Features of the process of painting with powder paint
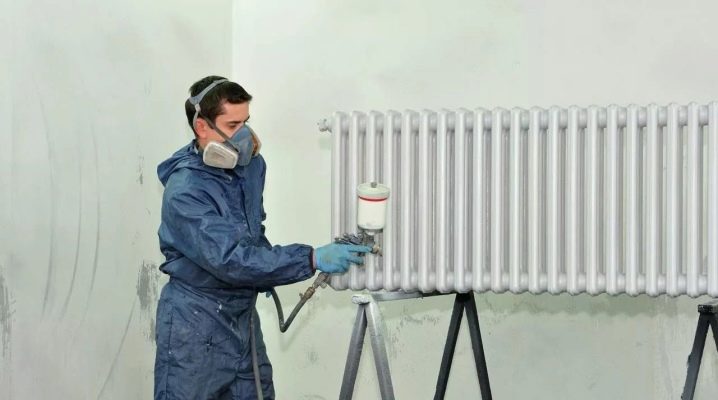
Powder paint has been used for a long time. But if you do not possess the technology of its application to the required degree, if you do not have the necessary experience, you will have to thoroughly study all the information in order to avoid mistakes. It is their prevention that we dedicate this material to.
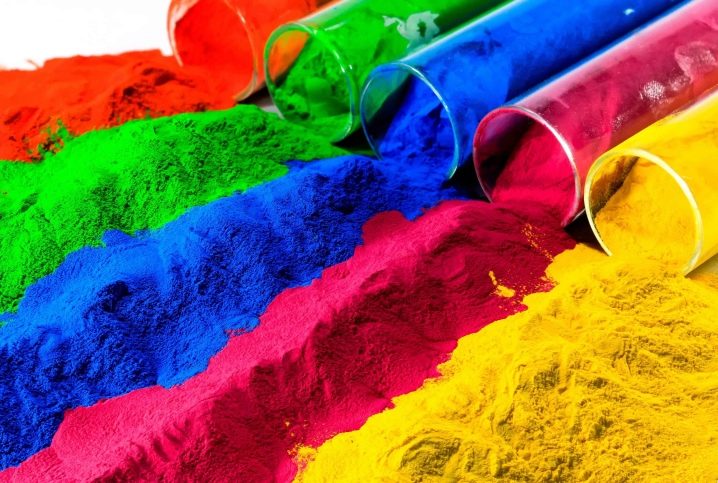
Peculiarities
Powder paint is made from polymers that are powdered and then sprayed onto a specific surface. To give the coating the desired properties, it is thermally processed, the melted powder turns into a film uniform in thickness. The key advantages of this material are corrosion resistance and significant adhesion. Under the influence of high temperatures, including when they alternate with low ones, powder paint retains its positive qualities for a long time. Mechanical and chemical influences are also well tolerated by it, and contact with moisture does not disturb the surface.
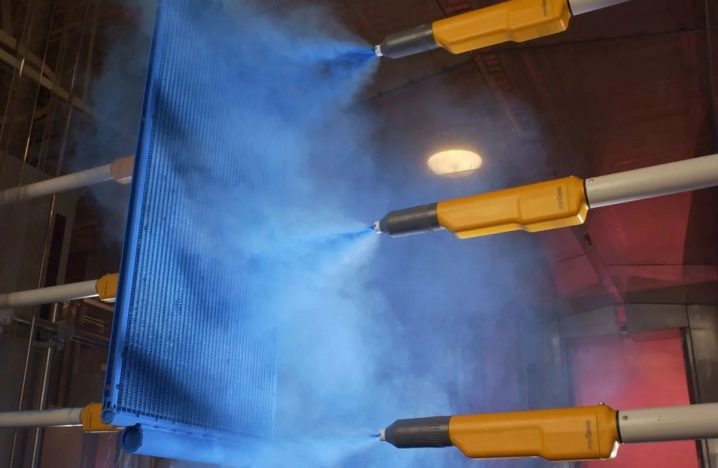
Powder paint retains all these advantages for a long time along with visual appeal. You can paint the surface to achieve a wide variety of tones and textures by varying the additives added. Matte and glossy shine are just the most obvious examples and can be created with powder paint quickly and easily. But a more original painting is also possible: with a three-dimensional effect, with the reproduction of the appearance of wood, with imitation of gold, marble and silver.
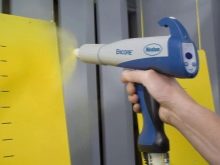
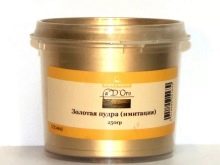
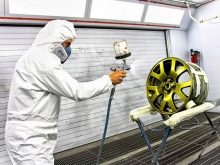
The undoubted advantage of powder coating is the ability to complete all work with the application of one layer, when working with liquid formulations this is unattainable. In addition, you will not need to use solvents, and monitor the viscosity of the paint and varnish composition. Any unused powder that has not adhered to the desired surface can be collected (when working in a special chamber) and sprayed again. As a result, with constant use or with large one-time volumes of work, powder paint is more profitable than others. And the good thing is that there is no need to wait for the drying of the coloring layer.
All these advantages, as well as optimal environmental friendliness, no need for powerful ventilation, the ability to almost completely automate work, should be taken into account.

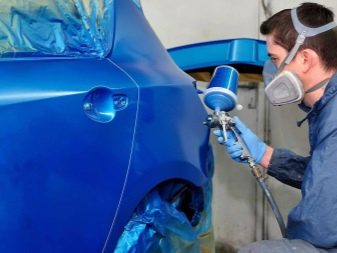
Do not forget about the negative aspects of this technique:
- If a defect appears, if the coating is damaged during work or subsequent use, you will have to repaint the entire object or at least one of its facets from scratch.
- At home, powder painting is not carried out, it requires very sophisticated equipment, and the size of the chambers limits the size of the objects to be painted.
- It is impossible to tint the paint, nor can it be used for parts, structures that are to be welded, since the burnt parts of the paint layer are not restored.
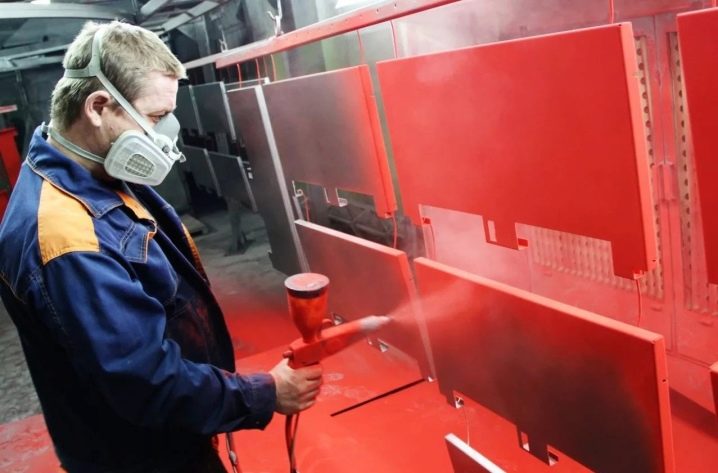
What surfaces can it be used for?
Powerful adhesion makes powder coating ideal for stainless steels. In general, when processing metal products for household, industrial and transport purposes, powder is used much more often than liquid formulations. This is how the components of warehouse and trading apparatus, machine tools, metal of pipelines and wells are painted. In addition to the ease of application, the attention of engineers to this method of processing is attracted by the safety of the paint in fire and sanitary terms, the zero level of its toxicity.
Forged structures, aluminum and stainless steel products may well be powder painted. This method of coating is also practiced in the production of laboratory, medical equipment, sports equipment.
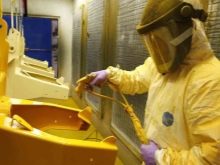
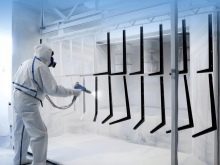
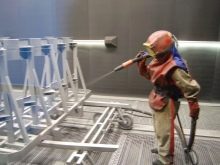
Articles made of ferrous metals, including those with an outer zinc layer, ceramics, MDF, and plastic can also be a good substrate for powder painting.
Dyes based on polyvinyl butyral are distinguished by increased decorative properties, are resistant to the effects of gasoline, do not conduct electric current, and tolerate contact with abrasive substances well. The ability to survive the ingress of water, even salty water, is very useful when creating pipelines, heating radiators, and other communications in contact with liquid.
When applying a special powder to the surface of an aluminum profile, the priority is not so much corrosion protection as giving a beautiful appearance. It is imperative to select the operating mode, depending on the composition of the dye and the characteristics of the substrate, to take into account the specifics of the equipment. An aluminum profile with a thermal insert is processed for at most 20 minutes when heated to no higher than 200 degrees. The electrostatic method is worse than the tribostatic method when painting metal products with blind holes.
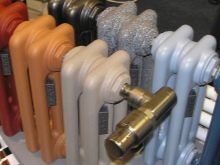
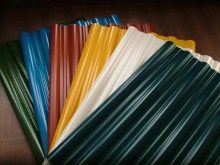
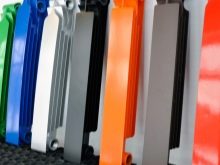
The use of fluorescent powder paint is practiced when working on road signs and other informational structures, when the glow in the dark is more important. For the most part, aerosol formulations are used, as the most practical and creating the most even layer.
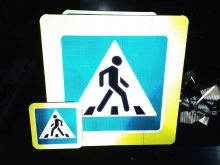
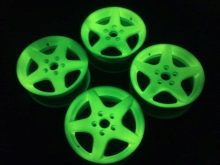
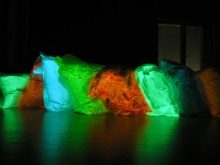
How to breed?
The question of how to dilute the powder paint, in what proportion should it be diluted before applying the coating, is not a question for professionals in principle. As you already know, coloring with this type of paints is done in a completely dry form, and no matter how hard the fans of experiments try to dilute and dissolve this mixture, they will not get anything good.
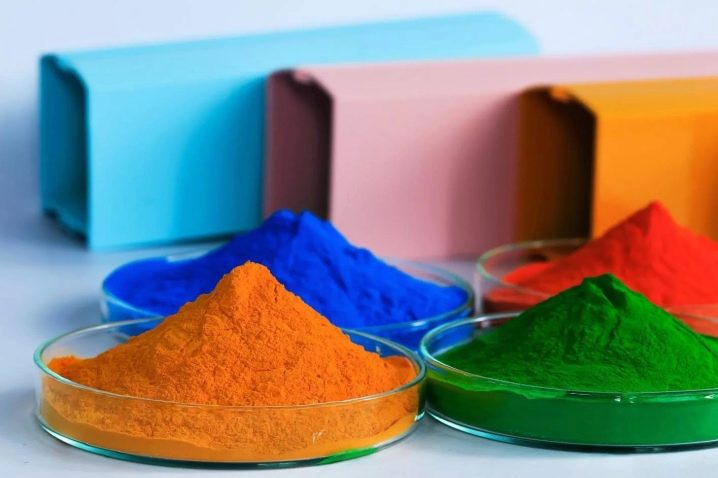
Consumption
The attractiveness of powder paint is beyond doubt. However, you need to accurately determine the need for it, find out how much the coloring composition goes for each m2. The minimum layer thickness to be created is 100 µm, in order to reduce the use of dye, it is advisable to spray it. The aerosol method of application allows you to spend from 0.12 to 0.14 kg of material per 1 square meter. But all these calculations are only approximate, and allow you to determine the order of the numbers.
An accurate assessment can be given by knowing the properties of a particular type of paint. and the characteristics of the substrate to which it will be applied. Remember that the norm indicated on labels and packaging, which is shown on advertising posters, implies a surface painting that is absolutely free of pores. Plastic or metal has only a slight porosity, and therefore, even when painting them, you will need to use a little more dye than prescribed by the manufacturer. When other materials need to be processed, costs will increase significantly. So do not be indignant if you find “inflated” figures in the bills for powder painting services.
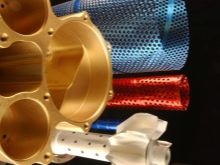
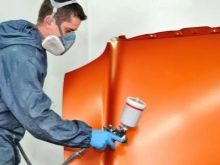
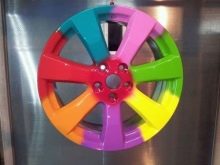
Distinguish between decorative, protective and combined coating, depending on the belonging to a particular group, a layer of different thickness is formed. You also need to take into account the geometric shape of the surface and the difficulty of working with it.
Coloration
As you already know, you cannot paint anything with powder paints at home. The main difficulties in using them on an industrial scale arise in the process of preparatory work. The technology provides that the slightest dirt must be removed from the surface, degreased. It is imperative that the surface is phosphated so that the powder adheres better.
Failure to comply with the preparation method will lead to a deterioration in the elasticity, strength and visual appeal of the coating. It is possible to remove dirt by mechanical or chemical cleaning; the choice of approach is determined by the decision of the technologists.
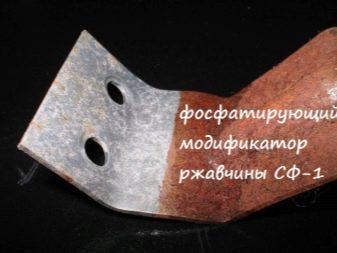
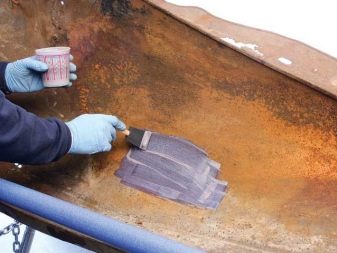
To remove oxides, corroded areas and scale, shot blasting machines that spray sand, or special granules made of cast iron or steel are often used. Abrasive particles are thrown in the desired direction by compressed air or centrifugal force. This process takes place at high speeds, due to which foreign particles are mechanically beaten off the surface.
For the chemical preparation of the painted surface (the so-called etching), hydrochloric, nitric, phosphoric or sulfuric acid is used. This method is somewhat simpler, since there is no need for complex equipment, and the overall performance is increased. But immediately after etching, you need to wash off the acid residues and neutralize them. Then a special layer of phosphates is created, its formation plays the same role as applying a primer in other cases.
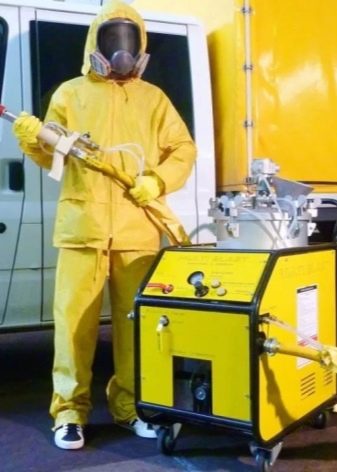
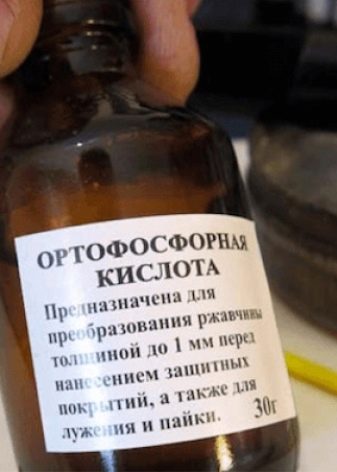
Next, the part must be placed in a special chamber: it not only reduces the consumption of the working mixture by capturing it, but also prevents paint contamination of the surrounding room. Modern technology is invariably equipped with bunkers, vibrating sieves, and suction devices. If you need to paint a large thing, use the type of cameras through passage, and relatively small parts can be processed in dead-end devices.
Large factories use automated painting booths, into which the manipulator of the "pistol" format is built. The cost of such devices is quite high, but getting fully finished products in seconds justifies all the costs. Usually a spray gun uses an electrostatic effect, that is, the powder first receives a certain charge, and the surface receives the same charge with the opposite sign. The "pistol" "shoots" not with powder gases, of course, but with compressed air.
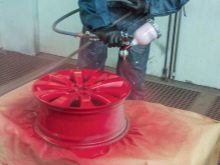
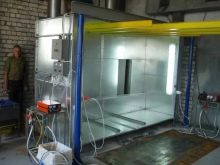
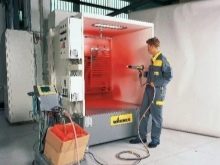
Only the work does not end there. The workpiece is placed in a special furnace, where it is covered with a viscous layer at an elevated temperature; with further exposure, it dries and becomes homogeneous, as strong as possible. The processing rules are very strict, so it is required not only to use professional equipment, but also to entrust the entire process exclusively to specialists. The thickness of the paint layer will be small, and its exact value depends on which composition was used. In some cases, you can replace the primer with another pre-applied paint, necessarily from inorganic components.
Please note that you can paint any material with powder only in a protective mask., regardless of whether you are sure of the tightness of the chamber. It is absolutely impossible to polish the powder paint, it is applied once and then can only be repainted or removed completely. Always check the applied layer using a thickness gauge to check the accuracy of the craftsmen's words and accompanying documents.
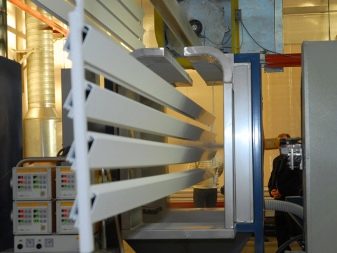
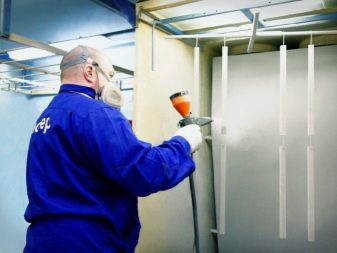
See below for the powder coating process.
The comment was sent successfully.