All about boiler rooms

It is important to know everything about boiler houses for everyone who builds a large cottage or is going to settle in a cottage community. There are no trifles here - you will have to take into account the difference between liquid fuel boiler houses, and the peculiarities of the construction and repair of chimneys, and many other nuances. An important role is played, in particular, by the choice of the type of coolant, the specific location of the complex.
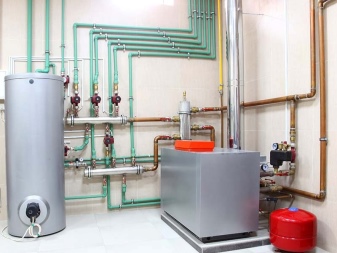
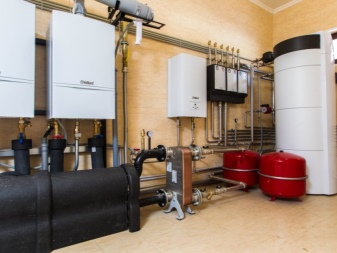
What it is?
The widespread opinion says that a boiler room is "such a room or a large building where water or other heat carrier is simply heated in large volumes." However, this interpretation is very far from reality. In fact, this is not just a building or a room with a boiler, but a whole complex where dozens, sometimes hundreds of different devices operate around the boiler.
In large industrial and power boiler houses, the length of internal pipelines can be measured in kilometers.
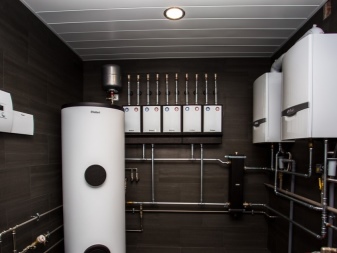
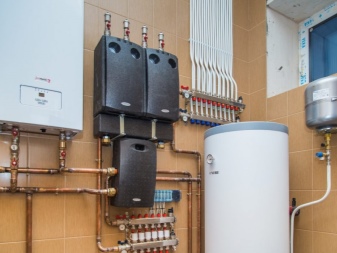
It is customary to divide such systems into:
- heating;
- heating and industrial;
- purely industrial types.
For communication with consumers, a heating main or steam pipelines are used. In some cases, both of these options can be used. All components of boiler houses are in any case technologically connected and designed with the expectation of solving certain problems. The most common options are those in which heat is obtained through the combustion of mineral, less often organic fuel. In some cases, heat is generated by electricity or by using alternative heating methods.

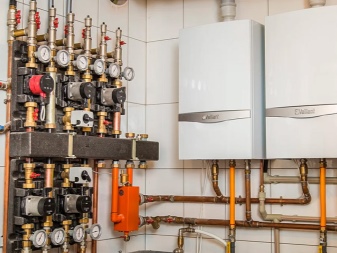
Primary requirements
All any large boiler houses responsible for heating the microdistrict or a larger area operate according to a strict temperature schedule. It displays the correspondence of the temperature to which the dispensed heat carrier is heated and the temperature of the ambient air. In any case, they are trying to achieve that it is possible to maintain a temperature of at least +18 degrees in heated buildings everywhere.
Also used in the work "return heat carrier diagram"; if it comes on the return circuit cooled to a predetermined value, then the operation of the boiler house is recognized as 100% efficient.
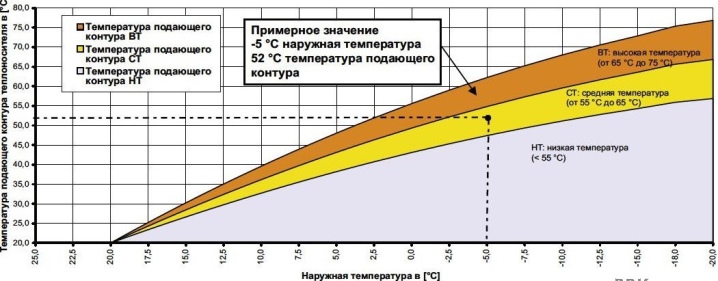
But the return of unjustifiably hot water or steam usually indicates either an excessive flow of the coolant, or too much heating.
The so-called heat balance of the unit is of great importance. It, in fact, expresses the equality of the amount of heat entering the boiler and its consumption. But we must understand that the total chemical energy of the fuel, the incoming electricity is converted into heat only partially. And even heat energy is partially dissipated when moving inside the unit and along the supply line. The less this dissipation, and the greater the proportion of potential heat reaches the consumer, the more perfect the boiler complex is considered. All these requirements, of course, apply to systems that heat a private house or supply heat to a separate non-residential premises.
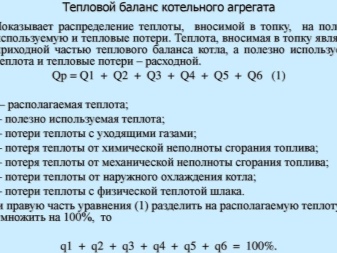
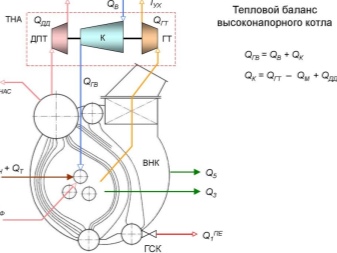
When drawing up a project, he strictly signs:
-
how much and what kind of fuel can be used;
-
what coolant will be used;
-
what should be its quality;
-
how much coolant is used and wrapped in the system;
-
total thermal performance of installations;
-
Efficiency of the boiler room and its individual equipment;
-
the amount of solid and gaseous combustion waste;
-
the use of filters and treatment facilities;
-
characteristics of the main and control equipment used;
-
limiting pressures and temperatures in all units, circuits.
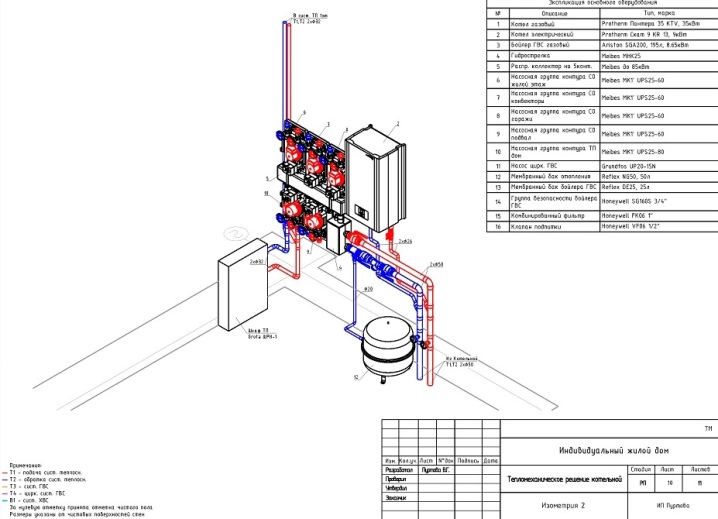
When installing a boiler room in a private house (especially in it itself), equipment with a window should be provided. Its area is strictly standardized according to SNiP. The total area of the room (depending on the power of the equipment) is also normalized. From the boiler room, there must certainly be a door to the street; installing a door directly into the house, on the other hand, is usually prohibited.
Important: as a door leaf, there should be easily resettable structures that allow to reduce the destructive consequences of explosions - due to the free propagation of a part of the overpressure front.
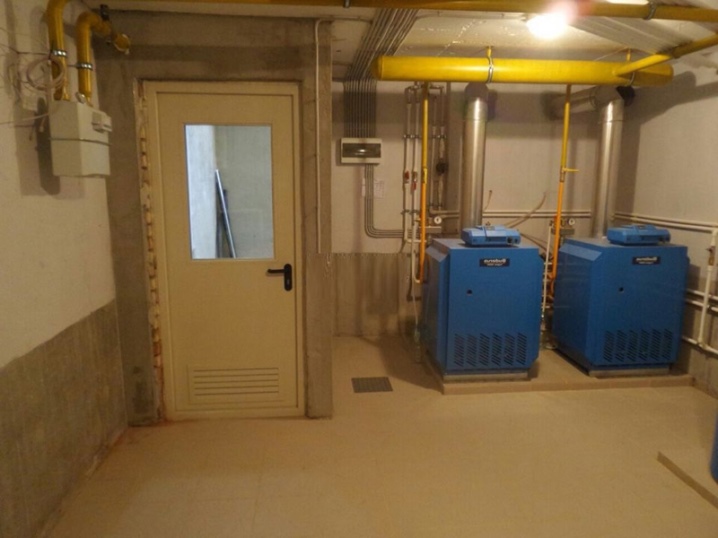
Description of species
Perhaps the most important difference is observed between industrial and domestic boiler houses. Industrial grade equipment heats entire factories and other large areas. Even the most powerful of the household boiler rooms will not "stretch" such a task. The mass of industrial boilers and their dimensions are usually much larger. The fuel consumption, the coolant turnover, the total amount of heat generated, and a number of other parameters have also been increased.
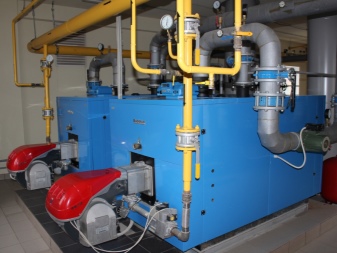

By type of fuel
A fairly large number of boiler equipment is still running on liquid fuel. In addition to diesel fuel, this category also includes crude oil, fuel oil, and used industrial oil. Commissioning is fast enough. There is no requirement to obtain permission to use liquid fuel boilers. If necessary, they can be used independently.
If the principle of operation of a boiler plant involves the use of natural or liquefied gas, then it turns out to make the operation of the system more economical and environmentally friendly.
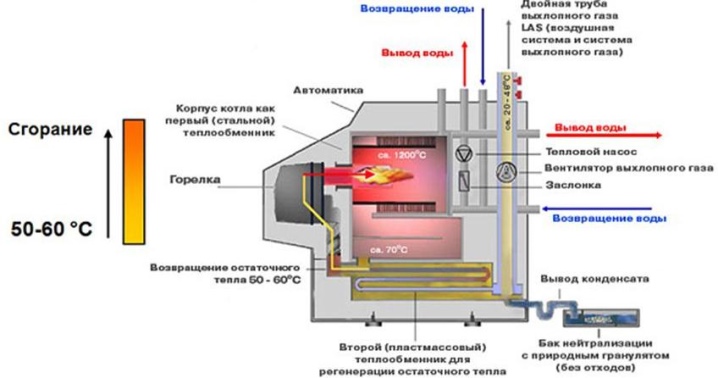
Such complexes do not contain complex dimensional equipment. They can be easily taken offline when needed. Systems with a solid fuel boiler are also quite widespread. It can use firewood, coal, logging waste, peat and some other types of fuel.
The solid fuel equipment itself is inexpensive, affordable and the fuel used. However, feeding it into the combustion chamber is difficult and requires special components. Systems for removing slag and ash should also be provided. A coal-fired boiler house is a traditional, proven method of generating heat energy for decades. Its equipment and infrastructure have been worked out to the smallest detail.

Characteristic properties of solid fuel boilers:
-
independence from backbone networks;
-
decent efficiency (in modern models, efficiency of 80 - 84% has become commonplace);
-
the availability and practicality of coal itself;
-
minimum costs for the arrangement of the complex;
-
limited number of employees;
-
fuel storage difficulties;
-
the need for daily maintenance of fireboxes;
-
severe air clogging;
-
the need to constantly monitor the workflow.

As for liquid fuel boilers, they are typical:
-
achievement of efficiency 86 - 98%;
-
installation without special approvals;
-
the ability to switch to natural gas by simply replacing the burner;
-
increased equipment autonomy;
-
suitability for work on alternative types of fuel (not only on "diesel", as is often believed);
-
effective connection to any heating system (regardless of the circulation of water or antifreeze);
-
rather high costs for the arrangement of the working space;
-
the need for large fuel tanks;
-
rather unpleasant smell from the fuel itself, especially when burning it;
-
increased requirements for the quality of fuel (the supply of good liquid fuel is difficult in a number of remote areas).
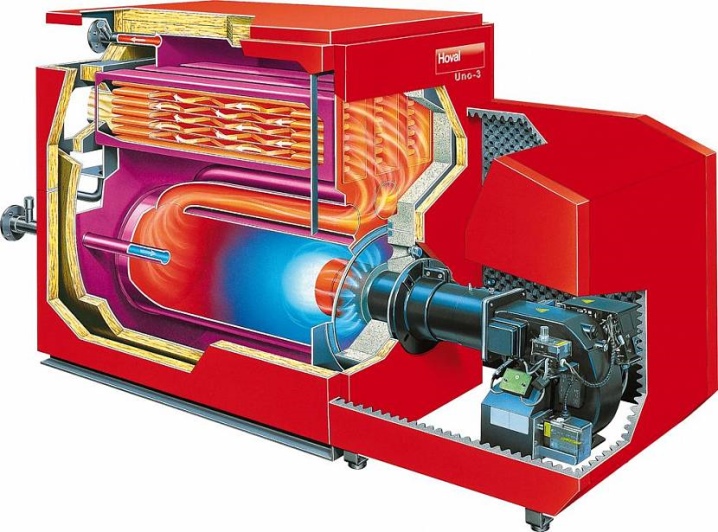
Separately, it is worth mentioning systems with an electric boiler. Such boiler rooms do not require a separate room and do not need a chimney. An electric heating device is relatively inexpensive. There is no need to prepare any kind of fuel storage for it. And everything will be in perfect order with environmental indicators; the only serious drawback is the high cost of using electricity for heating.

By placement
The classification of boiler installations by location is also very important. The classic version involves the arrangement of a stationary combustion chamber. It is used in all cases when the design capacity of the installation exceeds 30 MW. The volume of construction and installation work in this version is very large. We have to equip both walls and many partitions.
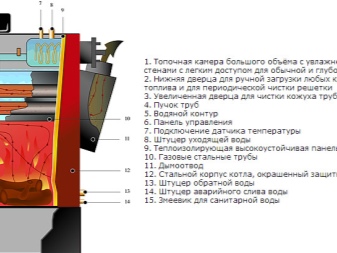
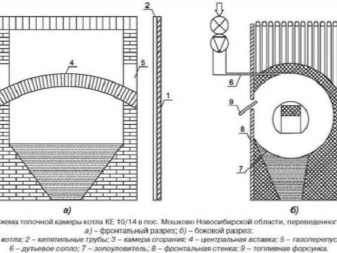
In a number of situations, it is more correct to use mobile block-modular boiler rooms, and their popularity is growing rapidly.
You can mount and run such a system quickly enough. It will usually differ in autonomy and other valuable practical parameters. The efficiency of mobile block-modular devices is quite high. They are used in a free-standing, attached version, mounted inside buildings, and sometimes even placed on the roof of a house.
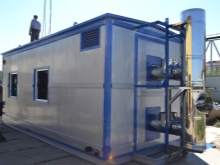
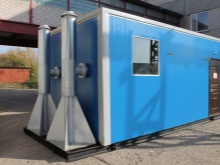
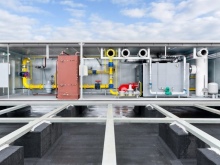
By type of coolant
The basic design of a heat-transferring system can imply the use of:
-
aquatic;
-
steam;
-
airway communications.
Accordingly, there are:
-
hot water;
-
steam;
-
air-heating boiler plants.
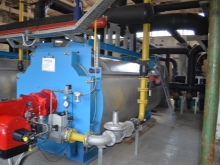
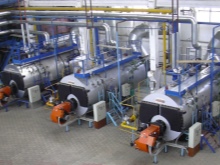
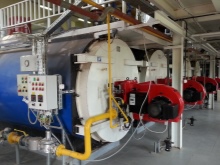
Water heating is mainly used for private and collective heat supply. If the capacity of the equipment is high, it is always equipped with forced circulation complexes. To increase the efficiency, the pressure inside the heat generator is raised to 0.7 kg per 1 cubic meter. cm, and the temperature is up to 115 degrees. Hot water either enters directly into the heating devices of consumers, into the water supply system, or indirectly heats up the network water in boilers.
As for steam boilers, they are performed according to a single-drum or double-drum scheme; the working environment circulates repeatedly.
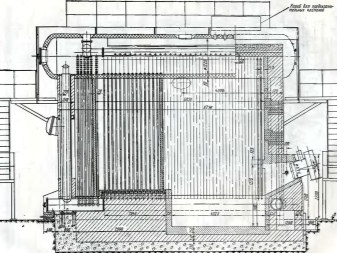
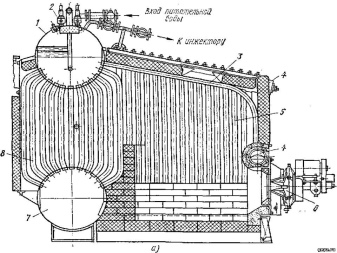
Even with natural circulation, it is possible to ensure from 5 to 30 circulation cycles of the coolant. Economizers and air heaters help to improve the quality of work. Hot water boilers are used for heating small industrial enterprises. The movement of air inside the pipes is carried out by natural convection. Only when it is necessary to increase the speed of its circulation are fans also used.
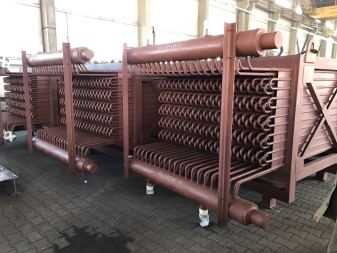
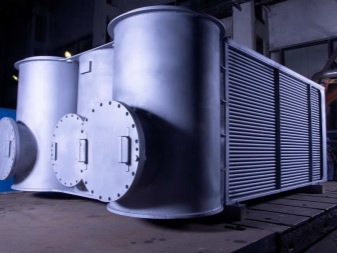
By the degree of mechanization
Depending on how exactly the fuel should be supplied, there are:
-
semi-mechanical;
-
completely manual;
-
mechanized boiler plants.
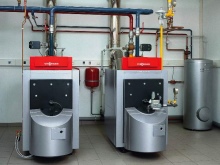

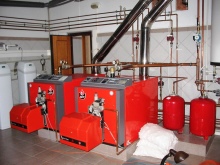
Where to place?
In the case of large boiler houses, trained engineers usually answer this question. And they know for sure much more nuances than could be reflected in the most detailed article. But for a private house, the location of the boiler room will have to be selected independently. In any case, the plan of the house, the amount of energy resources and other subtleties are analyzed. The main requirements are, of course, related to ensuring safety and comfort:
-
natural lighting should be maintained in all parts of the boiler room;
-
if possible, it should be taken out in a separate building;
-
it is required to observe fire-fighting measures (distance).

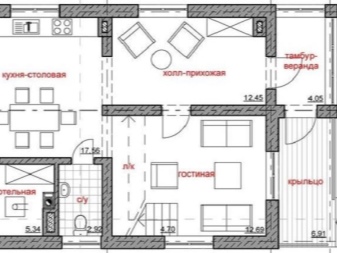
Boiler houses standing separately from residential buildings are connected to them by means of engineering communications. We are talking not only about the heating main, but also about the water supply, the gas pipeline, and sometimes the electrical wiring.
The versatility of individual boiler rooms is due to the fact that inside them you can put any unit designed for a wide variety of fuels.
In some cases, boilers and other components are installed on rooftops.But such a step is taken extremely rarely, because the operation is then extremely difficult.
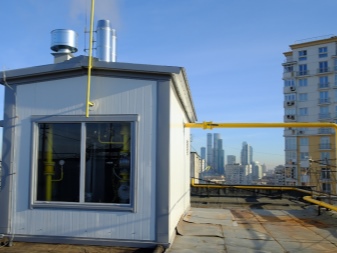
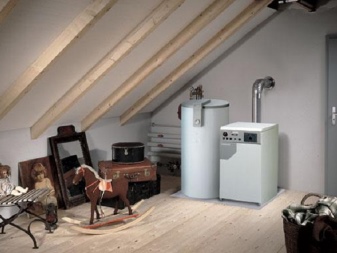
Features of transportation
Almost always, boilers and related equipment are classified as oversized cargo. Their transportation itself is possible only with special permission and with the coordination of the route. You will also have to select carefully transport with the necessary characteristics. The specifics of loading and unloading operations are discussed in advance. Only trained professionals with solid experience can perform these works, as well as the transportation itself.
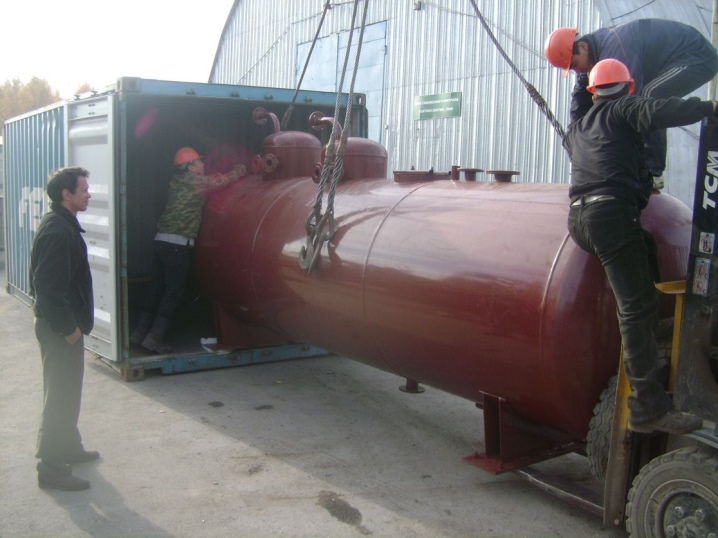
The contract between the customer and the transportation provider clearly states:
-
weight and size of the boiler;
-
its technical features and related limitations;
-
parameters of the provided transport;
-
exact route of movement;
-
loading, rigging works;
-
peculiarities of unloading at the recipient;
-
insurance obligations;
-
security, technical support.

For transportation of boilers use:
-
powerful lifts;
-
transport cranes;
-
low frame platforms;
-
loaders;
-
trawls;
-
jacks;
-
carts;
-
specialized cars.
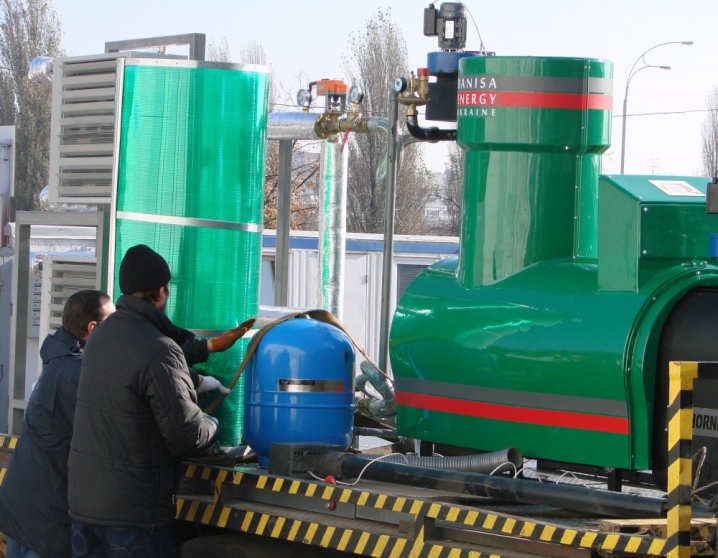
Construction
The construction of turnkey boiler houses is offered by quite a few companies. Even block-modular transportable complexes need to be designed and calculated according to strict rules. On average, the payback of construction is 2.5 - 3 years. It will not be more expensive than connecting to main heating networks. The thermal diagram of the boiler house graphically displays the main and auxiliary equipment, as well as its connections with the help of engineering networks.
According to the diagram, it is possible to unmistakably recognize the heat carrier flows going through the pipes towards the heating devices (or larger end consumers). When drawing up such documents, the recommendations contained in SNiP are taken into account.
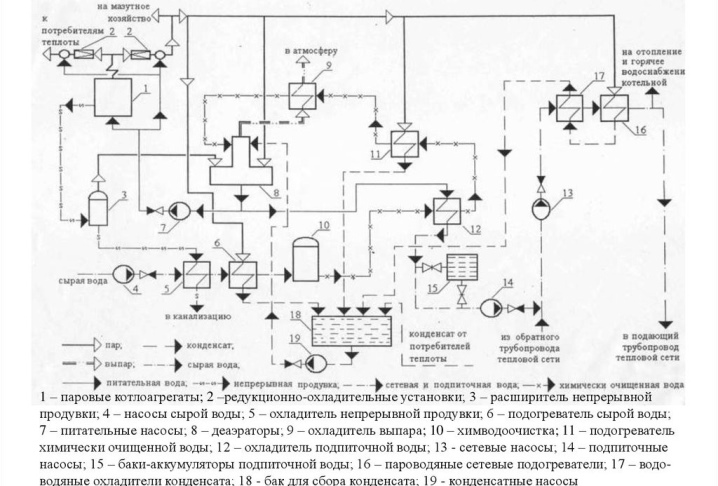
The location of the locking fittings and safety devices is shown in the diagrams. Correct ventilation calculation plays a very important role.
When using gas, it is assumed that 10 times the volume of oxygen is required. For greater reliability, the same approach can be applied to complexes using other fuels. It provides for redundancy of power supply and accumulation of fuel reserves. The slightest deviation from projects is either not allowed or must be carefully motivated. It makes sense to entrust the construction of boiler houses only to advanced companies.
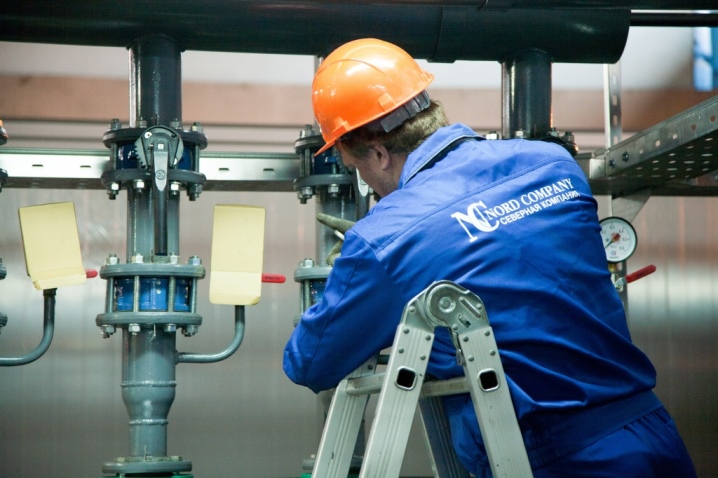
Strapping scheme
The pump head can be ignored. Even its minimum is enough for most houses of the sane area. For your information: the circulation of water or steam through the heating system of a nine-story building is provided with a pressure of only 2 m. Circulation pumps are usually placed before the boiler according to the movement of the coolant. If it is planned to use at least periodically also natural circulation, the pump will have to be cut not at the break of the filling, but in parallel to it; the tie-ins are separated by a ball valve, instead of which a check valve with negligible resistance is sometimes used.
Closed heating systems must have:
-
expansion tank with membrane;
-
safety valve (and drainage tube with it);
-
auto air vent;
-
pressure gauge.
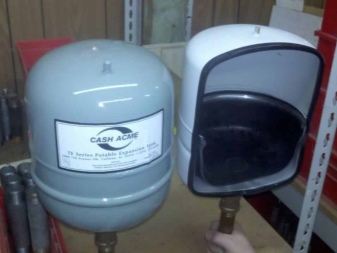
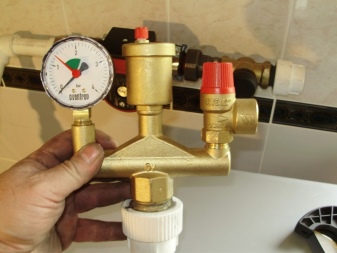
Maintenance
Scheduled maintenance of boiler rooms is carried out continuously. It is complemented by monthly maintenance. At the same time, they take care of the condition of boilers and heating mains, fuel storage facilities and control automation. Additionally, work is carried out with the filters that come with the boiler. Craftsmen repair gas pipes, adjust burners and automatics, examine internal pipelines; additionally study the technical parameters of pressure gauges, emergency and working thermostats, taps, valves, water tanks and filters.
All works are displayed in action plans. During technical inspection, they immediately fight against defects and check the compliance with technical standards.
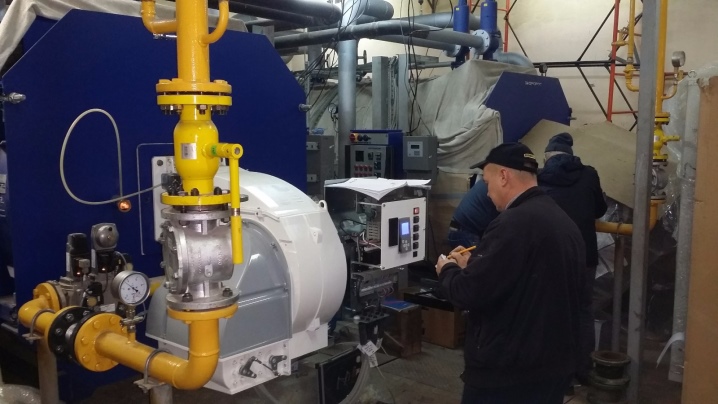
All mechanisms are also checked, defective parts are replaced. Additionally, the oil seals are adjusted and the serviceability of the mothballed units is checked. In the inspection plan, work with:
-
sensors;
-
buildings;
-
lids;
-
insulation of wires;
-
fan motors;
-
security group.
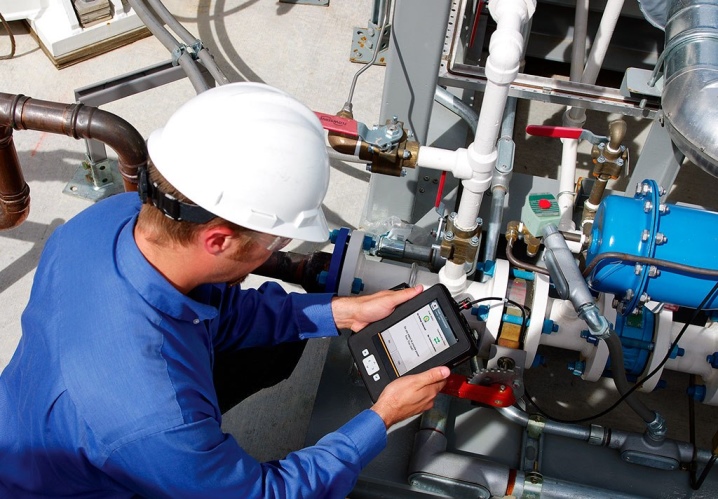
Technical structures need to be washed periodically. It also requires a systematic lubrication of the bolts and those connections where they are installed. The measuring equipment is adjusted once every 30 days. The electric motors must be inspected and tested every 3 months. The frequency of adjustment of the emergency reserve power supply is determined by the manufacturer's regulations.
When inspecting the boiler, they also adjust the heat sensors and check the parameters of the air flows in the gas pipeline. During the regime adjustment, they prepare for the terms of reference and carry it out. Be sure to record the time it took for a particular procedure. Additionally, the boiler unit is monitored, as a result of which a regime map is formed. It must be renewed every 3 to 5 years.
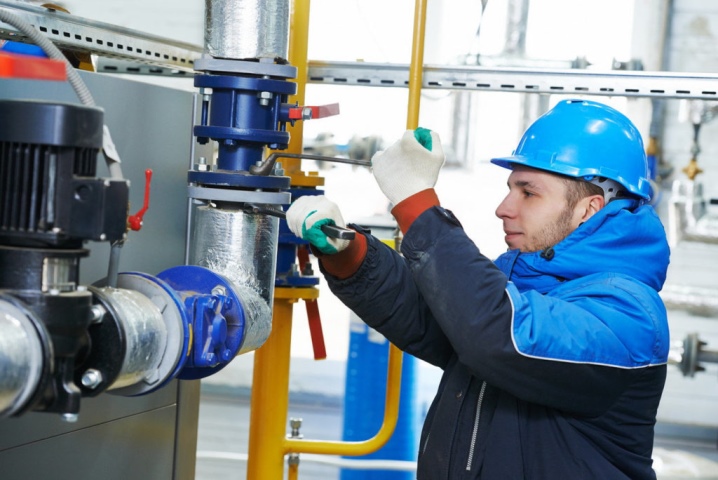
Both in boilers and in electric boilers, only a professional can fix all problems. He will study the regulations and check how the protection devices work. The maximum that you can fix with your own hands is minor problems (for example, a loose connection of the nozzle). Minor sensor problems can be fixed on the fly. Every year, the information on the wear of the lining, assemblies and frame parts is updated.
How to automate the boiler room, see below.
The comment was sent successfully.