All about the installation of boiler rooms
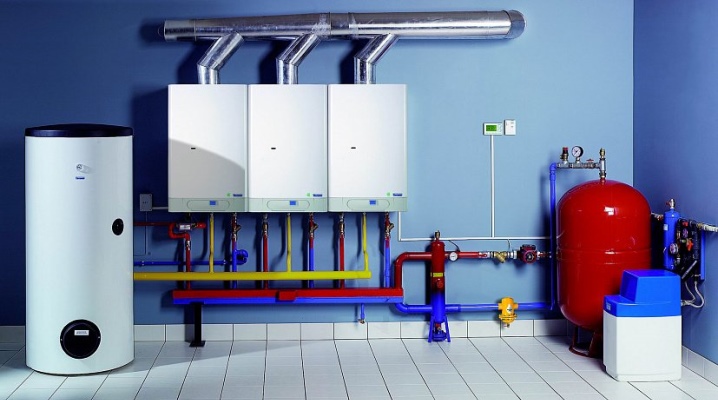
Knowing everything about the installation of boiler rooms is no less important than knowing about the organization of water supply, capital construction or landscape design. In private country houses, industrial installations with a buffer tank and many other equipment options can be installed. So that the result does not disappoint, you need to carefully analyze the features of each type of technique and the nuances of its application.
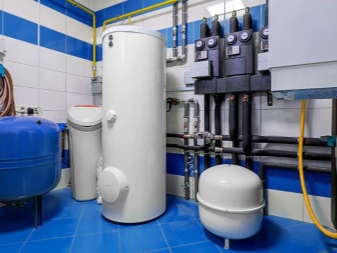
Peculiarities
Installation of boiler rooms in private country houses is a procedure that requires special attention. Do not think that any room of a suitable size will be useful for this purpose. Only low-pressure boilers can provide a normal heat supply. They are placed in basements or on the ground floors. But if there is an opportunity to set aside a separate building for heating equipment, it must be used.
But what should definitely be avoided is placing such objects under residential areas. The minimum height of industrial boilers is 3 m. Their volume cannot be less than 15 m3. According to safety rules, the door must be opened strictly outward.
Another topical point is the use of thoughtful and carefully designed ventilation.
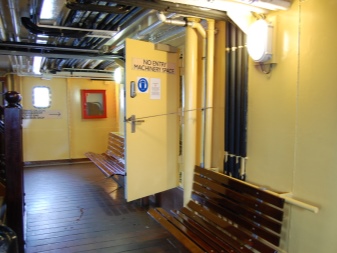
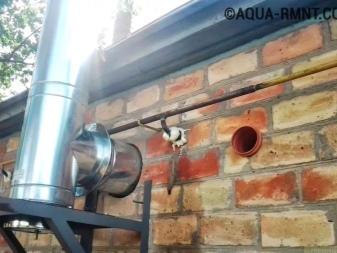
In the presence of adjacent rooms, even technical rooms, the walls must have a fire resistance of at least ¾ hour. It is recommended to use specially designed pipes for fume extraction. A high-class substation is almost always equipped with sophisticated technology and special machines. In the household segment, you can do without this, but extending communications should still be thought out in advance.
Excavation works are usually provided as well. In many cases, stationary boiler houses with steam boilers and with a buffer tank are used. Its role is the temporary accumulation of surplus generated heat, and then the use of these reserves.
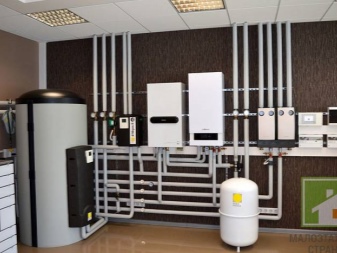

If you additionally use a mixing unit, then as long as there is enough heat given off by the buffer, the temperature in the house will not leave the values specified in the project. However, it will be necessary to carry out a careful calculation for all indicators.
Industrial modular boiler houses rarely need a solid foundation. True, at least minimal preparation of the foundation is still needed. When choosing the type of support structure, they are guided by the type of boiler room and the level of the resulting load.
For the greatest reliability, a simple reinforced concrete slab is placed. Regardless of this, at a very early stage, the base for the chimney is also prepared.
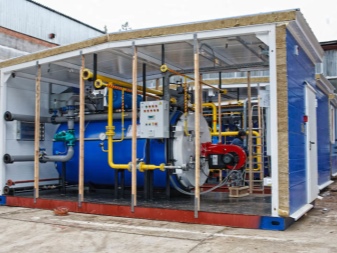
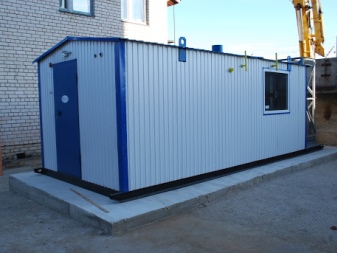
Main steps
Boiler room selection
It is often thought that the choice of a modular boiler room can be made taking into account only the capacity of the equipment. But this creates a number of mistakes that you will have to regret later. The assessment of the conditions of use should include familiarity with:
the geographical location of the facility;
average annual humidity and temperature;
wind rose;
the availability and justification of the use of different types of fuel;
available technological communications (taking into account all that has been said, only a trained high-class specialist can make the right choice).
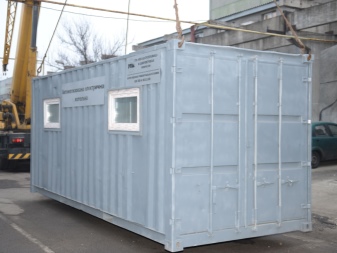
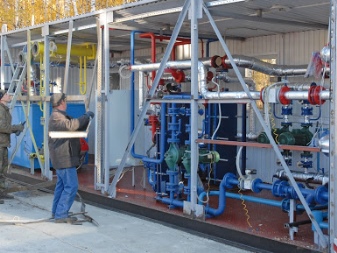
Design
Similarly, drawing up a diagram of the arrangement of boilers and other equipment with your own hands (as opposed to performing direct work) is almost impossible. A key design step is the selection of the most suitable type of fuel and the methods of feeding it to the boilers.In the project, of course, the pumps and pipelines used, ventilation systems and emergency means will have to be displayed. Also a good project contains directions on how to use:
heat exchangers;
sensors;
signaling and measuring devices;
shut-off valves of pipelines;
electrical inputs;
water expansion tanks;
chimneys;
emergency power supply systems;
main and emergency exits.
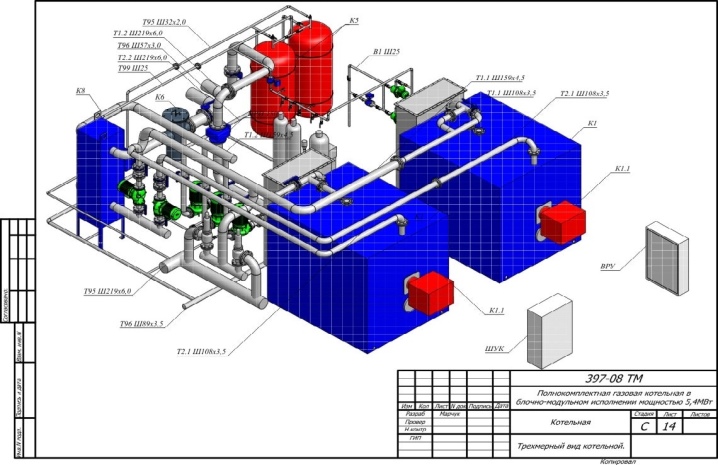
The project should also display sound insulation measures. Even the best boiler equipment is simply a source of loud sounds in accordance with physical laws. Already when drawing up sketch diagrams, it is required to show the arrangement of the heat supply system in the entire building (or in several serviced buildings). When calculating the power of boilers, a certain reserve is taken into account, because an unusually frosty winter can always come. You should also think about:
maintenance and daily operation would be easy and hassle-free;
the supply of water and the removal of energy would take place at the smallest possible distance;
the most adequate modern automation was used;
a safety check was carried out (conclusions about which can only be made by an expert commission).
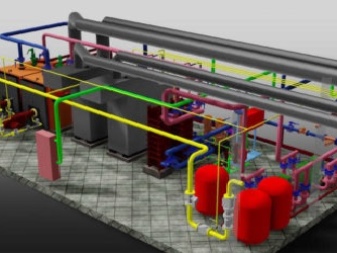
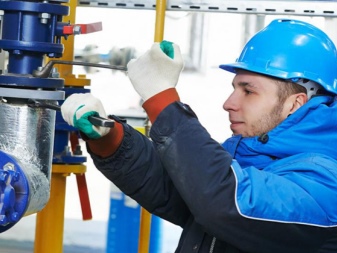
Place selection
Before starting the installation work according to the project, you still need to correctly select the site for them. The necessary information can be found in SNiP 42-01-2002. Additionally, it is worth familiarizing yourself with SP 42-101, as well as recommendations for a specific model of boiler equipment. With a boiler power from 60 to 150 kW, a separate room is allocated for it. If the power exceeds 150 kW, a separate building is required.
It is most convenient to choose the point where water and sewage have already been supplied. If this is not possible, you need to focus on those places where it will be easier to place equipment and connect it to communications.
Important: despite the high cost and complexity, in any case, a separate boiler room is more practical than one built into a residential building. It also provides an increased level of security. This moment is especially relevant when using gas fuel.
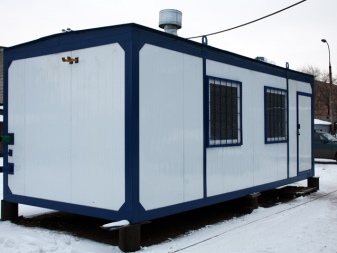
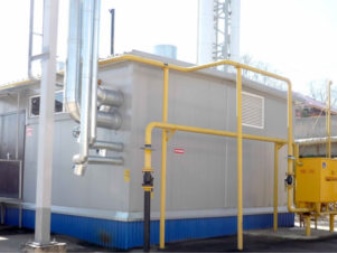
Preparation
At this stage:
once again check all design and estimate documentation;
obtain the necessary permits;
stretch technological communications;
align the installation area;
free it from foreign objects and objects that can interfere with the normal construction and / or subsequent operation of the modular boiler room;
think over and check access roads;
they select places where it will be possible to temporarily supply mounted structures, various dismantled equipment, construction waste.
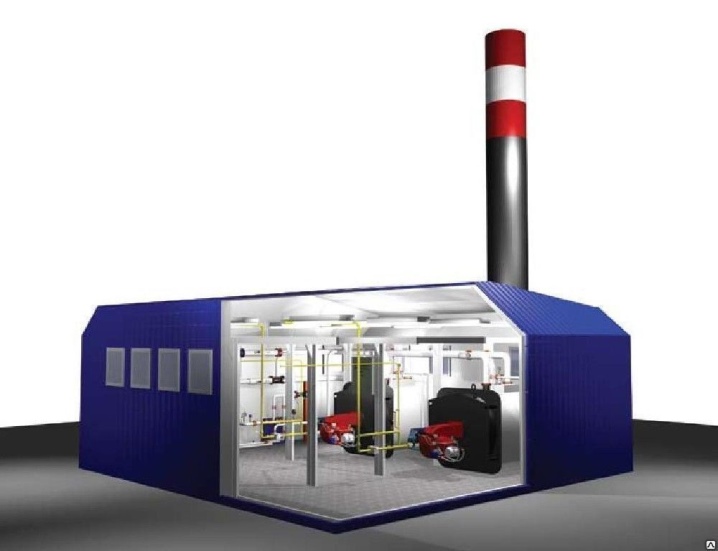
Foundation
This moment, when arranging the heating unit of a cottage, should also not be ignored. Experts consider concrete slabs to be the optimal basis. When choosing them, the desired geometry and size are taken into account. As already mentioned, the site for laying the slabs must be leveled in advance. In some cases, a layer of sand and gravel is poured under the foundation, and drainage contours are also provided.
A typical block-modular boiler room is placed on a concrete base according to the typical scheme:
fall asleep and tamp the soil (up to 0.2 m);
crushed stone is poured (up to 0.3 m);
a concrete layer of 0.25 m is poured;
gird from above with asphalt concrete (strip 0.1 m).
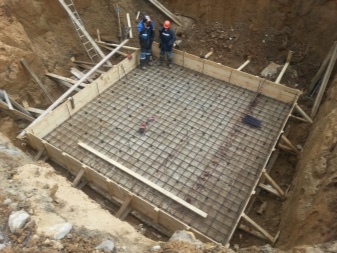
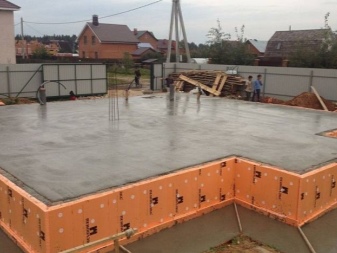
Installation
When arranging a boiler room in a private house, one should not forget about fast-assembly pumping systems. The use of such devices is facilitated by the fact that they are not only assembled at the factory, but also pressure tested. Finally, such products look more aesthetically pleasing than those chosen arbitrarily by the consumers themselves. In large buildings, especially multi-storey buildings, heat collection points can even be mounted on the roof.Of course, this is allowed only if the load on the supporting structures is carefully calculated, and indirectly on the foundation.
A separate topic is the organization and operation of the hood at the heating point. They are guided primarily by considerations of threefold replacement of the entire volume of air in the room in one hour.
But the user will only benefit if this replacement occurs 4 or even 5 times per hour.
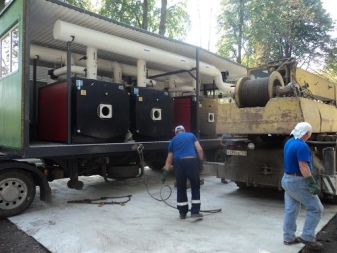
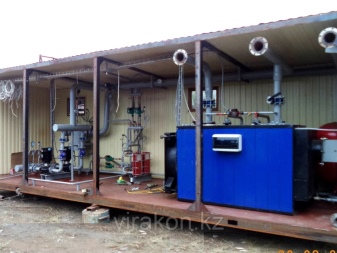
Therefore, exceeding the standard indicators cannot be considered something unprofitable, entailing only unnecessary costs. The ventilation ducts must be carefully sealed, the slightest leakage of the exhaust gases is unacceptable.
In large, serious boiler rooms, it is imperative to provide for forced air exchange. Most often, duct fans are used for this purpose. Important: when assessing the capacity of the ventilation circuit, a margin of 30 - 40% should be left. Then no surprises and "blocking winds" will interfere with normal work. Equipping with outflow and inflow fans helps to increase reliability additionally; savings on this often "go sideways".
Adjustment
But even if everything is designed and installed properly, this does not mean that all possible problems have been solved. Commissioning works are designed to:
evaluate the performance of individual modules and devices;
adjust the system as a whole;
achieve increased productivity;
ensure resource savings.
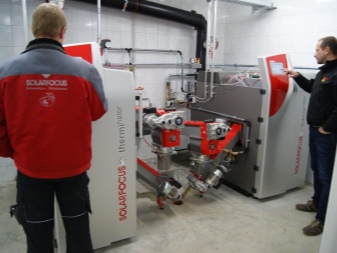
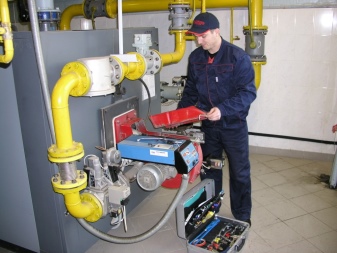
The duration of such works is 2-14 days. Here, both the performance of the boiler house and the set of equipment included in it are of decisive importance.
The check is carried out sequentially for all nodes. They start with a dry test, and then gradually increase all hydraulic and thermal loads to the standard level. At the same time, they check the readiness and adequacy of the control automation, security systems, signaling devices, and manual control elements.
Complex commissioning includes:
research of fuel supply lines, thermal mechanical systems, instrumentation and automation;
checking the water treatment system and the efficiency of its work;
adjustment of the equipment operation in all possible modes;
conclusion to the required characteristics of ventilation, water supply and sewerage;
creation of the necessary documentary and instructional materials for those working in the boiler room.

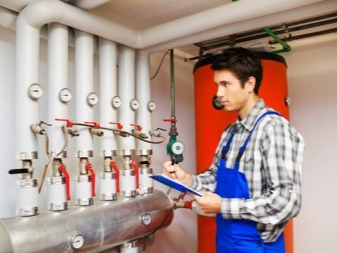
If even small flaws are identified, after the problem is eliminated, the entire commissioning is repeated from scratch. The normal result of this work is the confident functioning of the entire system and its components for at least 72 hours. In this case, the nominal load is set, and the coolant and fuel must comply with the design requirements.
At the end of everything, inspection and testing is carried out by Rostechnadzor inspectors. Based on the results of the check, they form an inspection report and a permit for admission drawn up on its basis. In addition, based on the results of complex testing at rated load, a regime map is drawn up, where they note:
key performance indicators;
basic regulatory parameters;
benchmarks;
Efficiency;
specific fuel consumption.

Recommendations
Normally, the installation of a modular boiler room takes no more than 3 - 4 days. But in order to achieve this, it is imperative that a preliminary survey of the site is carried out. Therefore, you should not trust firms that do not send engineers and experts right away. Practice shows that this only significantly increases the operating time and has a bad effect on the quality of heat supply. The easiest way to install heating equipment is natural gas.
And here the use of liquefied gas, not to mention coal, wood or diesel fuel, requires the organization of a warehouse. In addition, the waste from the combustion of fuel will have to be placed somewhere.In order to prevent errors during commissioning, one should be guided not only by their methodology for gas-using equipment, but also by the operating standards of thermal installations as a whole.
Only specialists who have passed certification in accordance with RD 03-19-2007 can be allowed to work.
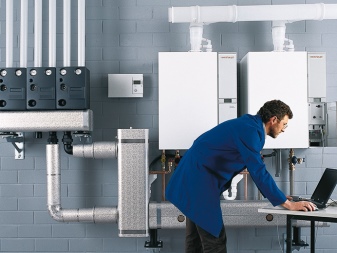
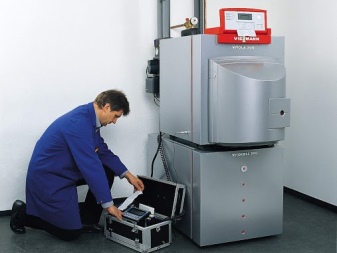
Here are some more tips:
if possible, adapt standard projects to your needs;
use only proven shut-off valves from well-known manufacturers;
comply with the norms of distance from other buildings;
think over the features of power cables.
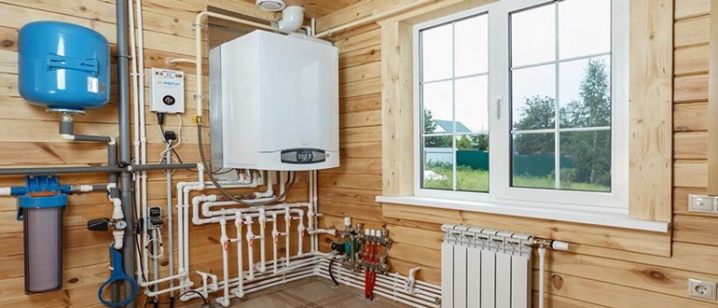
The installation of the boiler room is described in the next video.
The comment was sent successfully.