Spray gun pressure gauges: purpose and principle of operation

Using a pressure gauge for a spray gun improves the quality of the painted surface and reduces paint consumption. From the article you will learn why ordinary pressure gauges and models with an air pressure regulator for a spray gun are needed, the principles of operation, and how to connect them correctly.
Appointment
To paint a product quickly and well, you need to correctly configure the equipment. The air pressure in the atomizer plays a major role in this. If it is weak, then the paint will fly out in large drops, streaks and graininess will appear on the product. If too strong, the color will be uneven.
The pressure gauge installed on the compressor will not give the required measurement accuracy. The air flow weakens in the fittings and transitions, is lost in the hose, falls on the moisture separator. Total losses can be up to 1 ATM.


Therefore, it is advisable for both a professional and a home craftsman to use a special pressure gauge for the spray gun. With its help you can:
-
accurately determine the gas supply to the atomizer;
-
adjust pressure;
-
smooth out fluctuations in the air flow in the system;
-
prevent accidents.
By varying the pressure, a thick, protective coating can be obtained on the product. Or give it a beautiful look by painting it with a thin layer.


You can increase the air flow, then the object will be painted quickly and easily. Car bodies, walls and ceilings in rooms do not take much time. And if you reduce the air speed, then you can touch up local areas, chips, scratches and scuffs.
Therefore, spray gun pressure gauges have firmly taken their place among the tools. Moreover, thanks to their design, they can work for decades.
Operating principle
The device consists of 2 parts - a scale and a sensor with an arrow. Thanks to the large numbers on the scale, the measurement readings are clearly visible, there are markings for low, medium and high pressure. Often the scale is graduated in different measurement systems - ATM, MPa and others. However, in some models, instead of a scale, there is an LCD display. Everything for your convenience.


The sensor is usually mechanical; it measures the micro-movements of the sensing element. But he does it in different ways, so manometers are divided into several types.
-
Spring loaded. In them, the main element is a spring, which is compressed under pressure. Its deformation moves the arrow on the scale.
-
Membrane. A thin metal membrane is fixed between the two bases. When air is supplied, it bends, and its position is transmitted through the rod to the indicator.
-
Tubular. In them, pressure is applied to a Bourdon tube, a hollow spring that is sealed at one end and wound into a spiral. Under the influence of gas, it tends to straighten, and its movement is fixed by the indicator.
-
Digital. This is the most advanced design, although it is still very expensive. They have a strain gauge installed on the membrane, which changes its resistance depending on deformation. Changes in the electrical signal are recorded by an ohmmeter, which converts these readings into bars and displays them.

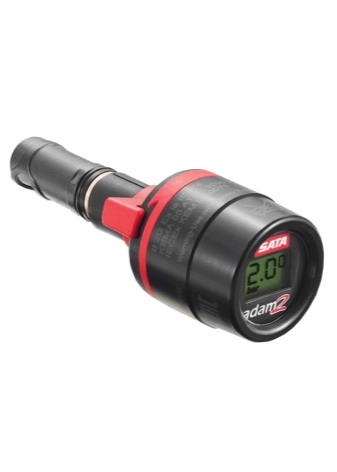
By the way, the price for electronic models is quite reasonable. The load cells are made of alloy steel or aluminum, and the contacts are coated with silver, gold and platinum.
This is to reduce electrical resistance. Therefore, even such a small device can cost 5,000, 7,000, 10,000 rubles and more.
Some models of pressure gauges are equipped with air pressure regulators, and they can change the cross section of the gas channel.But this is not always necessary, often there are adjusting screws on the spray gun itself. We will now talk about what kind of meters are.

Types and models
By the type of sensing element, pressure gauges are divided into spring, diaphragm and electronic.
-
Spring loaded. They have the simplest design, they are durable, reliable, and at the same time inexpensive. Such models are very popular and often become the choice of users. The disadvantage is that over time, the spring weakens, and the error increases greatly. Then calibration is required.
-
Membrane. They are compact but not precise. A thin membrane reacts too actively to temperature changes, is afraid of drops and sudden surges in pressure. Therefore, such devices are not widely used.
-
Electronic. Due to the high price, they are found only among professionals, although they are the most accurate in showing pressure and adjusting the ratio of air and paint. In some spray guns, they are built into the body. These sensors can be used to automatically adjust the pressure in gas pressure regulators. This is especially true in industries when one pneumatic accumulator feeds several nozzles at once.



Manufacturing firms compete with each other. By improving the quality of their products and reducing the cost, they lure customers to themselves. We can single out several worthy companies:
-
SATA;
-
DeVilbiss;
-
INTERTOOL;
-
STAR.
These firms produce high-quality meters that have long been loved by masters.
-
For example, the Sata 27771 pressure gauge. It is equipped with a regulator. The largest measurement limit is 6.8 bar or 0.68 MPa. It costs about 6,000 rubles.
-
There are also lesser known models such as the Iwata AJR-02S-VG Impact. Its characteristics are the same as that of the Sata 27771, and the price is about 3,500 rubles.
-
DeVilbiss HAV-501-B costs about the same, but its measurement limit is 10 bar.
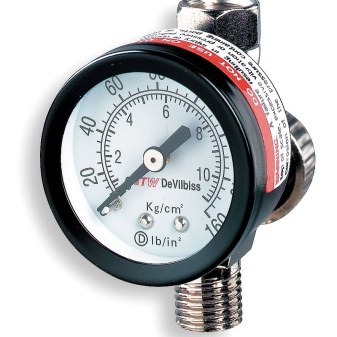
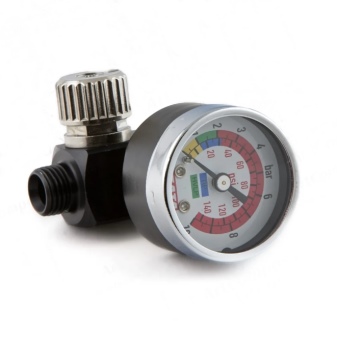
The mass of such pressure gauges does not exceed 150-200 grams, so they are hardly felt in operation. But there are many benefits. Of course, if you connect them correctly.
How to connect?
Just make sure the threads on the gauge match the threads on your sprayer. When all is well, you can proceed to the spray gun upgrade.
-
The best place to install is the spray handle. If a moisture trap is installed, it will reduce accuracy. Then build the pneumatic system as follows: air supply hose - moisture separator - pressure gauge - spray gun.
-
The structure can be bulky, and this will lead to difficulties when working in tight spaces. To avoid this, use a short (10-15 cm) hose through which you need to connect the spray handle and the pressure gauge. Then the cramped conditions will not become an obstacle, but you will have to work more carefully.
All elements of the system are connected by a thread. If not, use clamping clamps. And to check the tightness, apply soapy water to the joints. If there is an air leak, tighten the connecting nuts or replace the gasket.
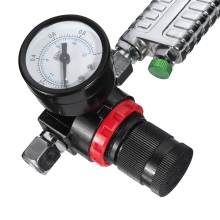


The comment was sent successfully.