All about Knauf water panels
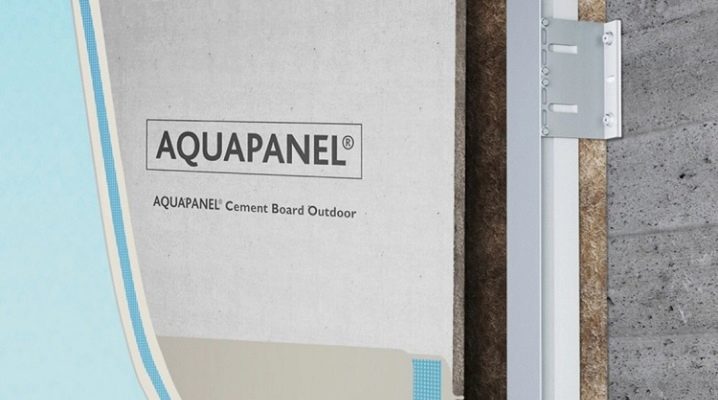
For the implementation of interior and exterior facing works, ready-made dry compositions are practiced, often unable to cope with their functions in conditions of high humidity. The problem is eliminated by adding various modifiers to the mixture or by adding an additional layer insulating against water, which increases the cost of the work.
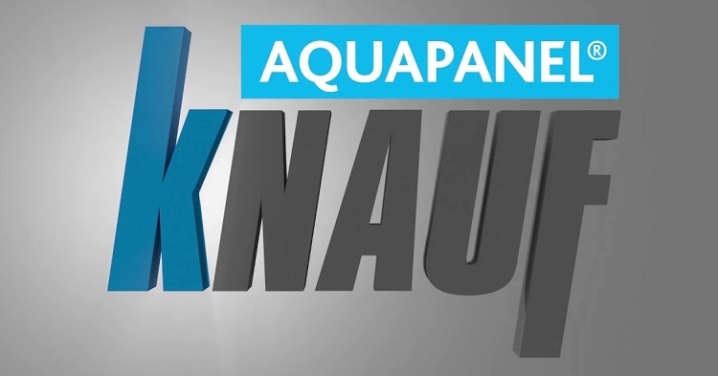
Actually, for such tasks the company from Germany Knauf and has created water panels that are suitable for interior and exterior decoration of premises for various purposes... Let's talk about the key characteristics and properties of Knauf water panels.
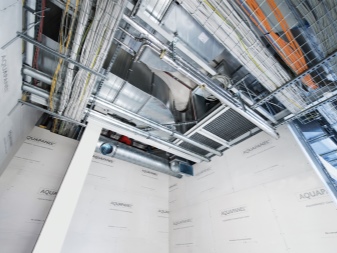
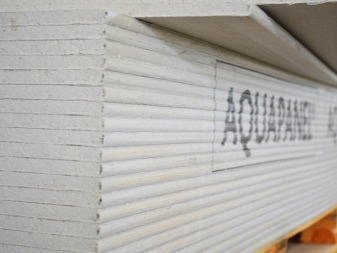
What it is?
Aquapanels are a sheet material in the shape of a rectangle based on a lightweight material consisting of small granular particles of aerated concrete. At all edges, except for the end edges, the panels are reinforced with fiberglass mesh. The ends are reinforced with fiberglass. Due to the fiberglass mesh, the sheets can be bent without preliminary moistening with a radius of up to 100 centimeters. This makes it possible to veneer non-linear surfaces.
The material is absolutely moisture-resistant, does not swell or crumble from moisture, is resistant to mold and mildew, is hardy and shock-resistant. Keeps the geometric dimensions and configuration unchanged in a variety of weather conditions and temperature fluctuations.
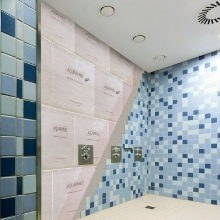
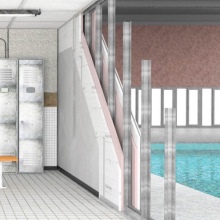
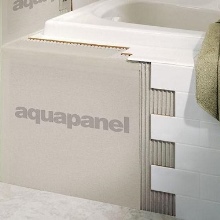
It does not need special sealing, it is indispensable for the protection of damp and unheated rooms - loggias, baths, showers, bathrooms and others. Water panels are not afraid of moisture, which is concentrated on the finishing cladding (for example, tiles) and seeps through the seams or areas of the walls. The material showed itself excellently even when used in hammams and public baths, where the temperature reaches +70 degrees. It is equally suitable for facing fireplace portals.
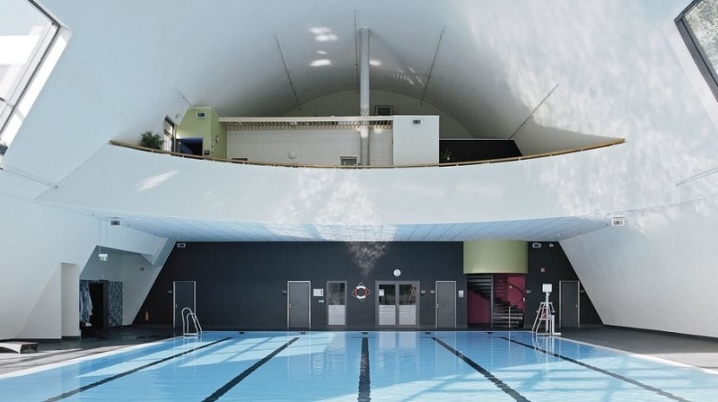
This building material does not swell even if it is completely immersed in liquid. There are no organic substances in the structure of the aquapanels, therefore they do not rot. And the absence of asbestos in the material makes them completely harmless to human health. Among the positive features with which this material is endowed, one can indicate:
- high reliability;
- resistance to strong mechanical influences;
- the ability to finish curved surfaces.
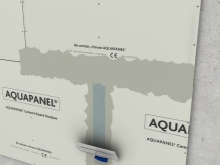
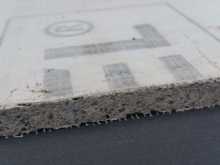
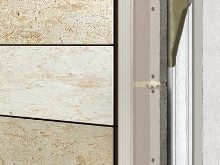
Assortment overview
Currently, this material is produced in two versions.
Sheet materials
All panels are divided into front (external) and internal. There is some slight difference in size and individual parameters.
- The fundamental property of a building material is exceptional moisture resistance. To date, there is no material with similar characteristics. There are similar panels that are able to maintain their physical qualities in rooms with high humidity, only they have a limit.
- Panels have a rectangular configuration and include an impermeable Portland cement and lightweight mineral filler core. Their surfaces are reinforced with reinforcing fiberglass mesh. All this helps to protect against mold and mildew, which periodically appear in rooms with high levels of humidity.
- It's pretty easy to work with them. An ordinary knife is required for cutting. He will effortlessly make cuts along the fiberglass mesh, and then you can simply break it with your hands.And also it will not be difficult to mount the water panels on the wall or ceiling. A quickly assembled structure made of wooden blocks or metal profiles will serve as a base on which the panel will be fixed with ordinary screws.
- Thanks to innovative developments, this building material is multifunctional. It is suitable both for interior cladding of premises and will be an excellent base for finishing decorative cladding of external walls. Since it is able to withstand extreme atmospheric conditions, sharp temperature fluctuations.
- The panels have a long service life, up to 50 years. And by the end of the operational period, they, in essence, do not lose their physical parameters.
- Thanks to the reinforcing fiberglass mesh, aquapanels have the ability to bend with a radius of up to one meter "dry", that is, without pre-wetting. They will be ideal when decorating rooms with arched structures.
The panels are able to become the basis for any finishing cladding. Since they have a smooth, absolutely flat surface.
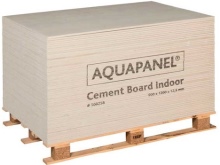
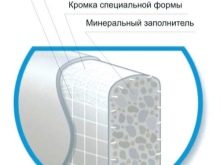
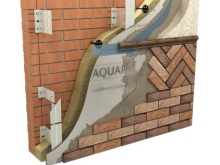
To determine the choice of building material, you should familiarize yourself with the assortment and some of the characteristics of Knauf water panels.
- Universal cooker. Cement panel is a strong and durable multifunctional building material intended for use as a base for any kind of finishing wall and ceiling cladding, mainly in rooms with high humidity levels. The material is used as a base for ceramic tiles and plaster. The slab serves as an unshakable protection against atmospheric influences. Technical specifications:
- size (L × W × T) 1200x900x8 and 6 mm;
- the smallest bending radius is 1 meter;
- weight 7.0 / 8.0 kg / m2.
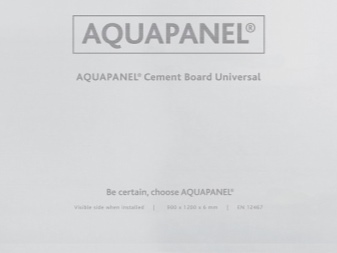
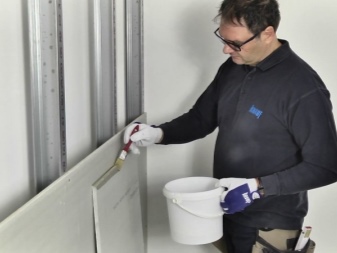
- Skylight Stove is a lightweight and sturdy slab for installation on the ceiling of suspended structures indoors and outdoors. Technical specifications:
- size (L × W × T) 900x1200x8 mm;
- the smallest bending radius is 1 meter;
- weight about 10.5 kg / m2.

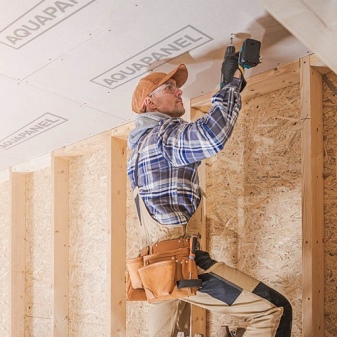
- Outer plate is a strong and durable building material. The material gives all the advantages of the "dry construction" method, its strength is comparable to the characteristics of blocks and bricks. It provides a solid foundation that can withstand extreme weather. Technical specifications:
- dimensions 900x1200, 900x2400, 900x900; 900x2000; 1200x1200; 1200х2400х12.5 mm, as well as by special order, length - 2500/2800/3000 mm;
- thickness 12.5 mm;
- weight about 16 kg / m2.
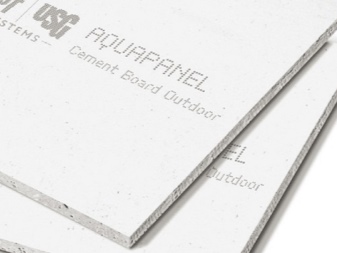
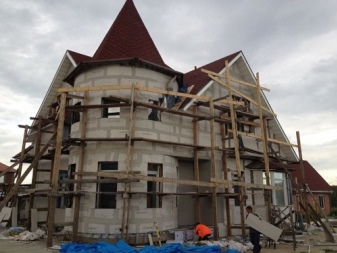
- Internal plate is a strong and durable building material that is used as a base for any kind of finishing inside the object. Technical specifications:
- width 900/1200 mm;
- length 1200/2400/900/2000/2400 / by special order 2500/2800/3000 mm;
- thickness 12.5 mm;
- weight about 15 kg / m2.
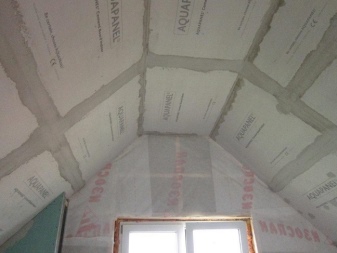
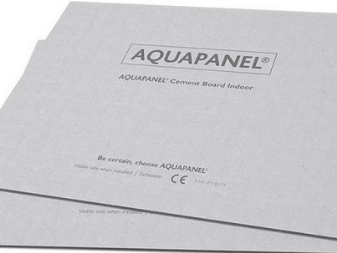
- Slab Base Tile Flooring is a lightweight, highly durable cementitious panel that is used as a thin base under a wide variety of tile and stone types for installing timber floors. The material is mainly suitable for the installation of thin floor structures. The panel thickness of 6 mm guarantees a smooth transition between tiles and carpet, which eliminates the appearance of thresholds at the border of two floor coverings. Specifications:
- dimensions (L × W × T) 900x1200x6 mm;
- weight about 8.5 kg / m2.
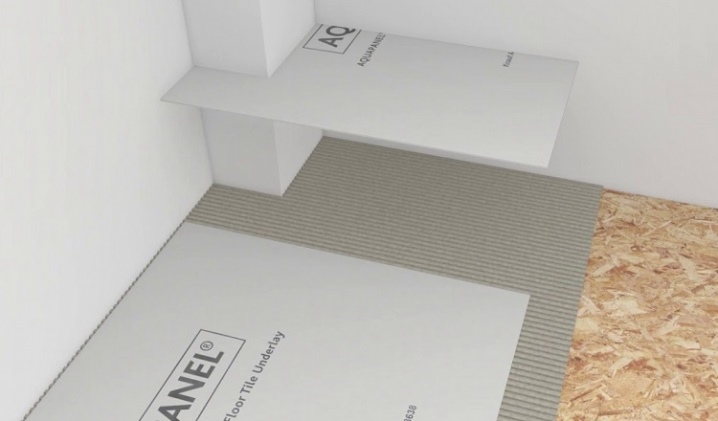
Complex systems
- Suspended facade system with an air gap is a multilayer construction for insulating the load-bearing part of the wall. Excellent protection of the heat insulator against the effects of wind and rain. It is used to insulate walls from the outside in structures for various purposes:
- protection of walls from weather factors;
- ventilation of the inner layers of the outer wall structure;
- protection of the heat insulator from dampness;
- smoothing thermal destruction;
- alignment of surface irregularities;
- the ability to manufacture smooth seamless surfaces.
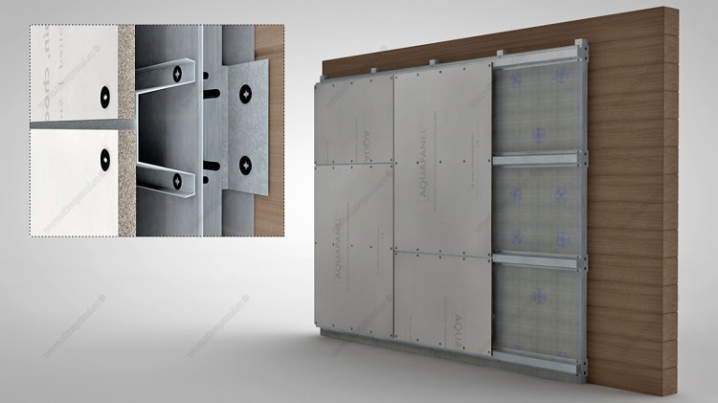
- Outer wall. Frame-sheathing non-load-bearing external enclosing structure. A lighter, more flexible and thinner building system compared to bulky block and brick structures. It is practiced for the construction of facades in buildings of different directions:
- an alternative to block and brickwork;
- short construction time;
- slim and lightweight design;
- reduction in the cost of construction work;
- the ability to form curved surfaces.
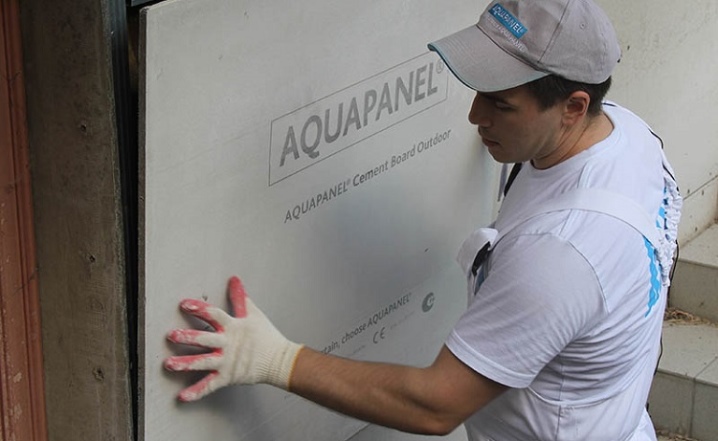
- Internal. Structural elements of partitions with one-layer and two-layer cladding from the Internal Aquapanel slab on an iron or wooden frame. Practiced as internal enclosing structures in various types of premises, including rooms with damp and humid operation:
- high moisture resistance without destruction and shedding;
- immunity to mold and mildew;
- able to withstand elevated temperatures;
- high impact resistance;
- simple and quick installation;
- the formation of nonlinear surfaces.
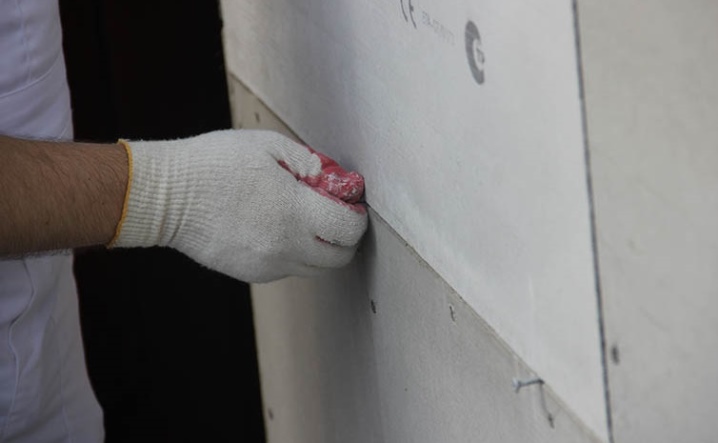
- Skylight. Constructions of suspended ceilings in rooms with a wet operating mode (RE) - swimming pools, latrines, steam rooms, bathrooms and shower rooms, as well as car wash complexes, when used outside. Protection of building structures from dampness, natural factors and mold.
- light weight of the slab - easy and simple to install;
- for indoor and outdoor use;
- 100% moisture resistant;
- immunity to mold and mildew;
- protection from atmospheric influences;
- the formation of curved surfaces.
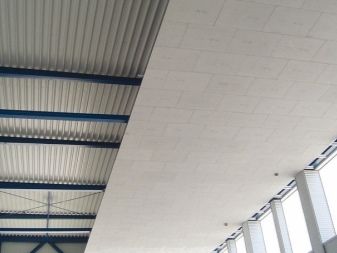
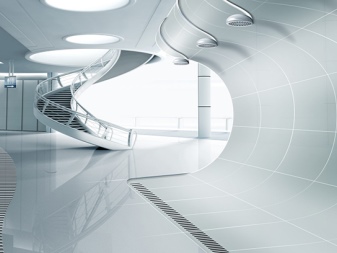
Components
Knauf manufactures specialized materials for working with water panels.
- Cement-based white putty - to prepare the base for painting or plaster for decorative wall decoration. With a 4 mm layer thickness, the consumption is 3.5 kilograms per m2.
- Cement based gray putty - for sealing butt joints between sheets. Consumption when sealing butt joints is 0.7 kg / m2. When filling the surface, the consumption is 0.7 kg / m2, if the layer is one millimeter thick.
- Interior primer - to enhance the adhesion of the tile adhesive to the boards. Consumption 40-60 g / m2.
- Polyurethane joint glue. Sold in ready-made tubes of 310 milliliters, consumption 50 ml / m2 (one tube is enough for 6-6.5 m2 of wall).
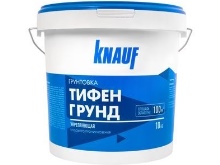
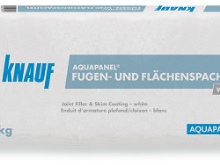
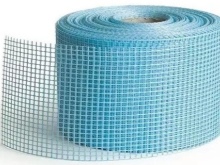
Installation tips
It is advisable to carry out installation work during the finishing work, before mounting the finished floor, when all the "wet" work has already been completed, and the wiring and pipes have been wired. Indoor temperature should be no more than + 10 ° C.
Attention! Due to the high weight of the panels (35-55 kilograms), it is advisable to work with them with a partner. Despite its high strength characteristics, this material is quite fragile when unsecured and must be moved carefully.
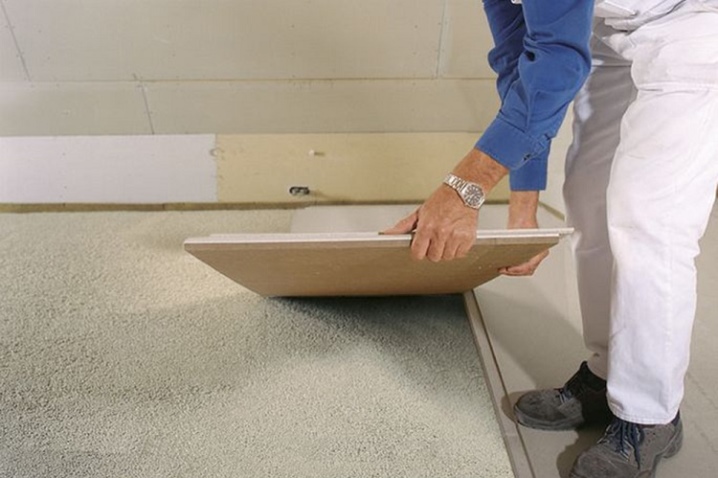
The installation procedure for water panels covers the following phases of work.
- Layout of the location of the cladding on the walls, floor and ceiling.
- Installation of the skeleton.
- Installation of electrical wiring and communications inside the skeleton. Installation of embedded elements for heavy attachments.
- Laying and fixing the insulation (if required).
- Facing the frame with Knauf aquapanel panels.
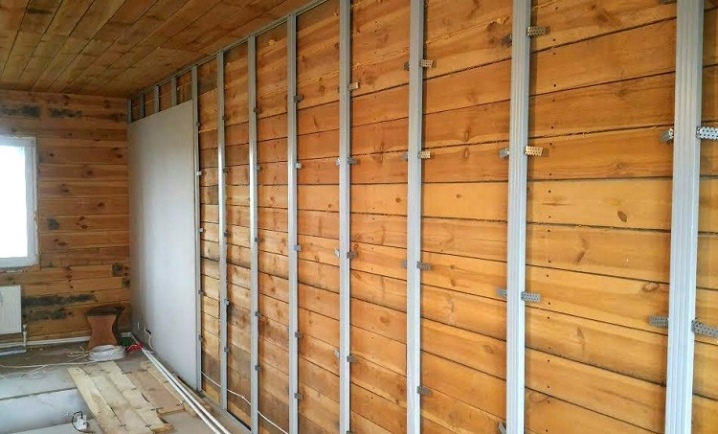
Attention! Installation can be carried out exclusively on a frame made of strong and reliable rigid profiles; it will not work to glue the boards like gypsum plasterboards due to the large mass.
- First, the sheet is screwed onto the self-tapping screws to the skeleton in increments of no more than 25 centimeters. When screwing in the self-tapping screws for lining the frame, be sure to press down on the panels, otherwise they will come off and crack.
- The edges of the panel are wiped off dirt with clean water.
- The adhesive composition from the tube is applied along the contour of the sheet to make tight joints.
- The adjoining sheet is attached tightly so that excess adhesive comes out.
- After 24 hours, the excess glue is cut off with a spatula or knife.
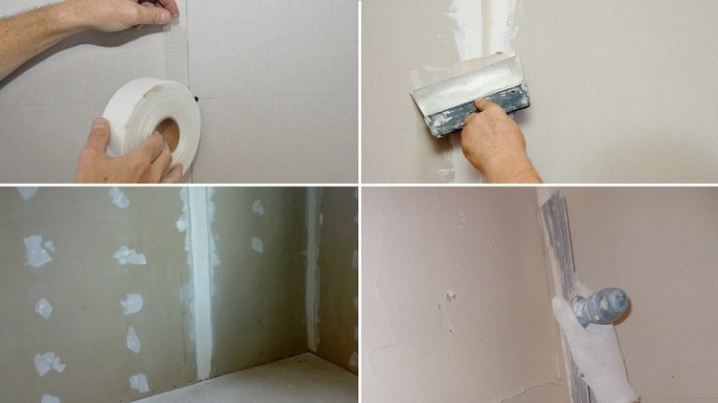
You can cut the slab with an ordinary knife. It is necessary to cut the top layer of fiberglass, and break the core, and then cut off the rest of the fiberglass from the bottom. It is uncomfortable to cut panels with a simple clerical knife due to the large free play of the blade, the cut will come out uneven.
- Putty of butt joints for each layer of cladding.
- Installation and putty of Knauf PU 31x31x3000 mm Corner Protective Profiles.
- Finishing putty of joint joints, self-tapping screw heads and priming for finishing lining.
- Wall cladding is carried out after installing the finished floor.
Ceramic tiles can be laid the next day after finishing the wall and floor cladding with water panels.
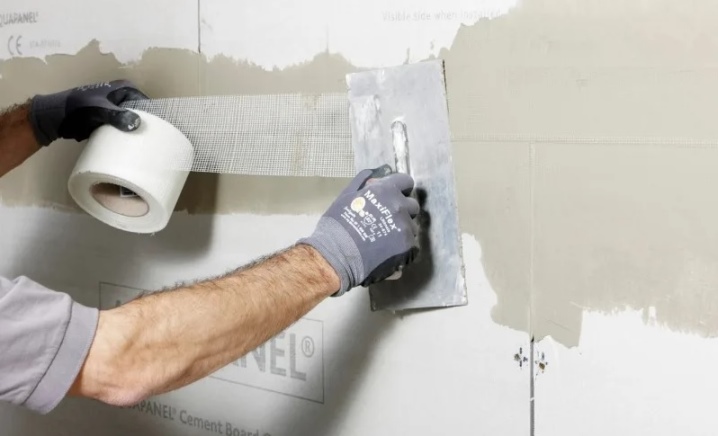
Facade cladding specifics
The outdoor Knauf water panel is mounted differently.
- A sheet of a suitable size is applied to the frame. Clearances on each side should be 3-5 millimeters. To make the perfect gap, slip self-tapping screws under the slab.
- On self-tapping screws 25-35 millimeters, we attach the panel along the edges and in the middle to the skeleton. We remove the supporting self-tapping screws.
- Using the Knauf Sevener mixture, we cover the butt joints. The average thickness of the adhesive should be no more than 3 millimeters.
- Immediately after that, we attach and press a strip of fiberglass mesh 15 centimeters wide with a spatula into the solution.
- After 3-5 hours, we apply a 4-5 millimeter layer of mortar to the entire plane of the panel, and reinforce it with a wide fiberglass mesh.
After 3-5 days, the wall will be ready for subsequent finishing work.
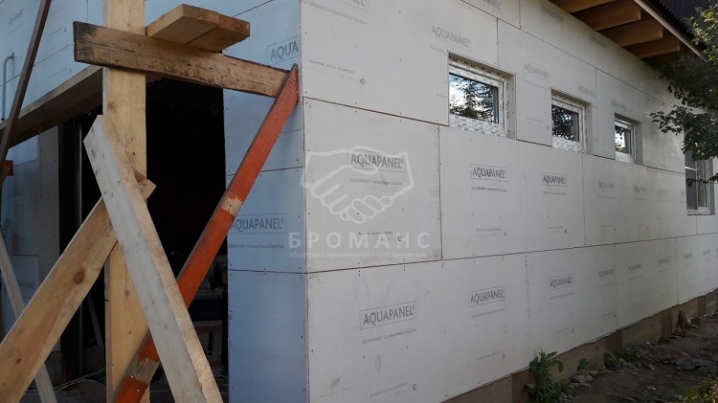
The comment was sent successfully.