All about boiler equipment
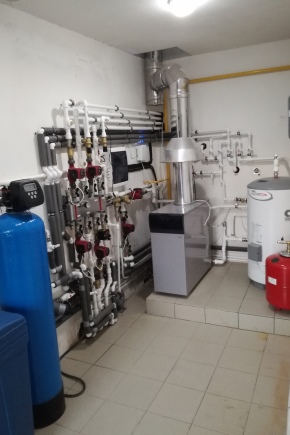
Large private houses and especially multi-storey residential buildings, their entire complexes, often require sophisticated communal systems. You need to know everything about boiler equipment and other subtleties and nuances. These devices differ in the method of installation, materials of manufacture, order of operation.... All these subtleties should be clarified in advance.
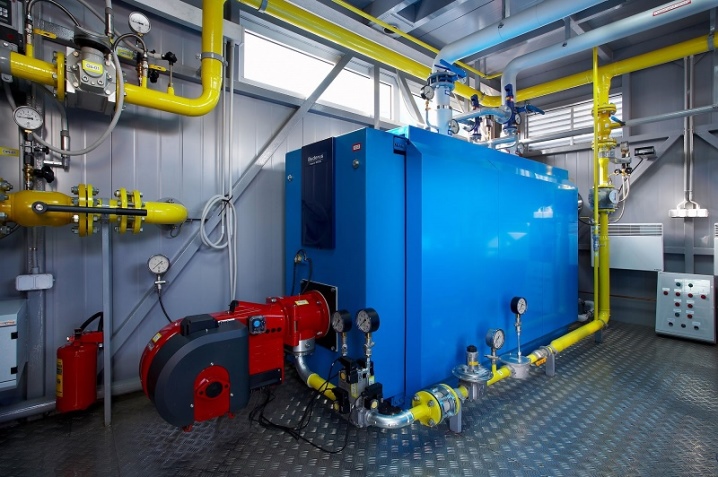
What it is?
First you need to tell what boiler equipment and installations are. Such devices are needed to supply heat to residential buildings and neighborhoods. They are also used in public baths, at industrial and agricultural facilities, at construction sites. The possibilities of using boiler houses in various technological schemes are very large. The demand for such equipment is steadily growing as the development of hard-to-reach areas continues.
Modern hardware systems can run on very different things, including "junk" fuel. In addition to boilers, they may include other devices:
- burners;
- heat exchangers;
- chimneys;
- pumps (in liquid configuration);
- a number of other systems and units that increase the efficiency, safety or ease of use of technology.

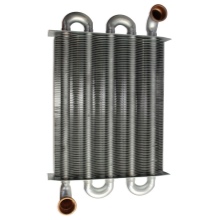
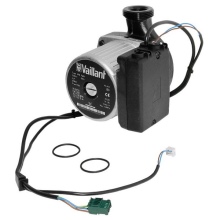
The primary direction in the development of boiler equipment is now the modernization of automation systems. "Squeezing" something due to mechanical, hydraulic, thermal processes is already quite rare and small. It is the control systems that provide the most rational options and modes of operation that help save resources and control remotely.
There are a number of other benefits that would not be possible without electronics at all. The general principle, however, has remained unchanged since ancient times: the burned fuel emits heat, which is transferred to the coolant circulating for various purposes.
SNiP II-35-76 operated earlier. However, now it has been replaced by another standard - a joint venture from 2016. This act regulates:
- design work;
- construction and subsequent reconstruction;
- major overhaul;
- retrofitting in various cases;
- basic requirements for content and practical application.
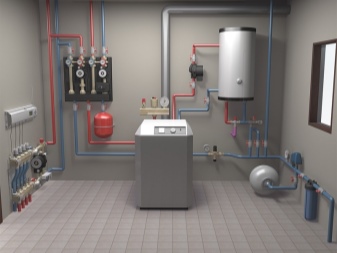
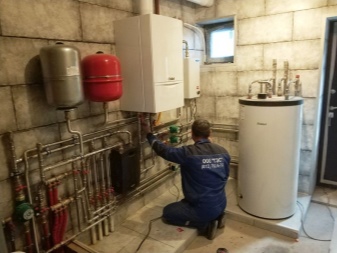
Species overview
Of course, the list of the main boiler equipment includes themselves boilers. If the complex is not equipped with such a technical means, there is no point in using other systems. Hot water boilers can heat the coolant up to a maximum of 150 degrees. In steam systems, various masses of saturated or superheated steam are generated under a pressure of at least 1 MPa. The boiler is closely connected to the firebox (in professional use, this is a separate design).
So that the heat source itself does not lose an unnecessary amount of energy, lining is used. It also increases the gas density of the plant. The metal frame structure supports all used parts and mechanisms in a predetermined position, without displacement. Also, the main systems include:
- superheating unit;
- economizer (inside which, depending on the design, the water is continuously heated to 100 degrees or does not reach this point);
- air heater;
- fittings for adjustment (including all kinds of valves);
- headset (manholes, hatches, air dampers, explosion valves).
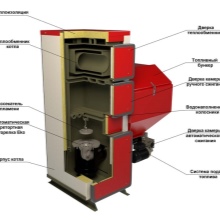
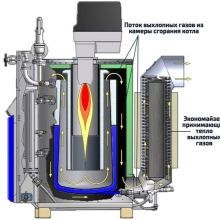
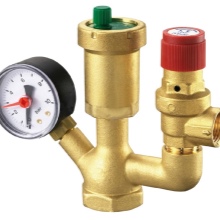
But in order for the industrial boiler equipment of the main series to work normally, various auxiliary equipment is needed.... After all, fuel, water and even air must be carefully prepared before being fed into the boiler. If you submit them in their original form, problems and even failure of a number of expensive devices are inevitable. The auxiliary link consists of:
- fuel supply complexes;
- smoke cleaning devices;
- pumps providing pumping and circulation of water;
- draft systems;
- separation segments of the boiler;
- equipment for water treatment.
Under the name "draft technology" fans are hidden, ensuring the normal operation of the gas-air lines. This group also includes smoke exhausters. Separators help separate steam from water. Steam boilers must be equipped with a pair of electric pumps that develop a pressure at least 25% higher than in the boiler water line.
Their nominal steam capacity should be at least 10% higher than that of all steam generators in the system.

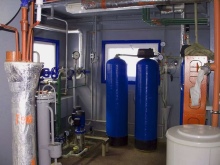
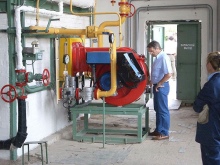
By type of fuel
Almost all modern boiler houses run on gas fuel - it is economical, practical and environmentally friendly... But one has to reckon with high explosive risks. However, this is largely balanced by the significant fire hazard from all other types of fuel. Normal operation of boiler rooms, however, is inconceivable without electrical equipment, and these are not only pumps, but also fans, and control automation.
If not limited to one gas, it is worth mentioning that the fuel oil can include (in various proportions):
- light gas oil;
- heating oil;
- residues of cracking products;
- waste oil production;
- heating oil;
- technological export fuel.
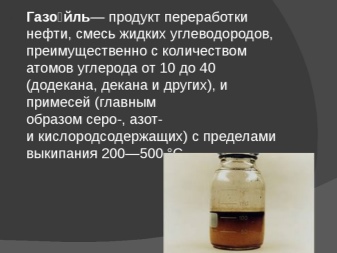
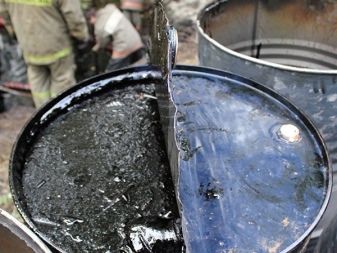
Critical to normal operation are:
- usefulness of combustion;
- discharge and flood characteristics;
- conformity of the fuel to the consumer equipment device.
From an energy point of view, electricity can also be considered a "fuel"... However, it is quite expensive. Power supply of a powerful boiler can only be organized using large section cables, which must be connected to power transmission lines or power plants.
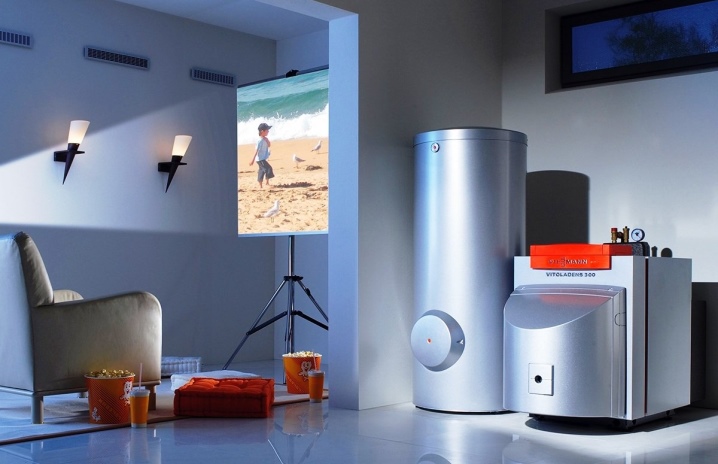
By installation method
Relocatable boiler rooms are block modules (another name is "container module"). These are one-storey complexes made of non-combustible materials. By default, all used equipment can be put into a single block-box. In this case, it is often recommended to use windows or openings. Boiler installations with a capacity of not more than 30 kW can be installed in rooms of country houses.
If performance is higher, you will need detached building. Such systems are installed on the ground floor, in a building with a capacity of at least 15 m3, and preferably 20 m3.
The division into the following options for boiler equipment is also used:
- roof;
- intended for basements;
- built into buildings;
- isolated;
- transported.
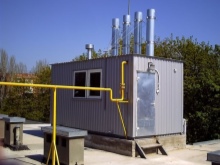
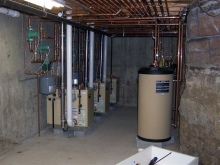
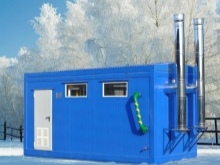
By material
All key materials of the main equipment of boiler houses operate at high temperature and pressure. They are affected by direct mechanical stress and an unfavorable environment in general. Even minor components can be exposed to high humidity and temperature. However, despite the limited range of substances capable of withstanding the corresponding loads, they have an internal division. The most common material in boiler equipment is sheet steel with a low carbon content.
Its appeal is due to:
- excellent plastic properties;
- ease of processing in hot and cold conditions;
- simplicity of welding;
- decent corrosion resistance;
- relative resistance to "brittle destruction".
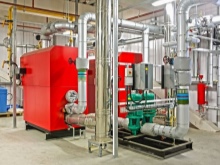
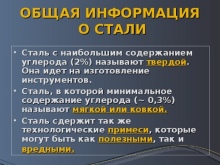
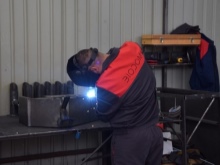
Carbon steel it is customary to divide into alloys of standard quality, high quality and distinguished by special quality.In turn, steel of ordinary quality can have a guaranteed chemical composition, mechanical parameters - both together (denoted by the letters A, B and C, respectively). Grades from 0 to 6 are grouped in order of increasing strength (and simultaneous deterioration of ductility and technological parameters). Steel grades also determine whether a particular metal can be used for heated or cold parts of boiler equipment.
Heat exchangers can be made from:
- become;
- cast iron;
- copper.
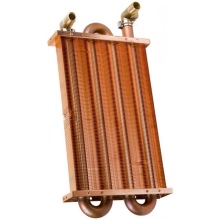
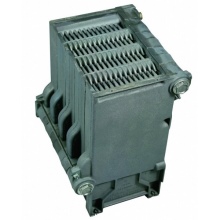
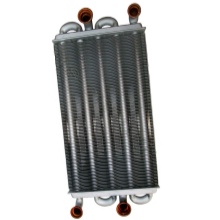
According to the ability to obtain hot water
Not all boilers produce hot water. Steam boiler equipment is quite widespread, which allows you to receive mainly or exclusively steam with different characteristics. It is these systems that are installed at thermal power plants and at a number of industrial facilities.
Production and heating equipment along with steam successfully generates hot water, supplies steam to heating and ventilation systems.
Purely heating installations are for the most part of the hot water type, but there are exceptions.
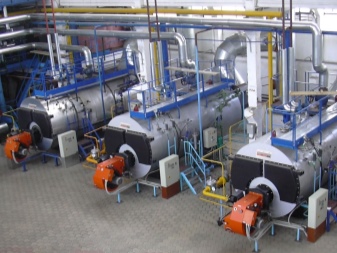
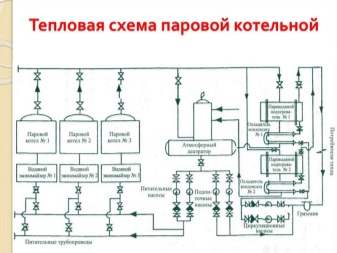
Popular manufacturers
The products of the Biysk boiler plant, which have been operating since 1942, are in demand. Sending a part of goods for export testifies in favor of the enterprise. The range includes both boilers and heat exchangers for them.
High pressure boiler units are also made by the plant in Barnaul. Its products also include:
- fittings for locking and regulating water;
- mufflers of noise;
- steam cooling devices;
- control cabinets and a number of other devices.
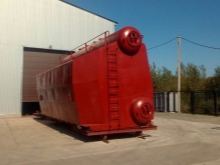
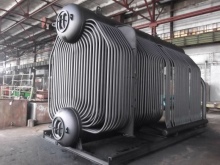
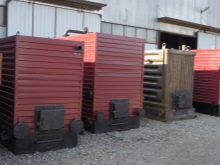
It is worth paying attention to the products of the following companies:
- Izhevsk boiler plant;
- Krasnoyarsk boiler plant;
- East Siberian Boiler Plant;
- Nizhniy Tagil Boiler and Radiator Plant;
- JSC "BKMZ" (also performs installation and warranty work);
- Novomoskovsk boiler-mechanical plant;
- Rosenergoprom;
- "Dorobuzhkotlomash".
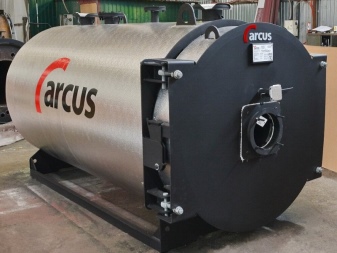
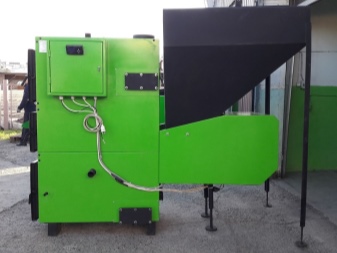
Among foreign suppliers, firms that have worked for 100 years or more deserve attention. First of all it is Buderus and Viessmann (FRG), as well as the Swedish CTC. Less perfect, but also more economically profitable goods from:
- Belgian concern Saint Roch;
- the Belgian ACV supplier;
- German company Winter Warmetechnik;
- Finnish company Kaukora Ltd (Jaspi brand).
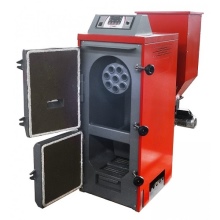
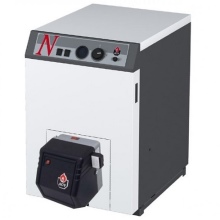
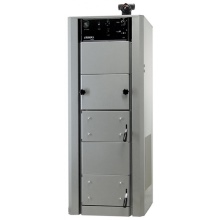
Nuances of choice
From the very beginning, it is worth deciding whether a steam or hot water boiler will be used. This moment depends on the purpose of using the boiler room and the level of loads on it. The next crucial step is to determine the capacity of all installations. Unit power is calculated for the highest winter mode... Technological heat supply and hot water supply must be provided stably.
For serious objects, a feasibility study is required. But ideally, it should be carried out both for cottages and for private houses. The total amount of generated heat and water is calculated taking into account both needs and inevitable losses. The choice of the type of fuel is determined by considerations of both economy and ease of production, as well as environmental friendliness.
In private homes, gas heating is predominantly used.
This solution makes it possible to exclude the construction of additional warehouses or connection to high-tech equipment networks.

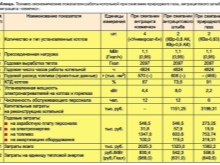
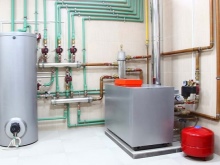
Returning to the types of fuel boilers, it is necessary to mention about electric boilers. It is not easy to obtain permission to install such systems. You will have to documentary proof of your readiness to perform the work. That is why gas fuel is used for many boiler houses of both domestic and industrial levels.
Handling it is even easier in many respects than electrical equipment. The efficiency of gas heating is quite high. However, one should carefully prepare documentation for gas distribution networks and connection to them. We'll have to use a reliable, well-thought-out boiler automation. It is also worth considering that if the pressure in the gas line drops, the boiler room will not be able to work normally.
Liquid fuel (diesel, occasionally gasoline) boilers are quite popular. To arrange their installation and connection, if necessary, then at a minimum. The fuel consumption will be quite high.
Special fire safety precautions must be taken and space must be allocated for storing diesel fuel.
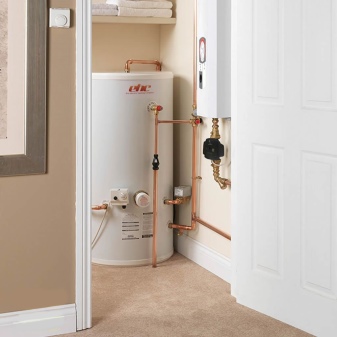
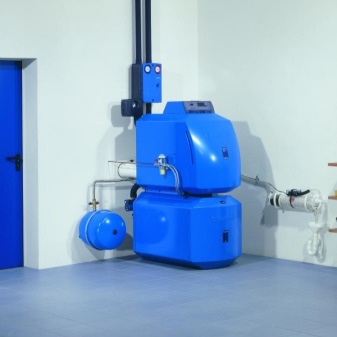
It is worth dwelling separately on solid fuel complexes. They are readily available and allow the use of cheap, widely available fuels. However, coal, firewood and so on will have to be stored somewhere. Air can enter the furnace even without preliminary preparation. Some solid fuel boilers can operate without electricity.
But we must remember that:
- firewood, coal, pellets do not emit too much heat;
- you will have to lay the fuel manually;
- combustion will be uneven;
- incomplete combustion is likely at the slightest deviation from the normal mode;
- control of solid fuel boilers is quite laborious and requires constant monitoring;
- it is quite difficult to maintain the temperature accurately in residential and other serviced premises.
Cast iron heat exchangers are highly resistant to corrosion processes. However, such equipment is relatively expensive. The steel heat exchanger can be made in a variety of ways. This device is cheaper than cast iron and requires less complicated maintenance.
The problem arises due to the high level of corrosion.
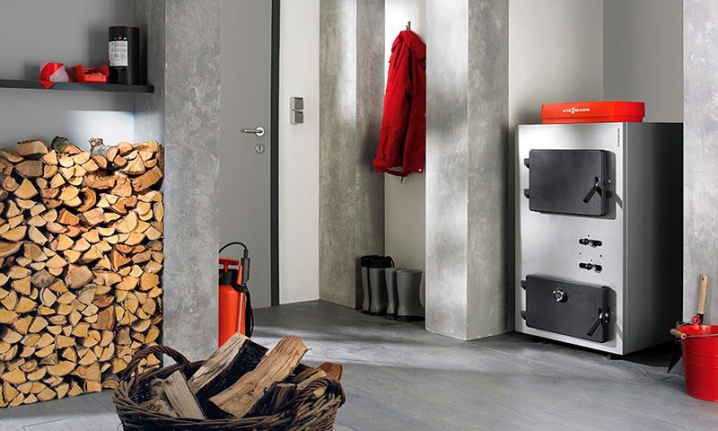
Copper heat exchanger used mainly on boilers of low power. Such a device is extremely susceptible to the ingress of hard water. Boilers with one circuit have only one heat exchanger for DHW and / or heating. Double-circuit devices are used mainly in more powerful systems. It is important to choose a good economizer - it will allow you to use energy much more efficiently.
Concerning air heatersthen their steel models are usually made of 1-4 links. With a larger number of moves, the efficiency almost ceases to grow and does not justify the complication of the system. A cast iron air heater can be found mainly in large, powerful boiler houses. Glass heaters should be selected for boilers using sulphurous fuels.
Blowing systems and apparatus are selected according to the required air intake power. There must be at least 2 fans, each capable of handling the full load.
Attention should be paid to the choice pumping devices... When evaluating a specific specimen, the viscosity, fluidity and heat capacity of the pumped substance are taken into account. Pump performance is calculated very carefully. A power reserve must be imperative to guarantee stability even under increased load.
The permissible differential pressure must also be taken into account.
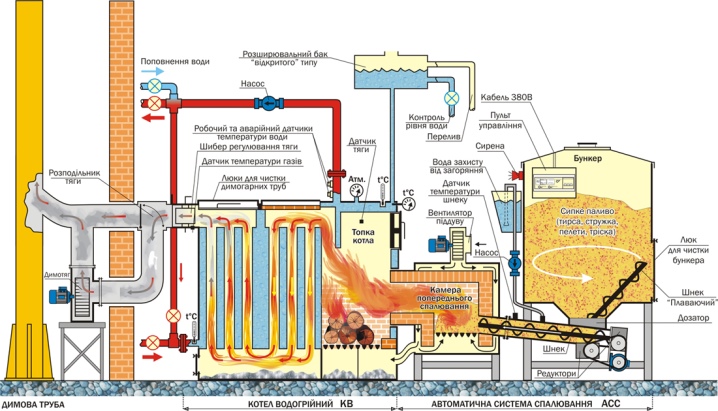
Installation features
The location of the equipment depends primarily on the type of fuel used.... All incineration plants operate normally only with stable ventilation. Boilers must be placed on the podium, where they are tiled or painted with moisture-resistant paint. The supply of equipment to the boiler room is carried out using receiving windows or doorways. The assembly and placement of boilers and other equipment is carried out according to regulatory schemes.
The connection of water mains and other communications is carried out only to the equipment fixed in the designated place. They have the right to connect gas boiler equipment only accredited organizations. In the last phase of work, sensors and electronic equipment are connected, as well as chimneys. When everything is done, equipment, joints need to be inspected and examined.
It is better not to try to install the equipment yourself, but to entrust the case to professionals.
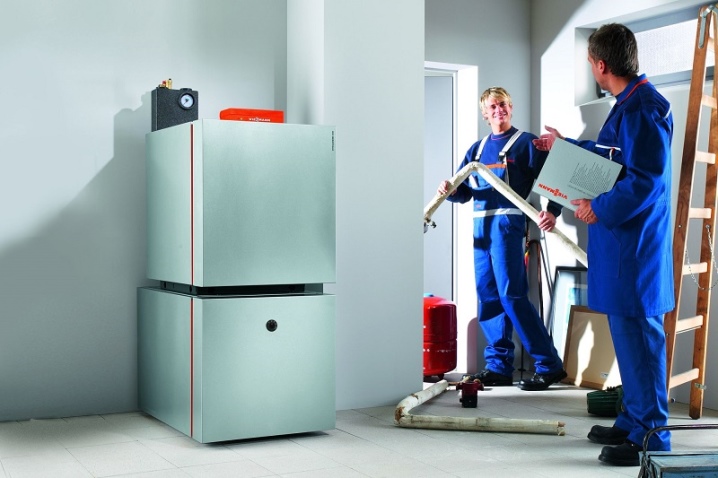
In any serious boiler room, it is impossible to do without water treatment systems. Aeration complexes play a special role among them. If you have to supply hard water, chemical preparation is required. Most often these are modern ion-exchange devices, devices for removing iron and manganese. Removal of harmful minerals and distillation are performed by reverse osmosis; initially it is required to allocate space for such devices.
An open boiler room installation scheme is cheaper than a closed one, but its use itself is much more expensive. The reason is simple: the coolant is in direct contact with air, and therefore heat losses increase significantly. In every room, even a very large one, it is impossible for technical reasons to put more than 2 boilers. All structures of the premises are made of durable non-combustible materials, the finishing is also non-combustible or minimized.
Important: you should leave free space not only for the equipment itself, but also for its maintenance.
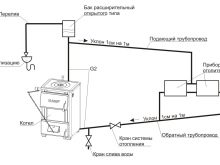
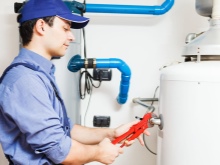
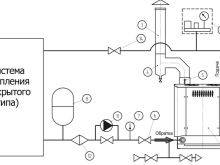
Operating tips
Systematic cleaning of the air inlet is imperative. Overlapping it is categorically unacceptable. Even with a short air shortage, the fuel is not completely combusted. This is not only harmful to health, but also damages the equipment itself.
The atmospheric turbocharged boiler with a sealed firebox operates through general ventilation. But it is required to monitor the full flow of air from the outside. The setup process includes, first of all, the establishment of the optimal combustion mode (or the optimal mode of electricity consumption). After that, safety automation and technical regulation are established.
Last of all, the fuel supply circuits and auxiliary technical means are tuned.
Immediately after the end of such work, it is worth removing all the measured indicators for more accurate accounting later.
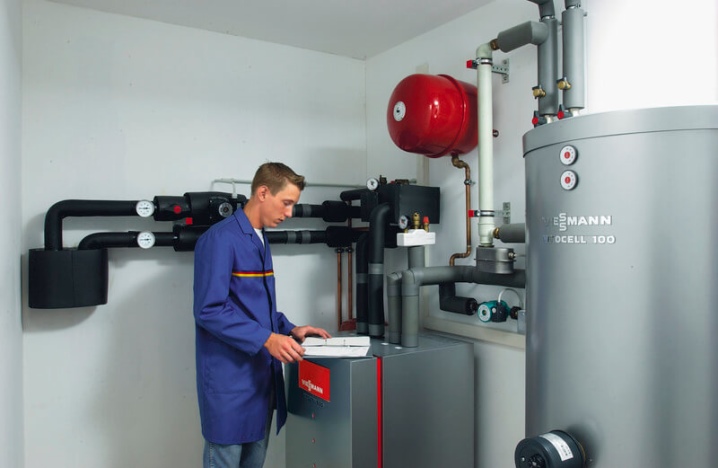
A separate project is being prepared for the grounding of the boiler room. Without it, the commissioning of any serious objects is not allowed. Generally accepted safety measures when servicing boiler equipment imply that only adults with good medical conditions and special training can be allowed to such work. It is worth focusing on similar requirements in the private sector. Inside the boiler room and on its separate equipment, it is imperative to maintain perfect order and cleanliness.
When using gas, the room must be ventilated for at least 3 minutes before starting the furnace. Work with fasteners on communications and devices under pressure is not allowed. At large facilities, mechanics responsible for the condition of the equipment are necessarily involved in work. Even if they are not directly involved, they should still be present in the process. It is not allowed to turn on boilers if:
- isolation is broken;
- the combustion chamber and special communications are not sealed;
- the insulation of the wires is warmed up to more than 60 degrees;
- parts of the boiler and steam lines, hot lines are not thermally insulated;
- fuel oil accumulates in the furnace and under the pumps;
- there are no required fire-fighting equipment.
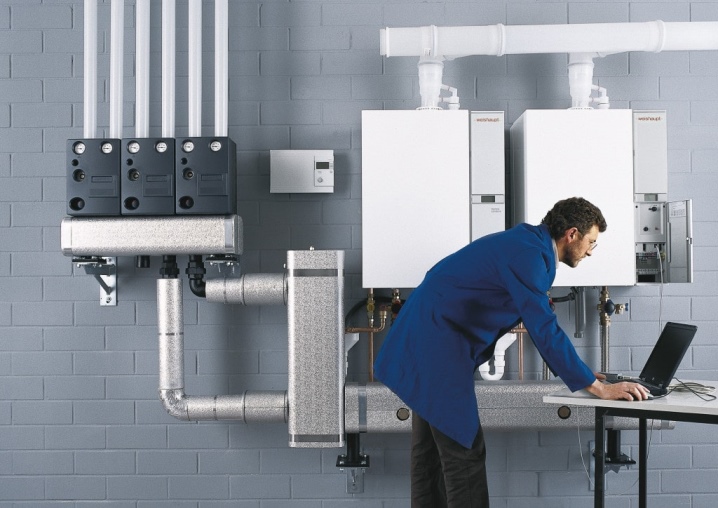
Systematic safety briefing for boiler room personnel is carried out every 6 months. After any incident, the briefing is repeated, regardless of the main timing. The start-up of systems can only be carried out with fully operational control and information devices. Standard and emergency electric lighting is required. When working, it is imperative that:
- use overalls;
- inspect serviced devices;
- use only a tool that is suitable in accordance with all standards and regulations.
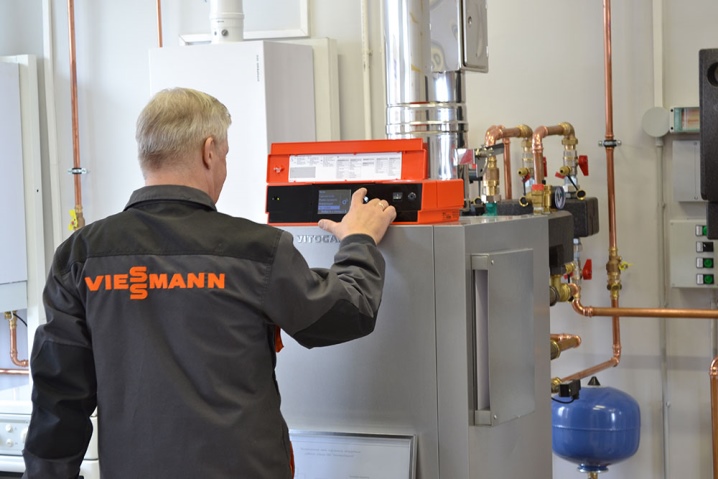
You can clearly find out what elements a modern boiler room consists of from the video below.
The comment was sent successfully.