subjected to additional processing.
- Flushing - is necessary for cleaning the material from dust and clay. The need for flushing arises only if the permissible rate for the presence of clay and dust particles is exceeded. The washing process is quite laborious and expensive; moreover, additional drying of the product is required. Washed crushed stone is rarely made and only for specific purposes.
- Bitumen impregnation - crushed stone with this treatment is used in road construction, it is covered with tar, bitumen or bitumen mortar. The process takes place in asphalt mixing equipment.Bituminous or black crushed stone cannot be stored for a long time, since its useful life is short, usually it is immediately sent to the work site.
- Dyeing - such processing is used only for decorative purposes. Granite can be stained in factories or at home. Colored crushed stone is produced only by prior order and in small batches. In this case, it is worth remembering that even the highest quality dye will fade or begin to chip over time.
- Grinding (tumbling) - such granite is also used in decorative works. Tumbled crushed stone is a material that has undergone mechanical stress, as a result of which sharp edges are smoothed out. Processing takes place in a tumbling drum, where natural stone, abrasive substances and water are placed. Due to friction against each other and against abrasives, the grinding process takes place.
Tumbling is a rather costly process, so polished crushed stone is made only by prior order.
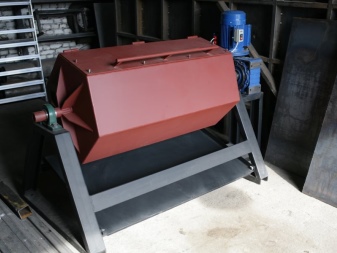
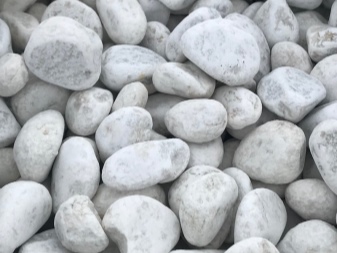
Faction overview
One of the most important characteristics of crushed stone is its fractionation, it is assigned at the stage of extraction, and then at the stage of processing granite. Subdivided into categories.
- From 0 to 10 mm - ShchPS (crushed stone-sand mixture), the composition contains components such as sand and crushed stone. According to GOST, the products have their own granulometric classification, respectively, there are several types of sand-crushed stone mixture. Excellent as a drainage layer, used for asphalting roads.
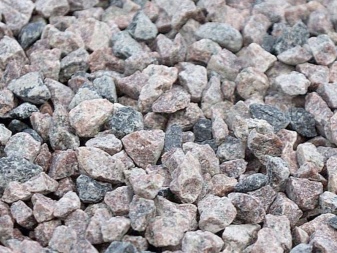
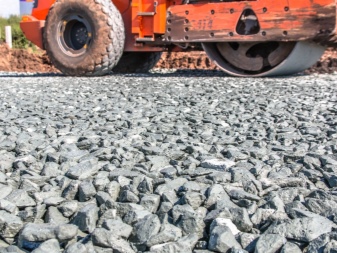
- From 5 to 10 mm - fine granite. The products are distinguished by their durability and affordable price category. It is used for the manufacture of concrete compositions used in work with massive and heavy objects.
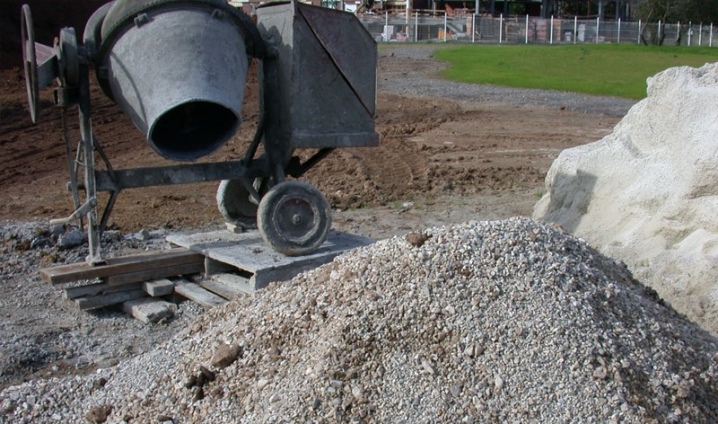
- 5 to 20 mm are two size grades mixed together. Ideal for laying the foundations of houses.
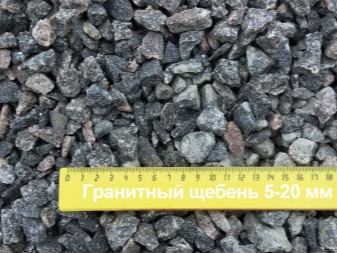
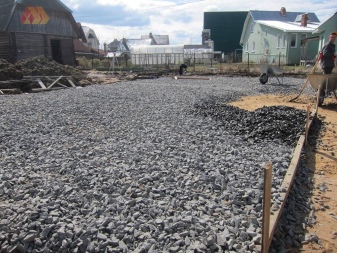
- 20 to 40 mm - Medium Granite, the material found its purpose in filling the foundations of residential buildings, factory premises, asphalting, laying tram lines.
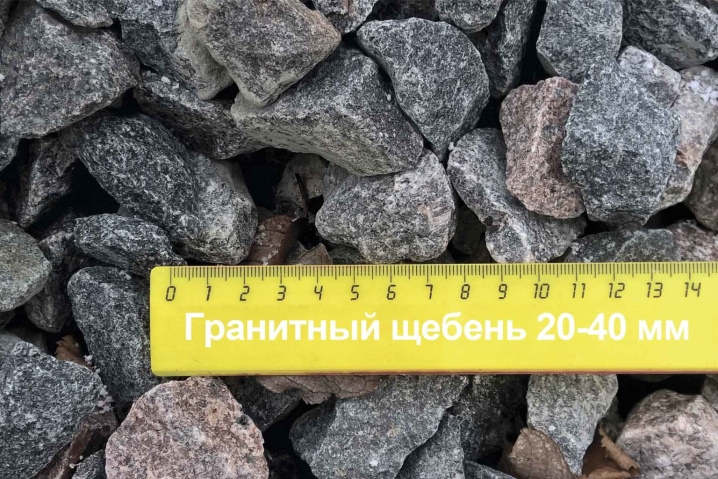
- From 40 to 70 mm - high-strength large-sized granite stones. They are used on construction sites of large-scale objects.
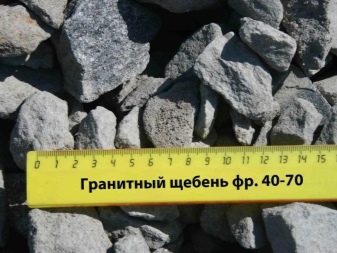
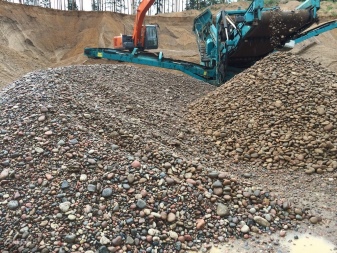
- 70 to 120 mm, 150 to 300 mm - granite of large standard size with irregular shape. GOST for this category is listed in special tables used in the construction of bridges and dams. Due to its increased strength, it is used when laying rubble concrete base.
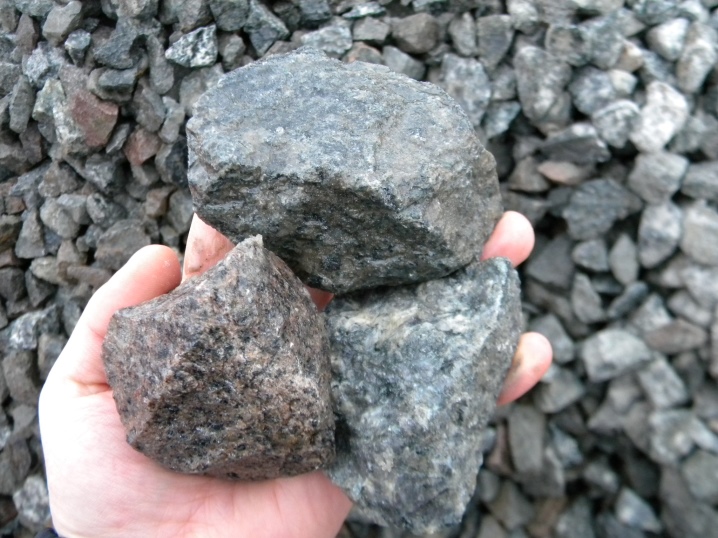
Dropout
Fraction from 0 to 5 mm or granite chips - this category is the smallest, it appears as a secondary or side material. The appearance of the screenings resembles sand, but with the properties of granite.
It is used in the arrangement of pedestrian paths, sidewalks, park areas.
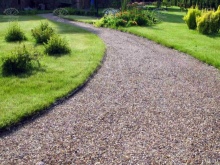
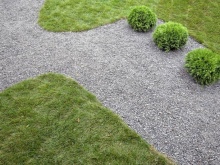
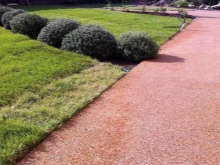
Applications
- In construction - for creating concrete, a drainage layer, for splitting into smaller sizes, strengthening the soil under the foundations of buildings, for leveling plots and sites.
- In road works - for dirt, asphalt and railways.
- Land improvement - for paths and paths, entrance to the territory, soil compaction, dumping of parking areas and sports grounds, protection from ice and ice.
- For landscape design - decoration of flower beds, streams, artificial water bodies, gabions and alpine slides.
- In production - for paving stones and reinforced concrete products, mineral bulk substances.
- Engineering works - for bridges, dams and dams, overpasses.
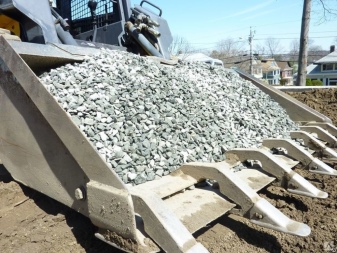
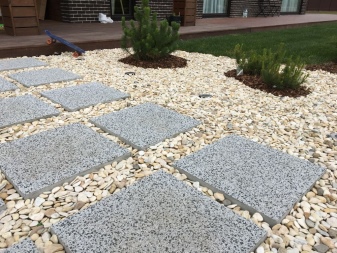
The comment was sent successfully.