All about band saws

The band saw machine is considered high-tech equipment, it can work with a variety of materials and cut curly and rectangular contours. The principle of operation is based on the functioning of a tape of durable flexible steel, connected in a ring. The machine was patented in England at the beginning of the 19th century. But only a hundred years later they learned how to correctly connect the cutting blade, which ensured the jewelry cutting accuracy.

Peculiarities
The band saw is the main tool for working with a wide variety of materials. The band saw consists of a flexible looped band with teeth on one side. The tape is put on the pulleys that are attached to the engine.
Saws can be made in a wide variety of configurations, which makes it possible to use such a tool in a wide variety of areas: from furniture production to the manufacture of building materials. Varieties of band saws:
- toothed;
- toothless;
- electrospark principle of action.



This tool differs from simple hacksaws in that it has a closed principle of operation. Almost any material can be cut with such devices.
Aggregates operating on friction and electric spark action are somewhat different from classic band saws.
When choosing a device, you should know how such a unit functions. For example, a band saw for metal is cutting all kinds of workpieces. The presence of rotary mechanisms makes it possible to cut at any angle. Band saw selection criteria:
- engine power;
- how much the unit weighs;
- what are the dimensions of the pulleys.


Differentiation of equipment is usually like this:
- pulley diameter 355 mm - considered a light machine;
- pulley diameter 435-535 mm - medium;
- if the diameter exceeds 535 mm, that such machine is considered heavy.
The first type of machines is equipped with a 1.9 kW engine, if the unit is more massive, then its power can reach 4.2 kW.
Special standards are required for the canvas. When cutting metal, bimetallic blades are also used; they are made of several types of materials. Most often it is:
- durable plastic steel;
- wire made of special high-strength steel.


Canvases based on carbon steel are very popular. Tape blades also vary:
- with congruent density Constant hardness;
- with flexible base and durable Flex back - Hard Edge teeth;
- hardened Hard Back canvases.



The first blades, whose hardness coefficient is identical, can work on pulleys with minimum diameters; at the same time, their strength can reach 49 units (HRc scale).
Saws of the second type, which are made of ductile steel, have a hard tooth and have a rather complex structure. Only the upper edge of the cutting tooth is hardened (hardness 64–66 on the HRc scale).
And finally, the third type is the most durable (hardness up to 68 on the HRc scale).
The hardness of the teeth provides the level of productivity of the tool, its durability.
If there is a high stiffness of the band, then it is possible to do sawing work at high feed rates.


Device
The principle of operation of a band cutting machine is simple: there is a frame on which an electric motor and roller wheels are fixed. A flexible tape with teeth moves along them.Power from the engine is transferred via a pulley to this dynamic unit, which is adjusted using head equalizing springs.
The equipment operates from the network in three phases and one phase, much depends on the type of model. The workpiece is fed at a certain speed that can be adjusted. The parameters of the teeth are related to the width of the working area (usually it has a ratio of 1/5).
The machine can have 4 pulleys, the number of pulleys reduces the size of the machine and lengthens the working blade. The blade itself can be tensioned hydraulically or manually. A strain gauge is used to check the belt tension level.



Blades can be of universal and specialized types, they can be used for various types of steels. Much depends on the characteristics of the teeth, which vary according to the following criteria:
- sizes;
- hardness coefficient;
- configuration;
- grain;
- sharpening.

An example is the fact that large-toothed blades are used to process metal sheets. The use of teeth of different sizes is also practiced, which significantly reduces vibration and increases cutting efficiency.
The performance of the tool and its durability directly depends on the steel grade that is used. Usually, M44 metal is used (this designation indicates the strength of the edge on the Vickers scale - 950 units).
There are few such indicators for machining strong steel, therefore, the hardness of steel grade M72 is required for the teeth (100 points are present on the Vickers scale). The average hardness of the material starts from the M52 mark.


The configuration dictates the sharpening angle as well as the shape of the cutter's profile.
The teeth must have reinforced backs, then it will be possible to process hardened steel, which is present on such elements:
- corner;
- channel;
- pipe.
When working with tough steel, a large gap is left between the teeth.
The setting of the teeth in band saws is also important. For example, if you have to machine a large solid wood, you need to create a narrow and wide set, then you can avoid pinching the tool.


Views
The types of tape aggregates depend on the density of the texture with which they work:
- saw on stone;
- saw for aluminum (soft metals);
- diamond saw for carbon metals;
- saw for processing stainless steel;
- mini hand saw for wood.




When cutting dense materials, the blade is reinforced with teeth made from special alloys. This must be done - otherwise the tool may become unusable. Also band saws are:
- tabletop;
- rechargeable;
- vertical;
- horizontal.
Joiner's band saws are mounted on a base on which various elements are mounted. You can design a band saw yourself if you want, it is not particularly difficult to do this. A solid block of wood is used for the bed to reduce vibration. The plane of the desktop is sheathed with thick sheets of plywood. Corners are attached to the sidewall. The carrier bar is machined from the beam. The necessary drawing is preliminarily drawn, where all the necessary calculations are carried out.
It is important that the size of the device corresponds to the necessary needs, then the work on the unit will be comfortable. Be sure to take into account the location and parameters:
- pulleys (lower and drive);
- placement of the engine itself;
- where the shavings will go.


Most often, the bed is made in the form of a massive quadrangular block, the sides of which are closed. The sidewall is formed in such a way that waste chips accumulate in them, which is then convenient to collect.
The tabletop is usually mounted on a frame, sometimes there is not enough height, so this kind of structure can be of help.
The bar is made of an 8x8 cm profile, supports are attached to it, on which the wheels are attached.Supports should be made of durable material that can withstand significant loads (wood, metal). The distance between the wheels should be such that a massive log can easily pass between them.
The thickness of the pulleys can be any: the stronger the pulley, the better the result will be. There are generally accepted standards for the ratio of the working blade to the pulley thickness: 1/100. Example: if the belt is 5 mm wide, then the wheel should be 500 mm. The edge of the pulleys is machined and sloped, which allows the center to be re-centered automatically. On the pulley itself, it is necessary to cut a groove so that the belt is attached there. Often, bicycle tubes are attached to the pulley, which prevents the belt from sliding off.



The upper pulley is mounted on a block that moves horizontally. A block is required for this, the role of which can be successfully played by an ordinary bar, which is attached to the lever.
The lower pulley is made up of two wheels that are attached to the axle. One wheel performs a driving function, the other a driven one. When setting up the unit, it is important that the wheel has no backlash - this will avoid the appearance of "eights".
After completing the assembly of the unit, tests are carried out: it is important that all units work harmoniously, there is no excess vibration, which has a detrimental effect on the material and fasteners.
It is also important to correctly position the guides on the bar along the saw end: the saw should run smoothly and the band should not sag or deform.


Often they do this: three bearings are attached to the beam, two of which set the direction at the edges, and the third supports the tape. Often, in addition to the bearings, wooden retainers are mounted.
Soldering the tape is an important step on which success in work depends. It usually takes place in an equipped workshop. Guides are most often made dynamic so that the elements can be adjusted. It is imperative to make a protective apron that covers the pulley. In case of slipping, the employee will not be injured.
The engine is also closed with an apron - this will extend its service life, less mechanical particles will get into it


Manufacturers rating
The best band saws are manufactured by Makita and Bosch, and the reviews are 95% positive.
Makita 2107FW
- band-saw;
- power - 715 W;
- speed is regulated progressively;
- weighs 5.8 kg;
- costs from 43 to 52 thousand rubles.
Differs in accuracy, performance and endurance. One consumable is enough to process up to 3 tons of metal.


Makita 2107FK
- power 715 W;
- speed is smoothly regulated;
- weight - 6 kg;
- costs from 23 to 28 thousand rubles.

Bosch GCB 18 V – LI
- works from the power supply;
- speed is adjusted gradually;
- weighs 3.9 kg;
- costs from 18 to 22 thousand rubles.

Bison ZPL-350-190
- power 355 W;
- weighs 17.2 kg;
- costs 11-13.5 thousand rubles.
The guides are not very strong, the saws also become dull quite quickly, but in general the unit is trouble-free and works perfectly.

Makita LB1200F
One of the best band saws is the Makita LB1200F:
- power 910 W;
- weighs 83 kg;
- costs from 46 to 51.5 thousand rubles.
Nice build. The set includes 4 saws. All knots fit perfectly. Smooth cast iron table. You can increase the cut up to 235 mm. Works quietly. Saw cut of excellent quality at different speeds. High quality aluminum stop. Excessive vibration appears at too high speeds (this is a drawback). The guides are on bearings, the pulleys must be adjusted. Large weight, but it is difficult to call it a disadvantage, the stability is excellent.


Proma PP-312
- engine power 810 W;
- weighs 74 kg;
- the price is from 49 to 59 thousand rubles.

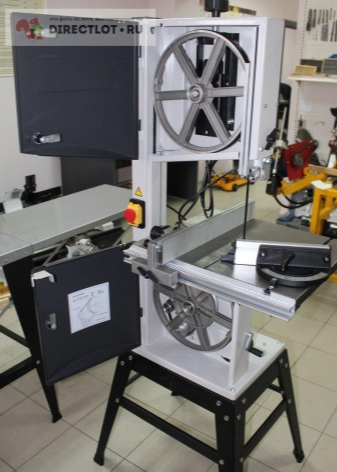
JET JWBS-14
- engine power 1100 W;
- weighs 92 kg;
- the price is from 89.5 to 100 thousand rubles.


Additional accessories
The cutting unit can be easily upgraded. Some additional accessories help significantly in the work process.
- The good rip fence and rip fence allow quality straight cuts. When processing narrow parts, the stop can be located close to the machine, sometimes it is even placed under the guide block. Some models have additional regulators in the kit that change the parameters of the stops.
- For a band saw, it is necessary to set the guides correctly, then the band will not deform significantly.
- The setting of the teeth is done manually or for this purpose, an adjustable machine is used. Correctly adjusted teeth affect tool life and noise and vibration levels during operation.
- A strain gauge is a device for measuring tape tension, it is difficult to do without this device.


Choice
Before choosing the right tool, you should know the main criteria by which band saws differ:
- the size of the cut;
- which canvas is involved;
- Energy consumption;
- engine power;
- compactness of parameters;
- the weight;
- the ability to customize;
- type of material supply.


The equipment can be different, in accordance with this, the prices for it vary.
The belt itself can also change the speed of movement from 12 to 98 meters per second.
Also, the units differ in the parameters of the belt tension. The tape has a power of 2100 W and can reach 3000 W and even more.
When choosing equipment, do not forget about the importance of the cutting belt, which bears the main load. Usually, products of a wide type are preferred, since a thin fabric deforms quickly enough and fails. If you have to process workpieces where there is thin metal, then you have to use a narrow belt.


Visually, it is easy to determine when buying: if the tape has large teeth, this means that it cuts to a great depth. There is one more indicator - this is the setting of the teeth, it directly affects the efficiency of the saw. For small jobs, a wave profile is sufficient. The most effective option is the arrangement of the teeth in pairs.
Subtleties of operation
During cutting, the saw inevitably loses its performance characteristics, the teeth become dull. Periodically, it is necessary to do the correct sharpening, spreading and adjustment. To set up the instrument correctly, you need to follow these phases:
- preliminary sharpening;
- cleaning;
- product wiring;
- finishing sharpening.


To restore the technical characteristics of the cutting tool, as a rule, cutting machines are used. First of all, defects in the sinus of the tooth should be eliminated, as well as its symmetry with respect to other elements should be reanimated.
During routing, the angle of inclination of the front and rear corners changes. Finishing sharpening "brings gloss", aligns all elements. To do such a job correctly, practical skills are required: in order for the teeth to return to the same thickness, it is often necessary to cut the saw edge to a rather large depth.
It is also recommended to carefully read the instructions that are attached to each unit of the sold product.
Replacing V-belt drive belts can also be helpful. The old pulley "remembers" the trajectory of movement, over time it becomes too rigid. Causes this phenomenon to excessive vibration. It is recommended to change such a belt to a segment one, which is more flexible.


The balance of the saw pulleys should be adjusted periodically. To do this, first you need to cut off the old belt and see how the pulleys work in free mode.
Both pulleys are marked relative to the bed, the operation is repeated several times. If the marks have good spread, then the pulleys are well adjusted. If the marks are grouped at one point, then the pulley must be aligned.
If you want to saw the side boards, then you need a wide band with teeth with a special sharpening angle. Variable tooth pitch is also practiced quite often.


Double bearings are also very important: they prevent the blade from curling, reduce vibration and coefficient of friction. Also, double bearings significantly reduce the heating temperature of the working part of the tool, which significantly extends its service life.
Ceramic crackers are also important - these inexpensive devices will reduce the friction of the tape during operation, and reduce the temperature. Ceramic crackers practically do not grind, the manufacturer gives a 50-year guarantee on them.
In work, it is also important to have high-quality springs, it is easy to replace them. It is better to put more massive springs - they are cheap, but they provide a good tension to the tape.
The handwheels are also important in the operation of the band saw. It is best to use a cast small flywheel (145 mm) which has a convenient swing arm. Such an important "trifle" allows you to easily adjust the tension of the web.


When working, it is important that good lighting is present. You can additionally purchase LED lights that will illuminate the work area. These devices are low power consumption and the battery can be placed at the bottom of the machine.
When purchasing a unit, you should definitely think not only about the performance characteristics of the mechanism, warranty conditions, the availability of borers on the market and their cost are also important.
Before buying, it is advisable to read the reviews on social networks. In recent years, innovative Bilork band saws have appeared on the market - they are made of ultra-strong steel with various composite additives, such a material withstands a record number of sharpenings.

For the safety of working on a band saw, including a homemade one, see the next video.
The comment was sent successfully.