Hand-molded brick: features, manufacturing, selection rules

Hand-molded bricks differ from ordinary bricks in technical parameters, as well as in unusual colors and textures. Such products are used mainly for restoration and interior work (facing of stoves and fireplaces, restoration of old buildings).




Manufacturing features and molding methods
The production of clay blocks has its own secrets. The shaping work may seem simple, but it is a long and laborious process that requires the master to strictly adhere to all stages of the work.
For manufacturing, use fine clay, well cleaned of impurities. It is mined from special deposits and has different colors (white, blue, gray, red). By mixing them in different proportions, manufacturers can achieve any shade. The type of clay that does not require additional additives is considered the most suitable for brick production.



Hand-molded bricks should be made under a canopy or indoors. The sifted clay is diluted with water to a soft, dense mass that holds its shape well.
Even before the process of placing in the molds, the master manually begins the shaping. The prepared mass on the table is cut into pieces using a wire. Each piece must be sized to fit the shape to fill it completely.


The brick mold is a box with a smooth inner surface. Such boxes are made of wood with a dense texture, so in the process they do not distort or swell.
Before filling the mold, the inside is covered with fine sand to facilitate the extraction process. Also, sand helps to achieve the effect of an aged brick. After firing, the brick is thrown from about a meter in height so that small cracks and grooves appear on the surface, which further enhance the imitation of "antiquity".
Experts recommend that the chopped clay be thrown into the prepared mold with force. This will fill the form completely, and the quality of the finished product will increase. Do not add clay mass to the mold if it turns out to be insufficient. This will reduce the quality of the brick. When the mold is complete, the excess clay is cut off with a knife or wire.


Then the raw block is carefully removed from the mold and sent to dry. To form the next brick, the mold is cleaned of the remains of clay and again sprinkled with sand. The next stage of production is drying. This process is necessary to remove excess moisture and prepare for firing. After drying, raw blocks should contain no more than 10% moisture. The drying room must be kept at a constant temperature and well ventilated. Raw blocks are dried from one to three weeks, it all depends on external conditions (temperature, humidity, etc.). Excess moisture can also be removed by blowing warm air over the blocks.


The final stage is firing in a special oven. Calcination takes place in several stages at different temperatures. First, at a temperature of 2000 ° C, heating and removal of moisture residues take place. Then the temperature increases to 8000 ° C, the process of sintering and the formation of an integral block begins. After that, the temperature gradually decreases. The whole process takes over 6 hours.

There are two main molding methods in the industry:
- plastic;
- semi-dry.
With the plastic method, the green blocks are dried before firing for several weeks. If the block is not dry enough, it may crumble in the oven. If this does not happen, the quality of the finished product will still significantly deteriorate.
Many manufacturers speed up the drying process, trying to avoid cracking of the finished product by adding impurities (shale, sawdust, coal) to the clay. However, brick made with violations of technology has dark spots on the surface. Such products are of poor quality and short-lived.


The semi-dry method came into use much later. It is considered to be more economical in terms of both time and investment. Special drums are used to dry the clay. The knee-lever presses then form bricks from the clay powder, which can be sent directly for firing. This method allows not only to save time, but also to obtain better quality products.


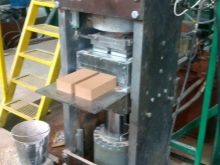
When molded by hand, bricks are produced in small batches. The process does not require an impressive investment. In addition, small-scale production technology is better followed, so the blocks are characterized by high strength and durability.


Difference from clinker
For the manufacture of bricks by hand, a special type of clay is used - Cambrian. A different grade is suitable for clinker, more ductile and fire resistant. This clay contains little chemically bound water in comparison with other varieties.


The clinker is molded under high pressure and calcined at temperatures up to 20,000 ° C. The clinker contains lime and salt, which provides strength and prevents efflorescence. Firing at a high temperature allows you to get a dense block without cracks and pores, with an even and smooth surface.
Clinker walls withstand moisture and sudden changes in temperature well. Handmade bricks can be destroyed by temperature extremes, so they are practically not used in house construction. In this case, due to its operational and mechanical properties, clinker is considered the most suitable material.


Advantages and disadvantages
The main advantage of hand-molded bricks is their high strength. For several decades, it retains its properties and appearance.
Other advantages of hand-molded bricks:
- does not allow moisture to pass through, leaves the room dry;
- possesses frost resistance, suitable for use in all climatic zones;
- does not undergo deformation and cracking;
- has good sound and heat insulation properties;
- is environmentally friendly.
The downside is its high price, which is associated with the laboriousness of the process and low productivity (in comparison with factory automated production).
Applications
Hand-molded bricks are suitable for facing the pedestals of monuments, building facades. It is used for exclusive interior design, fireplaces, chimneys and other interior structures that heat up. It can be put in a doorway or window opening, you can lay it out with a fence, column, arch, vault, gazebo or bench.
Hand-molded bricks are much more expensive than ordinary bricks. But due to its excellent performance properties, high strength, rich colors and unusual texture, it justifies its price. This brick will be especially appreciated by lovers of luxurious semi-antique designs.

Criterias of choice
When choosing, you need to consider the following points:
- the dimensions must be optimally selected to reduce the amount of waste;
- it is important to determine the exact color in advance;
- the strength of the blocks should be selected taking into account the requirements of the project (recommended moisture absorption - up to 10%, frost resistance class - F50).
When choosing bricks from a foreign manufacturer, you need to take into account the characteristics declared by the manufacturer, as well as the climatic conditions in which the products can be used. Dutch manufacturers produce bricks of all standard sizes that are suitable for various jobs - from building houses to facing facades. At a cost, they exceed their counterparts, but the parameters speak for themselves: the strength of M100-M300, frost resistance is higher than F100, moisture absorption is from 8 to 10%.
For the conditions of our climate, the products of the German company Muhr, which are of high quality, are suitable.
Benefits of the German brand:
- a large selection of shades, textures;
- high class of frost resistance;
- preservation of properties at high humidity and under the influence of direct sunlight;
- no risk of embrittlement during use;
- the presence of only harmless materials in the composition.


Donskiye Zori stands out among Russian manufacturers. In terms of quality, the products are most similar to analogues of foreign manufacturers. The cost of bricks of this brand is lower than the prices for imported products due to the use of domestic raw materials. The products comply with Qbricks quality standards.
According to production standards, facing ceramic bricks must have the following characteristics:
- voidness - no more than 48%;
- compressive strength - not less than M75;
- frost resistance - not less than F50;
- moisture absorption - not less than 6%, but not more than 28%


Manufacturers
The Russian market consists mainly of imported products:
- Wienerbeger (Austria) - one of the leading companies sells half of its products in Russia;
- Nelissen (Belgium) - differs in that it produces bricks of rare colors, many of which are not available from other companies;
- Lode (Latvia) - products have a large selection of colors and textures;
- CRH (Ireland) - the company that first created a brick that changes color depending on the lighting (to achieve this effect, not chemical additives are used, but a special firing method);
- Klinkerwerke MUHR (Germany) used mainly for restoration work.
The plant "Kerambrok" (Ukraine) was one of the first to set up mass production and began to produce handmade material under the brand name "Yekaterinoslavsky brick". Each piece is unique in its own way, since the entire manufacturing process is carried out by craftsmen by hand.
The trading house "Petrovsky brick" (Russia) relatively recently began to produce handmade bricks (since 2015). Brick blocks are produced in European format, in accordance with all requirements. The company is constantly expanding its assortment, is engaged in the manufacture of products according to individual parameters, and has a stable dealer network. She has already entered the markets of the near abroad.


For more information on hand-molded bricks, see the video below.
The comment was sent successfully.