What are boiler room pumps?
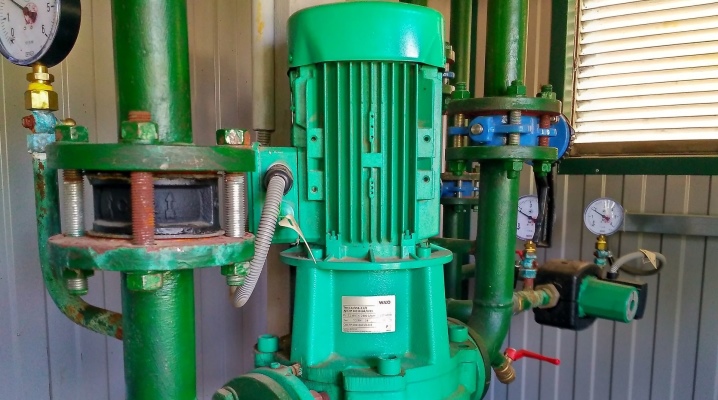
Pumps are often used to ensure the stable operation of the boiler room. They are necessary in order to pump hot water in the heating network system. The main advantage of such devices is that they have a simple design, which allows you to easily install or replace them if necessary.
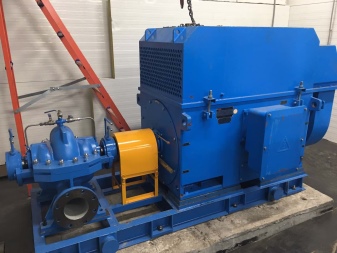
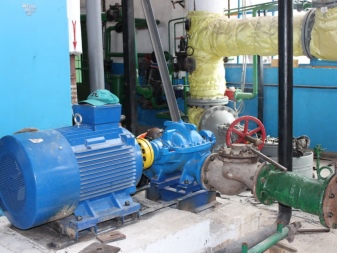
Peculiarities
The operation of a modern boiler house is almost impossible to imagine without pumping equipment. Among the main features, a number of characteristics can be noted.
- The volume that the pump can pump out over a period of time is measured in cubic meters. meters per hour.
- The limiting temperature of the liquid that is pumped. For each pump, the manufacturer sets a certain limit, upon reaching which the device may simply break.
- The force of the head that is generated by the pump. Here, too, everything depends on a specific model. There are many types on the market, so you can choose the best one for any boiler room.
Most experts advise using 2 pumps at the same time in large boiler houses, as this will ensure greater reliability during operation.
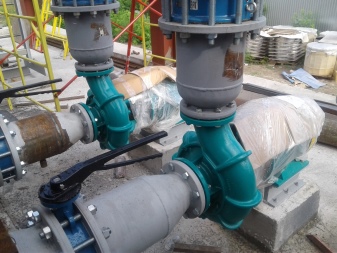

Distinctive features of pumps for boiler rooms are ease of installation and ease of maintenance. During the production of such elements, high quality steel and cast iron are used, which ensures excellent strength and durability of the product.
Due to their technical properties, such units are capable of working only with clean water, therefore, installation of filters is often required. For most models on the market, the amount of impurities in the water should not exceed 0.2 mm.
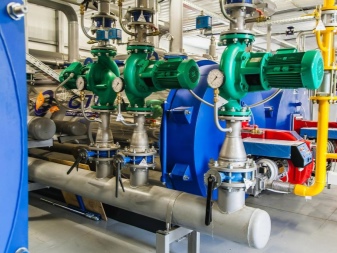
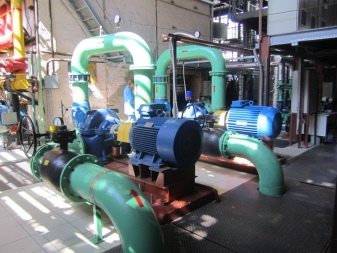
Appointment
Today it is difficult to imagine a boiler room without a pump, since it is he who ensures its stable and uninterrupted operation. In most cases, these units are used to create water circulation, as well as when servicing a boiler room.
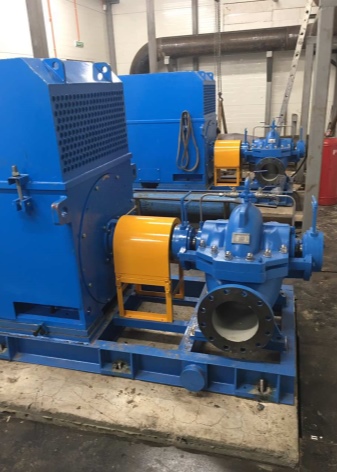
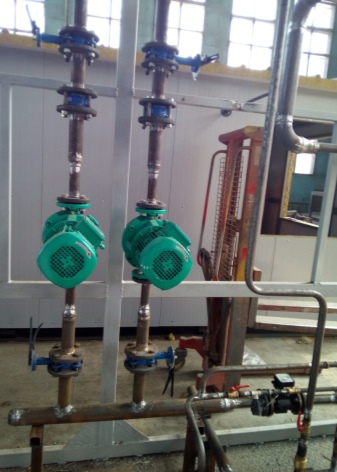
The method of application depends on how the pump was made: with one or two gears. It should be noted that the pumps can be used not only for boiler rooms. This type of equipment is actively used to supply fuel and lubricants to the bases, as well as in the process of pumping various reagents and other similar liquids.
As for the boiler rooms, they usually use network pumps, which boast the presence of an electric motor.
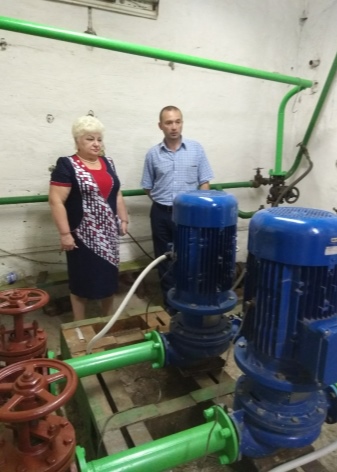
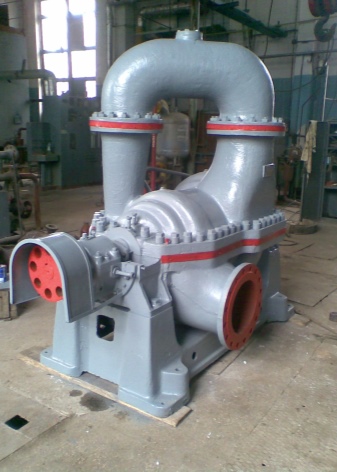
Varieties
On the modern market, there are many varieties of pumping equipment for boiler rooms, which differ in their design features. These devices are network, circulation and water. Besides, the make-up, centrifugal or steam version is in great demand today.
Network
Network pumps are very popular and are used to guarantee the ideal speed of water movement inside the boiler room. In other words, the main job of such a pump is to ensure the stable operation of the boiler house by working with a heat carrier. That is why such units can be seen in half of the boiler houses.
The main disadvantage of such equipment is that it is capable of pumping water that is not hotter than 180 degrees Celsius. Otherwise, the pump parts will immediately fail. Installing a pair of devices will create a powerful network that will be enough even for industrial needs.
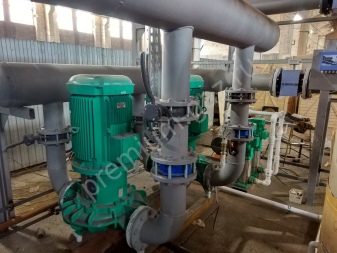
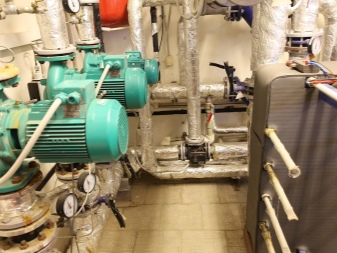
Among the main advantages of the network pump are high strength and excellent efficiency. Strength was achieved thanks to the high quality of the structural elements, which boast resistance to wear and tear. During manufacturing, cast iron alloys are mainly used, which makes the parts so durable.
Besides, network pumps are distinguished by their unpretentious maintenance, and also do not require serious maintenance. Anyone can connect them to the system, and if used correctly, they will last for many years.
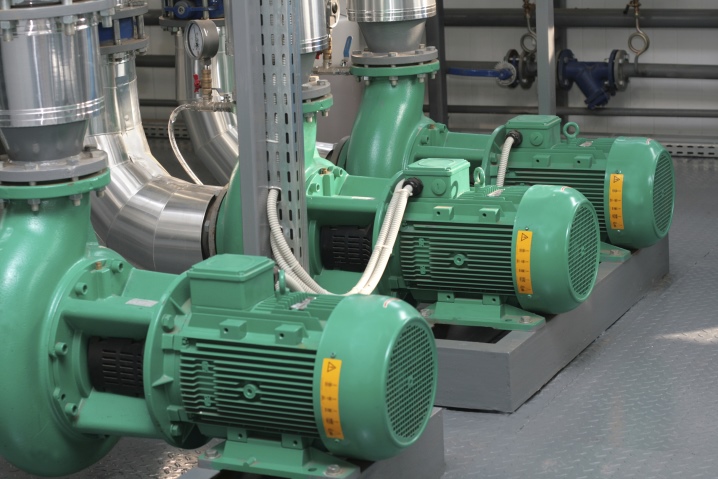
During operation, close attention must be paid to the restrictions set by the manufacturer. The temperature limit is not the only thing that can damage the device. The quality of the liquid used should also be taken into account. If it is water, then it should not contain any additional impurities and pollutants.
For most models, the maximum particle size should not exceed 0.2 mm. Such options are great if boiler houses are oil-based or operate on solid fuels.
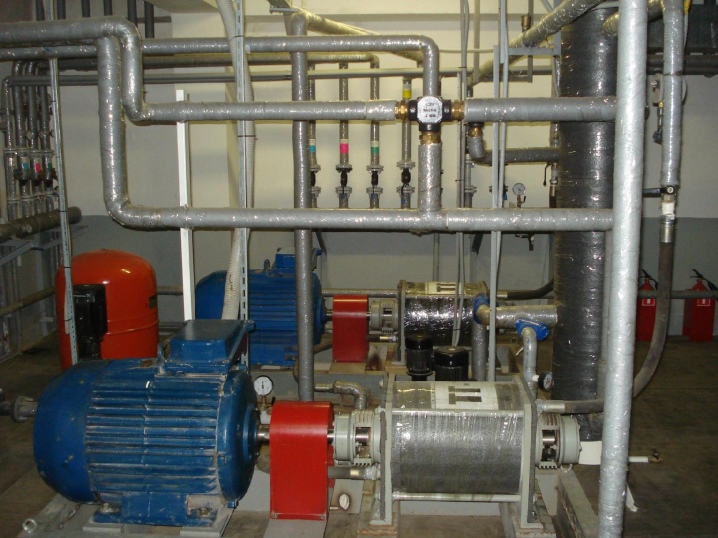
Aquatic
Water pumps are also in great demand today. They are used for the boiler room to ensure a stable raw water head. In addition, such units are actively used today in order to supply water treated with the help of special substances into vessels with hot water.
In other words, the main task of this type of pump is to ensure the availability of the required water level in the hot water tank. In order for this type of pumping equipment to be able to fully fulfill its obligations, close attention in the selection process must be paid to capacity.
It should be selected based on the actual conditions in which the pump will operate.

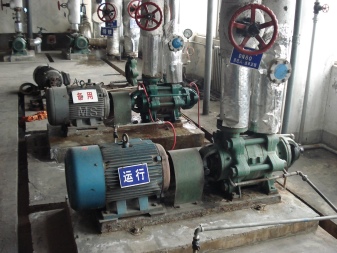
Circulating
If the primary task of the pump is to ensure a high speed of movement of the coolant through the pipes, then for such tasks it is best to choose circulation options. Usually several units are installed at the same time, which at the same time differ in different capacities. Thanks to this, it is possible to form a reliable network that can operate smoothly and ensure the pumping of the coolant.
A distinctive feature of the circulation pump is its design features. The presence of a branch pipe allows for fastening directly to the line, which greatly simplifies the process of installation and operation.
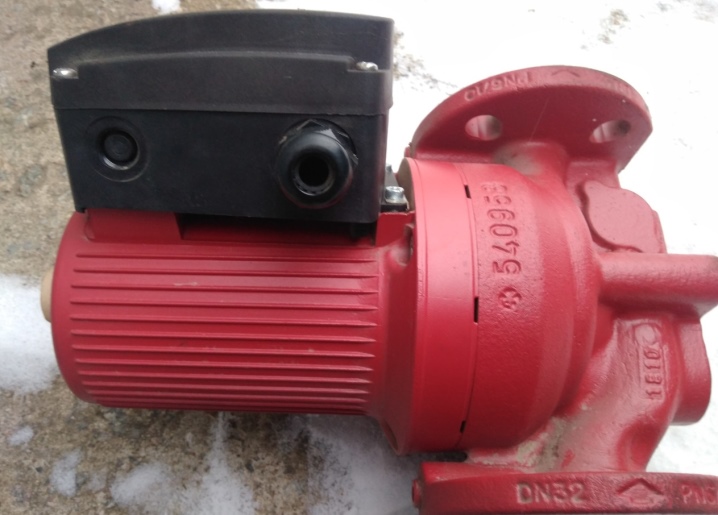
This type of pumping unit also works only with clean liquids. That is why the cleaning process should be given close attention so that there are no mechanical particles. Technical properties make it possible to install such devices on both private and large systems.
The main thing in this case is to correctly select the power of the device so that it is enough to pump the required volume of liquid.
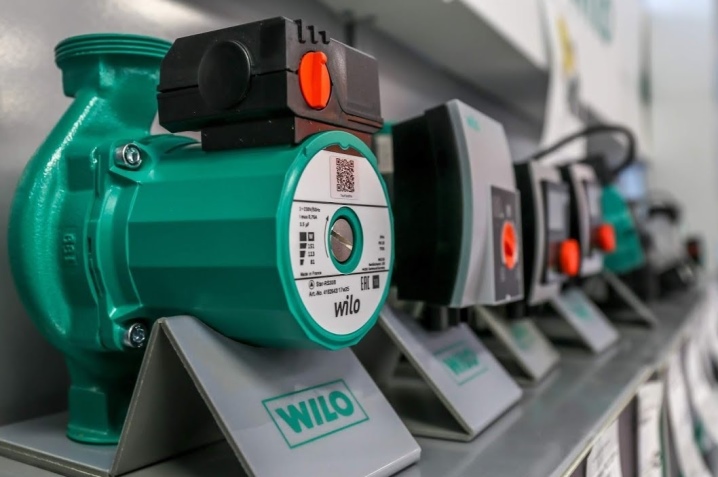
Marking
Before choosing the most suitable pump for the boiler room, you need to carefully study and decipher the alphanumeric designations located on the label. Regardless of the pump type, there is usually some important information entered there.
- UP - shows the type of pump used.
- S / E - indicates a control method. Thanks to these markings, it is possible to understand how the gear changes take place.
- Now comes the numeric pointers. First, the data of the pump diameter from the inside are indicated, and then the maximum allowable head.
- The last figures show the installation length, which is usually indicated in millimeters. This indicator is important in the event that a tie-in of the unit is carried out.
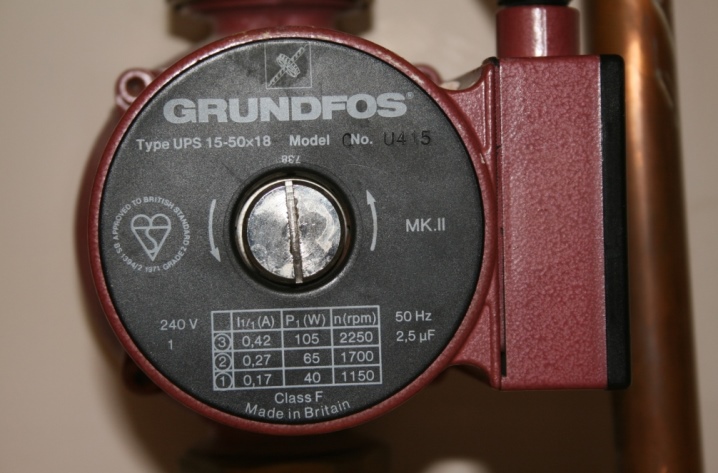
It should be noted that some manufacturers may provide additional information. This can be data about the materials that were used in the production of the case, the method of connection with pipes, as well as the class of electricity consumption.
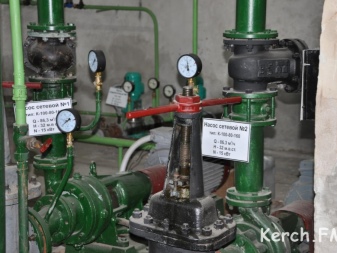
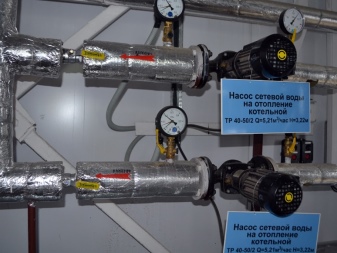
Selection and calculation of pressure
In order for the pumping equipment to perfectly cope with its tasks, you need to pay close attention to the selection process, taking into account the following points:
- the length of the heating system to which the purchased unit will be connected;
- the number of floors to which the system will be connected;
- characteristics of the relief of the region where the highway passes.
During the selection of the optimal option, the requirements set by the manufacturer are also important. This can be the maximum allowable temperature of the fluid in the pipes, the pressure in the system, or the amount of fluid that the pump can pump out.
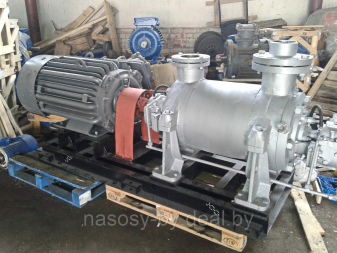
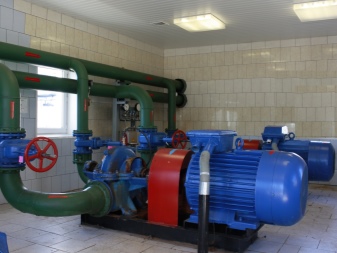
Pumps for boiler rooms must be selected based on the requirements that are present in the heating system itself. First of all, we are talking about pressure. In order to determine the required pressure, you need to use a formula specially created for this, which looks like this:
H = (L sum * R beats + r) / (Pt * g).
Initially, it may show that everything is rather complicated, but in practice, you just need to understand the decryption.
- H is the required size of the head.
- L sum - the length of the contours. Everything should be considered here. For example, if a warm floor is installed, then we must take into account the length of all installed pipes under the floor.
- R beats - resistance level of pipes.
- r is the resistance of the system pipeline.
- Pt is the density of the liquid used in the heating system.
- G is a constant value, which is 9.8 m.
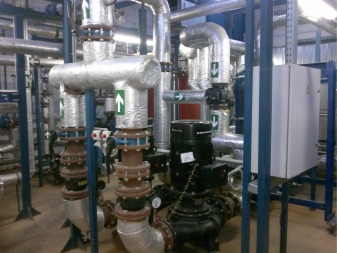
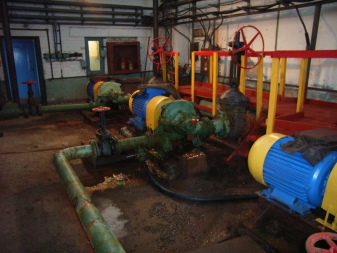
If calculations are made for a conventional system, then the presence of standard valve fittings should be taken into account, therefore a correction factor of 1.3 is taken.
Competently performed calculations allow you to create the necessary fluid pressure in the pipeline so that it can cope with hydraulic resistance. In addition, this makes it possible to be sure that the movement of the liquid will be constant and will be able to reach all elements of the heating system.
The calculation of the head is important to determine the place where the pump will be used: for heating a dwelling or an industrial version.
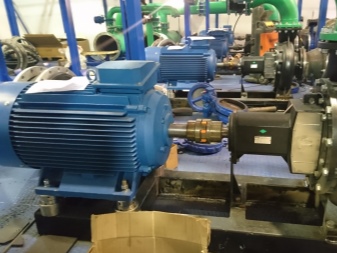
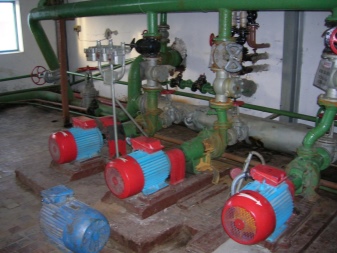
Installation
Installing the pump, although a fairly simple task, should be extremely careful. If the installation is carried out incorrectly, then the device will malfunction and sooner or later will completely fail.
During installation, it is worth following the recommendations of specialists.
- To make installation as convenient as possible, it is best to attach ball valves on all sides of the pump.
- Pumps break down due to the presence of mechanical impurities in the water. Therefore, it is best to install a special filter that will allow you to install them.
- Installing an automatic or manual air valve will facilitate the removal of oxygen, which often collects inside the pipe.
- Each model has its own characteristics, which must be taken into account during the installation work. That is why you need to carefully study the body of the device and the manufacturer's recommendations.
- It is necessary to embed pumps in heating systems horizontally so as not to harm the operation of the electric motor.
- All joints are processed with special sealants and sealed with washers and spacing.
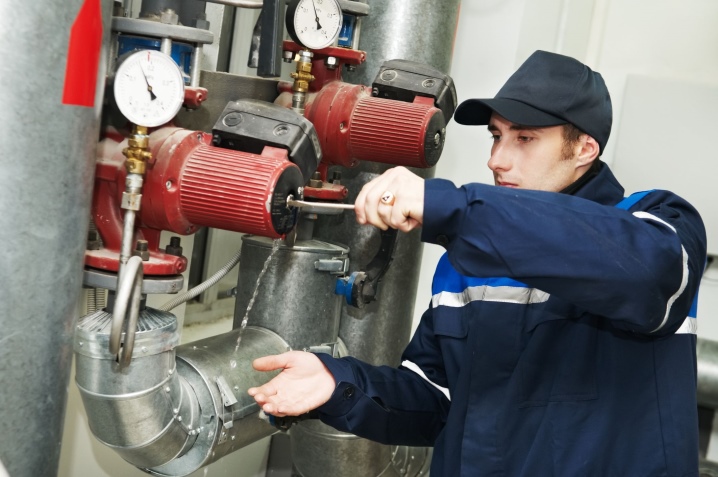
Before starting the installation, it is imperative to study the diagram, draw up a plan for the manufacture of a control cabinet and its installation.
Thus, boiler room pumps are unique units that are designed to pump liquid through the heating system. In the selection process, close attention should be paid to the principle of operation and the power of the device, since it is on them that the ability of the unit to perform its functions depends.
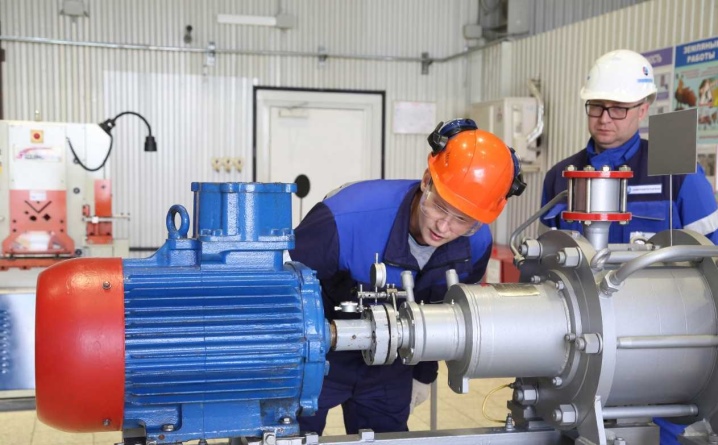
The pump for the boiler room is presented in the video below.
The comment was sent successfully.